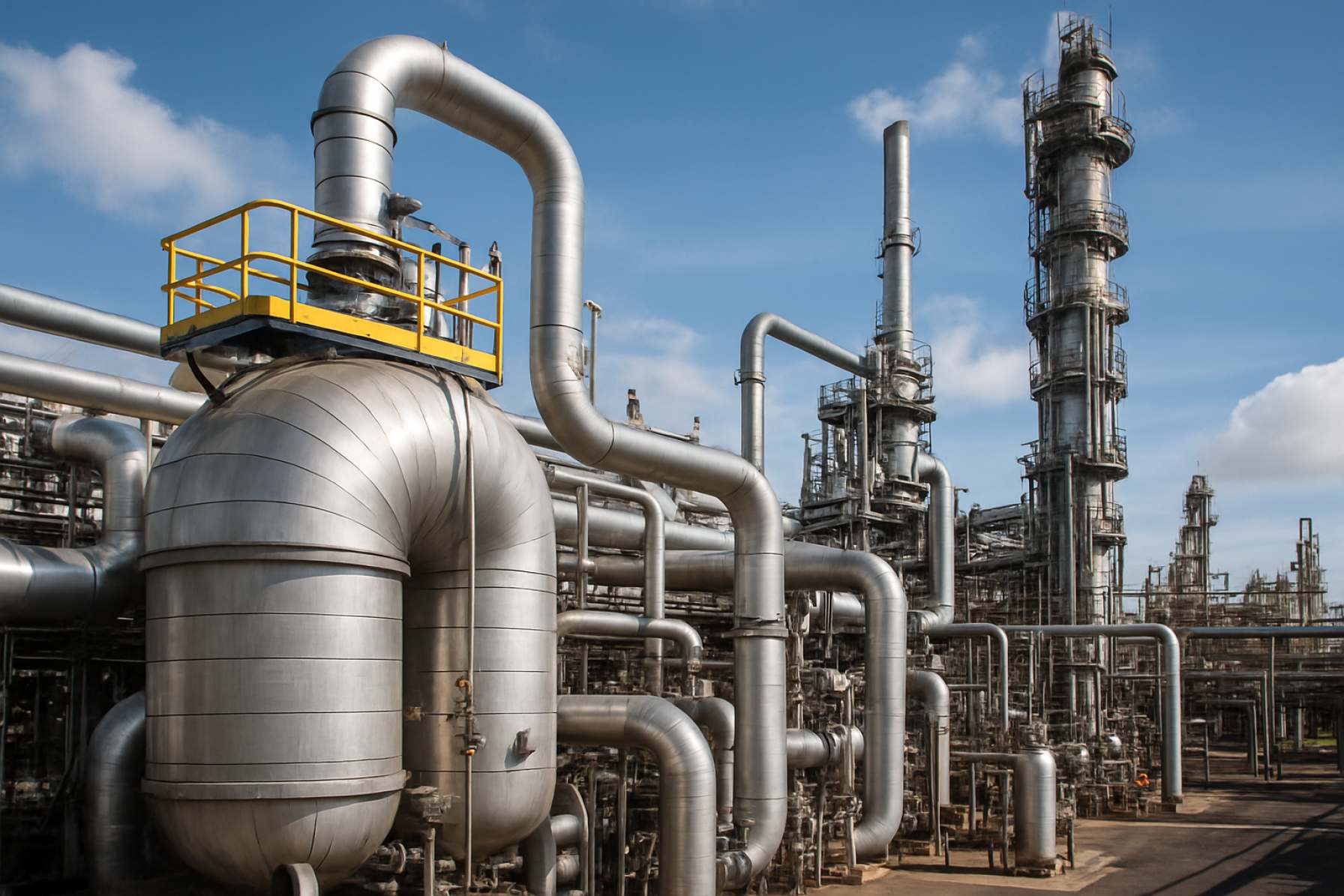
Catalytic Pyrolysis Technology Development in 2025: Unleashing Next-Gen Solutions for Sustainable Chemical and Fuel Production. Explore How Innovation and Policy Are Shaping a Rapidly Expanding Industry.
- Executive Summary: Catalytic Pyrolysis in 2025 and Beyond
- Market Size, Growth Rate, and 2025–2030 Forecasts
- Key Technology Innovations and Process Advancements
- Leading Companies and Industry Collaborations
- Feedstock Trends: Biomass, Plastics, and Waste Streams
- Commercialization Status and Pilot Projects
- Policy, Regulation, and Sustainability Drivers
- Competitive Landscape and Strategic Partnerships
- Challenges, Barriers, and Risk Factors
- Future Outlook: Opportunities and Disruptive Trends
- Sources & References
Executive Summary: Catalytic Pyrolysis in 2025 and Beyond
Catalytic pyrolysis technology is poised for significant advancement in 2025 and the coming years, driven by the urgent need for scalable solutions to plastic waste and the transition to a circular economy. Unlike conventional pyrolysis, catalytic pyrolysis employs specialized catalysts to enhance the breakdown of plastic polymers, resulting in higher yields of valuable products such as naphtha, olefins, and aromatics, while reducing process energy requirements and unwanted byproducts.
In 2025, several industry leaders are accelerating the commercialization of catalytic pyrolysis. SABIC, a global chemical manufacturer, has partnered with technology providers to integrate advanced catalytic pyrolysis units at its facilities, aiming to process mixed plastic waste into feedstocks for new polymers. Similarly, BASF is scaling up its ChemCycling™ project, which leverages proprietary catalysts to convert post-consumer plastics into high-quality chemical building blocks. These initiatives are supported by collaborations with waste management and consumer goods companies, reflecting a growing ecosystem around catalytic pyrolysis.
On the technology supplier side, Honeywell has launched its UpCycle Process Technology, which incorporates tailored catalysts to improve conversion efficiency and product selectivity. The company reports that its process can handle a broader range of plastic waste streams, including multilayer and contaminated plastics, which have traditionally been challenging for mechanical recycling. Lummus Technology is also advancing its proprietary catalytic pyrolysis solutions, focusing on modular plant designs that can be rapidly deployed and integrated with existing petrochemical infrastructure.
The next few years are expected to see a rapid increase in commercial-scale deployments, with several plants under construction or in the planning phase across Europe, North America, and Asia. Regulatory drivers, such as the European Union’s targets for recycled content in packaging and extended producer responsibility schemes, are accelerating investment in catalytic pyrolysis. Industry bodies like PlasticsEurope and American Chemistry Council are actively promoting chemical recycling, including catalytic pyrolysis, as a critical pathway to achieving circularity in plastics.
Looking ahead, ongoing R&D is focused on catalyst optimization, process intensification, and integration with renewable hydrogen and carbon capture technologies. The outlook for 2025 and beyond suggests that catalytic pyrolysis will transition from pilot and demonstration phases to full commercial operation, playing a pivotal role in the sustainable management of plastic waste and the production of circular chemicals.
Market Size, Growth Rate, and 2025–2030 Forecasts
Catalytic pyrolysis technology, a process that leverages catalysts to enhance the conversion of waste plastics and biomass into valuable fuels and chemicals, is experiencing accelerated development and commercialization as of 2025. The market for catalytic pyrolysis is being driven by tightening global regulations on plastic waste, increasing demand for circular economy solutions, and the need for low-carbon feedstocks in the chemical and fuel industries.
In 2025, the global installed capacity for catalytic pyrolysis is estimated to be in the low hundreds of kilotons per year, with several large-scale demonstration and commercial plants either operational or under construction. Notably, SABIC has partnered with technology providers to scale up advanced recycling facilities in Europe and the Middle East, targeting the conversion of mixed plastic waste into feedstock for new polymers. Similarly, BASF is advancing its ChemCycling™ project, which includes catalytic pyrolysis as a core technology for transforming post-consumer plastics into virgin-quality materials.
The growth rate for catalytic pyrolysis technology is projected to exceed 15% CAGR between 2025 and 2030, as more chemical producers and waste management companies invest in advanced recycling infrastructure. LyondellBasell has announced plans to expand its MoReTec molecular recycling technology, which incorporates catalytic pyrolysis, with pilot plants in Europe and North America. Meanwhile, Shell is collaborating with partners to develop and deploy catalytic pyrolysis units capable of processing a wide range of plastic waste streams, aiming for commercial-scale operations by the late 2020s.
In Asia, companies such as Sinopec are investing in catalytic pyrolysis research and pilot projects, recognizing the technology’s potential to address the region’s mounting plastic waste challenge and to supply feedstock for the petrochemical sector. The Middle East is also emerging as a key region for deployment, with integrated oil and chemical companies seeking to diversify their product portfolios and reduce environmental impact.
Looking ahead to 2030, the market outlook for catalytic pyrolysis is robust, with expectations of multi-million ton annual capacity globally. The technology’s scalability, ability to handle mixed and contaminated waste streams, and compatibility with existing petrochemical infrastructure position it as a cornerstone of the future circular plastics economy. Ongoing innovation in catalyst design and process integration is anticipated to further improve yields, reduce costs, and expand the range of feedstocks, supporting continued market expansion and adoption.
Key Technology Innovations and Process Advancements
Catalytic pyrolysis technology is undergoing rapid development in 2025, driven by the urgent need to convert plastic waste and biomass into valuable fuels and chemicals with higher efficiency and selectivity. The integration of advanced catalysts, process intensification, and modular plant designs are at the forefront of these innovations.
A major trend is the deployment of proprietary catalyst formulations that enhance product yields and reduce undesirable byproducts. Companies such as SABIC and BASF are actively developing and commercializing zeolite-based and metal-modified catalysts tailored for mixed plastic and biomass feedstocks. These catalysts enable lower reaction temperatures and improved selectivity towards light olefins and aromatics, which are critical for circular polymer production and petrochemical feedstock integration.
Process intensification is another key area, with several technology providers focusing on continuous-flow reactor systems and modular plant configurations. Licella Holdings and Anzaplan are notable for their hydrothermal and catalytic pyrolysis platforms, which are being scaled up for commercial demonstration. These systems offer improved heat transfer, better catalyst contact, and the flexibility to process diverse waste streams, including contaminated or multilayer plastics.
In 2025, pilot and demonstration plants are being commissioned globally, with a focus on integrating catalytic pyrolysis units into existing petrochemical complexes. SABIC has announced the operation of advanced recycling units in Europe, leveraging catalytic pyrolysis to produce certified circular polymers. Similarly, BASF is collaborating with partners to validate the scalability and economic viability of their ChemCycling™ process, which utilizes proprietary catalysts to convert plastic waste into feedstock for new chemicals.
The outlook for the next few years includes further optimization of catalyst lifetimes, reduction of coke formation, and the development of catalysts that can tolerate higher levels of feedstock impurities. Industry bodies such as PlasticsEurope are supporting standardization efforts and lifecycle assessments to facilitate regulatory acceptance and market uptake of catalytic pyrolysis-derived products.
Overall, the convergence of advanced catalysis, modular engineering, and industry collaboration is expected to accelerate the commercialization of catalytic pyrolysis technologies, positioning them as a cornerstone of the emerging circular economy for plastics and biomass by the late 2020s.
Leading Companies and Industry Collaborations
The landscape of catalytic pyrolysis technology is rapidly evolving in 2025, with several leading companies and industry collaborations driving advancements in process efficiency, scale-up, and commercialization. The focus is on converting plastic waste and biomass into high-value fuels and chemicals, leveraging proprietary catalysts and reactor designs to improve selectivity and yield.
Among the most prominent players, SABIC has emerged as a global leader, actively developing and deploying catalytic pyrolysis solutions for plastic waste recycling. SABIC’s TRUCIRCLE™ initiative, in collaboration with technology partners and downstream users, has resulted in the commissioning of advanced recycling plants in Europe and the Middle East. These facilities utilize proprietary catalysts to break down mixed plastic waste into feedstocks suitable for new polymer production, with commercial-scale operations expected to expand further in 2025.
Another key innovator is BASF, which has invested heavily in its ChemCycling™ project. BASF collaborates with technology providers and waste management companies to integrate catalytic pyrolysis into existing chemical value chains. In 2024, BASF announced the successful operation of pilot plants in Germany, and in 2025, the company is scaling up to semi-commercial demonstration, aiming to process thousands of tons of plastic waste annually. BASF’s approach emphasizes the use of tailored catalysts to maximize monomer recovery and minimize contaminants.
In North America, LyondellBasell is advancing its proprietary MoReTec technology, which employs a catalytic pyrolysis process to convert post-consumer plastics into feedstocks for new plastics. The company’s pilot plant in Ferrara, Italy, has demonstrated continuous operation, and in 2025, LyondellBasell is pursuing joint ventures with waste management firms to secure feedstock supply and accelerate commercialization.
Industry collaborations are also shaping the sector. Shell has partnered with technology developers and consumer goods companies to integrate catalytic pyrolysis oils into its refining and petrochemical operations. Shell’s efforts include co-developing advanced catalysts and optimizing process conditions to improve product quality and reduce energy consumption.
Looking ahead, the next few years are expected to see increased cross-sector partnerships, with chemical producers, catalyst manufacturers, and waste management companies forming consortia to address feedstock variability and regulatory challenges. The European Union’s policy push for circular plastics and the U.S. Department of Energy’s funding for advanced recycling are likely to accelerate technology deployment and standardization. As these collaborations mature, catalytic pyrolysis is poised to become a cornerstone of sustainable materials management by 2030.
Feedstock Trends: Biomass, Plastics, and Waste Streams
Catalytic pyrolysis technology is rapidly evolving as a key solution for converting diverse feedstocks—such as biomass, plastics, and mixed waste streams—into valuable fuels and chemicals. As of 2025, the sector is witnessing significant advancements in both catalyst design and reactor engineering, driven by the urgent need for scalable, efficient, and economically viable recycling and valorization pathways.
A major trend is the shift toward more robust and selective catalysts, particularly zeolites and metal-modified materials, which enhance product yields and selectivity for target hydrocarbons. Companies like BASF and Clariant are actively developing proprietary catalyst formulations tailored for specific feedstocks, including mixed plastic waste and lignocellulosic biomass. These catalysts are designed to minimize coke formation and improve process lifetimes, addressing a key bottleneck in commercial deployment.
On the technology front, modular and continuous-flow pyrolysis reactors are gaining traction, enabling better heat transfer, scalability, and integration with existing waste management infrastructure. Eni and Shell are among the energy majors piloting and scaling up catalytic pyrolysis units capable of processing several thousand tons of waste plastics annually. These systems are increasingly being co-located with material recovery facilities to streamline logistics and feedstock supply.
Feedstock flexibility is another area of focus. The latest catalytic pyrolysis plants are being engineered to handle a broader range of input materials, from agricultural residues and forestry byproducts to multilayer packaging and contaminated post-consumer plastics. This adaptability is crucial for maximizing resource recovery and supporting circular economy goals. For example, Licella Holdings is advancing hydrothermal and catalytic pyrolysis platforms that can process mixed waste streams, including those with high moisture content, which are traditionally challenging for conventional pyrolysis.
Looking ahead to the next few years, the outlook for catalytic pyrolysis is strongly positive. Industry collaborations and joint ventures are accelerating technology validation and commercialization. Regulatory drivers—such as extended producer responsibility and recycled content mandates—are expected to further boost investment and deployment. By 2027, several commercial-scale plants are anticipated to come online in Europe, North America, and Asia, with a focus on producing drop-in fuels, monomers for plastics, and specialty chemicals. The continued evolution of catalyst systems and reactor designs will be pivotal in reducing costs, improving product quality, and expanding the range of viable feedstocks.
Commercialization Status and Pilot Projects
Catalytic pyrolysis technology, which leverages catalysts to enhance the conversion of plastic and biomass waste into valuable fuels and chemicals, is transitioning from laboratory research to commercial-scale deployment. As of 2025, several companies and consortia are advancing pilot and demonstration projects, with a focus on scaling up, improving process efficiency, and integrating with existing petrochemical infrastructure.
One of the most prominent players is SABIC, which has been actively developing and piloting advanced recycling technologies, including catalytic pyrolysis, at its facilities in Europe and the Middle East. SABIC’s collaborations with technology providers and consumer goods companies aim to produce certified circular polymers, with commercial-scale operations targeted for the mid-2020s. The company’s demonstration plants are designed to process mixed plastic waste streams, using proprietary catalysts to improve yield and product quality.
In North America, LyondellBasell is advancing its MoReTec technology, which utilizes a catalytic pyrolysis process to convert post-consumer plastic waste into feedstocks for new plastics. The company’s pilot plant in Ferrara, Italy, has been operational since 2020, and in 2024, LyondellBasell announced plans to scale up to a commercial demonstration facility, with the goal of reaching full commercial operation by 2026. The company is also exploring partnerships to license its technology globally.
Another significant initiative is led by BASF, which is piloting its ChemCycling project. BASF’s approach involves catalytic pyrolysis of mixed plastic waste to produce pyrolysis oil, which is then used as a feedstock in its existing chemical plants. The company has partnered with waste management and recycling firms to secure feedstock supply and is targeting commercial-scale integration by 2025–2026.
In Asia, Toray Industries is developing catalytic pyrolysis processes for both plastics and biomass, with pilot projects underway in Japan. Toray’s focus is on optimizing catalyst formulations to maximize the yield of high-value monomers and reduce process energy requirements, with commercial deployment anticipated in the latter half of the decade.
Looking ahead, the commercialization of catalytic pyrolysis is expected to accelerate as regulatory pressures on plastic waste management intensify and demand for circular polymers grows. The next few years will likely see the commissioning of the first large-scale plants, further technology optimization, and increased collaboration between chemical producers, technology developers, and waste management companies. The success of these pilot and demonstration projects will be critical in establishing catalytic pyrolysis as a viable solution for circular economy goals.
Policy, Regulation, and Sustainability Drivers
Catalytic pyrolysis technology is rapidly evolving in response to intensifying policy, regulatory, and sustainability drivers worldwide. As of 2025, governments and industry bodies are accelerating mandates for circular economy practices, particularly targeting plastic waste and decarbonization. The European Union’s Circular Economy Action Plan and the Single-Use Plastics Directive are pushing member states to adopt advanced recycling technologies, including catalytic pyrolysis, to meet ambitious recycling and recycled content targets by 2030. Similarly, the United States Environmental Protection Agency (EPA) is increasing scrutiny on chemical recycling, with several states enacting or considering legislation to classify pyrolysis as manufacturing rather than waste disposal, thereby streamlining permitting and encouraging investment.
In Asia, China’s “Zero Waste Cities” initiative and Japan’s Plastic Resource Circulation Act are driving demand for scalable, efficient recycling solutions. These policies are fostering partnerships between technology developers and petrochemical majors to deploy catalytic pyrolysis at commercial scale. For example, SABIC has announced collaborations with technology providers to integrate catalytic pyrolysis into its feedstock recycling operations, aiming to produce certified circular polymers for consumer goods and packaging applications.
Sustainability commitments from major brands and industry alliances are also shaping the technology landscape. The Alliance to End Plastic Waste and the PlasticsEurope association are supporting pilot projects and scale-up efforts for catalytic pyrolysis, recognizing its potential to convert mixed and contaminated plastic waste into high-value hydrocarbons with lower energy input and emissions compared to traditional thermal pyrolysis. These organizations are working with stakeholders to develop certification schemes and traceability systems for recycled outputs, aligning with evolving regulatory requirements for recycled content and product stewardship.
Looking ahead to the next few years, policy momentum is expected to intensify. The EU is preparing to implement mandatory recycled content quotas for packaging, while the US is considering national extended producer responsibility (EPR) frameworks. These measures are likely to accelerate investment in catalytic pyrolysis R&D and commercialization, with a focus on improving catalyst lifetimes, process selectivity, and integration with existing petrochemical infrastructure. Industry leaders such as BASF and Shell are actively developing proprietary catalytic pyrolysis processes, aiming to scale up demonstration plants and secure supply agreements with consumer brands seeking to meet sustainability pledges.
In summary, the convergence of regulatory pressure, corporate sustainability goals, and technological innovation is positioning catalytic pyrolysis as a key enabler of circular plastics and low-carbon feedstocks. The next few years will be critical for translating policy drivers into commercial deployment, with ongoing collaboration between technology developers, chemical producers, and policymakers essential for overcoming technical and market barriers.
Competitive Landscape and Strategic Partnerships
The competitive landscape for catalytic pyrolysis technology is rapidly evolving in 2025, driven by increasing regulatory pressure to address plastic waste and the need for scalable, economically viable recycling solutions. Key players in this sector are advancing proprietary catalyst formulations, reactor designs, and process integration to improve yields, product selectivity, and operational efficiency. Strategic partnerships—spanning feedstock suppliers, chemical producers, and technology licensors—are central to accelerating commercialization and de-risking investments.
Among the most prominent companies, SABIC has continued to expand its TRUCIRCLE™ portfolio, leveraging catalytic pyrolysis to convert mixed plastic waste into certified circular polymers. In 2024, SABIC announced new collaborations with global consumer brands and waste management firms to secure feedstock streams and scale up advanced recycling capacity. Similarly, BASF is advancing its ChemCycling™ project, which utilizes proprietary catalysts to depolymerize post-consumer plastics. BASF has entered into joint development agreements with technology providers and downstream users to validate product quality and integrate recycled feedstocks into existing chemical value chains.
In North America, LyondellBasell is piloting its MoReTec technology, which employs a catalytic process to break down plastic waste into feedstock for new polymers. The company has established partnerships with academic institutions and engineering firms to optimize reactor design and scale-up. Meanwhile, Shell is investing in catalytic pyrolysis as part of its broader circular economy strategy, collaborating with technology developers and waste aggregators to secure supply and offtake agreements.
Startups and technology licensors are also shaping the competitive landscape. Quantafuel, based in Norway, operates commercial-scale plants using proprietary catalysts and has entered into supply agreements with major petrochemical companies. Agilyx (formerly Agrauxine) is another notable player, focusing on chemical recycling of polystyrene and mixed plastics, and has formed joint ventures with industry leaders to expand its technology footprint.
Looking ahead, the next few years are expected to see intensified collaboration between technology developers, polymer producers, and consumer goods companies. The formation of consortia and cross-sector alliances is likely to accelerate, as stakeholders seek to harmonize standards, secure long-term feedstock contracts, and demonstrate the environmental benefits of catalytic pyrolysis at scale. As regulatory frameworks mature and demand for recycled content grows, companies with robust intellectual property, proven process reliability, and strong partnership networks are poised to lead the market.
Challenges, Barriers, and Risk Factors
Catalytic pyrolysis technology, which aims to convert plastic waste and biomass into valuable fuels and chemicals, faces several significant challenges and barriers as it moves toward broader commercialization in 2025 and the coming years. Despite notable progress in pilot and demonstration projects, the sector must address technical, economic, and regulatory hurdles to achieve large-scale deployment.
One of the primary technical challenges is catalyst deactivation. Catalysts used in pyrolysis processes are prone to fouling and poisoning due to contaminants in feedstocks, such as chlorine, sulfur, and heavy metals. This leads to reduced efficiency and increased operational costs, as frequent catalyst regeneration or replacement is required. Companies like BASF and SABIC are actively developing more robust and selective catalysts, but achieving long-term stability and high selectivity remains a key research focus.
Feedstock variability is another barrier. The heterogeneous nature of post-consumer plastic waste and biomass introduces inconsistencies in process yields and product quality. This variability complicates process optimization and scale-up. Efforts by technology developers such as Licella Holdings and ANZAPLAN are focused on pre-treatment and sorting technologies to improve feedstock consistency, but these add to capital and operational expenditures.
Economic viability is a persistent risk factor. Catalytic pyrolysis plants require significant upfront investment, and their profitability is sensitive to fluctuating oil prices and the value of end products. The cost competitiveness of pyrolysis-derived fuels and chemicals compared to conventional petrochemical routes is not yet assured, especially in regions with low fossil fuel prices. Companies such as Shell and TotalEnergies are piloting integrated approaches to improve economics, but large-scale commercial plants remain limited.
Regulatory uncertainty also poses a barrier. The classification of pyrolysis oils and their acceptance as recycled content under various national and international frameworks is still evolving. For example, the European Union’s evolving waste and chemical regulations impact the marketability of pyrolysis products. Industry groups like PlasticsEurope are engaging with policymakers to clarify standards and certification pathways, but regulatory harmonization is still in progress.
Looking ahead to 2025 and beyond, overcoming these challenges will require coordinated efforts in catalyst innovation, feedstock management, process integration, and regulatory alignment. Strategic partnerships between technology developers, chemical producers, and waste management companies are expected to accelerate progress, but the pace of commercial adoption will depend on resolving these persistent barriers.
Future Outlook: Opportunities and Disruptive Trends
Catalytic pyrolysis technology is poised for significant advancements and market expansion in 2025 and the following years, driven by mounting regulatory pressure to address plastic waste and decarbonize the chemical sector. The technology, which uses catalysts to convert plastic and biomass waste into valuable fuels and chemicals at lower temperatures and with higher selectivity than traditional pyrolysis, is attracting substantial investment and industrial collaboration.
Several major chemical and energy companies are scaling up pilot and demonstration plants, aiming for commercial deployment by the mid-2020s. BASF is advancing its ChemCycling™ project, which integrates catalytic pyrolysis oils into its existing steam crackers, with plans to increase capacity and expand partnerships with waste management firms. SABIC is collaborating with technology providers and consumer brands to develop closed-loop solutions, leveraging catalytic processes to produce certified circular polymers. Shell is also investing in catalytic pyrolysis, focusing on scaling up its technology for both plastics and biomass, and has announced new projects in Europe and Asia targeting commercial operation by 2026.
On the technology front, the next few years will see a focus on catalyst innovation—particularly the development of robust, selective, and regenerable catalysts that can handle mixed and contaminated waste streams. Companies such as Honeywell are commercializing proprietary catalysts and modular reactor designs, aiming to improve process economics and product quality. Lummus Technology is also active in this space, offering integrated solutions for catalytic pyrolysis and downstream upgrading.
A disruptive trend is the integration of catalytic pyrolysis with existing petrochemical infrastructure, enabling the direct use of pyrolysis oils as feedstock for new plastics and chemicals. This approach is being piloted by several industry leaders and is expected to accelerate the adoption of circular economy models. Additionally, the emergence of digital process control and real-time analytics is enhancing operational efficiency and product consistency, further supporting scale-up efforts.
Looking ahead, the outlook for catalytic pyrolysis technology is highly promising. Regulatory drivers such as the EU’s mandatory recycled content targets and extended producer responsibility schemes are expected to boost demand for advanced recycling solutions. As more demonstration plants reach commercial scale, the sector is likely to see increased standardization, cost reductions, and broader adoption across regions. Strategic partnerships between technology developers, chemical producers, and waste management companies will be crucial in overcoming feedstock variability and supply chain challenges, positioning catalytic pyrolysis as a cornerstone of sustainable materials management in the coming years.
Sources & References
- BASF
- Honeywell
- Lummus Technology
- PlasticsEurope
- American Chemistry Council
- LyondellBasell
- Shell
- Licella Holdings
- Anzaplan
- Clariant
- Toray Industries
- Quantafuel
- Agilyx
- TotalEnergies