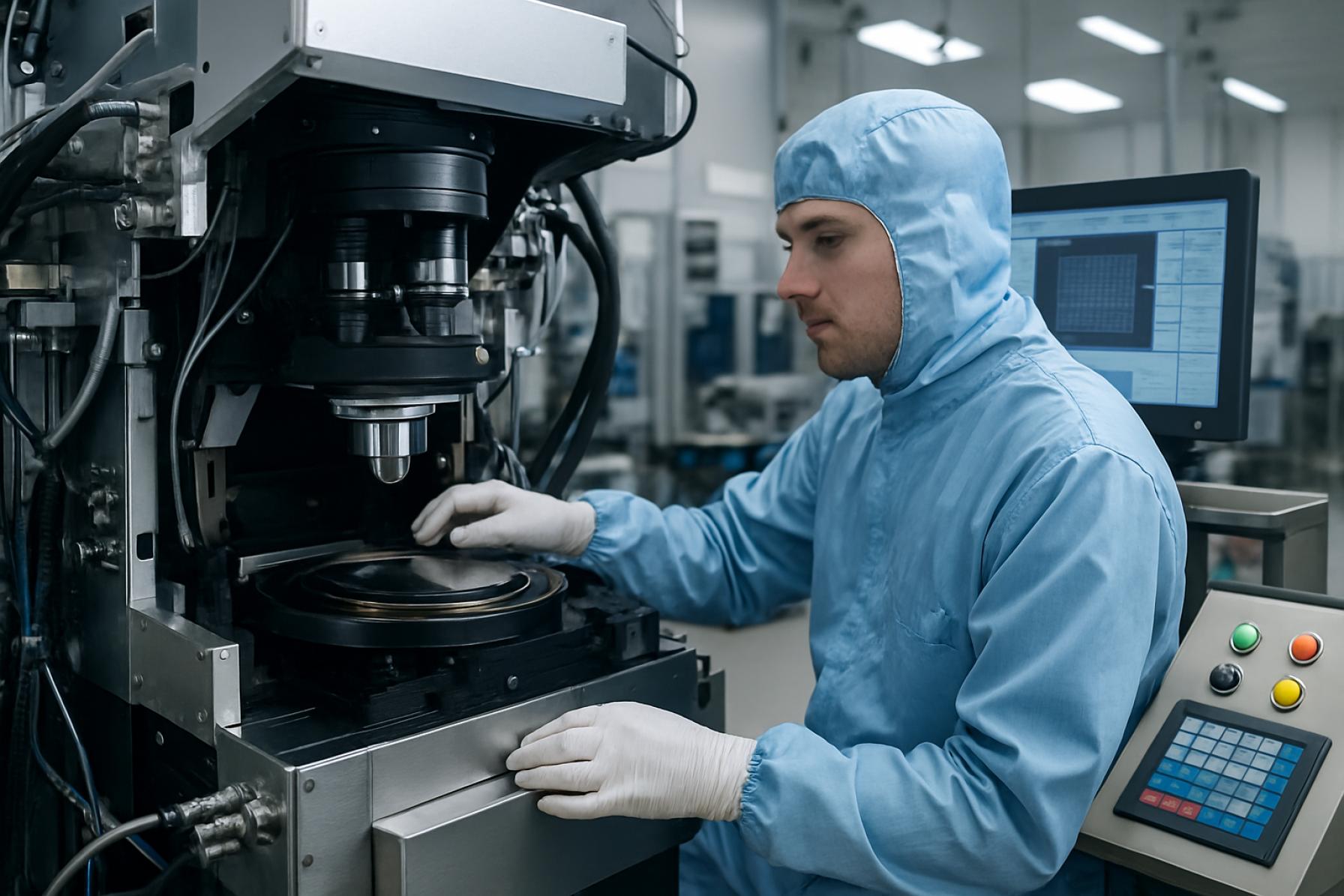
Photolithography Equipment Manufacturing in 2025: Unveiling the Next Wave of Semiconductor Innovation. Explore How Advanced Lithography Tools Are Powering the Future of Microchip Production and Market Expansion.
- Executive Summary: Key Trends and 2025 Outlook
- Market Size, Growth Rate, and 2025–2030 Forecasts
- Competitive Landscape: Leading Manufacturers and New Entrants
- Technological Innovations: EUV, DUV, and Beyond
- Supply Chain Dynamics and Geopolitical Impacts
- End-User Segments: Semiconductor, Display, and MEMS Applications
- Sustainability and Environmental Considerations in Equipment Manufacturing
- Regional Analysis: Asia-Pacific, North America, and Europe
- Investment, M&A, and Strategic Partnerships
- Future Outlook: Challenges, Opportunities, and Disruptive Trends
- Sources & References
Executive Summary: Key Trends and 2025 Outlook
The photolithography equipment manufacturing sector is entering 2025 amid robust demand, technological innovation, and significant geopolitical and supply chain pressures. Photolithography, a cornerstone of semiconductor fabrication, is dominated by a small group of highly specialized manufacturers, with ASML Holding as the clear global leader in extreme ultraviolet (EUV) and deep ultraviolet (DUV) lithography systems. The company’s EUV systems remain essential for advanced logic and memory chip production at nodes below 7nm, and its order backlog continues to grow, reflecting persistent demand from leading foundries and integrated device manufacturers.
In 2025, the industry is characterized by several key trends:
- Continued EUV Expansion: The transition to EUV lithography is accelerating, with major chipmakers such as TSMC, Samsung Electronics, and Intel Corporation expanding their EUV capacity to support advanced process nodes (3nm and below). ASML’s latest High-NA EUV systems, which promise even finer resolution, are expected to see initial deployment in pilot lines during 2025.
- DUV Demand Remains Strong: Despite the EUV shift, demand for DUV lithography equipment remains high, especially for mature nodes and specialty applications. Companies like Nikon Corporation and Canon Inc. continue to supply DUV systems, particularly to markets in China and Southeast Asia, where mature node production is expanding.
- Geopolitical and Supply Chain Dynamics: Export controls and trade restrictions, particularly those imposed by the United States and its allies, are impacting the supply of advanced photolithography equipment to certain regions, notably China. This is prompting efforts to localize equipment manufacturing and diversify supply chains, with Chinese firms accelerating R&D in domestic lithography technologies.
- Investment and Capacity Expansion: Major semiconductor manufacturers are investing heavily in new fabs and equipment, with multi-billion-dollar capital expenditure plans announced for 2025 and beyond. This is driving sustained order growth for photolithography equipment, though lead times remain extended due to component shortages and complex system integration.
Looking ahead, the photolithography equipment market is expected to maintain strong growth through 2025 and into the following years, underpinned by the global push for advanced semiconductor manufacturing, ongoing digital transformation, and the proliferation of AI, automotive, and IoT applications. However, the sector faces ongoing challenges related to technology complexity, supply chain resilience, and geopolitical uncertainty, which will shape the competitive landscape and innovation trajectory for the foreseeable future.
Market Size, Growth Rate, and 2025–2030 Forecasts
The photolithography equipment manufacturing sector is a cornerstone of the global semiconductor industry, underpinning the production of advanced integrated circuits. As of 2025, the market is experiencing robust growth, driven by surging demand for high-performance chips in applications such as artificial intelligence, 5G, automotive electronics, and data centers. The transition to advanced process nodes (5nm, 3nm, and beyond) is intensifying the need for cutting-edge photolithography tools, particularly extreme ultraviolet (EUV) systems.
Industry leaders such as ASML Holding, Canon Inc., and Nikon Corporation dominate the global photolithography equipment market. ASML Holding is the sole supplier of EUV lithography systems, which are essential for manufacturing at the most advanced nodes. The company reported net sales of €27.6 billion in 2023, with a significant portion attributed to EUV system shipments, and anticipates continued growth in 2025 as leading foundries and integrated device manufacturers (IDMs) ramp up investments in next-generation fabs.
The overall photolithography equipment market size is projected to surpass $20 billion in 2025, with a compound annual growth rate (CAGR) estimated between 8% and 10% through 2030. This expansion is fueled by aggressive capital expenditure plans from major semiconductor manufacturers, including Taiwan Semiconductor Manufacturing Company (TSMC), Samsung Electronics, and Intel Corporation, all of whom are investing heavily in advanced process technologies and new fabrication facilities.
Looking ahead to 2030, the market outlook remains positive. The proliferation of AI-driven applications, the rollout of 6G networks, and the electrification of vehicles are expected to sustain high demand for leading-edge chips, thereby supporting continued investment in photolithography equipment. The introduction of High-NA EUV systems, which promise even finer patterning capabilities, is anticipated to further boost market value and technological differentiation among equipment suppliers. ASML Holding has already announced plans to deliver its first High-NA EUV systems to customers in 2025, marking a significant technological milestone for the industry.
- 2025 market size: >$20 billion
- 2025–2030 CAGR: 8–10%
- Key drivers: AI, 5G/6G, automotive, advanced process nodes
- Leading suppliers: ASML Holding, Canon Inc., Nikon Corporation
- Major customers: TSMC, Samsung Electronics, Intel Corporation
Competitive Landscape: Leading Manufacturers and New Entrants
The competitive landscape of photolithography equipment manufacturing in 2025 is characterized by a small number of dominant players, significant technological barriers to entry, and a growing interest from new entrants, particularly in response to geopolitical and supply chain pressures. The sector is crucial for the semiconductor industry, as photolithography tools are essential for producing advanced integrated circuits.
The undisputed leader in the field is ASML Holding, headquartered in the Netherlands. ASML is the only company in the world capable of producing extreme ultraviolet (EUV) lithography machines, which are indispensable for manufacturing chips at the most advanced process nodes (5nm, 3nm, and below). In 2024, ASML reported record revenues, with demand for its EUV and deep ultraviolet (DUV) systems outstripping supply, and its order backlog extending well into 2025 and beyond. The company’s technological edge is underpinned by a complex global supply chain and exclusive partnerships with key component suppliers, such as Carl Zeiss AG for optics and TRUMPF for laser technology.
Other major players include Canon Inc. and Nikon Corporation, both of Japan, which primarily focus on DUV lithography systems. While these companies have lost market share in the most advanced nodes to ASML, they remain important suppliers for mature and specialty semiconductor manufacturing, such as automotive and power devices. Both Canon and Nikon continue to invest in incremental improvements to their DUV platforms and are exploring new applications, including panel-level and nanoimprint lithography.
The high cost, complexity, and intellectual property barriers have historically limited new entrants. However, 2025 sees increased efforts by Chinese companies, notably SMIC (Semiconductor Manufacturing International Corporation) and Shanghai Micro Electronics Equipment (SMEE), to develop indigenous photolithography capabilities. SMEE has announced progress on its 28nm DUV immersion lithography tool, aiming to reduce reliance on foreign suppliers. While these systems lag behind ASML’s EUV technology, they represent a significant step for China’s semiconductor self-sufficiency ambitions.
Looking ahead, the competitive landscape is expected to remain highly concentrated, with ASML maintaining its technological lead in EUV. However, ongoing export controls, government-backed R&D initiatives, and rising demand for mature node equipment are likely to foster incremental competition and innovation, particularly in regional markets. The next few years will be shaped by both the race for technological supremacy and the drive for supply chain resilience.
Technological Innovations: EUV, DUV, and Beyond
The photolithography equipment manufacturing sector is experiencing rapid technological evolution, with a strong focus on advancing extreme ultraviolet (EUV) and deep ultraviolet (DUV) lithography systems. As of 2025, these innovations are central to enabling the continued miniaturization of semiconductor devices, supporting the production of chips at 5nm, 3nm, and even more advanced nodes.
EUV lithography, operating at a wavelength of 13.5 nm, has become the cornerstone for leading-edge semiconductor fabrication. ASML Holding NV remains the sole supplier of high-volume EUV scanners, with its latest Twinscan NXE and EXE platforms being adopted by major foundries and integrated device manufacturers. In 2024 and 2025, ASML is ramping up shipments of its High-NA EUV systems, which offer higher numerical aperture optics to further improve resolution and patterning fidelity. These systems are critical for enabling sub-2nm process technologies, with customers such as Taiwan Semiconductor Manufacturing Company (TSMC), Samsung Electronics, and Intel Corporation investing heavily in their adoption.
DUV lithography, particularly immersion systems using ArF (argon fluoride) lasers at 193 nm, continues to play a vital role in both advanced and mature process nodes. Nikon Corporation and Canon Inc. are the primary competitors to ASML in the DUV segment, supplying scanners for memory, logic, and specialty device manufacturing. In 2025, DUV tools remain indispensable for multi-patterning steps and for manufacturing nodes where EUV is not yet cost-effective or available.
Looking beyond EUV and DUV, the industry is exploring next-generation lithography concepts, such as high-NA EUV, directed self-assembly (DSA), and nanoimprint lithography. ASML’s High-NA EUV systems, with a numerical aperture of 0.55, are expected to enter pilot production in 2025, targeting the 2nm and below technology nodes. Meanwhile, research collaborations involving leading equipment makers and consortia such as SEMI and imec are accelerating the development of alternative patterning techniques to address the challenges of further scaling.
The outlook for photolithography equipment manufacturing in the coming years is robust, driven by surging demand for advanced chips in AI, automotive, and high-performance computing. However, the sector faces challenges related to supply chain constraints, geopolitical tensions, and the immense capital investment required for next-generation tool development. Nevertheless, the ongoing technological innovations in EUV, DUV, and emerging lithography methods are set to define the competitive landscape and enable the semiconductor industry’s roadmap through the latter half of the decade.
Supply Chain Dynamics and Geopolitical Impacts
The photolithography equipment manufacturing sector is experiencing significant shifts in supply chain dynamics and geopolitical impacts as of 2025, with these trends expected to intensify in the coming years. Photolithography, a cornerstone of semiconductor fabrication, relies on a highly specialized and globalized supply chain, with a handful of companies dominating critical segments.
The most advanced photolithography systems, particularly extreme ultraviolet (EUV) lithography, are produced almost exclusively by ASML Holding NV, a Dutch company that supplies these machines to leading chipmakers worldwide. ASML’s supply chain is deeply interconnected with suppliers from the United States, Japan, and Europe, including optics from Carl Zeiss AG and components from Cymer (a subsidiary of ASML Holding NV), as well as precision mechatronics from various European firms.
Geopolitical tensions, particularly between the United States and China, have led to export controls and restrictions on the sale of advanced photolithography equipment to certain markets. In 2023 and 2024, the Dutch government, under pressure from the U.S., imposed licensing requirements on the export of ASML’s most advanced systems to China. This policy is expected to remain in place through 2025 and beyond, limiting China’s access to cutting-edge EUV technology and compelling Chinese manufacturers to rely on less advanced deep ultraviolet (DUV) systems or to accelerate domestic development efforts.
Meanwhile, Japanese companies such as Nikon Corporation and Canon Inc. continue to supply DUV photolithography equipment, but they too face increasing scrutiny and potential export restrictions. The U.S. government has also expanded its list of controlled technologies, affecting the supply of critical components and software from American firms to both Chinese and, in some cases, other international customers.
These geopolitical developments are prompting semiconductor manufacturers to diversify their supply chains and invest in regional manufacturing hubs. The European Union and the United States are incentivizing domestic semiconductor equipment production through policy initiatives and funding, aiming to reduce reliance on East Asian supply chains. At the same time, China is investing heavily in indigenous photolithography technology, though it remains several years behind the leading-edge capabilities of ASML and its partners.
Looking ahead, the photolithography equipment supply chain is likely to become more fragmented and regionally focused, with ongoing risks of disruption due to export controls, trade disputes, and the complexity of sourcing highly specialized components. The industry’s dependence on a small number of critical suppliers, particularly for EUV technology, will remain a strategic vulnerability through at least the latter half of the decade.
End-User Segments: Semiconductor, Display, and MEMS Applications
Photolithography equipment manufacturing is fundamentally driven by the requirements of three major end-user segments: semiconductor, display, and microelectromechanical systems (MEMS) industries. As of 2025, these sectors are experiencing divergent growth trajectories, each shaping the demand for advanced photolithography tools in distinct ways.
The semiconductor industry remains the dominant consumer of photolithography equipment, accounting for the vast majority of global demand. The ongoing transition to sub-5nm and even 3nm process nodes in logic and memory chip production is intensifying the need for extreme ultraviolet (EUV) lithography systems. ASML Holding NV stands as the sole supplier of EUV lithography machines, with its customers—major foundries and integrated device manufacturers—ramping up investments to expand advanced node capacity. In 2025, ASML projects shipping over 60 EUV systems, a significant increase from previous years, reflecting robust demand from leading-edge semiconductor fabs. Meanwhile, Canon Inc. and Nikon Corporation continue to supply deep ultraviolet (DUV) lithography systems, which remain essential for mature nodes and specialty semiconductor applications.
The display manufacturing segment, encompassing flat-panel displays (FPDs) such as OLED and LCD, is another important market for photolithography equipment. Here, the focus is on large-area lithography tools capable of handling glass substrates of increasing size and complexity. Both Canon Inc. and Nikon Corporation are key suppliers of FPD lithography systems, supporting the production of high-resolution displays for smartphones, televisions, and automotive applications. The shift toward advanced display technologies, including microLED and quantum dot displays, is expected to drive incremental demand for next-generation photolithography solutions tailored to these emerging formats.
MEMS applications, while representing a smaller share of the photolithography equipment market, are gaining prominence due to the proliferation of sensors and actuators in automotive, consumer electronics, and industrial IoT devices. MEMS fabrication typically relies on mature lithography platforms, but the push for miniaturization and integration is prompting some manufacturers to adopt more advanced photolithography techniques. Equipment suppliers are responding by offering flexible, cost-effective systems optimized for high-mix, low-volume MEMS production.
Looking ahead, the outlook for photolithography equipment manufacturing across these end-user segments remains positive. The semiconductor sector will continue to drive the bulk of investment, particularly as AI, high-performance computing, and 5G/6G technologies fuel demand for advanced chips. Display and MEMS markets are expected to provide steady, if more modest, growth, with innovation in display formats and sensor integration supporting ongoing equipment upgrades. Leading manufacturers such as ASML Holding NV, Canon Inc., and Nikon Corporation are well-positioned to capitalize on these trends through continued R&D and product portfolio expansion.
Sustainability and Environmental Considerations in Equipment Manufacturing
Sustainability and environmental considerations are increasingly central to the photolithography equipment manufacturing sector as the semiconductor industry faces mounting regulatory and societal pressure to reduce its ecological footprint. In 2025, leading manufacturers are intensifying efforts to minimize energy consumption, hazardous chemical use, and waste generation throughout the equipment lifecycle.
A key focus is the reduction of greenhouse gas emissions associated with both the manufacturing process and the operation of photolithography tools. ASML Holding NV, the dominant supplier of extreme ultraviolet (EUV) lithography systems, has publicly committed to achieving net zero greenhouse gas emissions in its own operations by 2025 and is working with its supply chain to reduce Scope 3 emissions. ASML’s latest EUV systems are designed to be more energy efficient, with innovations in power management and cooling systems that lower operational energy requirements per wafer processed.
Another major player, Canon Inc., emphasizes the use of recyclable materials and the reduction of hazardous substances in its photolithography equipment. Canon’s environmental initiatives include the development of energy-saving technologies and the implementation of closed-loop recycling systems for components and packaging. Similarly, Nikon Corporation has set targets for reducing CO2 emissions and is investing in the development of more resource-efficient manufacturing processes for its semiconductor lithography systems.
Water usage and chemical management are also critical concerns. Photolithography equipment manufacturing involves the use of ultra-pure water and various chemicals, some of which are hazardous. Companies are investing in advanced filtration and recycling systems to minimize water consumption and ensure safe handling and disposal of chemicals. For example, ASML has reported progress in reducing water usage per system produced and is collaborating with suppliers to improve chemical management practices.
Looking ahead, the industry is expected to face stricter environmental regulations, particularly in regions such as the European Union and East Asia, where semiconductor manufacturing is concentrated. Equipment manufacturers are responding by integrating life cycle assessment (LCA) methodologies into product design, aiming to quantify and reduce environmental impacts from raw material extraction through end-of-life recycling.
In summary, sustainability is becoming a competitive differentiator in photolithography equipment manufacturing. Companies like ASML, Canon, and Nikon are leading the way with ambitious environmental targets, eco-friendly design innovations, and transparent reporting. These efforts are likely to accelerate as customers and regulators demand greater accountability and as the industry seeks to align with global climate goals over the next several years.
Regional Analysis: Asia-Pacific, North America, and Europe
The global photolithography equipment manufacturing sector is heavily concentrated in three major regions: Asia-Pacific, North America, and Europe. Each region plays a distinct role in the supply chain, technology development, and market demand, with 2025 expected to reinforce these dynamics amid ongoing geopolitical and technological shifts.
Asia-Pacific remains the largest market and manufacturing hub for photolithography equipment, driven by the dominance of semiconductor fabrication in countries such as Taiwan, South Korea, China, and Japan. Taiwan’s Taiwan Semiconductor Manufacturing Company (TSMC) and South Korea’s Samsung Electronics are among the world’s leading chipmakers, accounting for a significant share of global wafer production and thus driving demand for advanced lithography tools. Japan’s Canon Inc. and Nikon Corporation are also key photolithography equipment manufacturers, particularly in the deep ultraviolet (DUV) segment. China continues to invest heavily in domestic semiconductor equipment capabilities, with companies like SMIC and NAURA Technology Group seeking to reduce reliance on foreign suppliers, though access to extreme ultraviolet (EUV) technology remains restricted due to export controls.
North America is home to several critical players in the photolithography supply chain, most notably Applied Materials, Inc. and Lam Research Corporation, which provide essential process equipment and subsystems. While the U.S. does not manufacture leading-edge photolithography scanners, it is a vital supplier of components, software, and materials. The U.S. government’s CHIPS Act and related incentives are expected to stimulate domestic semiconductor manufacturing and, by extension, demand for photolithography equipment through 2025 and beyond.
Europe is uniquely positioned as the global leader in advanced photolithography technology, primarily through ASML Holding N.V. of the Netherlands. ASML is the sole supplier of EUV lithography systems, which are essential for producing chips at the 5nm node and below. The company’s order backlog remains robust, with major customers in Asia and North America. European suppliers such as Carl Zeiss AG provide critical optical components for these systems. The region’s continued investment in R&D and its strategic role in the global semiconductor ecosystem are expected to sustain its leadership in photolithography innovation through the next several years.
Looking ahead to 2025 and beyond, the photolithography equipment manufacturing landscape will be shaped by ongoing technological advancements, supply chain realignments, and government policy interventions across these three regions. The interplay between Asia-Pacific’s manufacturing scale, North America’s component expertise, and Europe’s technological leadership will remain central to the industry’s evolution.
Investment, M&A, and Strategic Partnerships
The photolithography equipment manufacturing sector is experiencing heightened investment activity, mergers and acquisitions (M&A), and strategic partnerships as the global semiconductor industry intensifies efforts to secure advanced chipmaking capabilities. In 2025, the competitive landscape is shaped by the race to develop and deploy next-generation extreme ultraviolet (EUV) and deep ultraviolet (DUV) lithography systems, with significant capital flowing into both established leaders and emerging players.
The dominant force in the sector remains ASML Holding, the sole supplier of EUV lithography systems, which are critical for producing chips at the most advanced process nodes. ASML continues to invest heavily in expanding its production capacity and R&D, with capital expenditures projected to exceed €1.5 billion in 2025. The company has also deepened its strategic partnerships with key suppliers such as Carl Zeiss AG (optics) and TRUMPF Group (laser technology), ensuring a stable supply chain for its complex systems. These collaborations are essential for meeting the surging demand from leading foundries and integrated device manufacturers (IDMs) worldwide.
In parallel, Japanese manufacturers such as Nikon Corporation and Canon Inc. are intensifying their investments in DUV lithography and exploring new business models, including joint ventures and technology licensing, to maintain relevance in a market increasingly dominated by EUV. Both companies have announced plans to increase R&D spending in 2025, targeting niche applications and mature process nodes where DUV remains essential.
China’s ambition to localize semiconductor equipment production has led to a surge in domestic investment and strategic alliances. Companies like SMIC and NAURA Technology Group are collaborating with local photolithography toolmakers to accelerate the development of indigenous systems. The Chinese government continues to provide substantial funding and policy support, aiming to reduce reliance on foreign suppliers amid ongoing export controls.
M&A activity is expected to remain robust through 2025 and beyond, as smaller equipment manufacturers seek scale and technology access through consolidation. Strategic partnerships—particularly those focused on co-development of new lithography techniques, materials, and automation—are proliferating, with major players forming alliances with research institutes and universities to secure long-term innovation pipelines.
Looking ahead, the photolithography equipment manufacturing sector is poised for continued investment and collaboration, driven by the relentless demand for advanced semiconductors and the strategic imperative of supply chain resilience. The interplay of global competition, technological complexity, and geopolitical factors will ensure that investment, M&A, and partnerships remain central to the industry’s evolution in the coming years.
Future Outlook: Challenges, Opportunities, and Disruptive Trends
The photolithography equipment manufacturing sector is poised for significant transformation in 2025 and the years immediately following, driven by both persistent challenges and emerging opportunities. As the semiconductor industry pushes toward ever-smaller process nodes, the demand for advanced photolithography systems—particularly those utilizing extreme ultraviolet (EUV) technology—continues to surge. The market is dominated by a handful of key players, with ASML Holding maintaining a near-monopoly on EUV lithography systems, which are essential for producing chips at 5nm and below. ASML’s ongoing investments in high-NA (numerical aperture) EUV technology are expected to further extend the capabilities of photolithography, enabling sub-2nm manufacturing in the coming years.
However, the sector faces several challenges. The complexity and cost of EUV systems—each costing upwards of $150 million—pose significant barriers to entry and expansion. Supply chain constraints, particularly in the procurement of precision optics and specialized components, remain a concern. For instance, Carl Zeiss AG is a critical supplier of the high-precision mirrors used in EUV systems, and any disruption in their production can have cascading effects across the industry. Additionally, geopolitical tensions and export controls, especially those involving the United States, the Netherlands, and China, are influencing the global distribution and adoption of advanced photolithography equipment.
Opportunities abound as well. The rapid expansion of artificial intelligence, high-performance computing, and automotive electronics is fueling unprecedented demand for advanced semiconductors, which in turn drives investment in next-generation lithography tools. Companies such as Nikon Corporation and Canon Inc. continue to innovate in deep ultraviolet (DUV) lithography, targeting mature nodes and specialty applications where EUV is not yet cost-effective. Furthermore, the push for regional semiconductor manufacturing—exemplified by new fabs in the United States, Europe, and Asia—creates a robust pipeline for equipment orders and service contracts.
Disruptive trends are also on the horizon. The integration of machine learning and advanced process control into photolithography equipment promises to enhance yield and reduce downtime. There is growing interest in alternative patterning techniques, such as nanoimprint lithography and directed self-assembly, which could complement or, in specific niches, compete with traditional photolithography. Sustainability is becoming a critical focus, with manufacturers seeking to reduce the energy and resource intensity of their tools.
In summary, while the photolithography equipment manufacturing sector in 2025 faces high technical and geopolitical hurdles, it is also positioned for growth and innovation, underpinned by the relentless global demand for advanced semiconductors and the ongoing evolution of lithography technologies.