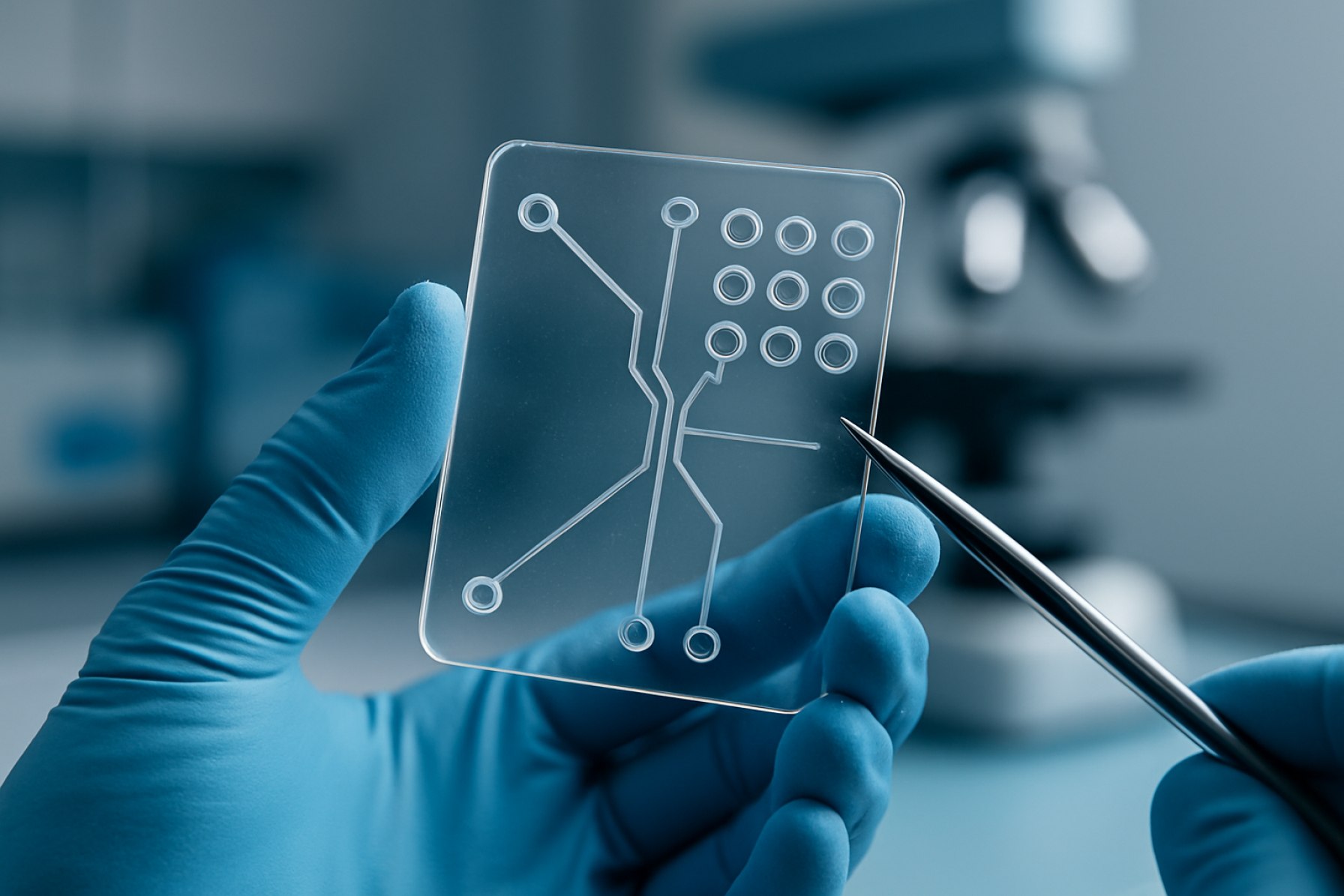
Microfluidic Lab-on-a-Chip Fabrication in 2025: Unleashing Precision, Speed, and Scalability for the Next Era of Diagnostics and Research. Explore How Advanced Manufacturing is Accelerating Market Expansion and Innovation.
- Executive Summary: Market Size, Growth Rate, and Key Drivers (2025–2030)
- Technology Landscape: Core Fabrication Methods and Emerging Innovations
- Material Advancements: Polymers, Glass, Silicon, and Hybrid Substrates
- Key Application Areas: Diagnostics, Drug Discovery, and Beyond
- Competitive Analysis: Leading Companies and Strategic Partnerships
- Regulatory Environment and Industry Standards (e.g., IEEE, ISO)
- Market Forecast: Revenue Projections and CAGR Analysis (2025–2030)
- Regional Trends: North America, Europe, Asia-Pacific, and Rest of World
- Challenges and Barriers: Scalability, Cost, and Integration
- Future Outlook: Next-Gen Technologies and Strategic Opportunities
- Sources & References
Executive Summary: Market Size, Growth Rate, and Key Drivers (2025–2030)
The global market for microfluidic lab-on-a-chip (LOC) fabrication is poised for robust growth between 2025 and 2030, driven by accelerating demand in healthcare diagnostics, life sciences research, and point-of-care testing. As of 2025, the sector is characterized by rapid technological advancements, increased adoption in clinical and industrial settings, and a growing ecosystem of established players and innovative startups.
Key industry leaders such as Dolomite Microfluidics, a subsidiary of Blacktrace Holdings, and Standard BioTools (formerly Fluidigm Corporation), continue to expand their product portfolios, offering advanced microfluidic chips and fabrication services. These companies are investing in scalable manufacturing processes, including injection molding, hot embossing, and 3D printing, to meet the rising demand for high-throughput and cost-effective LOC devices. Dolomite Microfluidics is particularly noted for its modular microfluidic systems and custom chip fabrication, serving both research and commercial applications.
The market is further propelled by the integration of microfluidics with digital health platforms and the miniaturization of diagnostic tools. The COVID-19 pandemic has underscored the value of rapid, decentralized testing, leading to increased investment in LOC technologies for infectious disease detection, cancer screening, and personalized medicine. Companies like Standard BioTools are leveraging their expertise in microfluidic chip design to enable multiplexed assays and single-cell analysis, supporting the shift toward precision diagnostics.
Geographically, North America and Europe remain the largest markets, supported by strong R&D infrastructure and favorable regulatory environments. However, Asia-Pacific is expected to witness the fastest growth, driven by expanding healthcare access, government initiatives, and the emergence of local manufacturers. Notable regional players include Microfluidic ChipShop in Germany, which specializes in polymer-based chip fabrication and custom solutions for academic and industrial clients.
Looking ahead to 2030, the microfluidic LOC fabrication market is anticipated to maintain a double-digit compound annual growth rate (CAGR), fueled by ongoing innovation in materials (such as biocompatible polymers and glass), automation of fabrication processes, and the convergence of microfluidics with artificial intelligence and IoT. Strategic collaborations between device manufacturers, diagnostics companies, and research institutions are expected to accelerate commercialization and broaden the application landscape, particularly in resource-limited settings and emerging markets.
Technology Landscape: Core Fabrication Methods and Emerging Innovations
The technology landscape for microfluidic lab-on-a-chip (LOC) fabrication in 2025 is characterized by a dynamic interplay between established manufacturing techniques and a surge of emerging innovations. Traditional methods such as soft lithography, injection molding, and hot embossing remain foundational, but the sector is witnessing rapid adoption of advanced additive manufacturing, hybrid integration, and scalable roll-to-roll processes.
Soft lithography, particularly using polydimethylsiloxane (PDMS), continues to be a mainstay for prototyping and academic research due to its flexibility and cost-effectiveness. However, for commercial-scale production, thermoplastics like cyclic olefin copolymer (COC) and polymethyl methacrylate (PMMA) are increasingly favored for their chemical resistance and compatibility with mass manufacturing. Companies such as Dolomite Microfluidics and Microfluidic ChipShop are prominent in providing both prototyping and scalable production services, leveraging injection molding and hot embossing for high-volume, reproducible chip fabrication.
Additive manufacturing, especially high-resolution 3D printing, is making significant inroads. The latest two-photon polymerization and digital light processing (DLP) techniques enable the creation of complex, multi-layered microfluidic architectures with sub-micron precision. This is particularly valuable for rapid prototyping and for integrating novel functionalities such as embedded sensors or valves. Nanoscribe is a leader in this domain, offering systems capable of fabricating intricate microfluidic structures directly from digital designs, which accelerates the design-to-device cycle.
Hybrid integration is another key trend, combining microfluidics with electronics, optics, and biosensors on a single chip. This convergence is driving the development of point-of-care diagnostics and organ-on-chip platforms. Companies like AIMicrofluidics and ZEON Corporation (producer of ZEONEX and ZEONOR COC materials) are actively developing materials and processes to support such integration, focusing on optical clarity, biocompatibility, and low autofluorescence.
Looking ahead, roll-to-roll (R2R) manufacturing is poised to transform the scalability and cost structure of microfluidic device production. R2R enables continuous fabrication of microfluidic patterns on flexible substrates, opening pathways for disposable diagnostics and wearable biosensors. DuPont and 3M are investing in R2R-compatible materials and process technologies, aiming to meet the growing demand for high-throughput, low-cost LOC devices.
In summary, the microfluidic lab-on-a-chip fabrication sector in 2025 is marked by a blend of mature and disruptive technologies. The focus is on improving scalability, integration, and device complexity, with industry leaders and material innovators shaping the next generation of LOC platforms for diagnostics, drug discovery, and environmental monitoring.
Material Advancements: Polymers, Glass, Silicon, and Hybrid Substrates
The landscape of microfluidic lab-on-a-chip (LOC) fabrication is rapidly evolving in 2025, driven by significant advancements in substrate materials. The choice of substrate—whether polymer, glass, silicon, or hybrid—directly impacts device performance, scalability, and application scope. Each material class is seeing innovation, with industry leaders and new entrants pushing the boundaries of manufacturability and function.
Polymers remain the dominant substrate for commercial LOC devices due to their low cost, ease of mass production, and biocompatibility. Poly(dimethylsiloxane) (PDMS) continues to be widely used for prototyping and research, but its limitations in chemical compatibility and scalability have spurred the adoption of thermoplastics such as cyclic olefin copolymer (COC), poly(methyl methacrylate) (PMMA), and polycarbonate. Companies like Dolomite Microfluidics and Microfluidic ChipShop are at the forefront, offering a range of polymer-based chips and custom fabrication services. In 2025, advances in injection molding and hot embossing are enabling higher throughput and finer feature resolution, making polymer LOCs more accessible for diagnostics and point-of-care applications.
Glass substrates are experiencing renewed interest, particularly for applications requiring optical transparency, chemical inertness, and high-pressure operation. The integration of glass microfluidics with advanced detection methods, such as fluorescence and Raman spectroscopy, is being actively pursued. SCHOTT, a global leader in specialty glass, is expanding its offerings for microfluidic applications, leveraging precision glass processing and bonding technologies. The development of rapid, low-temperature bonding techniques is reducing fabrication costs and broadening the use of glass in commercial LOCs.
Silicon, the original material for microfluidics, remains essential for high-precision and integrated electronic applications. The compatibility of silicon with MEMS processes allows for the integration of sensors, heaters, and actuators directly onto the chip. imec, a leading R&D hub, is advancing silicon-based microfluidics for genomics and single-cell analysis, focusing on wafer-level manufacturing and hybrid integration with photonics.
Hybrid substrates—combining polymers, glass, and silicon—are gaining traction as they enable the merging of desirable properties from each material. For example, glass-silicon hybrids offer both chemical resistance and electronic integration, while polymer-glass combinations provide cost-effective optical performance. Companies such as LioniX International are pioneering hybrid integration, particularly for photonic biosensors and lab-on-chip platforms.
Looking ahead, the next few years will see further convergence of material science and microfabrication, with a focus on sustainable materials, scalable manufacturing, and multifunctional integration. The ongoing collaboration between material suppliers, device manufacturers, and end-users is expected to accelerate the commercialization of advanced LOC systems across healthcare, environmental monitoring, and industrial analytics.
Key Application Areas: Diagnostics, Drug Discovery, and Beyond
Microfluidic lab-on-a-chip (LOC) fabrication is rapidly advancing, with 2025 poised to be a pivotal year for its application in diagnostics, drug discovery, and emerging fields. The miniaturization and integration of laboratory functions onto microchips are transforming how biological and chemical analyses are performed, offering faster, more cost-effective, and portable solutions.
In diagnostics, LOC devices are increasingly being adopted for point-of-care (POC) testing, especially in infectious disease detection and personalized medicine. Companies such as Abbott Laboratories and Thermo Fisher Scientific are at the forefront, leveraging microfluidic platforms to deliver rapid molecular diagnostics. For example, Abbott’s ID NOW system, while not strictly a microfluidic chip, exemplifies the trend toward compact, integrated diagnostic tools. Meanwhile, Thermo Fisher is investing in microfluidic consumables and instruments for genomics and proteomics, supporting the shift toward decentralized testing.
Drug discovery is another area witnessing significant impact from LOC fabrication. Microfluidic chips enable high-throughput screening of compounds, cell cultures, and organ-on-chip models, reducing reagent consumption and accelerating timelines. Dolomite Microfluidics specializes in custom microfluidic solutions for pharmaceutical research, offering modular systems that facilitate rapid prototyping and scale-up. Similarly, Standard BioTools Inc. (formerly Fluidigm) provides integrated microfluidic platforms for single-cell analysis, which are increasingly used in early-stage drug screening and biomarker discovery.
Beyond diagnostics and drug discovery, microfluidic LOC fabrication is expanding into environmental monitoring, food safety, and synthetic biology. For instance, Merck KGaA (operating as MilliporeSigma in the US and Canada) supplies microfluidic materials and components for a range of analytical applications, supporting the development of next-generation sensors and bioprocessing tools. The company’s focus on advanced polymers and surface treatments is enabling more robust and versatile chip designs.
Looking ahead, the next few years are expected to bring further integration of microfluidics with digital health platforms, AI-driven data analysis, and wireless connectivity. The adoption of scalable fabrication techniques—such as injection molding, 3D printing, and roll-to-roll processing—will be crucial for mass production and cost reduction. Industry leaders, including Carl Zeiss AG and Agilent Technologies, are investing in precision manufacturing and quality control systems to support this transition.
Overall, the convergence of microfluidic LOC fabrication with advances in materials science, automation, and data analytics is set to redefine key application areas, making laboratory-grade testing and experimentation more accessible and efficient across diverse sectors.
Competitive Analysis: Leading Companies and Strategic Partnerships
The microfluidic lab-on-a-chip (LOC) fabrication sector in 2025 is characterized by a dynamic competitive landscape, with established players and innovative startups driving advancements through strategic partnerships, technology integration, and global expansion. The market is shaped by the increasing demand for point-of-care diagnostics, personalized medicine, and high-throughput screening, prompting companies to invest in scalable manufacturing and robust supply chains.
Among the industry leaders, Dolomite Microfluidics stands out for its comprehensive suite of microfluidic chips, modular systems, and custom fabrication services. The company has continued to expand its global footprint, leveraging partnerships with academic institutions and biotechnology firms to accelerate the commercialization of novel LOC applications. Dolomite’s focus on glass and polymer chip fabrication, as well as its proprietary droplet generation technologies, positions it as a key supplier for both research and industrial clients.
Another major player, Standard BioTools (formerly Fluidigm), maintains a strong presence in the sector with its integrated microfluidic platforms for genomics and proteomics. The company’s strategic collaborations with pharmaceutical and diagnostic companies have enabled the development of next-generation LOC devices for single-cell analysis and clinical diagnostics. In 2024 and 2025, Standard BioTools has emphasized expanding its manufacturing capabilities and enhancing automation to meet growing demand.
In the Asia-Pacific region, Microfluidic ChipShop and Micronit are notable for their rapid prototyping and mass production of polymer-based microfluidic chips. Both companies have invested in advanced injection molding and hot embossing technologies, enabling cost-effective fabrication at scale. Their partnerships with medical device manufacturers and research consortia have facilitated the integration of LOC devices into diagnostic workflows, particularly in infectious disease testing and environmental monitoring.
Strategic alliances are increasingly shaping the competitive landscape. For example, collaborations between microfluidic chip manufacturers and major life science companies are accelerating the translation of research prototypes into commercial products. Companies such as Agilent Technologies and Thermo Fisher Scientific have entered into technology licensing and co-development agreements with microfluidics specialists to expand their product portfolios and address emerging market needs.
Looking ahead, the competitive environment is expected to intensify as new entrants leverage advances in 3D printing, digital microfluidics, and sustainable materials. The ongoing trend toward open innovation and cross-sector partnerships will likely drive further consolidation and the emergence of integrated solutions, positioning microfluidic LOC fabrication as a cornerstone of next-generation diagnostics and analytical instrumentation.
Regulatory Environment and Industry Standards (e.g., IEEE, ISO)
The regulatory environment and industry standards for microfluidic lab-on-a-chip (LOC) fabrication are rapidly evolving as the technology matures and its applications in diagnostics, drug development, and environmental monitoring expand. In 2025, the sector is witnessing increased attention from international standards organizations and regulatory bodies, aiming to harmonize quality, safety, and interoperability requirements.
The International Organization for Standardization (ISO) has been instrumental in developing standards relevant to microfluidics. ISO 22916:2022, for example, addresses terminology and classification for microfluidic devices, providing a common language for manufacturers and regulators. Ongoing work within ISO Technical Committee 48 (TC 48) focuses on standardizing test methods, material compatibility, and performance metrics for microfluidic systems, with new guidelines expected to be published or updated through 2025.
The Institute of Electrical and Electronics Engineers (IEEE) is also active in this space, particularly through the IEEE 2700-2017 standard, which defines a sensor performance parameter framework applicable to microfluidic sensors. In 2025, IEEE working groups are collaborating with industry stakeholders to expand standards for data interoperability and device communication, crucial for integrating LOC platforms with digital health and laboratory information systems.
In the United States, the U.S. Food and Drug Administration (FDA) continues to refine its regulatory approach to microfluidic devices, especially those intended for in vitro diagnostics (IVDs). The FDA’s Center for Devices and Radiological Health (CDRH) has issued guidance documents on the premarket submission requirements for microfluidic-based IVDs, emphasizing risk assessment, biocompatibility, and reproducibility. The agency is also piloting programs to accelerate the review of innovative LOC devices under its Breakthrough Devices Program.
Industry consortia such as the SEMI (Semiconductor Equipment and Materials International) Microfluidics Task Force are working to establish best practices for fabrication, packaging, and quality control. SEMI’s standards, such as SEMI MS1 for microfluidic device dimensions and interfaces, are gaining traction among manufacturers seeking to ensure compatibility and scalability.
Looking ahead, the regulatory landscape is expected to become more stringent and harmonized, with increased cross-border collaboration. The European Union’s In Vitro Diagnostic Regulation (IVDR), which fully applies from 2025, imposes stricter requirements on clinical performance and post-market surveillance for LOC-based diagnostics. As microfluidic technologies become more integrated into healthcare and industrial workflows, adherence to evolving standards will be critical for market access and user trust.
Market Forecast: Revenue Projections and CAGR Analysis (2025–2030)
The microfluidic lab-on-a-chip (LOC) fabrication market is poised for robust growth between 2025 and 2030, driven by expanding applications in diagnostics, drug discovery, environmental monitoring, and personalized medicine. Industry consensus points to a compound annual growth rate (CAGR) in the high single to low double digits, with revenue projections reflecting both increased adoption and technological advancements.
Key players such as Dolomite Microfluidics, a subsidiary of Blacktrace Holdings, and Standard BioTools (formerly Fluidigm Corporation), are at the forefront of commercializing microfluidic platforms and fabrication services. These companies, along with Agilent Technologies and Carl Zeiss AG, are investing in scalable manufacturing processes, including injection molding, hot embossing, and advanced photolithography, to meet rising demand for high-throughput and cost-effective LOC devices.
Recent announcements from Dolomite Microfluidics highlight the expansion of their microfluidic chip production facilities, aiming to support both prototyping and mass production for clinical and industrial clients. Similarly, Standard BioTools continues to report increased sales of its integrated fluidic circuits (IFCs), which are central to single-cell genomics and proteomics workflows.
Revenue projections for the global microfluidic LOC fabrication sector are expected to surpass several billion USD by 2030, with North America, Europe, and East Asia as leading markets. The growth is underpinned by the rapid adoption of point-of-care diagnostic devices, especially in response to global health challenges and the need for decentralized testing solutions. For instance, Agilent Technologies has expanded its microfluidics portfolio to address the growing demand for rapid, multiplexed assays in clinical and research settings.
The outlook for 2025–2030 also includes increased collaboration between device manufacturers and material suppliers, such as Carl Zeiss AG, which provides precision optics and microfabrication solutions. These partnerships are expected to accelerate the commercialization of next-generation LOC devices with enhanced sensitivity, throughput, and integration capabilities.
In summary, the microfluidic lab-on-a-chip fabrication market is set for sustained expansion, with a projected CAGR in the 8–12% range through 2030. This growth will be fueled by technological innovation, expanding application areas, and strategic investments by leading industry players.
Regional Trends: North America, Europe, Asia-Pacific, and Rest of World
The global landscape for microfluidic lab-on-a-chip (LOC) fabrication is marked by dynamic regional trends, with North America, Europe, and Asia-Pacific leading innovation and commercialization, while the Rest of World (RoW) regions are gradually increasing their participation. As of 2025, these trends are shaped by investments in healthcare, semiconductor manufacturing, and biotechnology, as well as the presence of key industry players and research institutions.
North America remains a dominant force in microfluidic LOC fabrication, driven by robust R&D infrastructure, a strong startup ecosystem, and significant funding for biomedical applications. The United States, in particular, is home to major companies such as Fluidigm Corporation (now Standard BioTools), which specializes in integrated fluidic circuits for genomics and proteomics, and Dolomite Microfluidics, which provides microfluidic chips and systems for research and industry. The region benefits from close collaboration between academia and industry, with institutions like MIT and Stanford contributing to advances in chip design and scalable fabrication methods. The U.S. government’s continued support for point-of-care diagnostics and personalized medicine is expected to sustain growth through 2025 and beyond.
Europe is characterized by a strong emphasis on quality manufacturing and regulatory compliance, with countries such as Germany, the Netherlands, and the UK at the forefront. Companies like Microfluidic ChipShop (Germany) and Dolomite Microfluidics (UK) are recognized for their expertise in polymer-based chip fabrication and custom solutions for diagnostics and drug discovery. The European Union’s Horizon Europe program continues to fund collaborative projects aimed at scaling up LOC production and integrating advanced materials, such as biocompatible polymers and glass. The region’s focus on sustainability and green manufacturing is also influencing the adoption of new fabrication techniques.
Asia-Pacific is experiencing rapid growth, fueled by expanding healthcare infrastructure, government initiatives, and a burgeoning electronics manufacturing sector. China, Japan, and South Korea are investing heavily in microfluidics, with companies like ChipSpirit (China) and Tosoh Corporation (Japan) advancing LOC fabrication for diagnostics and environmental monitoring. The region’s cost-effective manufacturing capabilities and increasing demand for point-of-care testing are expected to drive significant market expansion through the next few years. Additionally, partnerships between local universities and industry are accelerating the commercialization of novel chip designs.
Rest of World (RoW) regions, including Latin America, the Middle East, and Africa, are gradually entering the microfluidic LOC market, primarily through technology transfer and collaborations with established players. While local manufacturing is still limited, increasing investment in healthcare and diagnostics is expected to create new opportunities for regional adoption and innovation by 2025 and beyond.
Challenges and Barriers: Scalability, Cost, and Integration
Microfluidic lab-on-a-chip (LOC) fabrication is poised for significant growth in 2025 and the coming years, yet several persistent challenges and barriers continue to shape the sector’s trajectory. Chief among these are issues related to scalability, cost, and integration with existing laboratory and industrial systems.
Scalability remains a central hurdle. While prototyping microfluidic devices using soft lithography or 3D printing is now routine, transitioning from small-batch production to high-volume manufacturing is complex. Traditional methods such as photolithography and injection molding, though capable of mass production, require substantial upfront investment in cleanroom facilities and tooling. This limits accessibility for startups and smaller research groups. Companies like Dolomite Microfluidics and Fluidigm Corporation have developed modular platforms and standardized chip formats to address some of these issues, but the sector still lacks universally adopted manufacturing standards, which impedes interoperability and large-scale deployment.
Cost is another significant barrier. The price of high-precision fabrication equipment, specialized materials (such as PDMS, COC, or glass), and quality control processes can be prohibitive. While advances in polymer microfabrication and roll-to-roll processing are beginning to lower per-unit costs, these methods are not yet universally applicable to all device architectures. Furthermore, the need for biocompatibility and chemical resistance in clinical and pharmaceutical applications often necessitates the use of more expensive materials and stringent validation protocols. Companies such as ZEON Corporation (noted for their cyclo olefin polymer materials) and DuPont (a supplier of specialty polymers and films) are actively working to expand the range of cost-effective, high-performance materials available for LOC fabrication.
Integration with existing laboratory workflows and automation systems is a third major challenge. Many microfluidic devices require custom interfaces for fluidic, electronic, and data connections, complicating their adoption in established settings. Efforts by companies like AIM Biotech and Micronit to develop plug-and-play platforms and standardized connectors are ongoing, but widespread compatibility remains elusive. Additionally, regulatory requirements for clinical diagnostics and pharmaceutical manufacturing add further complexity, as devices must meet rigorous standards for reliability, traceability, and data integrity.
Looking ahead, the sector is expected to benefit from increased collaboration between material suppliers, device manufacturers, and end-users to develop scalable, cost-effective, and interoperable solutions. The emergence of open standards and modular design principles, as well as advances in digital manufacturing, are likely to play a pivotal role in overcoming current barriers and accelerating the adoption of microfluidic lab-on-a-chip technologies in both research and commercial settings.
Future Outlook: Next-Gen Technologies and Strategic Opportunities
The future of microfluidic lab-on-a-chip (LOC) fabrication is poised for significant transformation as the sector enters 2025, driven by advances in materials science, manufacturing automation, and integration with digital technologies. The next few years are expected to see a convergence of scalable production methods, novel substrate materials, and the adoption of artificial intelligence (AI) for design and process optimization.
One of the most notable trends is the shift toward high-throughput, cost-effective manufacturing. Companies such as Dolomite Microfluidics and Fluidigm Corporation are investing in automated microfabrication platforms that enable rapid prototyping and mass production of complex microfluidic devices. These systems leverage precision molding, laser ablation, and 3D printing to reduce turnaround times and support the customization required for point-of-care diagnostics and personalized medicine.
Material innovation is another key driver. While polydimethylsiloxane (PDMS) has been the dominant substrate, there is growing adoption of thermoplastics and hybrid polymers that offer improved chemical resistance, biocompatibility, and scalability. ZEON Corporation and DuPont are among the suppliers developing advanced polymer materials tailored for microfluidic applications, supporting the transition from research prototypes to commercial-grade devices.
Integration with digital technologies is accelerating. AI-driven design tools are being deployed to optimize channel geometries and fluid dynamics, reducing the need for iterative physical prototyping. Companies like Dolomite Microfluidics are also exploring the use of embedded sensors and wireless connectivity, enabling real-time data acquisition and remote device monitoring—capabilities that are increasingly demanded in decentralized healthcare and environmental monitoring.
Strategically, partnerships between microfluidic device manufacturers and end-users in diagnostics, pharmaceuticals, and environmental testing are expected to intensify. This collaborative approach is exemplified by Fluidigm Corporation, which has established alliances with clinical laboratories and biotech firms to co-develop application-specific LOC platforms.
Looking ahead, the sector is likely to benefit from regulatory harmonization and standardization efforts, which will streamline the path from prototype to market. As the global demand for rapid, portable, and multiplexed analytical tools grows, microfluidic LOC fabrication is set to play a pivotal role in next-generation healthcare, life sciences, and industrial analytics.
Sources & References
- Dolomite Microfluidics
- Standard BioTools
- Microfluidic ChipShop
- Nanoscribe
- ZEON Corporation
- DuPont
- SCHOTT
- imec
- LioniX International
- Thermo Fisher Scientific
- Carl Zeiss AG
- Micronit
- International Organization for Standardization (ISO)
- Institute of Electrical and Electronics Engineers (IEEE)
- ChipSpirit
- ZEON Corporation
- AIM Biotech