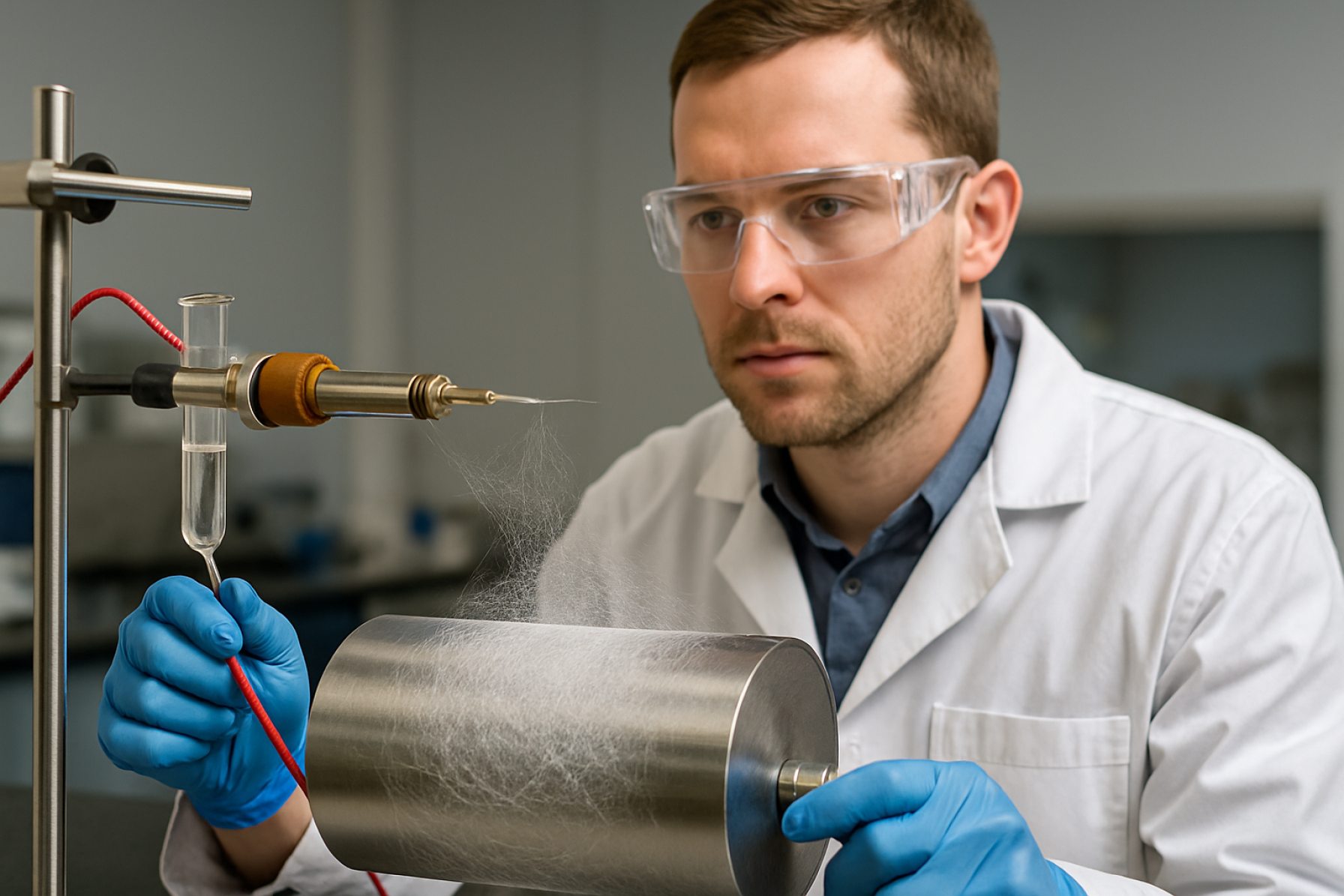
Textile Electrospinning Nanofiber Manufacturing in 2025: Transforming Fabrics with Advanced Nanotechnology. Explore Market Growth, Breakthroughs, and the Future of High-Performance Textiles.
- Executive Summary: Key Insights for 2025–2030
- Market Size, Growth Rate, and Forecast (2025–2030)
- Emerging Applications in Textiles and Beyond
- Technological Innovations in Electrospinning Processes
- Key Players and Strategic Partnerships
- Raw Materials and Supply Chain Developments
- Regulatory Landscape and Industry Standards
- Sustainability and Environmental Impact
- Regional Analysis: Leading Markets and Growth Hotspots
- Future Outlook: Opportunities, Challenges, and Disruptive Trends
- Sources & References
Executive Summary: Key Insights for 2025–2030
The textile electrospinning nanofiber manufacturing sector is poised for significant transformation between 2025 and 2030, driven by advances in scalable production, material innovation, and expanding end-use applications. Electrospinning, a process that creates ultrafine fibers from polymer solutions using electric fields, is increasingly being adopted for high-performance textiles, filtration media, medical devices, and smart fabrics. The period ahead is marked by a shift from laboratory-scale research to industrial-scale manufacturing, with several key players investing in capacity expansion and process automation.
Leading companies such as Freudenberg Group and AeroSpin Technology are at the forefront of commercializing nanofiber-based textiles. Freudenberg Group has integrated electrospun nanofibers into filtration products and technical textiles, leveraging their high surface area and tunable porosity for enhanced performance. Meanwhile, AeroSpin Technology specializes in scalable electrospinning systems, enabling mass production of nanofiber mats for diverse applications, including protective clothing and air filtration.
The industry is witnessing a surge in demand for nanofiber-enabled products, particularly in the healthcare, filtration, and smart textile sectors. For instance, the COVID-19 pandemic accelerated the adoption of nanofiber-based face masks and air filters, a trend expected to persist as regulatory standards for filtration efficiency become more stringent. Companies like Elmarco, a pioneer in industrial electrospinning equipment, are expanding their global footprint to meet this demand, offering turnkey solutions for both established manufacturers and new entrants.
Material innovation remains a key driver, with ongoing research into biodegradable and bio-based polymers to address sustainability concerns. The development of functionalized nanofibers—incorporating antimicrobial, conductive, or phase-change properties—is opening new avenues in smart textiles and wearable electronics. Organizations such as Nanofiber Labs are collaborating with textile manufacturers to integrate these advanced materials into commercial products.
Looking ahead to 2030, the outlook for textile electrospinning nanofiber manufacturing is robust. Industry bodies like INDA, Association of the Nonwoven Fabrics Industry anticipate continued growth, underpinned by investments in automation, quality control, and sustainable materials. The sector is expected to benefit from cross-industry partnerships, government support for advanced manufacturing, and the rising consumer demand for high-performance, eco-friendly textiles. As production costs decrease and process reliability improves, electrospun nanofibers are set to become a mainstream component of next-generation textile products.
Market Size, Growth Rate, and Forecast (2025–2030)
The textile electrospinning nanofiber manufacturing sector is poised for robust expansion between 2025 and 2030, driven by escalating demand for advanced materials in filtration, medical textiles, protective apparel, and energy applications. As of 2025, the global market for electrospun nanofibers in textiles is estimated to be in the low hundreds of millions USD, with projections indicating a compound annual growth rate (CAGR) exceeding 20% through 2030. This growth is underpinned by the unique properties of electrospun nanofibers—such as high surface area-to-volume ratio, tunable porosity, and enhanced mechanical performance—which are increasingly sought after in next-generation textile products.
Key industry players are scaling up production capacities and investing in automated, high-throughput electrospinning systems to meet rising demand. Freudenberg Group, a global leader in technical textiles, has expanded its nanofiber manufacturing capabilities, targeting filtration and medical applications. Similarly, Auburn Manufacturing, Inc. and Elmarco—the latter being a pioneer in industrial-scale electrospinning equipment—are actively involved in commercializing nanofiber-based textile solutions. Nanofiberlabs and Fibrothelium are also notable for their focus on specialty nanofiber textiles for biomedical and filtration markets.
The Asia-Pacific region, particularly China, Japan, and South Korea, is expected to dominate market share due to significant investments in nanotechnology infrastructure and the presence of major textile manufacturers. Companies such as Toray Industries, Inc. and Mitsui & Co., Ltd. are advancing nanofiber production for both domestic and international markets, leveraging their established supply chains and R&D capabilities.
Market growth is further catalyzed by regulatory trends favoring sustainable and high-performance textiles, as well as increased adoption in sectors such as personal protective equipment (PPE), where nanofiber membranes offer superior filtration efficiency. The COVID-19 pandemic accelerated investment in nanofiber-based mask and gown production, a trend expected to persist as healthcare and industrial safety standards evolve.
Looking ahead, the market outlook for 2025–2030 is characterized by continued innovation in scalable electrospinning technologies, integration of smart functionalities (e.g., sensors, antimicrobial properties), and expansion into new end-use sectors. Strategic collaborations between textile manufacturers, nanotechnology firms, and end-users are anticipated to further drive commercialization and market penetration of electrospun nanofiber textiles worldwide.
Emerging Applications in Textiles and Beyond
Electrospinning nanofiber manufacturing is rapidly transforming the textile sector, with 2025 marking a pivotal year for both commercial adoption and technological innovation. The process, which uses high-voltage electric fields to produce ultrafine fibers from polymer solutions, is enabling the creation of textiles with unprecedented properties—such as enhanced breathability, filtration efficiency, and functional surface area. These attributes are driving emerging applications across apparel, medical, filtration, and even energy sectors.
In the apparel industry, nanofiber-based fabrics are gaining traction for their lightweight, moisture-wicking, and antimicrobial properties. Companies like Nanofiber Labs and Fibrothelium are developing electrospun nanofiber membranes for sportswear and performance clothing, targeting improved comfort and durability. The integration of nanofibers into textiles is also being explored for smart clothing, where conductive or sensor-embedded fibers enable health monitoring and interactive features.
Medical textiles represent a significant growth area. Electrospun nanofibers are being used to fabricate wound dressings, tissue scaffolds, and drug delivery systems due to their biocompatibility and ability to mimic natural extracellular matrices. Freudenberg Group, a global leader in technical textiles, has expanded its portfolio to include nanofiber-based medical products, leveraging the technology for advanced wound care and filtration solutions. Similarly, Ahlstrom is investing in nanofiber nonwovens for medical and filtration applications, citing increased demand for high-performance materials post-pandemic.
Filtration is another sector witnessing rapid adoption. Nanofiber membranes offer superior particle capture and low airflow resistance, making them ideal for air and liquid filtration. Hollingsworth & Vose and Lydall (now part of Avient) are scaling up production of nanofiber filter media for HVAC, automotive, and industrial uses. These companies are investing in new electrospinning lines and automation to meet growing regulatory and consumer demands for cleaner air and water.
Looking ahead, the next few years are expected to see further integration of electrospun nanofibers into energy storage (such as battery separators and fuel cell membranes), protective clothing, and even agricultural textiles. Industry bodies like INDA (Association of the Nonwoven Fabrics Industry) are supporting standardization and knowledge exchange to accelerate commercialization. As manufacturing scalability improves and costs decrease, electrospinning nanofiber technology is poised to become a cornerstone of advanced textile manufacturing, with broad implications for sustainability and performance across multiple sectors.
Technological Innovations in Electrospinning Processes
The textile electrospinning nanofiber manufacturing sector is experiencing a period of rapid technological innovation as it moves into 2025, driven by the demand for advanced functional textiles in sectors such as healthcare, filtration, and smart wearables. Electrospinning, a process that uses high-voltage electric fields to produce continuous nanofibers from polymer solutions, is being refined to enable higher throughput, improved fiber uniformity, and integration with scalable textile production lines.
One of the most significant advancements is the transition from traditional single-needle electrospinning to multi-needle and needleless systems, which dramatically increase production rates. Companies such as Elmarco, a Czech-based pioneer, have commercialized industrial-scale needleless electrospinning machines capable of producing nanofiber webs at widths suitable for roll-to-roll textile manufacturing. Their Nanospider™ technology is widely adopted for applications ranging from filtration media to medical textiles, and ongoing developments focus on further scaling and automation.
In Asia, Forshung in Taiwan and Nanofiberlabs in Japan are advancing modular electrospinning platforms that allow for the integration of nanofiber layers directly onto conventional textile substrates. These systems are designed for compatibility with existing textile finishing lines, enabling the functionalization of fabrics with properties such as antimicrobial activity, water repellency, or enhanced breathability.
Material innovation is also a key trend. Companies like Fiberio in Germany are developing new polymer blends and composite nanofibers, including biodegradable and bio-based options, to meet sustainability goals and regulatory requirements. The ability to electrospin natural polymers such as cellulose and chitosan is opening new avenues for eco-friendly textile products, a trend expected to accelerate through 2025 and beyond.
Automation and digitalization are being incorporated into electrospinning lines, with real-time monitoring and process control systems ensuring consistent fiber morphology and quality. Elmarco and other leading manufacturers are investing in AI-driven process optimization, predictive maintenance, and data analytics to minimize downtime and material waste.
Looking ahead, the outlook for textile electrospinning nanofiber manufacturing is robust. The convergence of scalable production technologies, advanced materials, and digital process control is expected to lower costs and expand the range of commercial applications. Industry stakeholders anticipate that by 2027, nanofiber-enabled textiles will become mainstream in high-performance apparel, personal protective equipment, and smart textile systems, with ongoing innovation from established players and new entrants alike.
Key Players and Strategic Partnerships
The textile electrospinning nanofiber manufacturing sector is experiencing rapid evolution in 2025, driven by a combination of established industrial players, innovative startups, and strategic collaborations. The field is characterized by a blend of traditional textile manufacturers expanding into nanofiber technologies and specialized companies focusing exclusively on electrospinning processes and equipment.
Among the most prominent companies, Freudenberg Group stands out as a global leader in nonwoven textiles, with a significant focus on nanofiber-based solutions for filtration, medical, and technical textile applications. Freudenberg’s ongoing investments in R&D and its global manufacturing footprint position it as a key influencer in the adoption of electrospun nanofibers at scale.
Another major player is AeroSpin Technology, which specializes in advanced electrospinning equipment and turnkey nanofiber production lines. AeroSpin’s partnerships with textile manufacturers in Europe and Asia have accelerated the commercialization of nanofiber-based fabrics for high-performance apparel and industrial uses.
In the United States, Hollingsworth & Vose is leveraging its expertise in engineered materials to expand its nanofiber product portfolio, particularly for filtration and battery separator markets. The company’s collaborations with automotive and energy storage firms underscore the cross-sectoral relevance of electrospun nanofibers.
Strategic partnerships are a defining feature of the current landscape. For example, Elmarco, a Czech-based pioneer in industrial electrospinning machinery, has established alliances with both academic institutions and textile manufacturers to accelerate the development of scalable nanofiber production systems. Elmarco’s Nanospider™ technology is widely adopted for both research and industrial-scale manufacturing.
In Asia, Toray Industries is integrating electrospinning into its advanced materials portfolio, targeting applications in healthcare, filtration, and smart textiles. Toray’s global R&D network and history of innovation in fibers and polymers make it a significant force in shaping the future of nanofiber textiles.
Looking ahead, the next few years are expected to see increased joint ventures and technology licensing agreements, as companies seek to overcome scale-up challenges and meet growing demand in sectors such as medical textiles, air and liquid filtration, and wearable electronics. The convergence of expertise from textile, chemical, and engineering domains is likely to foster further innovation and commercialization, with leading players such as Freudenberg, Toray, and Elmarco at the forefront of these developments.
Raw Materials and Supply Chain Developments
The raw materials and supply chain landscape for textile electrospinning nanofiber manufacturing is undergoing significant transformation as the industry scales up to meet growing demand in filtration, medical, and advanced textile applications. In 2025, the sector is characterized by a shift toward high-purity polymers, increased sourcing transparency, and strategic partnerships to secure feedstock reliability.
Polyvinyl alcohol (PVA), polyacrylonitrile (PAN), polycaprolactone (PCL), and thermoplastic polyurethane (TPU) remain the dominant polymers for electrospinning, with ongoing research into biopolymers and recycled feedstocks. Major chemical suppliers such as BASF and Dow continue to expand their portfolios of high-performance polymers suitable for nanofiber production, emphasizing consistent molecular weight and purity to ensure process stability. In parallel, companies like DuPont are investing in bio-based and specialty polymers, responding to sustainability pressures and regulatory trends.
Supply chain resilience has become a focal point following recent global disruptions. Leading nanofiber manufacturers, including Freudenberg Group and Elmarco (a key supplier of industrial electrospinning equipment), are increasingly engaging in direct sourcing agreements with polymer producers to mitigate risks of shortages and price volatility. This trend is particularly pronounced in the medical and filtration sectors, where material traceability and regulatory compliance are paramount.
In 2025, the industry is also witnessing the emergence of regional supply hubs, especially in Asia and Europe, to reduce lead times and carbon footprints. For example, Toray Industries in Japan and Asahi Kasei are expanding their polymer production capacities and collaborating with local nanofiber manufacturers to streamline logistics and ensure a stable supply of specialty polymers.
Looking ahead, the next few years are expected to see further integration of recycled and bio-based raw materials, driven by both regulatory incentives and end-user demand for sustainable textiles. Companies such as Lenzing are pioneering cellulose-based nanofiber solutions, while others are exploring closed-loop systems to recover and reuse polymer waste from the electrospinning process.
Overall, the raw materials and supply chain for textile electrospinning nanofiber manufacturing in 2025 are defined by a move toward greater resilience, sustainability, and collaboration between polymer producers and nanofiber manufacturers, setting the stage for continued innovation and market expansion.
Regulatory Landscape and Industry Standards
The regulatory landscape for textile electrospinning nanofiber manufacturing is evolving rapidly as the sector matures and applications expand into critical fields such as medical textiles, filtration, and smart fabrics. In 2025, regulatory frameworks are increasingly focused on ensuring product safety, environmental sustainability, and quality assurance, reflecting both the unique properties of nanofibers and the growing scale of industrial production.
Globally, the textile nanofiber industry is subject to a patchwork of standards and guidelines, with significant activity in regions such as the European Union, the United States, and East Asia. The European Union continues to lead in nanomaterial regulation, with the Registration, Evaluation, Authorisation and Restriction of Chemicals (REACH) framework requiring detailed registration and risk assessment for nanomaterials, including those used in electrospun textiles. The European Chemicals Agency (ECHA) has issued specific guidance for nanomaterials, impacting manufacturers and importers of nanofiber-based products. In the United States, the Environmental Protection Agency (EPA) and the Food and Drug Administration (FDA) oversee nanomaterial use in consumer and medical products, respectively, with a focus on toxicity, biocompatibility, and labeling.
Industry standards are also being developed and updated to address the unique characteristics of electrospun nanofibers. The International Organization for Standardization (ISO) has published several standards relevant to nanotechnologies, such as ISO/TS 80004 for terminology and ISO/TR 13014 for material characterization. In 2025, further standardization efforts are underway to define test methods for nanofiber diameter, mechanical properties, and filtration efficiency, which are critical for quality control in textile applications. Organizations such as the American Society for Testing and Materials (ASTM) are actively working on protocols specific to nanofiber textiles.
Leading manufacturers are proactively engaging with regulatory bodies and standards organizations to ensure compliance and shape future guidelines. Companies like Freudenberg Group, a major supplier of nonwoven and nanofiber materials, and Auburn Manufacturing, Inc., which specializes in advanced textiles, are investing in certification and traceability systems. These efforts are aimed at meeting both regulatory requirements and the growing demand from end-users for transparency regarding nanomaterial content and safety.
Looking ahead, the regulatory environment is expected to become more harmonized, with increased international collaboration on standards and risk assessment methodologies. As the market for electrospun nanofiber textiles expands—particularly in healthcare, filtration, and protective apparel—regulatory scrutiny will intensify, driving innovation in safer, more sustainable manufacturing processes. Companies that anticipate and adapt to these evolving standards will be well-positioned to lead in the global market.
Sustainability and Environmental Impact
The sustainability and environmental impact of textile electrospinning nanofiber manufacturing are increasingly central to industry strategies in 2025 and beyond. As global textile production faces mounting scrutiny over resource consumption and waste, electrospinning is positioned as a transformative technology due to its potential for reduced material usage, energy efficiency, and compatibility with green materials.
Electrospinning enables the fabrication of nanofibers with high surface area-to-volume ratios, which can lead to lighter, stronger, and more functional textiles using less raw material compared to conventional spinning methods. This efficiency is particularly relevant as the industry seeks to minimize its environmental footprint. Companies such as Freudenberg Group and Auburn Manufacturing, Inc. are actively developing nanofiber-based nonwovens and technical textiles, emphasizing both performance and sustainability in their product lines.
A key sustainability advantage of electrospinning is its compatibility with bio-based and biodegradable polymers. For example, Fitesa, a global supplier of nonwoven solutions, has expanded its portfolio to include biopolymer-based nanofiber materials, targeting applications in hygiene and medical textiles. The use of renewable feedstocks and compostable polymers is expected to grow, driven by regulatory pressures and consumer demand for eco-friendly products.
Water and energy consumption are also critical considerations. Electrospinning typically operates at ambient temperatures and does not require water as a processing medium, unlike traditional wet spinning or dyeing processes. This can significantly reduce the environmental burden associated with textile manufacturing. Companies such as Nanofiber Labs are investing in process optimization to further lower energy requirements and scale up production while maintaining environmental standards.
Waste reduction is another area where electrospinning offers promise. The precision of the process allows for minimal material loss, and the ability to recycle off-spec fibers or integrate recycled polymers into the feedstock is under active development. Industry initiatives, such as those led by Freudenberg Group, are exploring closed-loop systems and circular economy models for nanofiber textiles.
Looking ahead, the outlook for sustainable electrospinning in textiles is positive. Ongoing research into solvent-free and water-based electrospinning, as well as the adoption of renewable energy sources in manufacturing, are expected to further enhance the environmental profile of nanofiber production. As regulatory frameworks tighten and end-users demand greener products, the sector is likely to see accelerated adoption of sustainable practices and materials, positioning electrospinning as a key enabler of the textile industry’s transition to a more circular and responsible future.
Regional Analysis: Leading Markets and Growth Hotspots
The global landscape for textile electrospinning nanofiber manufacturing in 2025 is characterized by dynamic regional growth, with Asia-Pacific, North America, and Europe emerging as the principal markets. These regions are distinguished by their advanced manufacturing infrastructure, robust R&D ecosystems, and increasing demand for high-performance textiles in sectors such as filtration, medical, and protective apparel.
Asia-Pacific continues to dominate the market, driven by the presence of major textile manufacturing hubs and rapid industrialization. China, in particular, is a focal point, with companies such as Donghua University and Sinofibers actively advancing electrospinning technologies and scaling up production capacities. South Korea and Japan are also significant contributors, leveraging their expertise in nanotechnology and materials science. For instance, Toray Industries in Japan is recognized for its innovations in nanofiber-based textiles, targeting both domestic and international markets.
North America is witnessing robust growth, particularly in the United States, where a strong focus on advanced materials and medical applications is evident. Companies such as FibeRio Technology Corporation and Elmarco (with a significant presence in both the US and Europe) are at the forefront of commercializing scalable electrospinning equipment and nanofiber products. The region benefits from collaborations between industry and research institutions, fostering innovation and accelerating the adoption of nanofiber textiles in filtration, wound care, and smart textiles.
Europe remains a key player, with Germany, the Czech Republic, and the United Kingdom leading in both research and industrial deployment. Freudenberg Group in Germany is notable for integrating nanofiber technology into filtration and performance apparel, while Elmarco (headquartered in the Czech Republic) is a global supplier of industrial electrospinning machinery. The European Union’s emphasis on sustainable and high-value textiles further supports regional growth, with ongoing investments in eco-friendly nanofiber production.
Looking ahead to the next few years, these regions are expected to maintain their leadership, propelled by continued investments in R&D, expansion of production facilities, and growing end-user demand. Emerging markets in Southeast Asia and the Middle East are also anticipated to increase their participation, supported by technology transfer and strategic partnerships with established players. The global outlook for textile electrospinning nanofiber manufacturing remains positive, with regional hotspots driving innovation and market expansion.
Future Outlook: Opportunities, Challenges, and Disruptive Trends
The future of textile electrospinning nanofiber manufacturing is poised for significant transformation as the industry enters 2025 and beyond. The convergence of advanced materials science, automation, and sustainability imperatives is shaping both opportunities and challenges for manufacturers and end-users.
One of the most promising opportunities lies in the scaling up of nanofiber production for high-value applications. Companies such as Fraunhofer and Elmarco are at the forefront of developing industrial-scale electrospinning equipment, enabling the transition from laboratory to mass production. These advancements are critical for meeting the growing demand in sectors such as medical textiles, filtration, and smart wearables. For example, Elmarco has commercialized needleless electrospinning technology, which allows for higher throughput and more consistent nanofiber mat production, addressing a key bottleneck in the industry.
Sustainability is another major driver. The push for biodegradable and bio-based nanofibers is intensifying, with companies like Fraunhofer and Nanofiberlabs (a US-based innovator) investing in research to replace petroleum-based polymers with renewable alternatives. This trend is expected to accelerate as regulatory pressures and consumer preferences shift toward greener materials, especially in the European Union and North America.
However, several challenges persist. Uniformity and reproducibility of nanofiber properties at scale remain technical hurdles. The sensitivity of the electrospinning process to environmental conditions and the need for precise control over fiber morphology require ongoing innovation in process monitoring and automation. Companies such as Elmarco are addressing these issues by integrating real-time quality control systems into their manufacturing lines.
Disruptive trends are also emerging. The integration of functional additives—such as antimicrobial agents, conductive materials, or phase-change materials—into nanofibers is opening new markets in healthcare, energy storage, and smart textiles. Collaborative efforts between textile manufacturers and technology providers, such as those fostered by AITEX (the Textile Industry Research Association in Spain), are accelerating the commercialization of multifunctional nanofiber products.
Looking ahead, the sector is expected to see increased investment in automation, digitalization, and sustainable materials. The next few years will likely witness the emergence of new business models, such as contract nanofiber manufacturing and on-demand production, further democratizing access to advanced textile technologies. As the ecosystem matures, partnerships between research institutes, equipment manufacturers, and end-users will be crucial in overcoming technical and market barriers, ensuring that electrospun nanofibers become a mainstream component of the global textile industry.
Sources & References
- Freudenberg Group
- Elmarco
- Nanofiber Labs
- INDA, Association of the Nonwoven Fabrics Industry
- Auburn Manufacturing, Inc.
- Fibrothelium
- Toray Industries, Inc.
- Mitsui & Co., Ltd.
- Ahlstrom
- Hollingsworth & Vose
- Lydall
- Avient
- BASF
- DuPont
- Elmarco
- Asahi Kasei
- Lenzing
- Fitesa
- Fraunhofer
- AITEX