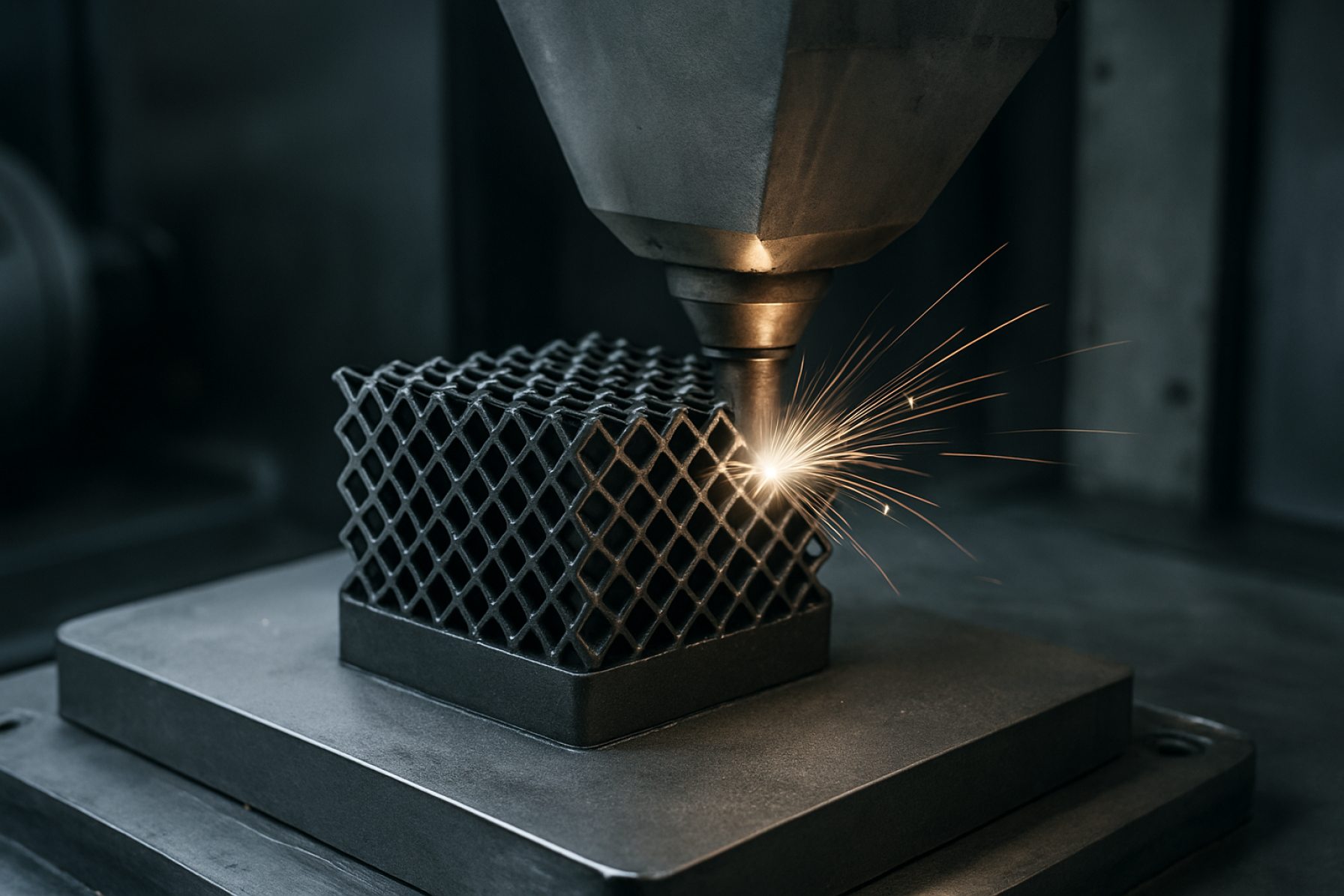
Bulk Metallic Glass 3D Printing in 2025: Transforming Advanced Manufacturing with Unmatched Strength and Precision. Explore Market Growth, Technology Innovations, and the Road Ahead.
- Executive Summary: 2025 Market Outlook and Key Drivers
- Bulk Metallic Glass Fundamentals: Properties and Advantages
- 3D Printing Technologies for Bulk Metallic Glass: Current State and Innovations
- Key Industry Players and Strategic Partnerships
- Market Size, Segmentation, and 2025–2030 Growth Forecasts
- Emerging Applications: Aerospace, Medical, Electronics, and Beyond
- Supply Chain, Material Sourcing, and Manufacturing Challenges
- Intellectual Property, Standards, and Regulatory Landscape
- Competitive Analysis and Barriers to Entry
- Future Outlook: Disruptive Trends and Opportunities through 2030
- Sources & References
Executive Summary: 2025 Market Outlook and Key Drivers
Bulk Metallic Glass (BMG) 3D printing is emerging as a transformative technology in advanced manufacturing, offering a unique combination of high strength, elasticity, and corrosion resistance. As of 2025, the market for BMG 3D printing is characterized by rapid innovation, with key drivers including the demand for high-performance components in aerospace, medical, and electronics sectors, as well as ongoing advancements in additive manufacturing hardware and feedstock development.
The current landscape is shaped by the efforts of pioneering companies and research institutions. Amorphology, a spin-out from NASA’s Jet Propulsion Laboratory, remains a leader in the commercialization of BMGs for precision gears and components, leveraging additive manufacturing to produce parts with complex geometries and superior mechanical properties. ExOne, now part of Desktop Metal, has also demonstrated binder jetting processes for BMGs, expanding the range of printable materials and enabling new applications in tooling and prototyping.
In 2025, the adoption of BMG 3D printing is being propelled by several key factors:
- Material Performance: BMGs offer a unique amorphous structure, resulting in exceptional hardness and wear resistance, which is highly attractive for industries requiring miniaturized, high-precision parts.
- Process Innovation: Advances in laser-based and binder jetting additive manufacturing systems are enabling the reliable processing of BMGs, overcoming previous challenges related to crystallization and brittleness during fabrication.
- Supply Chain Resilience: The ability to produce complex BMG parts on-demand supports decentralized manufacturing models, reducing lead times and inventory costs for critical components.
Looking ahead, the next few years are expected to see further integration of BMG 3D printing into high-value applications. Aerospace and defense sectors are anticipated to increase adoption due to the weight savings and durability offered by BMG components. The medical device industry is also exploring BMGs for minimally invasive surgical tools and implants, capitalizing on their biocompatibility and precision. Companies such as Amorphology are actively collaborating with OEMs to scale up production and qualify BMG parts for mission-critical uses.
While the market remains niche compared to conventional metal additive manufacturing, the unique properties of BMGs and the maturation of 3D printing processes are expected to drive steady growth through 2025 and beyond. Strategic partnerships between material innovators, equipment manufacturers, and end-users will be crucial in overcoming technical barriers and unlocking new commercial opportunities in the BMG 3D printing sector.
Bulk Metallic Glass Fundamentals: Properties and Advantages
Bulk metallic glasses (BMGs) are a unique class of amorphous metals characterized by their disordered atomic structure, which imparts exceptional mechanical and physical properties. Unlike crystalline metals, BMGs lack grain boundaries, resulting in high strength, superior elasticity, and remarkable corrosion resistance. These attributes make BMGs highly attractive for advanced engineering applications, particularly in sectors demanding high-performance materials such as aerospace, medical devices, and precision tooling.
The advent of 3D printing, or additive manufacturing (AM), has opened new avenues for processing BMGs, overcoming traditional challenges associated with casting and machining. In 2025, the integration of BMGs with 3D printing technologies is gaining momentum, driven by the need for complex geometries and customized components that leverage the unique properties of these materials. The most common AM techniques for BMGs include selective laser melting (SLM), laser powder bed fusion (LPBF), and direct energy deposition (DED). These methods enable rapid cooling rates necessary to retain the amorphous structure during solidification.
Key properties of BMGs relevant to 3D printing include:
- High strength-to-weight ratio: BMGs can exhibit yield strengths up to twice that of conventional titanium alloys, making them ideal for lightweight, high-strength parts.
- Elastic limit: BMGs can undergo elastic deformation up to 2%—significantly higher than most metals—enabling energy absorption and resilience in functional components.
- Corrosion and wear resistance: The absence of grain boundaries and passive oxide layers provide excellent resistance to environmental degradation.
- Precision and surface finish: The amorphous structure allows for the production of components with fine features and smooth surfaces, reducing post-processing requirements.
In 2025, several industry leaders are actively developing and commercializing BMG 3D printing solutions. Amorphology, a spin-off from NASA’s Jet Propulsion Laboratory, specializes in BMG alloys and has pioneered the use of additive manufacturing for producing gears and precision components. Heraeus, a global materials technology group, offers BMG powders and collaborates with additive manufacturing equipment manufacturers to optimize process parameters for industrial-scale production. Exmet, based in Sweden, focuses on the development of BMG feedstock and process integration for AM, targeting applications in medical and aerospace sectors.
Looking ahead, the outlook for BMG 3D printing is promising. Ongoing research aims to expand the range of printable BMG compositions, improve process reliability, and scale up production for larger and more complex parts. As additive manufacturing platforms become more sophisticated and material costs decrease, BMGs are expected to transition from niche applications to broader industrial adoption, unlocking new possibilities in high-performance engineering and design.
3D Printing Technologies for Bulk Metallic Glass: Current State and Innovations
Bulk metallic glass (BMG) 3D printing is emerging as a transformative technology in advanced manufacturing, leveraging the unique amorphous structure of BMGs to deliver components with exceptional strength, elasticity, and corrosion resistance. As of 2025, the field is witnessing significant progress, driven by both established industry leaders and innovative startups.
The most prevalent 3D printing technologies for BMGs are laser-based powder bed fusion (PBF-LB) and direct energy deposition (DED). These methods enable rapid cooling rates necessary to retain the amorphous structure of BMGs during fabrication. Notably, Amorphology, a spin-out from NASA’s Jet Propulsion Laboratory, has been at the forefront of commercializing BMG 3D printing. The company specializes in precision gears and components for robotics and aerospace, utilizing proprietary alloys and additive manufacturing processes to achieve near-net-shape parts with minimal post-processing.
Another key player, ExOne, has explored binder jetting for metallic glasses, focusing on scalability and cost-effectiveness for industrial applications. Meanwhile, Desktop Metal has developed systems compatible with BMG powders, targeting rapid prototyping and low-volume production for high-performance applications.
In the research and development landscape, collaborations between industry and academia are accelerating innovation. For example, Honeywell has partnered with research institutions to investigate the use of BMGs in aerospace components, aiming to exploit their superior wear resistance and mechanical properties. Additionally, GE has invested in additive manufacturing platforms capable of processing advanced metallic glasses, with a focus on turbine and medical device applications.
Recent advancements have addressed key challenges such as controlling crystallization during printing and optimizing process parameters for consistent amorphous structures. In 2024 and 2025, several groups have reported successful fabrication of complex BMG geometries with mechanical properties rivaling or exceeding those of conventionally cast BMGs. The integration of in-situ monitoring and closed-loop feedback systems is further enhancing process reliability and part quality.
Looking ahead, the outlook for BMG 3D printing is promising. Industry analysts anticipate broader adoption in sectors requiring high-performance, wear-resistant parts, such as medical devices, aerospace, and precision engineering. Ongoing material development, coupled with advances in printer hardware and process control, is expected to expand the range of printable BMG alloys and enable larger, more complex components. As companies like Amorphology and Desktop Metal continue to scale their offerings, BMG 3D printing is poised to become a mainstream solution for demanding engineering applications in the coming years.
Key Industry Players and Strategic Partnerships
The landscape of bulk metallic glass (BMG) 3D printing in 2025 is shaped by a select group of pioneering companies and strategic collaborations that are accelerating the commercialization and adoption of this advanced manufacturing technology. BMGs, known for their unique amorphous structure and exceptional mechanical properties, have attracted the attention of both established industry leaders and innovative startups seeking to unlock new applications in aerospace, medical devices, and high-performance tooling.
A central player in the BMG 3D printing sector is Amorphology, a California-based company spun out of NASA’s Jet Propulsion Laboratory. Amorphology specializes in the development and additive manufacturing of BMG components, leveraging proprietary alloy formulations and process expertise. In recent years, Amorphology has expanded its partnerships with aerospace and robotics firms, focusing on the production of wear-resistant gears and precision parts that benefit from the unique properties of BMGs. The company’s collaborations with major aerospace OEMs and robotics manufacturers are expected to deepen through 2025, as demand for lightweight, high-strength components grows.
Another significant contributor is Heraeus, a global technology group with a dedicated division for amorphous metals. Heraeus has invested heavily in the development of BMG feedstock materials optimized for additive manufacturing processes, including laser powder bed fusion and direct energy deposition. The company’s strategic alliances with 3D printer manufacturers and research institutions have resulted in the commercialization of new BMG alloys and the refinement of printing parameters, enabling broader adoption in industrial sectors. Heraeus’s ongoing collaborations with machine builders and end-users are anticipated to yield further advancements in print quality and scalability over the next few years.
In the additive manufacturing hardware space, Desktop Metal has emerged as a key enabler of BMG 3D printing. The company’s Studio System platform supports the processing of amorphous metal powders, and Desktop Metal has worked closely with material suppliers to qualify BMGs for its binder jetting and sintering workflows. This integration is expected to facilitate the entry of BMGs into prototyping and low-volume production environments, particularly in the medical and consumer electronics sectors.
Strategic partnerships between material innovators, printer manufacturers, and end-users are expected to intensify through 2025 and beyond. These collaborations are critical for overcoming technical challenges such as controlling crystallization during printing and ensuring repeatable part quality. As intellectual property portfolios expand and pilot projects transition to commercial production, the BMG 3D printing ecosystem is poised for significant growth, with industry leaders like Amorphology, Heraeus, and Desktop Metal at the forefront of this transformation.
Market Size, Segmentation, and 2025–2030 Growth Forecasts
The market for Bulk Metallic Glass (BMG) 3D printing is emerging as a specialized segment within the broader additive manufacturing industry, driven by the unique properties of BMGs—such as high strength, elasticity, and corrosion resistance—that are unattainable with conventional crystalline metals. As of 2025, the global BMG 3D printing market remains in its nascent stage, with commercial activity primarily concentrated in North America, Europe, and select parts of Asia. The market size is estimated to be in the low tens of millions USD, but is projected to grow at a compound annual growth rate (CAGR) exceeding 25% through 2030, as more industries recognize the advantages of BMGs for high-performance applications.
Segmentation of the BMG 3D printing market is primarily based on end-use industry, material composition, and printing technology. Key end-use sectors include aerospace, medical devices, electronics, and luxury goods. Aerospace and defense are expected to remain the largest consumers, leveraging BMGs for lightweight, high-strength components. The medical sector is also a significant adopter, utilizing BMGs for surgical tools and implants due to their biocompatibility and wear resistance. In terms of material, zirconium-based BMGs dominate current commercial offerings, though research into titanium- and magnesium-based BMGs is ongoing.
On the technology front, laser-based additive manufacturing methods—such as selective laser melting (SLM) and laser powder bed fusion (LPBF)—are the most widely used for BMGs, given their ability to rapidly cool molten metal and prevent crystallization. Companies like Amorphology (a Caltech spin-out) are at the forefront, offering both BMG feedstock and proprietary 3D printing solutions. ExOne, now part of Desktop Metal, has also demonstrated binder jetting of BMGs, expanding the range of printable geometries and part sizes. In Europe, Heraeus is a notable supplier of BMG powders and has partnered with additive manufacturing equipment manufacturers to optimize process parameters for industrial-scale production.
Looking ahead to 2030, the BMG 3D printing market is expected to benefit from continued advances in feedstock quality, process control, and post-processing techniques. The entry of larger metal 3D printing system manufacturers and materials suppliers is anticipated, which will help drive down costs and expand the addressable market. Regulatory approvals in the medical and aerospace sectors will further accelerate adoption. As intellectual property barriers diminish and open innovation increases, the market is likely to see a proliferation of new BMG alloys and application-specific solutions, positioning BMG 3D printing as a high-value niche within the broader additive manufacturing landscape.
Emerging Applications: Aerospace, Medical, Electronics, and Beyond
Bulk metallic glass (BMG) 3D printing is rapidly transitioning from laboratory research to real-world applications, with 2025 marking a pivotal year for its adoption in high-value sectors. BMGs, also known as amorphous metals, offer a unique combination of high strength, elasticity, corrosion resistance, and processability, making them attractive for industries demanding advanced material performance.
In aerospace, the drive for lightweight, high-strength components is accelerating the integration of BMG 3D printing. Companies such as NASA have been actively investigating BMGs for use in spacecraft mechanisms and structural parts, leveraging their superior wear resistance and the ability to produce complex geometries with additive manufacturing. The potential to print near-net-shape parts with minimal post-processing is particularly valuable for reducing both weight and cost in aerospace assemblies. In 2025, collaborative projects between government agencies and private aerospace manufacturers are expected to yield the first flight-qualified BMG 3D printed components, especially for satellite and unmanned aerial vehicle (UAV) applications.
The medical sector is another early adopter, capitalizing on BMGs’ biocompatibility and non-magnetic properties. Companies like Zimmer Biomet and Smith+Nephew are exploring BMG 3D printing for next-generation surgical tools, orthopedic implants, and dental devices. The ability to custom-print patient-specific implants with enhanced mechanical properties and smooth, wear-resistant surfaces is expected to drive regulatory submissions and pilot clinical use cases in 2025 and beyond. Additionally, the amorphous structure of BMGs reduces bacterial adhesion, a critical advantage for implantable devices.
In electronics, BMGs’ unique combination of high strength and soft magnetic properties is opening new avenues for miniaturized components. VACUUMSCHMELZE, a leader in advanced magnetic materials, is actively developing BMG-based components for inductors, transformers, and precision connectors. The precision of 3D printing enables the fabrication of intricate geometries that are difficult or impossible to achieve with traditional manufacturing, supporting the ongoing miniaturization trend in consumer and industrial electronics.
Beyond these sectors, BMG 3D printing is being explored for high-performance sporting goods, luxury watches, and even defense applications, where the combination of strength, elasticity, and corrosion resistance is highly valued. As machine manufacturers such as Desktop Metal and EOS continue to refine process parameters and expand material portfolios, the next few years are expected to see broader commercialization and the emergence of new application domains. The outlook for 2025 and beyond is one of accelerating adoption, driven by ongoing advances in both BMG alloy development and additive manufacturing technology.
Supply Chain, Material Sourcing, and Manufacturing Challenges
Bulk metallic glass (BMG) 3D printing is emerging as a transformative technology, but its supply chain, material sourcing, and manufacturing landscape in 2025 faces unique challenges and opportunities. BMGs—amorphous alloys with exceptional strength and elasticity—require precise alloy compositions and rapid cooling rates, making their production and processing more complex than conventional metals.
The supply chain for BMG 3D printing begins with the sourcing of high-purity raw materials, such as zirconium, titanium, copper, and nickel. These elements must be carefully alloyed to achieve the desired glass-forming ability. In 2025, the availability of these metals remains generally stable, but geopolitical factors and increased demand from aerospace and electronics sectors can cause price volatility, particularly for zirconium and rare earth elements. Companies like Materion Corporation and AMETEK, Inc. are among the recognized suppliers of specialty alloys and high-purity metals, supporting the BMG supply chain.
Material sourcing is further complicated by the need for ultra-clean processing environments to prevent contamination, which can compromise the amorphous structure. Only a handful of manufacturers globally have the capability to produce BMG feedstock at the required purity and in the powder or wire forms suitable for additive manufacturing. Liquidmetal Technologies remains a key player, holding patents and proprietary processes for BMG production and licensing its technology to partners in the medical, consumer electronics, and industrial sectors.
On the manufacturing side, the main challenge is adapting 3D printing hardware to handle BMGs’ unique thermal properties. BMGs require extremely high cooling rates (often above 1000 K/s) to avoid crystallization, which limits the choice of additive manufacturing techniques. Laser-based powder bed fusion and direct energy deposition are being refined to accommodate these requirements, but process control and repeatability remain hurdles. Equipment manufacturers such as GE (through its additive division) and TRUMPF Group are actively developing systems capable of processing advanced alloys, including BMGs, though widespread commercial availability is still in its early stages.
Looking ahead, the outlook for BMG 3D printing supply chains is cautiously optimistic. Industry collaborations are underway to standardize BMG feedstock specifications and improve recycling of offcuts and failed prints, which could reduce costs and material waste. However, scaling up production to meet anticipated demand in aerospace, medical, and tooling applications will require significant investment in both material production and printer technology. As more companies enter the field and as process reliability improves, the supply chain is expected to become more robust, but for now, BMG 3D printing remains a specialized, high-value manufacturing niche.
Intellectual Property, Standards, and Regulatory Landscape
The intellectual property (IP), standards, and regulatory landscape for Bulk Metallic Glass (BMG) 3D printing is rapidly evolving as the technology matures and commercial interest intensifies. As of 2025, the sector is characterized by a growing portfolio of patents, the emergence of preliminary standards, and the initial steps toward regulatory frameworks tailored to the unique properties and applications of BMGs.
Key players in BMG 3D printing, such as Amorphology and Heraeus, have been actively filing patents covering both proprietary BMG alloy compositions and novel additive manufacturing (AM) processes. Amorphology, a spin-out from NASA’s Jet Propulsion Laboratory, holds a significant IP portfolio in BMG feedstock and process optimization, particularly for high-precision gears and aerospace components. Heraeus, a global materials technology group, has developed and patented BMG powders and wire feedstocks, as well as process parameters for laser-based AM systems. The competitive IP landscape is further complicated by cross-licensing and collaborative agreements, as companies seek to accelerate commercialization while protecting core innovations.
On the standards front, organizations such as ASTM International and International Organization for Standardization (ISO) have begun to address the unique challenges posed by BMGs in additive manufacturing. While no BMG-specific AM standards have been fully ratified as of early 2025, working groups within ASTM F42 (Additive Manufacturing Technologies) and ISO/TC 261 are actively developing guidelines for material characterization, process qualification, and mechanical testing of BMG parts. These efforts are expected to yield draft standards within the next two to three years, providing a foundation for quality assurance and interoperability across the industry.
Regulatory oversight is also in its formative stages. For applications in medical devices and aerospace, regulatory bodies such as the U.S. Food and Drug Administration (FDA) and the European Union Aviation Safety Agency (EASA) are monitoring developments in BMG 3D printing. The FDA, for instance, has issued general guidance on additive manufacturing of medical devices, but BMG-specific pathways are still under discussion, particularly regarding biocompatibility and long-term performance. Similarly, aerospace regulators are evaluating the structural integrity and reliability of BMG components produced via AM, with certification processes expected to evolve as more data becomes available.
Looking ahead, the next few years will likely see a surge in patent filings as new BMG alloys and AM techniques are developed, alongside the formalization of standards and clearer regulatory pathways. This evolving landscape will be critical in enabling broader adoption of BMG 3D printing in high-value sectors, while ensuring safety, reliability, and fair competition.
Competitive Analysis and Barriers to Entry
Bulk metallic glass (BMG) 3D printing remains a highly specialized segment within the broader additive manufacturing (AM) industry as of 2025. The competitive landscape is shaped by a small number of pioneering companies, significant intellectual property (IP) barriers, and the technical complexity of both BMG materials and the required printing processes.
Key players in the BMG 3D printing space include Amorphology, a California-based company spun out of NASA’s Jet Propulsion Laboratory, which focuses on BMG alloys and precision components for aerospace, robotics, and medical applications. Amorphology has developed proprietary alloy compositions and printing techniques, positioning itself as a leader in the commercialization of BMG AM. Another notable entity is Exmet AB of Sweden, which collaborates with global partners to develop and license BMG feedstock and printing solutions, targeting industries such as automotive and consumer electronics.
The competitive advantage of these companies is reinforced by robust patent portfolios covering both alloy formulations and process innovations. For example, Amorphology holds patents on BMG compositions optimized for additive manufacturing, as well as on methods for producing amorphous parts with minimal crystallization. This IP landscape creates a high barrier to entry for new entrants, who must either license technology or invest heavily in R&D to circumvent existing patents.
Another significant barrier is the technical challenge of processing BMGs. Unlike conventional metals, BMGs require precise thermal management to avoid crystallization during printing. This necessitates specialized equipment, such as high-performance laser or electron beam systems, and advanced process monitoring. As a result, only a handful of machine manufacturers, such as EOS GmbH and GE Additive, are actively exploring or supporting BMG-compatible AM platforms, often in partnership with material specialists.
Supply chain limitations also restrict market entry. The production of high-purity BMG feedstock is complex and costly, with few suppliers able to meet the stringent requirements for additive manufacturing. Companies like Exmet AB have established proprietary feedstock production methods, further consolidating their market position.
Looking ahead, the outlook for new entrants remains challenging through the next several years. The need for multidisciplinary expertise—spanning materials science, process engineering, and application development—means that successful market entry will likely require strategic partnerships or licensing agreements with established players. However, as demand for high-performance, lightweight components grows in sectors such as aerospace, medical devices, and electronics, there is potential for increased collaboration and gradual expansion of the competitive landscape, particularly as more machine manufacturers and material suppliers invest in BMG-compatible technologies.
Future Outlook: Disruptive Trends and Opportunities through 2030
Bulk metallic glass (BMG) 3D printing is poised for significant advancements and disruptive impact through 2030, driven by ongoing research, industrial adoption, and the convergence of additive manufacturing with advanced materials science. As of 2025, the field is transitioning from laboratory-scale demonstrations to early-stage commercial applications, with several key trends shaping its future trajectory.
One of the most notable developments is the increasing involvement of established additive manufacturing companies and materials suppliers in BMG 3D printing. Heraeus, a global leader in precious and special metals, has been at the forefront, developing proprietary BMG alloys and collaborating with 3D printer manufacturers to optimize process parameters for reliable part production. Their work has enabled the fabrication of complex, high-strength components with superior wear and corrosion resistance, targeting industries such as medical devices, aerospace, and electronics.
Another key player, Amorphology, a spin-off from NASA’s Jet Propulsion Laboratory, specializes in BMG-based gears and precision components. The company has demonstrated the viability of BMG 3D printing for producing parts with exceptional hardness and elasticity, which are difficult to achieve with conventional crystalline metals. Amorphology’s partnerships with robotics and automotive manufacturers signal a growing interest in leveraging BMGs for high-performance, lightweight applications.
Technological advancements are also accelerating. The development of new 3D printing techniques—such as laser-based powder bed fusion and direct energy deposition—tailored for BMGs is overcoming previous challenges related to crystallization and process control. Companies like Desktop Metal have announced research initiatives and prototype systems capable of processing BMG powders, aiming to bring scalable solutions to market within the next few years.
Looking ahead to 2030, several disruptive trends are anticipated:
- Expansion of BMG alloy portfolios, enabling tailored properties for specific applications and broader adoption across industries.
- Integration of BMG 3D printing into digital manufacturing ecosystems, allowing for on-demand production of high-value, custom parts.
- Cost reductions through process optimization and increased availability of BMG feedstocks, making the technology accessible beyond niche markets.
- Emergence of hybrid manufacturing approaches, combining BMG 3D printing with traditional processes for multi-material or functionally graded components.
As intellectual property portfolios expand and standards for BMG additive manufacturing mature, the sector is expected to move from prototyping to full-scale production in critical sectors. The unique combination of mechanical performance and design freedom offered by BMG 3D printing positions it as a transformative technology for the next generation of engineered products.
Sources & References
- Amorphology
- ExOne
- Heraeus
- Desktop Metal
- Honeywell
- GE
- NASA
- Zimmer Biomet
- Smith+Nephew
- EOS
- Materion Corporation
- AMETEK, Inc.
- Liquidmetal Technologies
- ASTM International
- International Organization for Standardization (ISO)
- European Union Aviation Safety Agency (EASA)