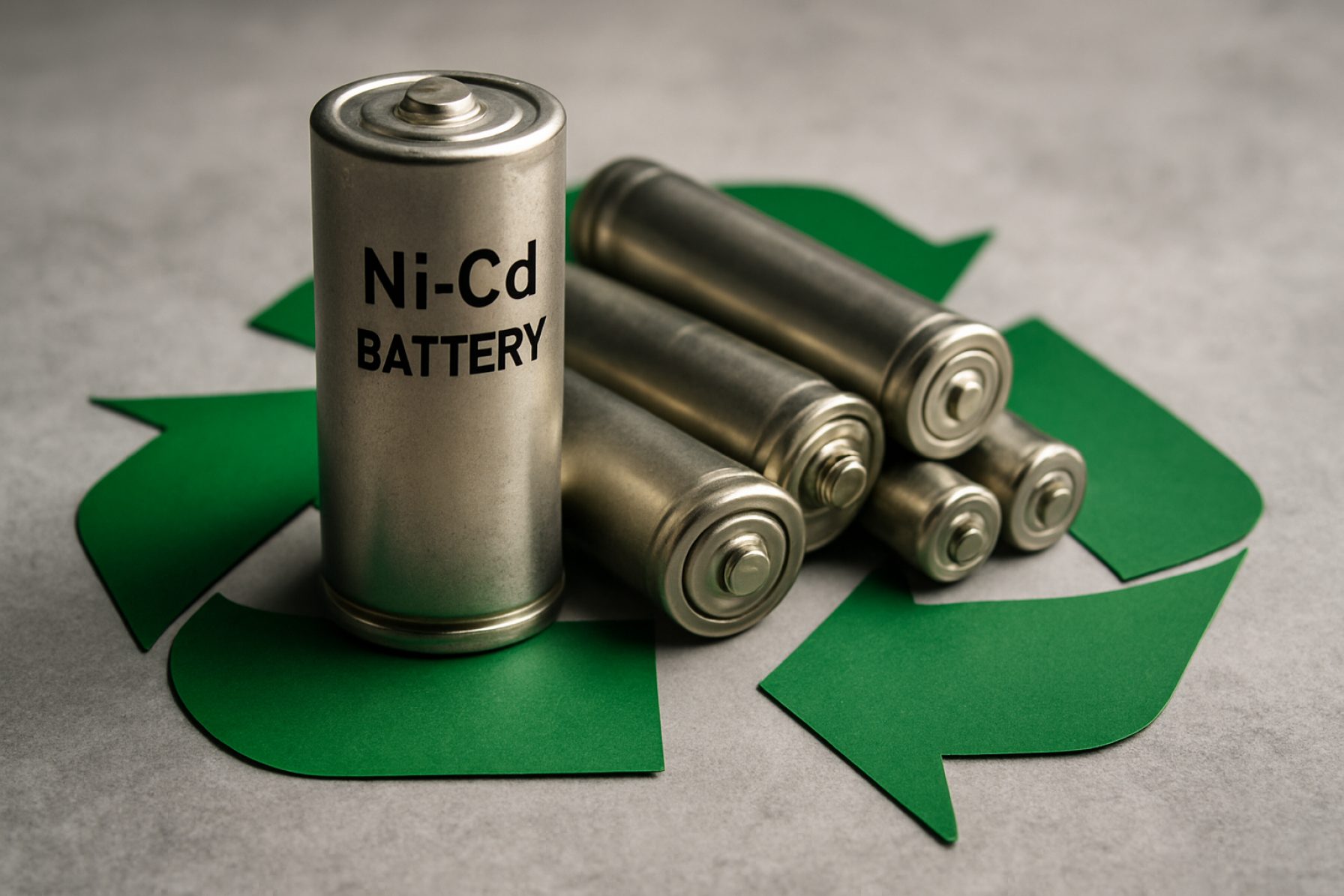
Nickel-Cadmium Battery Recycling Technologies in 2025: Innovations, Market Growth, and the Road to Sustainable Energy Storage. Explore how advanced recycling is reshaping the industry and driving a greener future.
- Executive Summary: Key Trends and Market Drivers
- Global Market Size and Growth Forecast (2025–2030)
- Regulatory Landscape and Environmental Compliance
- Technological Innovations in Ni-Cd Battery Recycling
- Major Industry Players and Strategic Initiatives
- Supply Chain Dynamics and Raw Material Recovery
- Economic and Environmental Impact Analysis
- Regional Insights: North America, Europe, Asia-Pacific
- Challenges, Risks, and Barriers to Adoption
- Future Outlook: Opportunities and Strategic Recommendations
- Sources & References
Executive Summary: Key Trends and Market Drivers
The landscape of nickel-cadmium (Ni-Cd) battery recycling technologies is undergoing significant transformation in 2025, driven by tightening environmental regulations, evolving industrial demand, and advances in recycling processes. Ni-Cd batteries, once dominant in industrial, emergency, and backup power applications, are now subject to stricter end-of-life management due to the toxicity of cadmium and the value of recoverable nickel. Regulatory frameworks in the European Union, North America, and parts of Asia are mandating higher collection and recycling rates, compelling manufacturers and recyclers to invest in more efficient and environmentally sound technologies.
Key industry players, such as Umicore and Accurec Recycling GmbH, are at the forefront of deploying advanced hydrometallurgical and pyrometallurgical processes. These methods enable the recovery of high-purity nickel and cadmium, while minimizing hazardous emissions. Umicore, a global leader in materials technology and recycling, operates dedicated facilities for Ni-Cd battery recycling in Europe, leveraging closed-loop systems to reintroduce recovered metals into new battery production. Similarly, Accurec Recycling GmbH specializes in the treatment of industrial batteries, utilizing proprietary processes to achieve high recovery rates and compliance with EU Battery Directive targets.
In 2025, the market is also witnessing increased collaboration between battery manufacturers, industrial users, and recyclers to streamline collection logistics and improve traceability. Initiatives led by organizations such as European Battery Recycling Association are fostering best practices and harmonizing standards across member states. In North America, companies like Call2Recycle are expanding their collection networks and public awareness campaigns, further boosting recycling rates for Ni-Cd batteries.
Despite the global shift toward lithium-ion chemistries, the installed base of Ni-Cd batteries in critical infrastructure ensures a steady stream of end-of-life units requiring responsible recycling. The outlook for the next few years points to continued investment in automation, process optimization, and digital tracking systems to enhance efficiency and regulatory compliance. As environmental scrutiny intensifies and resource recovery becomes more economically attractive, the Ni-Cd battery recycling sector is poised for incremental growth and technological refinement, with leading companies setting benchmarks for sustainability and circularity.
Global Market Size and Growth Forecast (2025–2030)
The global market for nickel-cadmium (Ni-Cd) battery recycling technologies is poised for steady growth from 2025 through 2030, driven by tightening environmental regulations, increasing industrial battery usage, and the ongoing transition to circular economy models. As of 2025, the market is characterized by a mix of established recycling operators and emerging technology providers, with Europe and Asia-Pacific leading in both capacity and regulatory enforcement.
In 2025, the European Union continues to enforce strict directives on battery collection and recycling, mandating high recovery rates for cadmium and nickel from spent batteries. This regulatory environment has fostered a robust recycling infrastructure, with companies such as Umicore and SNAM operating advanced hydrometallurgical and pyrometallurgical facilities. Umicore, headquartered in Belgium, is recognized for its closed-loop recycling processes, which recover metals for reuse in new batteries and other applications. France-based SNAM specializes in the recycling of industrial Ni-Cd batteries, supplying recovered materials to the European metals market.
In Asia-Pacific, China remains a significant player, with state-backed enterprises and private firms expanding recycling capacity to address both domestic consumption and export markets. Companies such as GEM Co., Ltd. have invested in large-scale recycling plants, utilizing proprietary technologies to extract nickel and cadmium efficiently. The region’s growth is further supported by government policies aimed at reducing hazardous waste and promoting resource recovery.
North America is also witnessing increased investment in Ni-Cd battery recycling, with firms like Call2Recycle facilitating collection programs and partnerships with recyclers. The U.S. and Canada are expected to see moderate growth, spurred by industrial demand and evolving regulatory frameworks.
From 2025 to 2030, the global Ni-Cd battery recycling market is projected to grow at a compound annual growth rate (CAGR) in the mid-single digits, reflecting both rising battery waste volumes and improvements in recycling efficiency. Technological advancements—such as enhanced separation techniques and automation—are anticipated to further reduce processing costs and environmental impact. The outlook for the sector remains positive, with ongoing innovation and policy support likely to drive expansion and consolidation among leading recyclers worldwide.
Regulatory Landscape and Environmental Compliance
The regulatory landscape for nickel-cadmium (Ni-Cd) battery recycling is evolving rapidly in 2025, driven by stringent environmental directives and the global push for sustainable resource management. Ni-Cd batteries, classified as hazardous waste due to their cadmium content, are subject to strict collection, transport, and recycling requirements in most industrialized regions. The European Union remains at the forefront, enforcing the Battery Directive (2006/66/EC) and its amendments, which mandate the separate collection and recycling of portable Ni-Cd batteries and set minimum recycling efficiencies. These regulations are mirrored by similar frameworks in North America and parts of Asia, where compliance is overseen by national environmental agencies and industry stewardship organizations.
In the EU, the Battery Regulation (EU) 2023/1542, which entered into force in 2023, is being fully implemented by 2025. It imposes higher collection targets, stricter recycling efficiency thresholds, and extended producer responsibility (EPR) for battery manufacturers and importers. The regulation requires that at least 75% of the average weight of Ni-Cd batteries be recycled, with cadmium recovery rates exceeding 80%. Producers must also ensure traceability and provide detailed reporting on the fate of collected batteries. These measures are enforced by national authorities and monitored by organizations such as Eucobat, which coordinates compliance across European battery collection schemes.
In the United States, the Mercury-Containing and Rechargeable Battery Management Act (Battery Act) continues to regulate Ni-Cd battery disposal and recycling, with stewardship programs operated by organizations like Call2Recycle. The U.S. Environmental Protection Agency (EPA) oversees compliance, and several states have introduced additional requirements for battery retailers and recyclers. In Canada, the stewardship model is similar, with provincial regulations mandating collection and recycling, and organizations such as Call2Recycle Canada facilitating compliance.
Asia-Pacific countries are tightening controls as well. Japan enforces the Act on the Promotion of Effective Utilization of Resources, requiring manufacturers to collect and recycle Ni-Cd batteries, while China’s Ministry of Ecology and Environment has issued new technical standards for battery recycling facilities. Major battery manufacturers, including Panasonic and Sony, have established take-back and recycling programs to meet these obligations.
Looking ahead, regulatory pressure is expected to intensify, with further increases in recycling targets and stricter controls on hazardous waste exports. The trend toward harmonized global standards is likely to continue, driven by international agreements and the growing adoption of circular economy principles. Companies operating in the Ni-Cd battery value chain must invest in advanced recycling technologies and robust compliance systems to meet evolving requirements and avoid penalties.
Technological Innovations in Ni-Cd Battery Recycling
Nickel-cadmium (Ni-Cd) battery recycling technologies are undergoing significant transformation as regulatory pressures, environmental concerns, and resource recovery imperatives intensify in 2025 and the coming years. The recycling of Ni-Cd batteries is particularly critical due to the toxicity of cadmium and the value of recovered nickel. Traditional hydrometallurgical and pyrometallurgical processes remain the backbone of industrial-scale recycling, but recent innovations are enhancing efficiency, safety, and material recovery rates.
Hydrometallurgical processes, which involve leaching metals from shredded batteries using acids or other solvents, are being refined to reduce chemical consumption and improve selectivity. Companies such as Umicore, a global leader in battery recycling, have invested in closed-loop systems that minimize emissions and maximize the recovery of both nickel and cadmium. Their facilities in Europe are recognized for integrating advanced purification steps, enabling the production of high-purity metal salts suitable for reuse in battery manufacturing.
Pyrometallurgical methods, which use high-temperature furnaces to separate metals, are also evolving. Accurec Recycling GmbH, a German specialist in battery recycling, has developed proprietary furnace technologies that allow for the efficient separation of cadmium as a distillate, while nickel and iron are recovered as alloys. These processes are being optimized to reduce energy consumption and improve the capture of volatile cadmium, addressing both economic and environmental concerns.
In 2025, a notable trend is the integration of pre-treatment steps such as mechanical sorting, automated dismantling, and advanced shredding. These innovations, adopted by companies like Batrec Industrie AG, enhance the separation of battery components, reduce contamination, and increase the yield of valuable metals. Batrec’s Swiss facility is recognized for its use of automated systems that safely handle hazardous materials and improve throughput.
Looking ahead, the outlook for Ni-Cd battery recycling technologies is shaped by the push for circular economy models and stricter regulations on hazardous waste. The European Union’s updated Battery Regulation, set to be fully enforced by 2025, is expected to drive further investment in recycling infrastructure and technology upgrades. Industry leaders are also exploring the potential of bioleaching—using microorganisms to extract metals—as a low-energy, environmentally friendly alternative, though this remains at the pilot stage.
Overall, the next few years will likely see continued advancements in process automation, material recovery efficiency, and environmental performance, positioning established recyclers such as Umicore, Accurec Recycling GmbH, and Batrec Industrie AG at the forefront of Ni-Cd battery recycling innovation.
Major Industry Players and Strategic Initiatives
The nickel-cadmium (Ni-Cd) battery recycling sector in 2025 is shaped by a combination of regulatory mandates, technological advancements, and the strategic positioning of major industry players. As environmental regulations tighten globally—particularly in the European Union, North America, and parts of Asia—manufacturers and recyclers are accelerating efforts to improve collection and processing rates for spent Ni-Cd batteries. The market is characterized by a handful of established companies with vertically integrated operations, as well as emerging players leveraging innovative recycling technologies.
One of the most prominent actors is Umicore, a Belgium-based materials technology group. Umicore operates one of the largest battery recycling facilities in Europe, with a dedicated process for Ni-Cd batteries that focuses on the recovery of nickel, cadmium, and iron. The company’s proprietary hydrometallurgical and pyrometallurgical processes are designed to maximize material recovery while minimizing environmental impact. In 2024 and 2025, Umicore has announced further investments in automation and digitalization to enhance process efficiency and traceability, aligning with the EU’s Battery Regulation requirements.
In North America, Call2Recycle stands out as a leading battery stewardship organization. It partners with manufacturers, retailers, and municipalities to collect and recycle Ni-Cd batteries across the United States and Canada. Call2Recycle’s network includes certified recycling partners that employ advanced separation and recovery technologies, ensuring compliance with both federal and state-level hazardous waste regulations. The organization has reported a steady increase in Ni-Cd battery collection volumes, driven by expanded take-back programs and public awareness campaigns.
Another significant player is Accurec Recycling GmbH, a German company specializing in the recycling of industrial batteries, including Ni-Cd chemistries. Accurec utilizes a combination of mechanical pre-treatment and vacuum thermal processes to recover cadmium in metallic form, which is then supplied back to battery manufacturers or other industries. The company has been actively investing in R&D to further reduce emissions and energy consumption, with pilot projects underway in 2025 to scale up these innovations.
Looking ahead, the industry is expected to see increased collaboration between battery manufacturers and recyclers, as well as the integration of digital tracking systems to ensure end-to-end traceability of battery materials. Strategic initiatives such as closed-loop recycling partnerships and the adoption of eco-design principles are likely to gain momentum, particularly as regulatory frameworks evolve and the demand for secondary raw materials intensifies. The ongoing efforts of major players like Umicore, Call2Recycle, and Accurec Recycling GmbH will be instrumental in shaping the future landscape of Ni-Cd battery recycling technologies.
Supply Chain Dynamics and Raw Material Recovery
Nickel-cadmium (Ni-Cd) battery recycling technologies are undergoing significant evolution as global supply chains adapt to stricter environmental regulations and the need for sustainable raw material recovery. In 2025, the recycling of Ni-Cd batteries remains a critical component of the battery industry’s circular economy, driven by both regulatory mandates and the intrinsic value of recovered nickel and cadmium.
The recycling process for Ni-Cd batteries typically involves mechanical separation, followed by hydrometallurgical or pyrometallurgical treatment to extract valuable metals. Leading companies such as Umicore and Accurec Recycling GmbH have established large-scale facilities in Europe, leveraging advanced hydrometallurgical processes to recover high-purity nickel and cadmium. Umicore, for example, operates integrated recycling plants that process a wide range of battery chemistries, including Ni-Cd, and is recognized for its closed-loop approach, returning recovered metals to the battery manufacturing supply chain.
In Asia, GEM Co., Ltd. is a prominent player, with recycling operations that focus on both Ni-Cd and other battery types. The company utilizes proprietary technologies to maximize metal recovery rates and minimize environmental impact, aligning with China’s increasingly stringent e-waste and hazardous waste regulations. Similarly, SungEel HiTech in South Korea has expanded its recycling capabilities to include Ni-Cd batteries, supporting regional supply chains for nickel and cadmium.
The supply chain dynamics for Ni-Cd battery recycling are shaped by the declining use of Ni-Cd batteries in consumer electronics, as lithium-ion chemistries become dominant. However, Ni-Cd batteries remain prevalent in industrial, emergency, and backup power applications, ensuring a steady stream of end-of-life units for recyclers. Regulatory frameworks, such as the European Union’s Battery Directive, continue to mandate high collection and recycling rates for Ni-Cd batteries, reinforcing the importance of established recycling infrastructure (Eucobat).
Looking ahead, the outlook for Ni-Cd battery recycling technologies in the next few years centers on process optimization, automation, and improved environmental performance. Companies are investing in more efficient separation and purification techniques to increase recovery yields and reduce energy consumption. Additionally, the integration of digital tracking and logistics solutions is expected to enhance the traceability of battery flows across the supply chain, supporting compliance and resource efficiency.
Overall, while the volume of Ni-Cd batteries entering the recycling stream may gradually decline, the sector’s technological advancements and regulatory drivers will ensure that raw material recovery remains robust and environmentally responsible through 2025 and beyond.
Economic and Environmental Impact Analysis
Nickel-cadmium (Ni-Cd) battery recycling technologies are undergoing significant evolution in 2025, driven by tightening environmental regulations and the economic imperative to recover valuable metals. The economic and environmental impacts of these recycling processes are increasingly scrutinized as global demand for battery materials rises and the hazards of cadmium become more widely recognized.
Economically, Ni-Cd battery recycling is shaped by the fluctuating prices of nickel and cadmium, as well as the costs associated with collection, transportation, and processing. The recovery of nickel, a critical material for stainless steel and battery manufacturing, provides a strong incentive for recycling. Leading companies such as Umicore and Accurec Recycling GmbH have established closed-loop systems that enable the efficient extraction and reuse of nickel and cadmium from spent batteries. These companies invest in hydrometallurgical and pyrometallurgical processes, which, while capital-intensive, allow for high recovery rates and the production of materials suitable for direct reuse in industry.
From an environmental perspective, Ni-Cd battery recycling is essential to prevent the release of toxic cadmium into the environment. Cadmium is classified as a hazardous substance, and improper disposal can lead to soil and water contamination. The European Union, through directives such as the Battery Directive, has mandated the collection and recycling of Ni-Cd batteries, resulting in high collection rates in member states. Companies like SNAM in France operate advanced recycling facilities that comply with strict environmental standards, minimizing emissions and ensuring safe handling of hazardous materials.
In 2025, the outlook for Ni-Cd battery recycling is influenced by the gradual phase-out of Ni-Cd batteries in many applications, replaced by lithium-ion technologies. However, significant volumes of legacy Ni-Cd batteries remain in circulation, particularly in industrial and backup power sectors. The recycling industry is expected to remain active for at least the next decade, focusing on efficient resource recovery and environmental protection. Innovations in process efficiency and automation are anticipated, with companies like Umicore investing in research to further reduce the environmental footprint of recycling operations.
- Economic incentives for recycling are closely tied to metal prices and regulatory compliance costs.
- Environmental benefits include the prevention of cadmium pollution and the conservation of natural resources.
- Industry leaders are investing in advanced technologies to improve recovery rates and reduce emissions.
- The sector is expected to remain relevant as long as legacy Ni-Cd batteries require responsible end-of-life management.
Regional Insights: North America, Europe, Asia-Pacific
Nickel-cadmium (Ni-Cd) battery recycling technologies are evolving rapidly across North America, Europe, and Asia-Pacific, driven by tightening regulations, environmental concerns, and the need to recover valuable metals. As of 2025, each region demonstrates distinct approaches and advancements in Ni-Cd battery recycling, shaped by local policy frameworks and industrial capabilities.
North America continues to emphasize producer responsibility and advanced recycling infrastructure. The United States and Canada enforce strict regulations on Ni-Cd battery disposal, with organizations such as Call2Recycle coordinating nationwide collection and recycling programs. The region’s recycling facilities typically employ hydrometallurgical and pyrometallurgical processes to recover nickel and cadmium efficiently. Major recyclers, including Umicore and Recycle Technologies, operate plants capable of processing large volumes of spent batteries, with ongoing investments in automation and emissions control. North America is also witnessing pilot projects exploring direct recycling and closed-loop systems to further reduce environmental impact.
Europe leads in regulatory stringency and technological innovation. The European Union’s Battery Directive mandates high collection and recycling rates for Ni-Cd batteries, spurring investment in state-of-the-art recycling plants. Companies such as SNAM (France) and Akkuser (Finland) utilize advanced hydrometallurgical techniques, achieving metal recovery rates exceeding 90%. Umicore, headquartered in Belgium, operates one of the world’s largest integrated battery recycling facilities, processing both industrial and consumer Ni-Cd batteries. The region is also at the forefront of research into greener leaching agents and energy-efficient processes, with several EU-funded projects targeting further improvements in recycling efficiency and safety.
Asia-Pacific is experiencing rapid growth in Ni-Cd battery recycling capacity, particularly in China, Japan, and South Korea. China, the world’s largest battery producer, has implemented strict e-waste regulations and supports a network of licensed recyclers, including major players like GEM Co., Ltd. and Hunan Brunp Recycling Technology. These companies employ both pyrometallurgical and hydrometallurgical processes, with increasing emphasis on automation and pollution control. Japan’s recycling sector, led by firms such as Sumitomo Metal Mining, focuses on high-purity metal recovery and closed-loop manufacturing. Across the region, governments are incentivizing technology upgrades and cross-border collaboration to address the growing volume of spent Ni-Cd batteries.
Looking ahead, all three regions are expected to further tighten regulations and invest in next-generation recycling technologies. The focus will be on maximizing resource recovery, minimizing environmental impact, and supporting the transition to a circular battery economy.
Challenges, Risks, and Barriers to Adoption
Nickel-cadmium (Ni-Cd) battery recycling technologies face a complex landscape of challenges, risks, and barriers to adoption as the industry moves through 2025 and into the coming years. Despite established recycling processes, several factors hinder widespread and efficient recycling of Ni-Cd batteries.
A primary challenge is the hazardous nature of cadmium, a toxic heavy metal. Stringent environmental and occupational safety regulations in regions such as the European Union and North America require specialized handling, transportation, and processing infrastructure. This increases operational costs and limits the number of facilities capable of safely recycling Ni-Cd batteries. For example, Umicore, a leading global recycler, operates advanced hydrometallurgical and pyrometallurgical facilities, but the capital and compliance requirements for such plants are significant.
Another barrier is the declining market share of Ni-Cd batteries, as lithium-ion and nickel-metal hydride chemistries become dominant in most applications. This trend reduces the volume of Ni-Cd batteries entering the waste stream, making it less economically attractive for recyclers to invest in dedicated Ni-Cd recycling lines. Companies like SNAM and Accurec Recycling GmbH continue to process Ni-Cd batteries, but often do so as part of broader multi-chemistry recycling operations, which can dilute process optimization and efficiency.
Collection rates also remain a persistent issue. Many Ni-Cd batteries are used in consumer electronics, power tools, and emergency lighting, leading to diffuse end-of-life collection points. Despite take-back schemes and producer responsibility programs, such as those coordinated by Call2Recycle in North America, significant quantities of Ni-Cd batteries are still improperly disposed of, ending up in landfills or incinerators, which poses environmental risks and reduces feedstock for recyclers.
Technological risks include the need for continuous process improvement to meet evolving regulatory standards and to recover valuable materials efficiently. The presence of mixed battery chemistries in waste streams can complicate sorting and processing, increasing the risk of contamination and reducing recovery yields. Companies like Umicore and SNAM invest in R&D to address these issues, but the pace of innovation is often constrained by the limited economic incentives associated with shrinking Ni-Cd volumes.
Looking ahead, the outlook for Ni-Cd battery recycling technologies will depend on regulatory enforcement, the effectiveness of collection schemes, and the ability of recyclers to integrate Ni-Cd processing into broader battery recycling operations. While the sector is expected to persist due to legacy waste and regulatory mandates, its growth and technological advancement may be limited compared to the rapidly expanding lithium-ion recycling industry.
Future Outlook: Opportunities and Strategic Recommendations
The future outlook for nickel-cadmium (Ni-Cd) battery recycling technologies in 2025 and the coming years is shaped by tightening environmental regulations, evolving industrial demand, and technological advancements. As global awareness of hazardous waste management grows, regulatory bodies in regions such as the European Union and North America are enforcing stricter directives on the collection and recycling of Ni-Cd batteries. The EU’s Battery Directive, for example, mandates high collection and recycling rates for portable batteries containing cadmium, driving investment in advanced recycling infrastructure.
Technological innovation is a key opportunity area. Traditional hydrometallurgical and pyrometallurgical processes are being refined to improve recovery rates, energy efficiency, and environmental performance. Companies like Umicore, a global leader in materials technology and recycling, are investing in closed-loop systems that maximize the recovery of cadmium and nickel while minimizing emissions. SNAM, a major European battery recycler, continues to expand its capacity and develop proprietary processes for the safe and efficient treatment of Ni-Cd batteries, focusing on reducing secondary waste and improving material purity.
In Asia, where industrial Ni-Cd battery use remains significant, companies such as INMETCO (a subsidiary of Inmetco, itself part of Inmetco under the Inmetco group) are scaling up recycling operations to meet both domestic and export market needs. These firms are leveraging automation and digital monitoring to enhance process control and traceability, aligning with global best practices.
Looking ahead, the market for Ni-Cd battery recycling is expected to remain robust, particularly in sectors where alternatives like lithium-ion are not yet fully viable, such as emergency lighting, aviation, and certain industrial backup systems. However, the gradual phase-out of cadmium in new batteries—driven by regulatory restrictions and the rise of less toxic chemistries—means recyclers must adapt their business models. Strategic recommendations for stakeholders include:
- Investing in R&D to further improve recovery yields and reduce environmental impact.
- Forming partnerships with battery manufacturers and end-users to secure feedstock and ensure compliance with take-back obligations.
- Expanding service offerings to include recycling of other chemistries, leveraging existing infrastructure and expertise.
- Engaging with policymakers to shape future regulations and promote sustainable recycling practices.
In summary, while the volume of Ni-Cd batteries entering the waste stream may gradually decline, the need for efficient, compliant, and environmentally sound recycling solutions will persist through 2025 and beyond. Companies that innovate and diversify will be best positioned to capture emerging opportunities in the evolving battery recycling landscape.