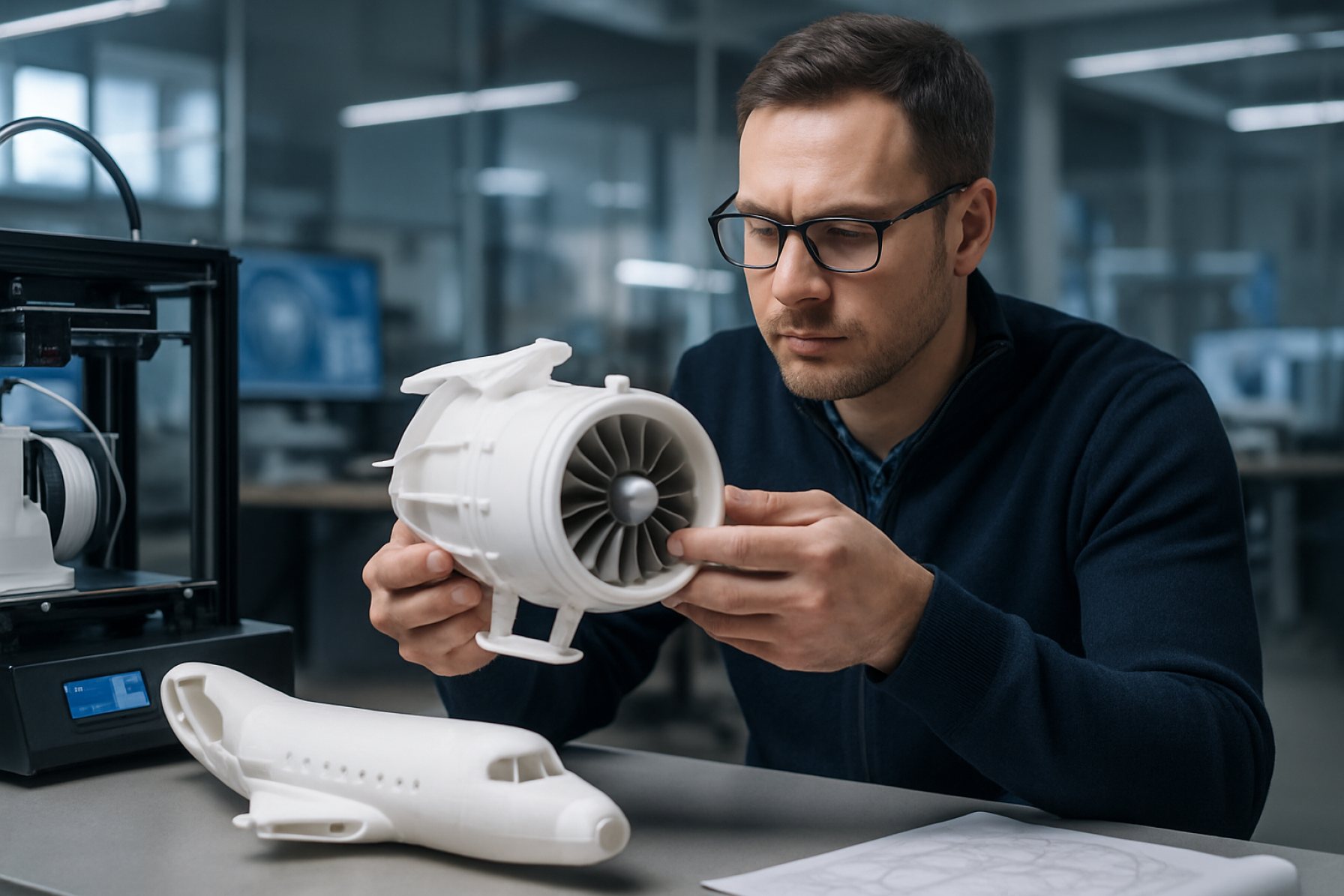
Hoe Rapid Prototyping de Ontwikkeling van Luchtvaartcomponenten Transformeert in 2025: Versnellen van Innovatie, Verlaging van Kosten, en een Geprojecteerde 14% CAGR Tot 2029
- Executive Summary: Belangrijke Trends en Marktdrivers in 2025
- Marktomvang en Groei Vooruitzicht (2025–2029): Het Kwantificeren van de Kans
- Kerntechnologieën: 3D-printen, CNC-frezen en Hybride Benaderingen
- Materiaalinnovaties: Geavanceerde Legeringen, Composieten en Polymeren
- Adoptie door Vooruitstrevende Luchtvaart-OEM’s en Tier 1 Leveranciers
- Regelgevende en Certificeringsuitdagingen voor Geprototypte Componenten
- Casestudies: Succesvolle Rapid Prototyping in Vliegtuigen en Ruimteschepen
- Concurrentielandschap: Sleutelfiguren en Strategische Partnerschappen
- Toekomstige Vooruitzichten: Opkomende Technologieën en Marktverstoorders
- Aanbevelingen: Strategische Acties voor Belanghebbenden in 2025 en Verder
- Bronnen & Referenties
Executive Summary: Belangrijke Trends en Marktdrivers in 2025
In 2025 blijft rapid prototyping de luchtvaartcomponentensector transformeren, gedreven door de behoefte aan versnelde innovatie, kostenefficiëntie en verbeterde ontwerpflexibiliteit. De adoptie van geavanceerde additive manufacturing (AM) technologieën, zoals selectieve laser smelting (SLM), elektronenstraalsmelting (EBM) en directe metaal laser sintering (DMLS), stelt luchtvaartfabrikanten in staat om ontwerpen snel te itereren en complexe geometrieën te produceren die voorheen niet haalbaar waren met traditionele methoden. Deze verschuiving is vooral duidelijk onder vooraanstaande luchtvaart-OEM’s en leveranciers, die rapid prototyping benutten om ontwikkelingcycli te verkorten en nieuwe producten sneller op de markt te brengen.
Belangrijke spelers in de sector, zoals Airbus en Boeing, hebben rapid prototyping geïntegreerd in hun productontwikkelingsprocessen, waarbij ze het gebruiken voor zowel functionele tests als de productie van vluchtklare componenten. Zo heeft Airbus aanzienlijke verminderingen in doorlooptijden gerapporteerd voor complexe onderdelen, terwijl Boeing zijn gebruik van AM voor lichtgewicht structurele componenten en cabine-interieurelementen blijft uitbreiden. Deze vooruitgang wordt ondersteund door samenwerkingen met technologieproviders zoals GE Aerospace, die de pionier is in het gebruik van additive manufacturing voor cruciale motoronderdelen, waaronder brandstofinjectoren en warmtewisselaars.
De markt getuigt ook van een toenemende investering in digitale ontwerp- en simulatiemiddelen, die rapid prototyping aanvullen door virtuele testen en optimalisatie mogelijk te maken voordat fysieke modellen worden geproduceerd. Bedrijven zoals Siemens bieden geïntegreerde softwareoplossingen die de overgang van digitale modellen naar fysieke prototypes stroomlijnen, waardoor het ontwikkelingsproces verder versnelt en het risico op kostbare ontwerpfouten wordt verminderd.
Materiaalinovatie blijft een belangrijke drijfveer, met luchtvaartleveranciers zoals Honeywell en Safran die nieuwe hoogwaardige legeringen en composieten verkennen die zijn toegesneden op additive manufacturing. Deze materialen bieden betere sterkte-gewichtsverhoudingen en thermische weerstand, en voldoen aan de strenge eisen van luchtvaarttoepassingen terwijl ze efficiëntere prototypingwerkstromen mogelijk maken.
Als we vooruitkijken, is de vooruitzichten voor rapid prototyping in de luchtvaartrobust. Verwacht wordt dat de sector een aanhoudende groei zal zien in de adoptie van AM-technologieën, gedreven door voortdurende vooruitgang in machinecapaciteiten, materiaalkunde en digitale integratie. Naarmate regelgevende instanties zoals de Federal Aviation Administration en European Space Agency certificeringspaden voor additief vervaardigde componenten verfijnen, zal de overgang van prototyping naar grootschalige productie waarschijnlijk versnellen, waardoor rapid prototyping zich kan vestigen als een hoeksteen van luchtvaartinnovatie tot 2025 en daarna.
Marktomvang en Groei Vooruitzicht (2025–2029): Het Kwantificeren van de Kans
De markt voor rapid prototyping van luchtvaartcomponenten staat tussen 2025 en 2029 voor robuuste groei, aangedreven door de versnelde adoptie van additive manufacturing (AM), digitaal ontwerp en geavanceerde materialen in zowel de commerciële als de defensieluchtvaartsector. Vanaf 2025 blijft de wereldwijde luchtvaartindustrie prioriteit geven aan rapid prototyping om ontwikkelingcycli te verkorten, kosten te verlagen en de productie van complexe, lichtgewicht onderdelen mogelijk te maken die voldoen aan strenge regelgevende en prestatie-eisen.
Belangrijke luchtvaartfabrikanten en leveranciers vergroten hun investeringen in rapid prototypingtechnologieën. Boeing en Airbus hebben beiden additive manufacturing en rapid prototyping geïntegreerd in hun productontwikkelingsprocessen, met honderden 3D-geprinte onderdelen die nu vliegen op commerciële en militaire platforms. GE Aerospace breidt zijn gebruik van rapid prototyping voor jetmotorcomponenten verder uit, gebruikmakend van zijn wereldwijde netwerk van additive manufacturing-faciliteiten. Lockheed Martin en Northrop Grumman bevorderen ook rapid prototyping voor zowel structurele als voortstuwingsapplicaties, met name in systemen voor de volgende generatie jachtvliegtuigen en ruimtevaart.
De marktkans wordt verder onderstreept door het groeiende ecosysteem van gespecialiseerde leveranciers. Stratasys, een leider in polymer 3D-printen, en 3D Systems, dat zowel polymer- als metaal-AM-oplossingen aanbiedt, breiden hun luchtvaartportefeuilles uit. Renishaw en EOS zijn opmerkelijk om hun metalen additive manufacturing-systemen, die steeds vaker gecertificeerd zijn voor vluchtuitrusting. Deze bedrijven werken samen met OEM’s en Tier 1-leveranciers om de kwalificatie van nieuwe materialen en processen te versnellen, wat een sleutelcomponent is voor marktgroei.
Kwantitatief gezien wordt verwacht dat het segment rapid prototyping binnen de luchtvaart sneller zal groeien dan de algemene industriële AM-groeisnelheden, met een jaarlijkse uitbreiding die wordt geprojecteerd in de hoge enkele tot lage dubbele cijfers tot 2029. Dit wordt aangedreven door stijgende vliegtuigproductieratio’s, de behoefte aan snellere iteraties in ontwerp en testen, en de druk voor duurzaamheid door materiaalefficiëntie en onderdelenconsolidatie. De defensiesector wordt verwacht een belangrijke drijfveer te zijn, aangezien overheden investeren in wendbare ontwikkeling en onderhoud van geavanceerde lucht- en ruimteplatformen.
Vooruitkijkend zal de markt profiteren van voortdurende vooruitgang in digitaal engineering, automatisering en certificeringsnormen. De integratie van rapid prototyping met digitale tweelingen en modelgebaseerde systeemengineering zal naar verwachting de ontwikkelingstijdlijnen verder verminderen en nieuwe ontwerpmogelijkheden ontgrendelen. Naarmate luchtvaart-OEM’s en leveranciers hun adoptie van rapid prototyping verdiepen, zal de sector een groter deel van de wereldwijde additive manufacturing-markt veroveren, waarbij het zijn rol als hoeksteen van luchtvaartinnovatie voor de volgende generatie versterkt.
Kerntechnologieën: 3D-printen, CNC-frezen en Hybride Benaderingen
Rapid prototyping voor luchtvaartcomponenten in 2025 wordt gekenmerkt door de convergentie van geavanceerd 3D-printen (additive manufacturing), precisie CNC-frezen en opkomende hybride productiebenaderingen. Deze kerntechnologieën stellen sneller ontwerpen in staat om iteraties uit te voeren, doorlooptijden te verkorten en complexe geometrieën te produceren die voorheen niet haalbaar waren met traditionele methoden.
3D-printen (Additive Manufacturing) blijft een transformerende kracht in luchtvaartprototyping. Belangrijke luchtvaart-OEM’s en leveranciers benutten metaal additive manufacturing voor zowel prototyping als eindgebruik onderdelen. GE Aerospace heeft zijn gebruik van laserpoederbedfusie en elektronenstraalsmelting uitgebreid om snel jetmotorcomponenten te prototypen en te valideren, waardoor de ontwikkelingcycli van maanden tot weken zijn verkort. Airbus gebruikt eveneens additive manufacturing voor structurele en cabinecomponenten, met een focus op lichtgewicht en onderdelenconsolidatie. De adoptie van hoogwaardige materialen zoals titanium en Inconel-legeringen versnelt, gedreven door de behoefte aan optimalisatie van sterkte/gewicht en thermische weerstand.
In 2025 ziet de industrie de rijping van grote-format additive systemen, die het prototypen van grotere assemblages zoals vleugelribben en rompsecties mogelijk maken. Stratasys en EOS zijn enkele van de technologieproviders die multipele materialen en hoge-snelheid printcapaciteiten bevorderen, ter ondersteuning van de snelle iteratie van zowel metalen als polymeer-gebaseerde luchtvaartonderdelen.
CNC-frezen blijft onmisbaar voor rapid prototyping, vooral voor hoogwaardige, strakke toleranties. Luchtvaartleveranciers investeren in 5-assige en multi-tasking CNC-machines om de productie van complexe prototypes uit luchtvaartgeschikte legeringen te versnellen. Haas Automation en DMG MORI zijn prominente fabrikanten wiens apparatuur veelgebruikte is in luchtvaartprototypingwerkplaatsen. CNC-frezen wordt vaak ingezet voor nabewerking van 3D-geprinte onderdelen om te zorgen dat kritische oppervlakken voldoen aan strenge luchtvaartnormen.
Hybride Productiebenaderingen—die additieve en subtractieve processen combineren—winnen aan terrein. Deze systemen staan de additieve opbouw van near-net-shape onderdelen toe, gevolgd door precisie CNC-afwerking. Yamazaki Mazak en TRUMPF ontwikkelen hybride machines die laser-metaaldepositie integreren met CNC-frezen, waardoor de snelle prototyping van complexe, hoogwaardige luchtvaartcomponenten met verminderd materiaalafval en verbeterde mechanische eigenschappen mogelijk wordt.
Vooruitkijkend wordt verwacht dat de integratie van digitaal ontwerp, simulatie en productieprocessen rapid prototyping verder zal stroomlijnen. De voortdurende investeringen van de luchtvaartsector in deze kerntechnologieën zullen naar verwachting leiden tot nog kortere ontwikkelingstijden, meer ontwerpvrijheid en verbeterde prestatievalidatie voor volgende generatie lucht- en ruimtevaartcomponenten tot en met 2025 en verder.
Materiaalinnovaties: Geavanceerde Legeringen, Composieten en Polymeren
Rapid prototyping transformeert de ontwikkeling van luchtvaartcomponenten, waarbij materiaalinovaties in geavanceerde legeringen, composieten en polymeren een cruciale rol spelen in 2025 en daarna. De vraag van de luchtvaartsector naar lichtere, sterkere en hittebestendige materialen drijft de adoptie van nieuwe rapid prototyping technieken, in het bijzonder additive manufacturing (AM), dat het gebruik van deze geavanceerde materialen in complexe geometrieën mogelijk maakt die voorheen niet haalbaar waren met traditionele fabricage.
In 2025 maken vooraanstaande luchtvaartfabrikanten gebruik van rapid prototyping om het ontwerp en de testing van componenten uit hoogwaardige legeringen zoals titaniumalumidines en nikkel-gebaseerde superlegeringen te versnellen. Zo gaat GE Aerospace voort met het gebruik van additive manufacturing voor onderdelen van jetmotoren, gebruik makend van gepatenteerde legeringen die superieure sterkte-gewichtsverhoudingen en thermische stabiliteit bieden. Deze materialen zijn cruciaal voor motoren van de volgende generatie, waar efficiëntie en emissiereductie van levensbelang zijn.
Composieten staan ook vooraan bij de vooruitgang in rapid prototyping. Bedrijven zoals Boeing en Airbus integreren koolstofvezel-versterkte polymeer (CFRP) en thermoplastische composieten in hun prototypingwerkstromen. Deze materialen maken de productie van lichtgewicht structurele componenten met hoge vermoeiingsbestendigheid mogelijk, wat essentieel is voor zowel commerciële als defensieluchtvaarttoepassingen. Het gebruik van geautomatiseerde vezelplaatsing (AFP) en 3D-printtechnologieën stelt hen in staat om snel te itereren en composietonderdelen aan te passen, waardoor doorlooptijden van maanden tot weken worden verkort.
Polymeren, met name hoogpresterende thermoplasten zoals PEEK en PEKK, worden steeds vaker gebruikt in rapid prototyping voor niet-structurele en semi-structurele luchtvaartcomponenten. Stratasys, een leider in polymer additive manufacturing, heeft samengewerkt met luchtvaartleveranciers om nieuwe materialen en processen te kwalificeren die voldoen aan strenge industriële normen voor vlam, rook en toxiciteit. Deze vooruitgangen stellen de snelle prototyping van cabine-interieurs, ducting en andere componenten mogelijk waar gewichtsbesparing en naleving van regelgeving van cruciaal belang zijn.
Vooruitkijkend zijn de vooruitzichten voor rapid prototyping in de luchtvaart gekarakteriseerd door voortdurende materiaalinovatie en procesintegratie. De convergentie van digitaal ontwerp, geavanceerde materialen en additive manufacturing zal naar verwachting de ontwikkelingstijden verder verminderen en meer wendbare reacties op evoluerende luchtvaartvereisten mogelijk maken. Industrieorganisaties zoals SAE International ontwikkelen actief normen om de kwalificatie en certificering van snel geprototypte componenten te ondersteunen, en zorgen voor veiligheid en betrouwbaarheid naarmate de adoptie versnelt door 2025 en in de latere jaren van het decennium.
Adoptie door Vooruitstrevende Luchtvaart-OEM’s en Tier 1 Leveranciers
De adoptie van rapid prototyping-technologieën door vooraanstaande luchtvaart-OEM’s en Tier 1 leveranciers is merkbaar versneld in 2025, gedreven door de noodzaak voor snellere ontwikkelingcycli, kostenefficiëntie en de toenemende complexiteit van luchtvaart- en ruimtevaartsystemen van de volgende generatie. Belangrijke spelers in de sector maken gebruik van additive manufacturing (AM), geavanceerde CNC-frezen en hybride prototypingmethoden om het ontwerp- tot productietraject voor cruciale componenten te stroomlijnen.
Airbus breidt zijn gebruik van rapid prototyping verder uit in zijn commerciële en defensieprogramma’s. In 2025 heeft Airbus geavanceerde metaal-additive manufacturing geïntegreerd voor zowel structurele als cabinecomponenten, waardoor snellere iteratie en validatie van onderdelen zoals beugels, luchtkanalen en zelfs dragende elementen mogelijk wordt. De locaties van het bedrijf in Filton en Hamburg hebben gerapporteerd dat de doorlooptijden voor prototype onderdelen zijn verminderd van enkele weken tot slechts een paar dagen, wat de wendbare ontwikkeling voor de A320neo en A350-families ondersteunt.
Boeing heeft zijn rapid prototyping-capaciteiten ook opgeschaald, vooral ter ondersteuning van zijn ecoDemonstrator- en nieuwe commerciële vliegtuiginitiatieven. Het gebruik van rapid prototyping door Boeing strekt zich uit tot zowel polymeer- als metaal-AM, met een focus op functionele tests en vluchtklare hardware. De partnerschappen van het bedrijf met toonaangevende AM-apparatuurleveranciers en materiaalontwikkelaars hebben de productie van complexe geometrieën en lichtgewicht structuren mogelijk gemaakt, die nu worden gevalideerd voor gebruik in zowel commerciële als defensieve platforms.
Onder Tier 1-leveranciers staan Safran en GE Aerospace vooraan in de adoptie van rapid prototyping. Safran heeft digitale thread- en rapid prototyping-werkstromen geïmplementeerd voor motorcomponenten, landingsgestellen en avionica-behuizingen, wat resulteert in significante reduceringen in ontwikkeltijd en verbeterde ontwerpflexibiliteit. GE Aerospace, een pionier in additive manufacturing voor onderdelen van jetmotoren, heeft zijn prototypingoperaties uitgebreid om hybride manufacturing en snelle gereedschapsproductie te omvatten, ter ondersteuning van zowel nieuwe motorprogramma’s als oplossingen voor de aftermarket.
De vooruitzichten voor de komende jaren suggereren een verdere integratie van rapid prototyping in de reguliere luchtvaartfabricage. OEM’s en leveranciers investeren in grotere-format AM-systemen, multi-materiaal capaciteiten en digitale simulatiehulpmiddelen om end-to-end digitale prototyping mogelijk te maken. Industrieorganisaties zoals SAE International actualiseren normen om de groeiende rol van rapid prototyping in certificerings- en kwalificatieprocessen weer te geven. Als gevolg hiervan staat de luchtvaartsector op het punt om een nog grotere wendbaarheid, innovatie en kostenbesparingen te realiseren door de voortdurende adoptie van rapid prototyping-technologieën.
Regelgevende en Certificeringsuitdagingen voor Geprototypte Componenten
De snelle adoptie van prototyping-technologieën, met name additive manufacturing (AM), in de luchtvaart hershape de regelgevende en certificeringslandschap in 2025. Terwijl luchtvaartfabrikanten steeds vaker gebruik maken van rapid prototyping voor zowel metalen als polymeercomponenten, werken regelgevende instanties en industriekrachten samen om certificeringskaders aan te passen om veiligheid, betrouwbaarheid en traceerbaarheid te waarborgen.
Een primaire uitdaging is de afstemming van rapid prototypingprocessen met de strenge luchtvaartcertificeringsnormen. Traditionele certificeringspaden, zoals die gedefinieerd door de Federal Aviation Administration (FAA) en de European Union Aviation Safety Agency (EASA), zijn ontwikkeld voor conventionele vervaardigingsmethoden. Deze normen vereisen uitgebreide documentatie, herhaalbaarheid en materiaaltraceerbaarheid—gebieden waar rapid prototyping, met name AM, nieuwe complexiteit introduceert. Bijvoorbeeld, de laag-voor-laag aard van AM kan resulteren in unieke microstructuren en potentiële variabiliteit tussen builds, wat nieuwe benaderingen van proceskwalificatie en componentvalidatie vereist.
In 2025 werken regelgevende agentschappen actief samen met leidinggevende industrie om richtlijnen te ontwikkelen en verfijnen die specifiek zijn voor geprototypte en additief vervaardigde componenten. De FAA blijft zijn richtlijnen over AM actualiseren, met een focus op procescontrole, inspectie en databeheer. Evenzo werkt EASA samen met fabrikanten om beste praktijken vast te stellen voor de certificering van AM-onderdelen, met de nadruk op de noodzaak van robuuste kwaliteitsborging en digitale documentatie.
Belangrijke luchtvaart-OEM’s en leveranciers, zoals Boeing, Airbus, en GE Aerospace, staan vooraan in deze inspanningen. Deze bedrijven investeren in interne certificeringsteams en digitale infrastructuur om de kwalificatie van geprototypte componenten te stroomlijnen. Bijvoorbeeld, GE Aerospace heeft de certificering van 3D-geprinte brandstofinjectoren gepionierd en blijft nauw samenwerken met toezichthouders om het scala aan certificeerbare AM-onderdelen uit te breiden.
Industrieorganisaties zoals SAE International en ASTM International spelen ook een cruciale rol bij het ontwikkelen van consensusnormen voor AM-processen, materialen en testprotocollen. Deze normen worden steeds vaker door zowel regelgevers als fabrikanten verwezen naar om conformiteit aan te tonen en het certificeringsproces te vergemakkelijken.
Vooruitkijkend, zijn de vooruitzichten voor regelgevende en certificeringskaders in rapid prototyping er een van voorzichtige optimisme. Hoewel aanzienlijke vooruitgang is geboekt, zal voortdurende samenwerking tussen regelgevers, fabrikanten en norminstellingen essentieel zijn om in te spelen op evoluerende technologieën en ervoor te zorgen dat veiligheid en betrouwbaarheid van het grootste belang blijven naarmate rapid prototyping meer geïntegreerd raakt in de ontwikkeling van luchtvaartcomponenten.
Casestudies: Succesvolle Rapid Prototyping in Vliegtuigen en Ruimteschepen
In de afgelopen jaren is rapid prototyping een hoeksteen van innovatie geworden in de luchtvaartsector, wat snellere ontwikkelingcycli, kostenbesparingen en verbeterde ontwerpflexibiliteit mogelijk maakt. Verschillende spraakmakende casestudies uit 2024 tot 2025 illustreren de transformerende impact van deze technologieën op zowel de ontwikkeling van vliegtuig- als ruimteschipcomponenten.
Een opmerkelijk voorbeeld is het gebruik van additive manufacturing (AM) door Airbus in de productie van structurele componenten voor commerciële vliegtuigen. In 2024 meldde Airbus de succesvolle integratie van 3D-geprinte titanium beugels in de A350 XWB, waardoor het gewicht van onderdelen met tot 30% werd verminderd en de doorlooptijden voor de levering van componenten werden verkort. Het bedrijf blijft zijn gebruik van rapid prototyping uitbreiden voor zowel metalen als polymeren, met lopende projecten gericht op het certificeren van meer complexe dragende structuren voor de vlucht in 2025.
Evenzo heeft Boeing rapid prototyping benut om de ontwikkeling van kritische systemen voor zijn volgende generatie vliegtuigen te versnellen. In 2024 hebben ingenieurs van Boeing geavanceerde 3D-printtechnologie gebruikt om ducts voor het milieubeheersysteem te prototypen en testen, met een vermindering van 50% in ontwikkelingstijd vergeleken met traditionele methoden. Het bedrijf werkt ook samen met leveranciers om nieuwe hoogwaardige materialen voor additive manufacturing te kwalificeren, met als doel het aandeel van 3D-geprinte onderdelen in toekomstige vliegtuigmodellen te verhogen.
In de wereld van de ruimteverkenning is NASA voorloper geweest in rapid prototyping voor ruimteschipcomponenten. Het Artemis-programma, gericht op maanmissies in het midden van de jaren 2020, heeft zwaar beroep gedaan op rapid prototyping om ontwerpen voor raketmotoronderdelen, crewmodule-structuren en levensondersteuningssystemen te itereren. In 2024 testte NASA met succes een 3D-geprinte verbrandingskamer voor de RS-25-motor, en demonstreerde een prestatiegelijkheid met conventioneel vervaardigde tegenhangers, terwijl de productie tijd van maanden tot weken werd verminderd.
Ook particuliere ruimtebedrijven omarmen rapid prototyping. SpaceX heeft additive manufacturing geïntegreerd in de productie van SuperDraco-thrusters en andere kritische componenten voor het Dragon-ruimtevaartuig. De rapid prototyping-capaciteiten van het bedrijf hebben snelle ontwerpitraties en versnelde testcycli mogelijk gemaakt, wat bijdraagt aan de betrouwbaarheid en herbruikbaarheid van zijn lanceervoertuigen.
Met het oog op 2025 en daarna, wordt verwacht dat de adoptie van rapid prototyping in de luchtvaart zal toenemen, gedreven door vooruitgangen in materiaalkunde, procesautomatisering en digitale ontwerptools. Brancheleiders investeren in grotere additive manufacturing-systemen en digitale tweelingen om de overgang van prototype naar gecertificeerde vluchthardware verder te stroomlijnen. Naarmate regelgevende kaders evolueren om deze nieuwe technologieën te accommoderen, zal rapid prototyping een belangrijke drijfveer blijven voor innovatie en concurrentievermogen in de luchtvaartsector.
Concurrentielandschap: Sleutelfiguren en Strategische Partnerschappen
Het concurrentielandschap voor rapid prototyping van luchtvaartcomponenten wordt gekenmerkt door een dynamische interactie tussen gevestigde luchtvaartfabrikanten, geavanceerde materiaalleveranciers en gespecialiseerde additive manufacturing (AM) technologieproviders. Vanaf 2025 getuigt de sector van een verscherpte samenwerking en strategische partnerschappen, gericht op het versnellen van innovatie, het verlagen van doorlooptijden en het verbeteren van de prestaties van cruciale componenten.
Belangrijke luchtvaart-OEM’s zoals Boeing en Airbus blijven zwaar investeren in rapid prototypingcapaciteiten, zowel intern als door middel van allianties. Boeing heeft zijn gebruik van additive manufacturing voor prototyping en laagvolume productie uitgebreid, gebruikmakend van partnerschappen met toonaangevende AM-technologiebedrijven om de ontwikkeling van complexe onderdelen voor commerciële en defensieve platforms te stroomlijnen. Evenzo heeft Airbus rapid prototyping geïntegreerd in zijn digitale manufacturing-ecosysteem, waarbij het samenwerkt met leveranciers om de kwalificatie van nieuwe materialen en processen voor vluchtkritische componenten te versnellen.
Op technologisch gebied zijn bedrijven zoals Stratasys en 3D Systems prominente aanbieders van industriële 3D-printoplossingen die zijn afgestemd op luchtvaarttoepassingen. Stratasys heeft partnerschappen opgebouwd met luchtvaartleveranciers om hoogwaardige polymeer- en composietprototypes te leveren, terwijl 3D Systems zich richt op metaal additive manufacturing voor functionele prototyping en gereedschappen. Beide bedrijven investeren in nieuwe materialen en procescertificering om te voldoen aan strenge luchtvaartnormen.
Materiaalinovatie is een andere concurrentiële as, waarbij bedrijven zoals Honeywell en GE Aerospace dubbele rollen spelen als zowel eindgebruikers als ontwikkelaars van geavanceerde legeringen en composieten voor rapid prototyping. GE Aerospace heeft de vooruitgang in additive manufacturing voor de prototyping van componenten van jetmotoren aanzienlijk verbeterd, vaak in samenwerking met AM-specialisten en onderzoeksinstellingen.
Strategische partnerschappen bepalen steeds meer de koers van de sector. Zo heeft Safran joint development-overeenkomsten gesloten met AM-technologieproviders voor de gezamenlijke ontwikkeling van rapid prototyping-oplossingen voor voortstuwings- en landingsgestelsystemen. Evenzo werkt Rolls-Royce samen met een netwerk van leveranciers en technologiepartners om de prototyping en validatie van onderdelen van de volgende generatie motoren te versnellen.
Vooruitkijkend wordt verwacht dat het concurrentielandschap verder zal consolideren rondom geïntegreerde digitale productieplatforms, waarbij sleutelfiguren strategische allianties aangaan om de veerkracht van de toeleveringsketen, certificeringsuitdagingen en de groeiende vraag naar duurzame materialen aan te pakken. De komende jaren zullen waarschijnlijk meer investeringen zien in automatisering, datagestuurd ontwerp en cross-industry partnerschappen, waardoor rapid prototyping als een hoeksteen van luchtvaartinnovatie kan fungeren.
Toekomstige Vooruitzichten: Opkomende Technologieën en Marktverstoorders
De toekomst van rapid prototyping voor luchtvaartcomponenten staat op het punt van significante transformatie, aangezien opkomende technologieën en marktverstoorders het landschap van de industrie in 2025 en daarna hervormen. De samenkomst van geavanceerde additive manufacturing (AM), digitaal engineering en nieuwe materialen versnelt het tempo waarin luchtvaartbedrijven complexe onderdelen kunnen ontwerpen, testen en itereren.
Een belangrijke drijfveer is de rijping van metaal-additive manufacturing, met name laserpoederbedfusie (LPBF) en elektronenstraalsmelting (EBM), die nu wordt toegepast voor zowel prototyping als eindgebruikcomponenten. Belangrijke luchtvaart-OEM’s zoals Boeing en Airbus hebben hun interne AM-capaciteiten uitgebreid, gebruikmakend van rapid prototyping om doorlooptijden voor cruciale onderdelen te verkorten en wendbare ontwikkelingscycli te ondersteunen. Zo heeft Airbus AM geïntegreerd in zijn digitale ontwerp- tot productie-werkflow, waardoor de snelle validatie van nieuwe geometrieën en lichtgewicht structuren voor vliegtuigmodellen van de volgende generatie mogelijk wordt.
Leveranciers zoals GE Aerospace en Rolls-Royce investeren ook in rapid prototyping om de ontwikkeling van geavanceerde voortstuwingssystemen te versnellen. GE Aerospace heeft het gebruik van AM gedemonstreerd voor prototyping en productie van complexe motorcomponenten, zoals brandstofinjectoren en warmtewisselaars, die profiteren van minder assemblagestappen en verbeterde prestaties. Ondertussen verkent Rolls-Royce hybride productiebenaderingen die additieve en subtractieve processen combineren om zowel snelheid als precisie te optimaliseren.
De adoptie van digitale tweelingen en simulatiegedreven ontwerp is een andere ontwrichtende trend. Door rapid prototyping te integreren met realtime data-analyse en virtueel testen, kunnen bedrijven ontwerpen sneller itereren en het aantal fysieke prototypes dat nodig is verminderen. NASA is voorloper in deze aanpak, waarbij digitale engineering wordt gebruikt om de prototyping van ruimteschipcomponenten te stroomlijnen en de prestaties onder extreme omstandigheden te valideren.
Vooruitkijkend zal de opkomst van nieuwe materialen—zoals thermohittebestendige polymeren, geavanceerde keramiek en functioneel gegradeerde legeringen—de mogelijkheden van rapid prototyping verder uitbreiden. Bedrijven zoals Stratasys en 3D Systems ontwikkelen gespecialiseerde AM-platforms die zijn afgestemd op luchtvaarttoepassingen en de productie van lichtgewicht, hoogsterke onderdelen met complexe interne structuren ondersteunen.
Naarmate regelgevende kaders zich ontwikkelen om additive manufacturing en digitale certificering te accommoderen, wordt verwacht dat de luchtvaartsector bredere adoptie van rapid prototyping zal zien voor zowel commerciële als defensietoepassingen. De komende jaren zullen waarschijnlijk meer samenwerking tussen OEM’s, leveranciers en technologieproviders veroorzaken, wat innovatie zal stimuleren en de time-to-market voor nieuwe luchtvaartcomponenten zal verminderen.
Aanbevelingen: Strategische Acties voor Belanghebbenden in 2025 en Verder
Naarmate rapid prototyping blijft transformeren in de ontwikkeling van luchtvaartcomponenten, moeten belanghebbenden strategische acties aannemen om concurrerend en innovatief te blijven in 2025 en verder. De volgende aanbevelingen zijn gericht op luchtvaartfabrikanten, leveranciers en technologiepartners die de voordelen van rapid prototyping-technologieën willen maximaliseren.
- Investeer in Geavanceerde Additive Manufacturing Capaciteiten: Luchtvaartbedrijven moeten prioriteit geven aan investeringen in state-of-the-art additive manufacturing (AM) systemen, zoals laserpoederbedfusie en elektronenstraalsmelting, die steeds vaker worden gebruikt voor prototyping en eindgebruikcomponenten. Vooruitstrevende luchtvaart-OEM’s zoals Airbus en Boeing hebben hun interne AM-capaciteiten uitgebreid, wat snellere iteratie en verminderde doorlooptijden voor complexe componenten mogelijk maakt.
- Versterk Samenwerking met Leveranciers en Digitale Integratie: Om prototypingcycli te versnellen, moeten belanghebbenden nauwere samenwerking met leveranciers en technologiepartners bevorderen. Digitale platformen en veilige gegevensuitwisselingsprotocollen zijn essentieel voor het delen van ontwerpbestanden en feedback in realtime. Bedrijven zoals Safran en GE Aerospace hebben digitale ecosystemen opgezet om prototyping- en kwalificatieprocessen in hun toeleveringsketens te stroomlijnen.
- Adopteer Agile Ontwerp- en Testmethodologieën: Rapid prototyping maakt iteratief ontwerp en testen mogelijk, waardoor het risico op kostbare wijzigingen in een laat stadium wordt verminderd. Luchtvaartorganisaties moeten agile ontwikkelingskaders implementeren, waarbij simulatie, virtueel testen en fysieke prototyping behoren. Rolls-Royce heeft de waarde van deze aanpak aangetoond door rapid prototyping te gebruiken om nieuwe motorcomponenten te valideren voordat volledige productie plaatsvindt.
- Focus op Opleiding van het Personeel en Talentontwikkeling: De adoptie van rapid prototyping-technologieën vereist een workforce die bekwaam is in digitaal ontwerp, AM-processen en kwaliteitsborging. Belanghebbenden moeten investeren in trainingsprogramma’s en partnerschappen met onderwijsinstellingen om expertise in deze gebieden op te bouwen, zoals blijkt uit initiatieven geleid door Lockheed Martin en NASA.
- Prioriteer Certificerings- en Standaardisatie-inspanningen: Naarmate de regelgevende vereisten zich ontwikkelen, moeten belanghebbenden samenwerken met brancheorganisaties om normen voor rapid prototyping in de luchtvaart te ontwikkelen en toe te passen. Deelname aan werkgroepen geleid door organisaties zoals SAE International en ANSI zal helpen ervoor te zorgen dat nieuwe prototypingmethoden voldoen aan veiligheidseisen en kwaliteitsnormen.
Door deze strategische acties te implementeren, kunnen luchtvaartbelanghebbenden rapid prototyping benutten om innovatie te versnellen, kosten te verlagen en compliant te blijven in een snel evoluerend technologisch landschap tot 2025 en in de komende jaren.
Bronnen & Referenties
- Airbus
- Boeing
- GE Aerospace
- Siemens
- Honeywell
- European Space Agency
- Lockheed Martin
- Northrop Grumman
- Stratasys
- 3D Systems
- Renishaw
- EOS
- Haas Automation
- DMG MORI
- Yamazaki Mazak
- TRUMPF
- GE Aerospace
- European Union Aviation Safety Agency
- ASTM International
- NASA
- Rolls-Royce
- ANSI