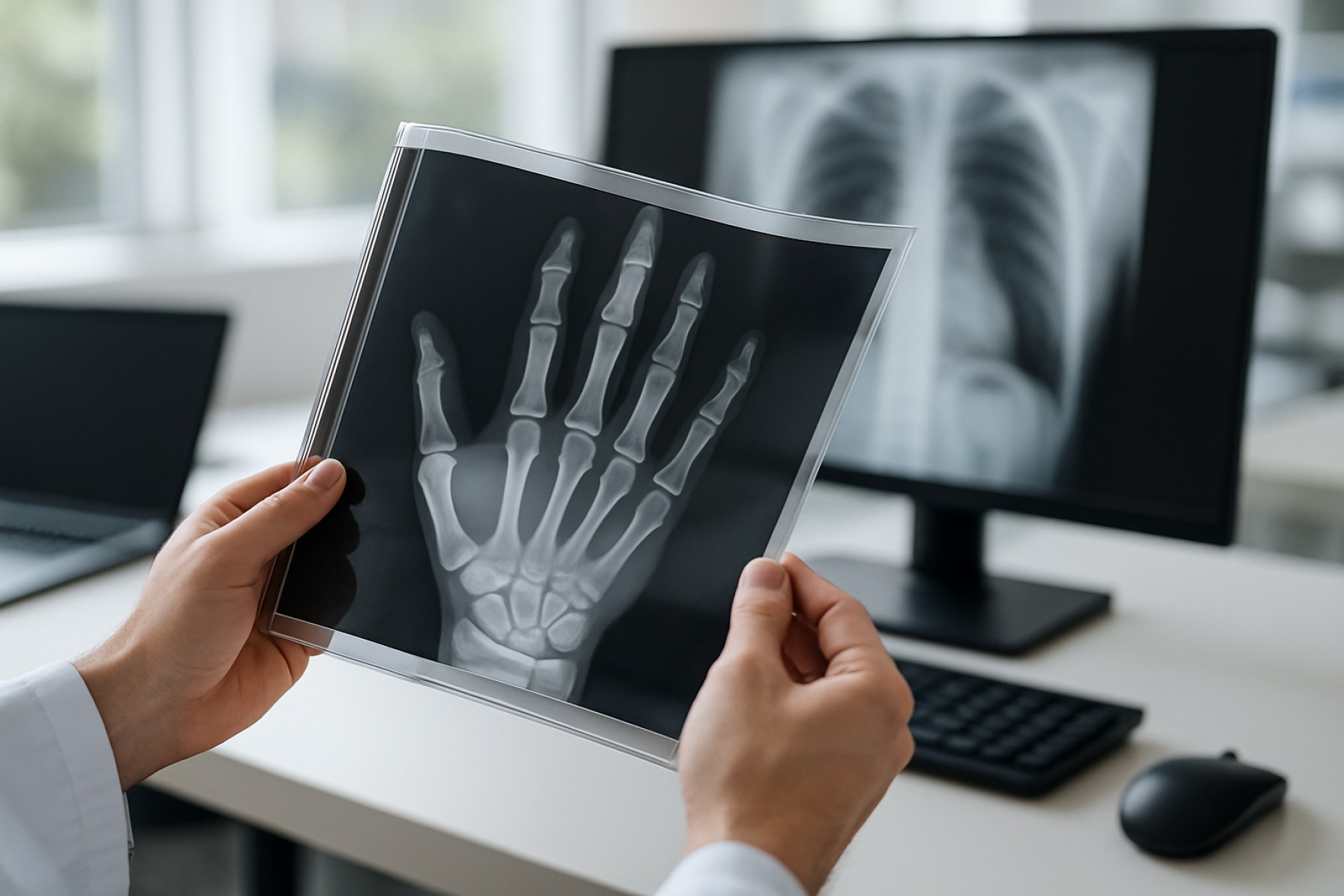
Flexible Printed X-ray Detectors Manufacturing in 2025: Unleashing Next-Gen Imaging with Scalable, Lightweight Solutions. Explore How Innovation and Demand Are Reshaping the X-ray Industry Landscape.
- Executive Summary: 2025 Market Highlights & Key Takeaways
- Technology Overview: Flexible Printed X-ray Detector Fundamentals
- Manufacturing Innovations: Materials, Processes, and Scalability
- Competitive Landscape: Leading Companies and Strategic Partnerships
- Market Size & Forecast (2025–2030): CAGR, Revenue, and Volume Projections
- Key Application Sectors: Medical, Security, Industrial, and Beyond
- Regulatory Environment & Industry Standards (e.g., ieee.org, iec.ch)
- Supply Chain Dynamics: Raw Materials, Suppliers, and Logistics
- Emerging Trends: Flexible Electronics, AI Integration, and Wearables
- Future Outlook: Growth Drivers, Challenges, and Strategic Opportunities
- Sources & References
Executive Summary: 2025 Market Highlights & Key Takeaways
The flexible printed X-ray detectors market is poised for significant advancements and commercial traction in 2025, driven by ongoing innovations in materials science, scalable manufacturing, and expanding application domains. The sector is transitioning from laboratory-scale prototypes to pilot and early-stage mass production, with a focus on cost-effective, lightweight, and conformable devices that address the limitations of traditional rigid detectors.
Key industry players such as Konica Minolta and Samsung Electronics are actively investing in flexible electronics and digital radiography, leveraging their expertise in imaging and materials to develop next-generation X-ray sensors. Konica Minolta has announced initiatives to integrate flexible substrates and organic photodiode technologies into their medical imaging portfolio, aiming to enhance portability and patient comfort. Meanwhile, Samsung Electronics continues to expand its digital X-ray detector offerings, with R&D efforts directed toward flexible and printed sensor architectures.
Emerging companies and research spin-offs are also shaping the competitive landscape. FlexEnable, a UK-based leader in organic electronics, is collaborating with partners to scale up the production of flexible X-ray detectors using organic thin-film transistors (OTFTs) and plastic substrates. Their technology enables ultra-lightweight, bendable detectors suitable for wearable medical devices and industrial inspection. Similarly, Royole Corporation is leveraging its proprietary flexible electronics platform to explore applications in medical imaging, with pilot projects underway for printed X-ray sensor arrays.
On the materials front, the adoption of solution-processable semiconductors, such as perovskites and organic photoconductors, is accelerating. These materials allow for low-temperature, roll-to-roll manufacturing, reducing production costs and enabling large-area detector fabrication. Industry consortia and academic-industry partnerships are expected to play a pivotal role in standardizing processes and ensuring device reliability over the next few years.
Looking ahead, the market outlook for 2025 and beyond is characterized by:
- Increased commercialization of flexible X-ray detectors in medical, dental, and non-destructive testing (NDT) applications.
- Greater investment in automated, scalable printing and coating technologies to meet rising demand.
- Continued collaboration between established imaging companies and flexible electronics specialists to accelerate product development and regulatory approval.
- Ongoing improvements in detector sensitivity, resolution, and mechanical durability, expanding the range of use cases.
As the ecosystem matures, flexible printed X-ray detectors are set to redefine imaging paradigms, offering unprecedented design freedom and accessibility across healthcare and industrial sectors.
Technology Overview: Flexible Printed X-ray Detector Fundamentals
Flexible printed X-ray detectors represent a transformative shift in radiation imaging technology, leveraging advances in materials science, additive manufacturing, and large-area electronics. Unlike traditional rigid detectors based on silicon or amorphous selenium, flexible printed detectors utilize solution-processable semiconductors—such as organic polymers, perovskites, or nanomaterials—deposited onto pliable substrates via scalable printing techniques. This approach enables lightweight, conformable devices suitable for wearable medical diagnostics, industrial inspection of curved surfaces, and portable security screening.
The manufacturing process typically begins with the selection of a flexible substrate, such as polyethylene terephthalate (PET) or polyimide, chosen for its mechanical robustness and thermal stability. Onto this substrate, functional layers—including electrodes, active semiconducting materials, and encapsulation barriers—are deposited using methods like inkjet printing, screen printing, or slot-die coating. These additive techniques allow for roll-to-roll (R2R) fabrication, which is essential for high-throughput, cost-effective production. In 2025, several industry leaders are scaling up R2R manufacturing lines to meet anticipated demand for flexible X-ray detectors in both medical and industrial markets.
Key players in this sector include Konica Minolta, which has developed flexible X-ray imaging panels using organic photoconductors, and Siemens, which is exploring hybrid organic-inorganic detector architectures for improved sensitivity and mechanical flexibility. Canon is also active in the field, leveraging its expertise in flat-panel detector technology to prototype flexible devices for next-generation medical imaging. Meanwhile, Fujifilm is advancing the integration of flexible electronics into digital radiography systems, focusing on durability and image quality.
Recent technical milestones include the demonstration of flexible detectors with spatial resolutions approaching those of conventional rigid panels, and X-ray sensitivities sufficient for low-dose imaging. For example, organic photodiode arrays printed on flexible substrates have achieved detection limits below 1 μGy, meeting clinical requirements for pediatric and mobile radiography. The use of perovskite semiconductors is also gaining traction, as these materials offer high X-ray absorption coefficients and can be processed at low temperatures compatible with plastic substrates.
Looking ahead, the outlook for flexible printed X-ray detector manufacturing is robust. Industry roadmaps anticipate further improvements in device lifetime, environmental stability, and integration with wireless data transmission. As R2R production matures, costs are expected to decrease, enabling broader adoption in resource-limited settings and new application domains. Collaborative efforts between manufacturers, materials suppliers, and healthcare providers will be crucial in standardizing performance metrics and accelerating regulatory approvals, paving the way for commercial deployment in the next few years.
Manufacturing Innovations: Materials, Processes, and Scalability
The manufacturing landscape for flexible printed X-ray detectors is undergoing rapid transformation in 2025, driven by advances in materials science, scalable printing processes, and the push for cost-effective, large-area devices. The sector is characterized by a shift from traditional rigid, silicon-based detectors to flexible substrates that enable new form factors and applications, particularly in medical imaging, security, and industrial inspection.
Key to this evolution is the adoption of novel semiconducting materials compatible with low-temperature, solution-based processing. Organic semiconductors, hybrid perovskites, and metal oxide nanoparticles are at the forefront, offering high X-ray absorption and charge mobility while being amenable to roll-to-roll (R2R) and inkjet printing. For instance, Konica Minolta has been actively developing flexible X-ray imaging panels using organic photoconductors, leveraging their expertise in organic electronics and large-area coating technologies. Their approach focuses on scalable deposition of organic layers onto plastic substrates, enabling lightweight and bendable detectors.
Another significant player, Samsung Electronics, has demonstrated flexible X-ray detectors based on oxide semiconductors and thin-film transistor (TFT) arrays, utilizing advanced sputtering and printing techniques. These processes allow for the integration of high-resolution pixel arrays on flexible substrates, a critical requirement for medical and dental imaging applications. Samsung’s manufacturing lines are increasingly incorporating automated inspection and in-line quality control to ensure device reliability at scale.
In parallel, LG Display is leveraging its expertise in flexible OLED and display manufacturing to adapt R2R processing for X-ray detector fabrication. Their focus is on multilayer barrier films and encapsulation methods that protect sensitive detector materials from moisture and oxygen, a key challenge for perovskite and organic-based devices.
On the materials supply side, companies like Merck KGaA (also known as EMD Electronics in North America) are scaling up production of specialty inks and printable semiconductors tailored for X-ray detection. Their portfolio includes high-purity perovskite precursors and metal oxide nanoparticle dispersions, designed for compatibility with industrial-scale printing equipment.
Looking ahead, the outlook for flexible printed X-ray detector manufacturing is promising, with pilot production lines transitioning to commercial-scale output. The convergence of advanced materials, precision printing, and robust encapsulation is expected to drive down costs and expand adoption across healthcare, security, and non-destructive testing sectors. Industry collaborations and standardization efforts are anticipated to accelerate, as manufacturers seek to ensure device reliability and regulatory compliance for widespread deployment.
Competitive Landscape: Leading Companies and Strategic Partnerships
The competitive landscape for flexible printed X-ray detectors is rapidly evolving as established electronics manufacturers, materials innovators, and emerging startups intensify their focus on next-generation medical imaging, security, and industrial inspection solutions. As of 2025, the sector is characterized by a blend of multinational corporations leveraging their scale and R&D capabilities, and agile startups pioneering novel materials and printing techniques.
Among the global leaders, Samsung Electronics has made significant investments in flexible electronics, including printed sensor arrays, leveraging its expertise in large-area electronics and advanced materials. The company’s ongoing research into organic semiconductors and thin-film transistor (TFT) technology positions it as a key player in the transition from rigid to flexible X-ray detector panels.
Konica Minolta is another major force, with a strong legacy in digital radiography and a growing portfolio of flexible detector prototypes. The company has announced strategic collaborations with materials suppliers and academic institutions to accelerate the commercialization of flexible, lightweight X-ray panels for both medical and non-destructive testing (NDT) applications.
In the United States, Varex Imaging is actively developing flexible detector technologies, building on its established position in X-ray imaging components. Varex’s partnerships with flexible electronics manufacturers and its investments in roll-to-roll (R2R) production processes are aimed at reducing costs and enabling large-area detector fabrication.
Startups and university spin-offs are also shaping the competitive landscape. Companies such as FlexEnable (UK) are commercializing organic electronics platforms that can be adapted for X-ray detection, while Kaimera (US) is developing proprietary printable photoconductive materials for high-sensitivity, flexible X-ray sensors. These firms often collaborate with established manufacturers to scale up production and access global markets.
Strategic partnerships are a defining feature of the sector. For example, several leading detector manufacturers have entered joint development agreements with specialty materials suppliers such as DuPont and Merck KGaA, focusing on printable semiconductors and barrier films essential for device performance and longevity. Additionally, consortia involving research institutes and industry—particularly in Europe and Asia—are accelerating the translation of lab-scale innovations into manufacturable products.
Looking ahead, the competitive landscape is expected to intensify as flexible printed X-ray detectors move from pilot production to commercial deployment. Companies with robust intellectual property portfolios, scalable manufacturing capabilities, and strong supply chain partnerships are likely to lead the market. The next few years will see increased M&A activity, cross-sector alliances, and the entry of new players from adjacent fields such as flexible displays and wearable electronics.
Market Size & Forecast (2025–2030): CAGR, Revenue, and Volume Projections
The global market for flexible printed X-ray detectors is poised for significant growth between 2025 and 2030, driven by rapid advancements in flexible electronics, increasing demand for lightweight and portable medical imaging devices, and expanding applications in security, industrial inspection, and non-destructive testing. As of 2025, the market is transitioning from early-stage commercialization to broader adoption, with several key manufacturers scaling up production and entering strategic partnerships to accelerate deployment.
Industry leaders such as Konica Minolta and Canon have made substantial investments in flexible X-ray detector technology, leveraging their expertise in digital radiography and materials science. Konica Minolta has announced pilot production lines for flexible detectors, targeting both medical and industrial markets, while Canon continues to expand its portfolio of digital X-ray solutions with a focus on flexible, lightweight form factors. Additionally, Siemens Healthineers and Fujifilm are actively developing flexible detector prototypes, with anticipated commercial launches within the next two to three years.
The market size for flexible printed X-ray detectors in 2025 is estimated to be in the low hundreds of millions (USD), with projections indicating a compound annual growth rate (CAGR) of 18–24% through 2030. This robust growth is underpinned by increasing adoption in point-of-care diagnostics, mobile imaging systems, and wearable health monitoring devices. Volume shipments are expected to rise sharply as manufacturing yields improve and production costs decrease, with annual unit sales projected to surpass several hundred thousand by 2030.
Geographically, North America and Asia-Pacific are anticipated to lead market growth, supported by strong healthcare infrastructure, government initiatives for digital health, and the presence of major manufacturers. Fujifilm and Konica Minolta are particularly active in Japan and broader Asia, while Canon and Siemens Healthineers maintain significant operations in both Europe and the United States.
Looking ahead, the flexible printed X-ray detector market is expected to benefit from ongoing R&D in organic semiconductors, printable photoconductors, and roll-to-roll manufacturing processes. As these technologies mature, the cost per unit is forecast to decline, further accelerating adoption across medical, security, and industrial sectors. Strategic collaborations between technology developers, healthcare providers, and equipment manufacturers will be critical in shaping the competitive landscape and driving market expansion through 2030.
Key Application Sectors: Medical, Security, Industrial, and Beyond
The manufacturing of flexible printed X-ray detectors is rapidly evolving, with significant implications for key application sectors such as medical imaging, security screening, and industrial inspection. As of 2025, the industry is witnessing a shift from traditional rigid, glass-based detectors to flexible, lightweight alternatives enabled by advances in materials science and roll-to-roll (R2R) printing technologies.
In the medical sector, flexible X-ray detectors are being developed to address the need for conformable, lightweight, and portable imaging solutions. These detectors can be integrated into wearable devices or wrapped around curved anatomical surfaces, improving patient comfort and enabling new diagnostic approaches. Companies like Siemens Healthineers and Canon Inc. are actively exploring flexible detector technologies, aiming to enhance digital radiography and computed tomography systems. The use of organic semiconductors and hybrid perovskite materials is being investigated to achieve high sensitivity and low-dose imaging, which is particularly valuable in pediatric and bedside applications.
In the security sector, the demand for flexible, large-area X-ray detectors is driven by the need for portable and deployable scanning systems at airports, border checkpoints, and public events. Flexible detectors can be integrated into mobile scanners or even embedded into infrastructure for real-time threat detection. Varex Imaging Corporation, a major supplier of X-ray imaging components, is investing in research and partnerships to develop flexible detector modules that can be rapidly deployed in the field.
The industrial sector is also a significant adopter, with flexible X-ray detectors enabling non-destructive testing (NDT) of complex-shaped components in aerospace, automotive, and energy industries. The ability to conform detectors to irregular surfaces allows for more accurate inspection of welds, pipes, and composite materials. GE (through its GE Inspection Technologies division) is exploring flexible detector solutions to enhance the versatility and efficiency of industrial radiography systems.
Beyond these core sectors, flexible printed X-ray detectors are opening new possibilities in fields such as art conservation, food safety, and environmental monitoring. The next few years are expected to see further commercialization, with pilot production lines and early market deployments by 2026–2027. The outlook is bolstered by ongoing collaborations between material suppliers, device manufacturers, and end-users, as well as support from industry bodies such as the Semiconductor Industry Association, which is fostering innovation in flexible electronics manufacturing standards.
Regulatory Environment & Industry Standards (e.g., ieee.org, iec.ch)
The regulatory environment and industry standards for flexible printed X-ray detectors are rapidly evolving as the technology matures and moves toward broader commercialization. In 2025, the sector is shaped by a combination of established international standards for X-ray devices and emerging guidelines specific to flexible and printed electronics. Regulatory compliance is critical, particularly for medical and security applications, where safety, reliability, and interoperability are paramount.
Globally, the International Electrotechnical Commission (IEC) plays a central role in setting standards for X-ray equipment, including performance, safety, and electromagnetic compatibility. The IEC 60601 series, which covers the safety and essential performance of medical electrical equipment, is particularly relevant for manufacturers of flexible X-ray detectors intended for clinical use. As flexible and printed electronics introduce new materials and form factors, the IEC is actively reviewing and updating standards to address these innovations, with working groups focusing on flexible substrates, organic semiconductors, and novel encapsulation methods.
In parallel, the Institute of Electrical and Electronics Engineers (IEEE) is developing standards for printed electronics, including those applicable to sensor arrays and imaging devices. The IEEE Standards Association has initiated projects to define test methods, reliability metrics, and interoperability protocols for flexible electronic components, which are expected to be finalized or updated in the next few years. These efforts aim to harmonize requirements across the supply chain, facilitating integration of flexible X-ray detectors into existing imaging systems.
Manufacturers such as Konica Minolta and Canon, both active in digital X-ray detector development, are engaging with regulatory bodies and standards organizations to ensure their flexible detector products meet evolving requirements. These companies are also participating in industry consortia to share best practices and accelerate the adoption of standardized testing and certification procedures.
Looking ahead, regulatory agencies in major markets—including the U.S. Food and Drug Administration (FDA) and the European Medicines Agency (EMA)—are expected to issue updated guidance for flexible and printed medical devices, reflecting the unique challenges of these technologies. This includes considerations for biocompatibility, mechanical durability, and long-term stability under repeated flexing. Industry stakeholders anticipate that by 2026–2027, harmonized international standards will be in place, streamlining approval processes and supporting the safe deployment of flexible printed X-ray detectors in healthcare, security, and industrial inspection.
Supply Chain Dynamics: Raw Materials, Suppliers, and Logistics
The supply chain for flexible printed X-ray detectors is evolving rapidly as the technology matures and demand increases across medical, security, and industrial sectors. In 2025, the manufacturing ecosystem is characterized by a complex interplay of raw material sourcing, specialized suppliers, and logistics strategies tailored to the unique requirements of flexible electronics.
Key raw materials for flexible X-ray detectors include organic semiconductors, photoconductive polymers, flexible substrates (such as polyimide or polyethylene terephthalate), and conductive inks based on silver, carbon, or copper. The supply of high-purity organic semiconductors and photoconductive materials remains concentrated among a handful of chemical manufacturers with expertise in electronic-grade materials. Companies like Merck KGaA and Dow are prominent suppliers, providing advanced materials tailored for printed electronics and flexible optoelectronic devices.
Flexible substrates are sourced from global polymer producers, with DuPont and Kuraray recognized for their high-performance films suitable for roll-to-roll processing. Conductive inks, a critical enabler for printed circuitry, are supplied by companies such as Sun Chemical and DuPont, both of which have expanded their portfolios to address the needs of flexible and stretchable electronics.
The supply chain is further shaped by specialized equipment manufacturers that provide printing and coating systems for large-area, high-throughput production. Meyer Burger Technology AG and Roland DG Corporation are notable for their advanced printing solutions, supporting the transition from laboratory-scale fabrication to industrial-scale manufacturing.
Logistics for flexible X-ray detector components and finished products require careful handling to prevent mechanical damage and contamination. Manufacturers are increasingly adopting just-in-time inventory strategies and partnering with logistics providers experienced in handling sensitive electronic materials. The global nature of the supply chain, with raw materials and components sourced from Asia, Europe, and North America, necessitates robust risk management to mitigate disruptions from geopolitical tensions or transportation bottlenecks.
Looking ahead, the supply chain is expected to become more resilient and localized as demand for flexible X-ray detectors grows. Strategic partnerships between material suppliers, equipment manufacturers, and device integrators are likely to intensify, with a focus on securing critical raw materials and streamlining logistics. Industry leaders are also investing in recycling and circular economy initiatives to ensure long-term sustainability and reduce dependence on volatile supply sources.
Emerging Trends: Flexible Electronics, AI Integration, and Wearables
The manufacturing landscape for flexible printed X-ray detectors is undergoing rapid transformation as the industry pivots toward lightweight, conformable, and cost-effective solutions for medical imaging, security, and industrial inspection. In 2025, the convergence of advanced materials, scalable printing techniques, and integration with artificial intelligence (AI) is accelerating the commercialization of these next-generation detectors.
Key players such as Konica Minolta and Canon are actively developing flexible X-ray detector prototypes, leveraging their expertise in imaging and materials science. Konica Minolta has demonstrated flexible flat panel detectors using organic photoconductors, aiming to deliver lightweight and bendable devices suitable for portable and wearable medical diagnostics. Similarly, Canon is investing in flexible sensor arrays, focusing on improving spatial resolution and mechanical durability for both medical and non-destructive testing applications.
The adoption of solution-processable semiconductors, such as organic and perovskite materials, is a defining trend. These materials enable roll-to-roll printing and other additive manufacturing methods, which are expected to reduce production costs and facilitate large-area detector fabrication. Companies like Siemens Healthineers are exploring hybrid approaches that combine flexible substrates with high-sensitivity photodiodes, targeting improved image quality and patient comfort in radiography.
In parallel, the integration of AI-driven image processing is becoming standard in flexible X-ray detector systems. AI algorithms enhance image reconstruction, noise reduction, and anomaly detection, allowing for lower radiation doses and faster diagnostics. Samsung Electronics is notable for embedding AI capabilities into its digital radiography platforms, and is expected to extend these features to flexible detector formats as the technology matures.
Looking ahead, the next few years will likely see increased collaboration between material suppliers, electronics manufacturers, and healthcare providers to address challenges such as long-term stability, environmental robustness, and regulatory compliance. The push for wearable and point-of-care imaging devices is expected to drive further innovation, with flexible printed X-ray detectors poised to play a central role in the evolution of personalized and mobile healthcare.
As manufacturing processes mature and economies of scale are realized, flexible printed X-ray detectors are anticipated to transition from pilot projects to mainstream adoption, particularly in applications where portability, adaptability, and patient-centric design are paramount.
Future Outlook: Growth Drivers, Challenges, and Strategic Opportunities
The future outlook for flexible printed X-ray detectors manufacturing in 2025 and the coming years is shaped by a convergence of technological advancements, market drivers, and strategic industry initiatives. The sector is poised for significant growth, propelled by the increasing demand for lightweight, portable, and conformable X-ray imaging solutions across medical, industrial, and security applications.
Key growth drivers include the rapid evolution of flexible electronics manufacturing techniques, such as roll-to-roll (R2R) printing and solution-processable semiconductors. These methods enable cost-effective, high-throughput production of large-area detectors on plastic substrates, reducing both material waste and device weight. Companies like Konica Minolta and Fujifilm are actively developing flexible X-ray imaging panels, leveraging their expertise in organic photoconductors and thin-film transistor (TFT) arrays. Konica Minolta has publicly highlighted its work on flexible X-ray detectors for medical and non-destructive testing, aiming to commercialize these products in the near term.
Another major driver is the push for point-of-care and mobile medical diagnostics, especially in underserved or remote regions. Flexible detectors can be integrated into portable X-ray systems, enabling rapid deployment in field hospitals, ambulances, and disaster zones. The industrial sector is also adopting flexible detectors for non-destructive evaluation of curved or irregular surfaces, where traditional rigid panels are impractical.
Despite these opportunities, several challenges remain. Achieving high spatial resolution, low noise, and long-term stability in flexible formats is technically demanding. Material innovation—particularly in organic semiconductors and hybrid perovskites—is critical to overcoming these hurdles. Additionally, ensuring compatibility with existing X-ray system architectures and meeting stringent regulatory standards for medical devices are ongoing concerns.
Strategically, partnerships between material suppliers, device manufacturers, and end-users are accelerating product development and market entry. For example, Fujifilm collaborates with academic and industrial partners to refine flexible detector technologies and expand their application scope. Meanwhile, companies such as Varex Imaging are exploring flexible and hybrid detector solutions to complement their established digital X-ray product lines.
Looking ahead, the flexible printed X-ray detector market is expected to see robust growth through 2025 and beyond, driven by ongoing R&D, expanding application areas, and the maturation of scalable manufacturing processes. As technical barriers are addressed and regulatory pathways clarified, flexible detectors are likely to transition from niche prototypes to mainstream commercial products, reshaping the landscape of X-ray imaging.
Sources & References
- FlexEnable
- Siemens
- Canon
- Fujifilm
- LG Display
- Varex Imaging
- DuPont
- Siemens Healthineers
- GE
- Semiconductor Industry Association
- Institute of Electrical and Electronics Engineers (IEEE)
- Kuraray
- Meyer Burger Technology AG
- Roland DG Corporation