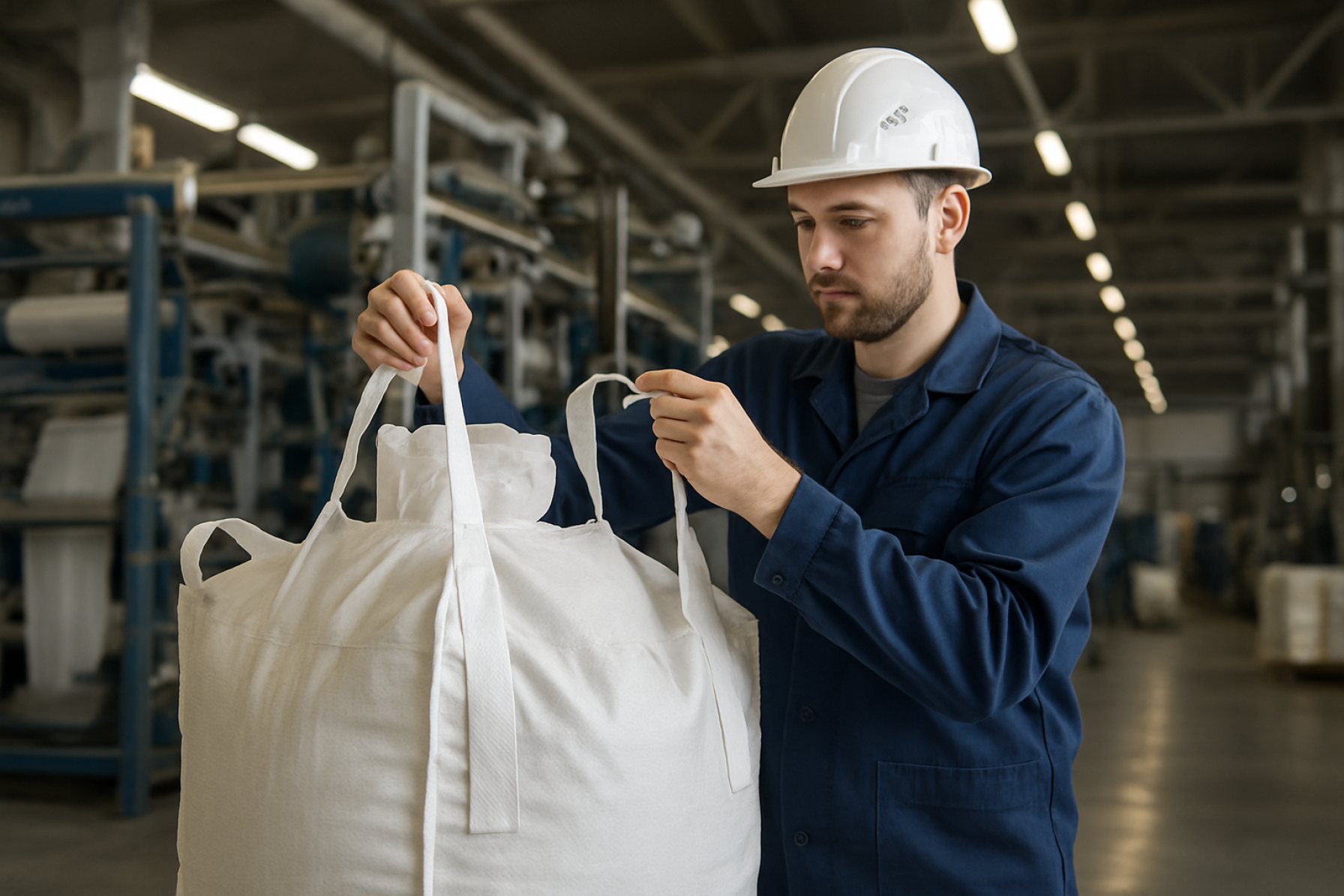
Jumbo Bag Manufacturing Industry Trends: How Innovation, Sustainability, and Global Demand Are Reshaping the Market. Discover What’s Driving the Next Wave of Growth in Bulk Packaging Solutions. (2025)
- Executive Summary: Key Takeaways and Market Momentum
- Global Market Size and Growth Forecasts Through 2030
- Emerging Technologies in Jumbo Bag Production
- Sustainability Initiatives and Eco-Friendly Materials
- Regional Trends: Asia-Pacific, Europe, and North America
- Major Players and Strategic Partnerships
- Regulatory Landscape and Compliance Standards
- End-User Industries: Agriculture, Chemicals, Construction, and More
- Challenges: Supply Chain, Raw Material Costs, and Labor
- Future Outlook: Innovation, Public Interest, and Projected 8–10% Annual Growth
- Sources & References
Executive Summary: Key Takeaways and Market Momentum
The jumbo bag manufacturing industry, also known as the FIBC (Flexible Intermediate Bulk Container) sector, is experiencing significant transformation in 2025, driven by evolving global supply chains, sustainability imperatives, and technological advancements. The industry’s momentum is underpinned by robust demand from sectors such as agriculture, chemicals, construction, and food processing, which rely on efficient bulk packaging solutions for storage and transportation.
A key trend shaping the market is the increasing adoption of sustainable materials and circular economy practices. Manufacturers are investing in recyclable polypropylene and exploring bio-based polymers to reduce environmental impact, aligning with global sustainability goals and regulatory pressures. This shift is particularly notable in regions with stringent packaging waste directives, such as the European Union, where compliance with the European Union’s packaging and packaging waste regulations is accelerating innovation in eco-friendly jumbo bags.
Automation and digitalization are also redefining production processes. The integration of Industry 4.0 technologies—such as automated cutting, sewing, and quality control systems—has improved operational efficiency and product consistency. Leading manufacturers are leveraging data analytics and IoT-enabled tracking to enhance supply chain transparency and traceability, responding to customer demands for real-time shipment monitoring and quality assurance.
Geographically, Asia-Pacific remains the dominant production and consumption hub, with countries like India and China expanding their manufacturing capacities to meet both domestic and export demand. This regional growth is supported by government initiatives to boost industrial output and infrastructure development, as seen in programs promoted by the Make in India campaign. Meanwhile, North America and Europe are witnessing steady demand, particularly for high-performance and food-grade FIBCs, driven by stringent safety and hygiene standards.
Looking ahead, the industry is expected to maintain a positive growth trajectory over the next few years. Key drivers include the expansion of global trade, the rise of e-commerce logistics, and ongoing investments in sustainable packaging solutions. However, manufacturers must navigate challenges such as fluctuating raw material prices and evolving regulatory landscapes. Strategic partnerships, R&D in advanced materials, and digital transformation will be critical for companies aiming to capture emerging opportunities and sustain competitive advantage in the dynamic jumbo bag market.
Global Market Size and Growth Forecasts Through 2030
The global jumbo bag manufacturing industry, also known as the Flexible Intermediate Bulk Container (FIBC) sector, is experiencing robust growth as it adapts to evolving demands in logistics, agriculture, chemicals, and food sectors. As of 2025, the industry is valued at several billion USD, with projections indicating a compound annual growth rate (CAGR) in the mid to high single digits through 2030. This expansion is driven by the increasing need for efficient, cost-effective, and sustainable bulk packaging solutions worldwide.
Key growth regions include Asia-Pacific, Europe, and North America. The Asia-Pacific region, led by manufacturing powerhouses such as India and China, continues to dominate global production and consumption. This is due to the region’s expanding industrial base, rising export activities, and the presence of major FIBC manufacturers. For instance, Flexituff Ventures International and Jumbo Bag Ltd. are among the leading companies headquartered in India, supplying to both domestic and international markets.
In Europe, stringent regulations on packaging waste and a strong focus on sustainability are shaping market trends. The European Union’s policies on circular economy and plastic waste reduction are prompting manufacturers to innovate with recyclable and reusable FIBC designs. North America, meanwhile, is witnessing steady demand from the chemicals and food processing industries, with companies like Greif and Berry Global playing significant roles in the region’s supply chain.
Technological advancements are also influencing the industry’s trajectory. Automation in manufacturing processes, adoption of high-strength and lightweight materials, and the integration of smart tracking features are enhancing product quality and operational efficiency. The use of UV-stabilized fabrics and food-grade liners is expanding the application scope of jumbo bags, particularly in sensitive sectors such as pharmaceuticals and food ingredients.
Looking ahead to 2030, the industry outlook remains positive. The global push for sustainable packaging, coupled with the growth of e-commerce and international trade, is expected to sustain demand for jumbo bags. Manufacturers are likely to invest further in R&D to develop eco-friendly materials and closed-loop recycling systems, aligning with global sustainability goals set by organizations such as the United Nations. As a result, the jumbo bag manufacturing industry is poised for continued expansion, with innovation and environmental stewardship at the forefront of its evolution.
Emerging Technologies in Jumbo Bag Production
The jumbo bag manufacturing industry is undergoing significant transformation in 2025, driven by the integration of emerging technologies and evolving market demands. One of the most notable trends is the adoption of automation and digitalization across production lines. Advanced robotics and automated cutting, sewing, and inspection systems are increasingly being implemented to enhance productivity, reduce labor costs, and improve product consistency. These technologies enable manufacturers to meet the growing demand for high-quality, customized flexible intermediate bulk containers (FIBCs) in sectors such as agriculture, chemicals, and construction.
Sustainability is another key driver shaping the industry. Manufacturers are investing in the development of eco-friendly jumbo bags by incorporating recycled polypropylene and biodegradable materials into their products. This shift is in response to stricter environmental regulations and the sustainability commitments of major end-users. For example, global chemical and agricultural companies are setting ambitious targets to reduce plastic waste and carbon emissions, prompting their suppliers to innovate in material sourcing and production processes. The use of life cycle assessment tools and environmental impact monitoring is becoming standard practice among leading producers.
Digital technologies are also transforming supply chain management within the jumbo bag sector. The integration of Internet of Things (IoT) sensors and RFID tags into FIBCs allows for real-time tracking of bags throughout the logistics chain, improving traceability, inventory management, and safety compliance. This is particularly important for industries handling hazardous materials, where regulatory requirements for packaging traceability are stringent. The adoption of blockchain technology is being explored to further enhance transparency and trust in the supply chain.
In terms of product innovation, manufacturers are focusing on developing high-performance jumbo bags with enhanced barrier properties, UV resistance, and anti-static features. These advancements are driven by the needs of industries such as pharmaceuticals and food processing, where product integrity and contamination prevention are critical. Research collaborations between manufacturers and polymer producers are accelerating the introduction of new material blends and coatings.
Looking ahead, the outlook for the jumbo bag manufacturing industry remains positive, with steady growth anticipated over the next few years. The sector is expected to benefit from ongoing investments in smart manufacturing, sustainability initiatives, and the expansion of global trade in bulk commodities. Organizations such as the United Nations Industrial Development Organization and the Plastics Industry Association are actively supporting innovation and best practices in industrial packaging, further driving the adoption of emerging technologies in jumbo bag production.
Sustainability Initiatives and Eco-Friendly Materials
The jumbo bag manufacturing industry is undergoing significant transformation in response to global sustainability imperatives and evolving regulatory frameworks. As of 2025, manufacturers are increasingly prioritizing eco-friendly materials and sustainable production processes to align with environmental goals and customer expectations.
A central trend is the adoption of recycled and bio-based polymers in the production of flexible intermediate bulk containers (FIBCs), commonly known as jumbo bags. Polypropylene (PP) remains the dominant material due to its strength and versatility, but there is a marked shift toward incorporating recycled PP and exploring alternatives such as polylactic acid (PLA) and other biodegradable polymers. This shift is driven by both regulatory pressures and voluntary commitments to reduce plastic waste and carbon footprints.
Major industry players are investing in closed-loop recycling systems, enabling the collection and reprocessing of used jumbo bags into new products. This approach not only conserves resources but also addresses the growing demand for circular economy solutions. For example, companies are collaborating with logistics and agricultural sectors to establish take-back programs, ensuring that used FIBCs are returned for recycling rather than disposed of in landfills.
In addition to material innovation, manufacturers are optimizing production processes to minimize energy consumption and emissions. The use of renewable energy sources, such as solar and wind, is becoming more prevalent in manufacturing facilities. Furthermore, advancements in weaving and coating technologies are reducing material waste and improving the durability and reusability of jumbo bags, extending their lifecycle and reducing overall environmental impact.
Regulatory bodies and international organizations are playing a pivotal role in shaping industry practices. The International Organization for Standardization (ISO) has established standards for FIBC safety and environmental performance, encouraging manufacturers to adopt best practices. Additionally, the United Nations Environment Programme (UNEP) continues to advocate for reduced plastic pollution and supports initiatives that promote sustainable packaging solutions.
Looking ahead, the outlook for the jumbo bag manufacturing industry is characterized by continued innovation in sustainable materials and processes. Stakeholders anticipate stricter regulations on single-use plastics and increased demand for traceable, eco-friendly packaging. As a result, companies that invest in sustainability initiatives are likely to gain a competitive advantage, meeting both regulatory requirements and the preferences of environmentally conscious customers.
Regional Trends: Asia-Pacific, Europe, and North America
The jumbo bag manufacturing industry, also known as the FIBC (Flexible Intermediate Bulk Container) sector, is experiencing distinct regional trends across Asia-Pacific, Europe, and North America as of 2025. These trends are shaped by evolving industrial demands, regulatory frameworks, and sustainability initiatives.
Asia-Pacific remains the dominant force in jumbo bag production, driven by rapid industrialization, robust export-oriented manufacturing, and the presence of major producers in countries such as India, China, and Vietnam. India, in particular, has established itself as a global hub for FIBC manufacturing, leveraging cost-effective labor, a strong textile base, and increasing investments in automation. The region’s growth is further propelled by rising demand from the chemicals, agriculture, and construction sectors. According to the Flexible Intermediate Bulk Container Association (FIBCA), Asia-Pacific accounts for the majority of global FIBC exports, with Indian manufacturers supplying to over 50 countries. The region is also witnessing a shift toward higher-quality, food-grade, and UN-certified bags to meet international standards.
Europe is characterized by stringent regulatory requirements and a strong emphasis on sustainability. The European Union’s focus on circular economy principles and plastic waste reduction is influencing manufacturers to adopt recycled materials and eco-friendly production processes. European FIBC producers are investing in advanced technologies for traceability, quality assurance, and compliance with REACH and food safety regulations. The European Recycling Industries’ Confederation (EuRIC) and other industry bodies are actively promoting the use of recycled polypropylene in FIBC manufacturing. Additionally, the region is seeing increased demand for specialized bags, such as conductive and food-safe variants, to serve the pharmaceutical and food processing industries.
North America is experiencing steady growth in the jumbo bag market, supported by the expansion of the chemical, agricultural, and mining sectors. The United States and Canada are focusing on supply chain resilience and domestic manufacturing capabilities, partly in response to recent global disruptions. North American manufacturers are adopting automation and digitalization to enhance efficiency and traceability. There is also a growing emphasis on compliance with safety and environmental standards set by organizations such as the Occupational Safety and Health Administration (OSHA) and the Environmental Protection Agency (EPA). Sustainability is gaining traction, with increased interest in reusable and recyclable FIBCs, though regulatory pressure is less pronounced than in Europe.
Looking ahead, the jumbo bag manufacturing industry across these regions is expected to see continued innovation in materials, automation, and sustainability practices. Regional differences in regulation and market demand will shape the pace and direction of these trends through 2025 and beyond.
Major Players and Strategic Partnerships
The jumbo bag manufacturing industry, also known as the FIBC (Flexible Intermediate Bulk Container) sector, is witnessing significant consolidation and strategic collaboration among major players as of 2025. Leading manufacturers are expanding their global footprints and investing in advanced production technologies to meet rising demand from sectors such as agriculture, chemicals, construction, and food processing. Notable companies in this space include Flexible Intermediate Bulk Container Association (FIBCA) members, which represent a broad spectrum of global FIBC producers and suppliers.
Key industry leaders such as Jumbo Bag Limited and BAG Corp have been at the forefront of innovation, focusing on sustainability and product customization. These companies are increasingly forming strategic partnerships with raw material suppliers and logistics providers to streamline supply chains and ensure consistent quality. For instance, collaborations with polymer manufacturers have enabled the development of lighter, stronger, and more recyclable FIBC materials, aligning with global sustainability goals.
In 2025, the industry is also seeing a trend toward vertical integration, with major players acquiring or partnering with companies in adjacent sectors such as woven polypropylene production and bulk logistics. This approach helps reduce costs, improve quality control, and enhance responsiveness to market fluctuations. Additionally, alliances with international distributors are enabling manufacturers to penetrate emerging markets in Asia, Africa, and South America, where demand for bulk packaging solutions is growing rapidly.
Trade associations like the Flexible Intermediate Bulk Container Association play a pivotal role in fostering industry collaboration, setting safety and quality standards, and facilitating knowledge exchange among members. These organizations also advocate for regulatory harmonization, which is crucial as manufacturers navigate varying compliance requirements across regions.
Looking ahead, the outlook for the jumbo bag manufacturing industry is shaped by ongoing investments in automation, digitalization, and sustainable materials. Strategic partnerships—whether through joint ventures, technology sharing, or supply chain integration—are expected to intensify as companies seek to differentiate themselves and address evolving customer needs. The continued emphasis on environmental responsibility and operational efficiency will likely drive further innovation and consolidation among the sector’s major players in the coming years.
Regulatory Landscape and Compliance Standards
The regulatory landscape for the jumbo bag (Flexible Intermediate Bulk Container, or FIBC) manufacturing industry is evolving rapidly in 2025, shaped by increasing global trade, heightened safety expectations, and a growing emphasis on sustainability. Regulatory bodies and standards organizations are playing a pivotal role in defining compliance requirements, particularly concerning material safety, environmental impact, and product traceability.
A central standard for FIBC manufacturing is the ISO 21898, which specifies requirements for the design, testing, and use of flexible intermediate bulk containers. This standard is widely referenced by manufacturers and regulatory authorities to ensure product safety and performance. In 2025, updates to ISO 21898 are under discussion, focusing on enhanced traceability and recyclability of materials, reflecting the industry’s shift toward circular economy principles. The International Organization for Standardization (ISO) continues to be the primary body overseeing these developments.
In the European Union, the European Commission enforces the Registration, Evaluation, Authorisation and Restriction of Chemicals (REACH) regulation, which impacts the selection of raw materials for jumbo bags, particularly regarding additives and colorants. Compliance with REACH is mandatory for manufacturers exporting to or operating within the EU, and recent amendments have tightened restrictions on certain phthalates and heavy metals, pushing manufacturers toward safer alternatives.
The United States, through agencies such as the Occupational Safety and Health Administration (OSHA) and the Environmental Protection Agency (EPA), enforces standards related to workplace safety and environmental protection. OSHA’s regulations on material handling and storage, as well as EPA’s guidelines on plastic waste management, are increasingly relevant as the industry faces scrutiny over microplastics and end-of-life disposal of FIBCs.
Globally, the United Nations Recommendations on the Transport of Dangerous Goods (the “Orange Book”) set out requirements for packaging hazardous materials, including FIBCs. Compliance with these recommendations is essential for manufacturers serving the chemicals, pharmaceuticals, and food sectors, where safe transport is critical.
Looking ahead, the regulatory outlook for the jumbo bag industry points toward stricter environmental standards, increased demand for recycled and recyclable materials, and digital traceability systems to ensure supply chain transparency. Manufacturers are expected to invest in advanced testing, certification, and documentation processes to meet evolving compliance requirements and maintain market access in key regions.
End-User Industries: Agriculture, Chemicals, Construction, and More
The jumbo bag manufacturing industry, also known as the FIBC (Flexible Intermediate Bulk Container) sector, is experiencing notable shifts in end-user demand and product innovation as it enters 2025. Key industries driving growth include agriculture, chemicals, construction, food, and pharmaceuticals, each with evolving requirements that shape manufacturing trends.
In agriculture, the demand for jumbo bags is rising due to the global emphasis on food security and efficient bulk handling of grains, seeds, and fertilizers. The adoption of advanced packaging solutions is particularly strong in regions with large-scale agribusiness operations, such as India and Brazil. Manufacturers are responding by developing bags with enhanced UV protection and moisture barriers to preserve product quality during storage and transport.
The chemicals sector remains a major consumer of jumbo bags, especially for the safe movement of powders, granules, and hazardous materials. Regulatory compliance is a significant driver, with manufacturers focusing on anti-static and conductive FIBC designs to meet international safety standards. Organizations such as the International Organization for Standardization (ISO) continue to update guidelines for packaging hazardous goods, prompting ongoing innovation in bag construction and testing.
Construction industry trends are also influencing the jumbo bag market. The global push for infrastructure development, particularly in Asia and the Middle East, is increasing the need for robust packaging for cement, sand, and aggregates. Manufacturers are introducing heavy-duty FIBCs with reinforced seams and higher load capacities to cater to these requirements. Additionally, the shift toward sustainable construction practices is encouraging the use of recyclable and reusable jumbo bags.
Food and pharmaceutical industries are driving demand for hygienic, contamination-resistant packaging. Compliance with food safety standards, such as those set by the U.S. Food and Drug Administration (FDA) and the European Food Safety Authority (EFSA), is leading to the adoption of food-grade FIBCs with advanced liners and tamper-evident features. Traceability and batch tracking are becoming standard, supported by digital labeling and RFID integration.
Looking ahead, sustainability is a cross-sector trend. End-users increasingly demand eco-friendly materials and closed-loop recycling systems. Industry groups like the European Bioplastics are advocating for biopolymer-based FIBCs, and several manufacturers are piloting bags made from recycled polypropylene. As regulatory and consumer pressures mount, the industry is expected to accelerate the adoption of greener solutions through 2025 and beyond.
Challenges: Supply Chain, Raw Material Costs, and Labor
The jumbo bag manufacturing industry, a critical segment within the global packaging sector, faces a complex array of challenges in 2025, particularly concerning supply chain disruptions, raw material costs, and labor dynamics. These factors are shaping both operational strategies and long-term outlooks for manufacturers worldwide.
Supply Chain Disruptions
The industry remains highly sensitive to global supply chain volatility. The COVID-19 pandemic exposed vulnerabilities in logistics and transportation, and while some recovery has occurred, ongoing geopolitical tensions and regional conflicts continue to disrupt the flow of raw materials and finished goods. For instance, the Red Sea shipping crisis and port congestion in major hubs have led to increased lead times and unpredictable delivery schedules. Manufacturers are responding by diversifying supplier bases and investing in digital supply chain management tools to enhance resilience. Organizations such as the International Chamber of Commerce have highlighted the need for greater supply chain transparency and risk mitigation strategies across the packaging sector.
Raw Material Costs
Jumbo bags, also known as FIBCs (Flexible Intermediate Bulk Containers), are primarily made from woven polypropylene, a derivative of crude oil. In 2025, fluctuations in global oil prices and ongoing supply constraints for petrochemicals have led to significant volatility in polypropylene costs. According to the Plastics Industry Association, the price of polypropylene has seen periodic spikes due to refinery outages, increased demand from competing sectors, and regulatory changes affecting plastic production. This cost pressure is prompting manufacturers to explore alternative materials, increase recycling rates, and negotiate long-term contracts with suppliers to stabilize input costs.
Labor Market Pressures
The industry is also grappling with labor shortages and rising wage demands, particularly in regions where jumbo bag production is concentrated, such as South and Southeast Asia. The International Labour Organization has reported that manufacturing sectors in these regions are experiencing increased competition for skilled workers, driven by urbanization and the growth of alternative employment opportunities. To address these challenges, companies are investing in automation, workforce training, and improved working conditions to attract and retain talent.
Outlook
Looking ahead, the jumbo bag manufacturing industry is expected to continue facing these intertwined challenges. Success will depend on the ability of manufacturers to adapt through supply chain innovation, cost management, and workforce development. Industry associations and global organizations are likely to play a pivotal role in facilitating best practices and supporting sector resilience in the coming years.
Future Outlook: Innovation, Public Interest, and Projected 8–10% Annual Growth
The jumbo bag manufacturing industry, also known as the FIBC (Flexible Intermediate Bulk Container) sector, is poised for robust growth in 2025 and the following years, with annual expansion rates projected between 8% and 10%. This outlook is driven by a confluence of innovation, heightened public and regulatory interest in sustainable packaging, and expanding demand from key end-use industries such as agriculture, chemicals, construction, and food processing.
A central trend shaping the industry is the accelerated adoption of advanced materials and manufacturing technologies. Producers are increasingly investing in automation, digital quality control, and high-performance polymers to enhance bag strength, reduce weight, and improve recyclability. The integration of smart manufacturing systems—such as IoT-enabled monitoring for quality assurance and traceability—has begun to transform production lines, enabling greater efficiency and consistency. These innovations are supported by global organizations like the United Nations Industrial Development Organization, which promotes sustainable industrialization and the adoption of cleaner technologies in manufacturing.
Sustainability is a defining theme for the industry’s future. Public interest in reducing plastic waste and carbon footprints has prompted manufacturers to develop recyclable and reusable jumbo bags, as well as to explore bio-based polymers. Regulatory frameworks in major markets, including the European Union and India, are increasingly mandating eco-friendly packaging solutions, further accelerating this shift. The European Union has set ambitious targets for packaging recyclability and waste reduction, directly influencing the design and lifecycle management of FIBCs.
Market expansion is also fueled by the globalization of supply chains and the growing need for efficient bulk packaging in emerging economies. The World Trade Organization notes that international trade in agricultural and chemical products—key sectors utilizing jumbo bags—continues to rise, necessitating reliable and scalable packaging solutions. Additionally, the construction sector’s recovery and infrastructure investments in Asia and Africa are expected to boost demand for FIBCs.
Looking ahead, the industry is likely to see increased collaboration between manufacturers, material science innovators, and regulatory bodies to meet evolving standards and consumer expectations. The convergence of digitalization, sustainability, and global trade dynamics positions the jumbo bag manufacturing sector for sustained growth, with leading companies and industry associations playing a pivotal role in shaping best practices and driving innovation.
Sources & References
- European Union
- Make in India
- Flexituff Ventures International
- Greif
- Berry Global
- United Nations
- United Nations Industrial Development Organization
- Plastics Industry Association
- International Organization for Standardization
- Flexible Intermediate Bulk Container Association
- European Recycling Industries’ Confederation
- Jumbo Bag Limited
- European Commission
- United Nations
- European Food Safety Authority
- European Bioplastics
- International Chamber of Commerce
- World Trade Organization