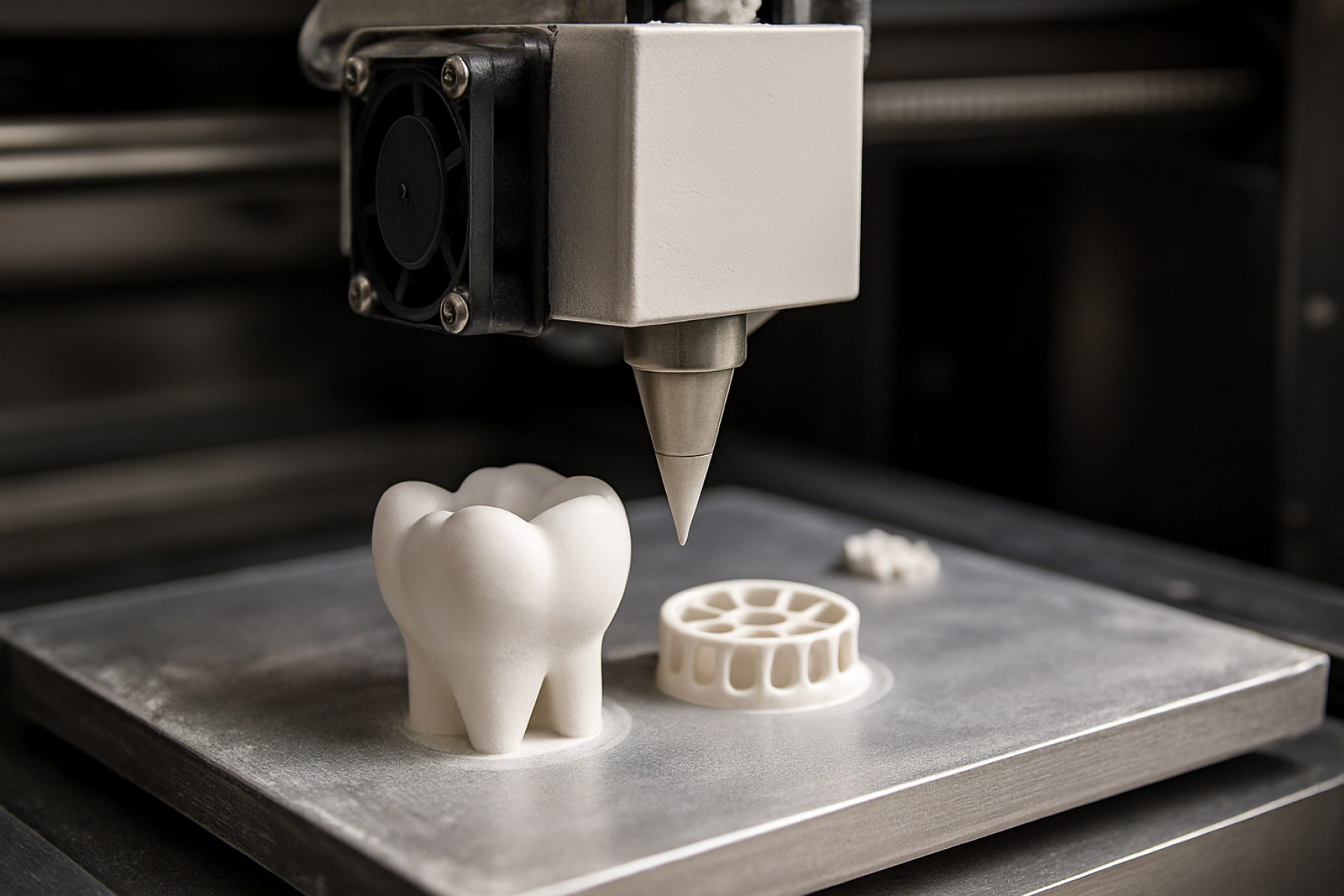
Zirconia Ceramic Additive Manufacturing in 2025: Unleashing Next-Gen Performance and Market Expansion. Explore How Advanced 3D Printing is Transforming High-Precision Industries.
- Executive Summary: Key Trends and Market Drivers in 2025
- Zirconia Ceramics: Properties, Applications, and Competitive Advantages
- Additive Manufacturing Technologies for Zirconia: Stereolithography, Binder Jetting, and Beyond
- Global Market Size, Segmentation, and 2025–2030 Growth Forecasts
- Key Players and Strategic Initiatives (e.g., 3DCeram, Lithoz, XJet, Admatec)
- Emerging Applications: Medical, Dental, Aerospace, and Electronics
- Supply Chain, Raw Materials, and Sustainability Considerations
- Regulatory Landscape and Industry Standards (e.g., ISO, ASTM)
- Innovation Pipeline: R&D, Patents, and Next-Gen Materials
- Future Outlook: Opportunities, Challenges, and Market Growth Projections (CAGR 2025–2030: ~18%)
- Sources & References
Executive Summary: Key Trends and Market Drivers in 2025
Zirconia ceramic additive manufacturing (AM) is poised for significant growth in 2025, driven by advances in material science, process optimization, and expanding industrial adoption. Zirconia, known for its exceptional mechanical strength, fracture toughness, and biocompatibility, is increasingly favored in demanding sectors such as dental, medical, aerospace, and electronics. The convergence of these properties with the design freedom of AM is unlocking new applications and accelerating market momentum.
Key trends in 2025 include the maturation of powder-based and slurry-based AM processes, such as stereolithography (SLA), digital light processing (DLP), and binder jetting, specifically tailored for zirconia ceramics. Leading equipment manufacturers like 3D Systems and Stratasys are expanding their ceramic-compatible printer portfolios, while specialized players such as Lithoz and XJet are pushing the boundaries of resolution and throughput for technical ceramics. Lithoz, for example, has reported significant increases in production capacity and partnerships with dental and medical device manufacturers, reflecting the sector’s shift from prototyping to end-use part production.
Material suppliers are also scaling up, with companies like Tosoh and 3M providing high-purity zirconia powders and feedstocks optimized for AM processes. These developments are enabling the production of complex, high-performance components with improved reliability and repeatability. The dental sector remains a primary driver, with zirconia AM enabling rapid, patient-specific restorations and prosthetics. In parallel, the medical field is leveraging zirconia’s biocompatibility for custom implants and surgical tools, while the electronics industry is exploring its use in insulating and wear-resistant components.
Looking ahead, the outlook for zirconia ceramic AM in the next few years is robust. Industry bodies and manufacturers anticipate double-digit annual growth rates, underpinned by ongoing R&D, cost reductions, and the integration of AM into mainstream manufacturing workflows. The focus is shifting toward automation, quality assurance, and the development of multi-material and hybrid AM systems. As regulatory pathways for medical and dental applications become clearer, adoption is expected to accelerate further. The sector’s trajectory is reinforced by strategic collaborations between printer manufacturers, material suppliers, and end-users, ensuring that zirconia ceramic AM will remain at the forefront of advanced manufacturing innovation through 2025 and beyond.
Zirconia Ceramics: Properties, Applications, and Competitive Advantages
Zirconia ceramic additive manufacturing (AM) is rapidly advancing as a transformative technology in the field of advanced ceramics, offering unique properties and competitive advantages for high-performance applications. As of 2025, the sector is witnessing significant momentum, driven by the demand for complex, high-strength, and biocompatible components in industries such as medical, dental, electronics, and aerospace.
Zirconia (zirconium dioxide, ZrO2) is prized for its exceptional mechanical strength, fracture toughness, wear resistance, and chemical inertness. These properties make it a preferred material for dental crowns, orthopedic implants, cutting tools, and components exposed to harsh environments. Additive manufacturing enables the production of intricate geometries and customized parts that are difficult or impossible to achieve with traditional subtractive methods.
Key players in the zirconia ceramic AM market include 3D Systems, which offers solutions for dental and medical zirconia parts, and XJet, whose NanoParticle Jetting technology is used for high-precision zirconia components. Lithoz is another prominent manufacturer, specializing in LCM (Lithography-based Ceramic Manufacturing) for dense, high-resolution zirconia parts, with installations in both industrial and research settings worldwide. CeramTec, a global leader in advanced ceramics, is also investing in additive manufacturing to expand its portfolio of zirconia-based solutions.
Recent years have seen the introduction of new zirconia AM materials and improved printing processes. For example, Lithoz has developed LithaCon 3Y 210, a 3 mol% yttria-stabilized zirconia (3Y-TZP) material optimized for high strength and translucency, targeting dental and medical applications. XJet continues to refine its support-free AM process, enabling the production of complex internal channels and undercuts in zirconia parts, which is particularly valuable for fluidics and microreactor applications.
The competitive advantages of zirconia ceramic AM include design freedom, rapid prototyping, and the ability to produce patient-specific implants and devices. The technology also reduces material waste and shortens lead times compared to conventional manufacturing. As digital workflows and post-processing techniques mature, the cost-effectiveness and scalability of zirconia AM are expected to improve further.
Looking ahead, the outlook for zirconia ceramic additive manufacturing is robust. Ongoing R&D by companies like 3D Systems and Lithoz is expected to yield new material formulations with enhanced translucency, toughness, and sintering efficiency. The adoption of zirconia AM in regulated sectors such as healthcare is anticipated to accelerate, supported by growing clinical validation and regulatory approvals. As the technology matures, it is poised to play a pivotal role in the next generation of high-performance ceramic components across multiple industries.
Additive Manufacturing Technologies for Zirconia: Stereolithography, Binder Jetting, and Beyond
Additive manufacturing (AM) of zirconia ceramics is rapidly advancing, with several technologies maturing for industrial and medical applications. As of 2025, three primary AM methods dominate the landscape: stereolithography (SLA), binder jetting, and material extrusion, each offering unique advantages for processing zirconia.
Stereolithography (SLA) remains the most widely adopted technique for high-precision zirconia parts. SLA uses photosensitive ceramic slurries, enabling the fabrication of dense, complex geometries with fine feature resolution. Companies such as Lithoz GmbH have established themselves as leaders, with their LCM (Lithography-based Ceramic Manufacturing) technology supporting medical, dental, and industrial applications. Lithoz’s systems are used globally for producing dental crowns, implants, and custom technical components, with ongoing R&D focused on increasing throughput and automation. Another notable player, CeramTec, is leveraging SLA for prototyping and small-batch production of advanced ceramic parts, particularly in the healthcare sector.
Binder Jetting is gaining traction for its scalability and cost-effectiveness in producing larger zirconia components. This process involves selectively depositing a binder onto a powder bed, followed by post-processing steps such as debinding and sintering. ExOne (now part of Desktop Metal) has developed binder jetting platforms compatible with technical ceramics, including zirconia, targeting industrial tooling and energy applications. The technology’s ability to produce parts with complex internal channels and reduced material waste is driving adoption, especially as sintering protocols improve to achieve near-theoretical densities.
Material Extrusion (including Fused Filament Fabrication, FFF) is also being adapted for zirconia, with companies like BASF offering ceramic-filled filaments under their Forward AM brand. This approach is attractive for prototyping and low-volume production, as it leverages widely available FFF printers and simplifies the supply chain. However, challenges remain in achieving the density and mechanical properties required for demanding applications, prompting ongoing material and process optimization.
Looking ahead, the next few years are expected to see further integration of digital workflows, increased automation, and the development of multi-material AM systems capable of combining zirconia with other ceramics or metals. Industry leaders such as Lithoz GmbH and CeramTec are investing in R&D to expand the range of printable zirconia formulations and to enable larger, more complex parts. As sintering and post-processing technologies mature, the cost per part is projected to decrease, making zirconia AM increasingly viable for both mass customization and serial production across dental, medical, and industrial sectors.
Global Market Size, Segmentation, and 2025–2030 Growth Forecasts
The global market for zirconia ceramic additive manufacturing (AM) is poised for significant expansion between 2025 and 2030, driven by increasing demand for advanced ceramics in high-performance applications across medical, dental, electronics, and industrial sectors. Zirconia’s unique combination of mechanical strength, biocompatibility, and chemical stability makes it a preferred material for additive manufacturing, particularly in applications where traditional manufacturing methods are limited.
In 2025, the zirconia ceramic AM market is expected to be characterized by a growing adoption of both powder-based and slurry-based 3D printing technologies. Key segmentation includes application (dental, medical, industrial, electronics), technology (stereolithography, digital light processing, binder jetting, material extrusion), and geography (North America, Europe, Asia-Pacific, and Rest of World). The dental sector remains the largest segment, with zirconia crowns, bridges, and implants produced via AM gaining traction due to their superior aesthetics and durability. Companies such as 3D Systems and Stratasys are actively expanding their ceramic AM portfolios, while specialized players like Lithoz and XJet are focusing on high-precision zirconia printing for both dental and industrial uses.
Geographically, Europe and Asia-Pacific are anticipated to lead market growth, supported by robust manufacturing infrastructure and strong demand from the dental and electronics industries. For instance, Lithoz (Austria) and CeramTec (Germany) are investing in expanding their AM capabilities, while in Asia, companies like Tosoh (Japan) are scaling up zirconia powder production to meet rising demand for 3D printing feedstocks.
From 2025 to 2030, the zirconia ceramic AM market is forecast to grow at a double-digit compound annual growth rate (CAGR), with estimates commonly ranging from 15% to 20% annually, depending on the segment and region. This growth is underpinned by ongoing advancements in AM hardware, software, and material formulations, which are improving the density, surface finish, and mechanical properties of printed zirconia parts. The introduction of new industrial-scale printers by companies such as 3D Systems and XJet is expected to further accelerate adoption in high-value sectors.
Looking ahead, the market outlook remains robust as end-users increasingly recognize the benefits of zirconia AM for rapid prototyping, mass customization, and the production of complex geometries unachievable by conventional methods. Strategic collaborations between printer manufacturers, material suppliers, and end-users are likely to drive further innovation and market penetration through 2030.
Key Players and Strategic Initiatives (e.g., 3DCeram, Lithoz, XJet, Admatec)
The zirconia ceramic additive manufacturing (AM) sector is witnessing rapid evolution in 2025, driven by a cohort of specialized technology providers and strategic collaborations. Key players are leveraging proprietary processes and expanding their global reach to address growing demand in medical, dental, electronics, and industrial applications.
3DCeram, headquartered in France, remains a leader in stereolithography (SLA) for technical ceramics, including zirconia. The company’s Ceramaker platform is widely adopted for producing high-density, complex zirconia parts, particularly in dental and biomedical fields. In 2024–2025, 3DCeram has intensified partnerships with dental labs and research institutes, focusing on process automation and post-processing integration to streamline production workflows.
Austrian-based Lithoz continues to set benchmarks with its LCM (Lithography-based Ceramic Manufacturing) technology, enabling the fabrication of intricate zirconia components with exceptional resolution and density. In 2025, Lithoz is expanding its global footprint, establishing new application centers in Asia and North America, and collaborating with leading dental and industrial ceramics manufacturers to accelerate the adoption of 3D-printed zirconia in serial production.
Israeli innovator XJet is advancing its NanoParticle Jetting™ technology, which allows for the production of high-purity zirconia parts with fine detail and smooth surface finishes. XJet has recently announced strategic alliances with major dental and electronics OEMs, aiming to scale up the use of zirconia AM for both prototyping and end-use components. The company is also investing in expanding its material portfolio and enhancing throughput for industrial-scale applications.
Dutch company Admatec (Admatec Europe BV) is recognized for its Digital Light Processing (DLP) and binder jetting solutions for technical ceramics, including zirconia. Admatec has focused on modular system upgrades and open material platforms, enabling customers to tailor zirconia formulations for specific mechanical and aesthetic requirements. In 2025, Admatec is strengthening its presence in the dental and industrial sectors through joint development agreements and expanded service offerings.
Other notable contributors include CeramTec, a global supplier of advanced ceramic materials, which is investing in AM-compatible zirconia powders and collaborating with printer manufacturers to optimize process-material compatibility (CeramTec). CoorsTek, another major ceramics producer, is also exploring additive manufacturing routes for zirconia, focusing on high-performance applications in electronics and energy (CoorsTek).
Looking ahead, the sector is expected to see further consolidation, with leading players forming strategic alliances to accelerate industrialization, standardization, and qualification of zirconia AM parts. The focus on end-use applications, particularly in regulated industries, is driving investments in quality assurance, process validation, and digital workflow integration.
Emerging Applications: Medical, Dental, Aerospace, and Electronics
Zirconia ceramic additive manufacturing (AM) is rapidly advancing, with 2025 marking a pivotal year for its adoption in high-value sectors such as medical, dental, aerospace, and electronics. The unique properties of zirconia—exceptional strength, fracture toughness, and biocompatibility—are driving its integration into applications where traditional manufacturing methods face limitations.
In the medical and dental fields, zirconia AM is revolutionizing the production of patient-specific implants, crowns, and bridges. The ability to fabricate complex geometries with high precision is particularly valuable for dental prosthetics, where customization and fit are critical. Companies like 3D Systems and CeramTec are actively developing and supplying zirconia-based AM solutions for dental labs and clinics. CeramTec, a global leader in advanced ceramics, has expanded its portfolio to include 3D-printed zirconia components, emphasizing their use in dental and orthopedic implants due to their excellent biocompatibility and wear resistance.
In aerospace, the demand for lightweight, high-performance materials is fueling interest in zirconia AM. The material’s thermal stability and resistance to corrosion make it suitable for components exposed to extreme environments, such as turbine blades and thermal barrier coatings. GE and Safran are among the aerospace manufacturers exploring ceramic AM for next-generation propulsion systems and heat-resistant parts. The ability to produce intricate cooling channels and lattice structures via AM is expected to enhance engine efficiency and longevity.
The electronics sector is also witnessing the emergence of zirconia AM for the fabrication of substrates, insulators, and sensor housings. Zirconia’s electrical insulation properties and chemical inertness are advantageous for miniaturized and high-frequency electronic devices. Toshiba and Kyocera, both established in advanced ceramics, are investing in additive processes to produce complex zirconia components for electronic and semiconductor applications.
Looking ahead, the next few years are expected to see further integration of zirconia AM in these sectors, driven by ongoing improvements in printing technologies, material formulations, and post-processing methods. The expansion of industrial partnerships and the entry of new players are likely to accelerate the commercialization of zirconia AM, with a focus on high-value, application-specific solutions. As the technology matures, regulatory approvals and standardization efforts will play a crucial role in enabling broader adoption, particularly in medical and aerospace applications.
Supply Chain, Raw Materials, and Sustainability Considerations
The supply chain for zirconia ceramic additive manufacturing (AM) is evolving rapidly in 2025, shaped by increasing demand for advanced ceramics in medical, dental, and industrial applications. Zirconia (zirconium dioxide, ZrO₂) is prized for its exceptional mechanical strength, biocompatibility, and thermal stability, making it a preferred material for 3D-printed dental prosthetics, orthopedic implants, and high-performance components.
Raw zirconia is primarily sourced from mineral sands, with major global suppliers including Rio Tinto and Iluka Resources, who extract zircon (ZrSiO₄) and process it into zirconia powders. The purity and particle size distribution of these powders are critical for AM processes such as stereolithography (SLA), digital light processing (DLP), and binder jetting. Leading powder manufacturers like Tosoh Corporation and 3M supply stabilized zirconia formulations tailored for additive manufacturing, ensuring consistent sintering behavior and mechanical properties.
The AM supply chain is also influenced by the development of specialized feedstocks. Companies such as CeramTec and Ceramco are investing in proprietary zirconia slurries and granulates optimized for 3D printing, addressing challenges like powder flowability, binder compatibility, and shrinkage control during sintering. Equipment manufacturers, including Lithoz and 3DCeram, are collaborating with material suppliers to certify feedstocks for their printers, further integrating the supply chain.
Sustainability is an increasing focus in 2025, as the energy-intensive nature of ceramic sintering and the environmental impact of mining zircon are scrutinized. Companies are exploring closed-loop recycling of unfired zirconia powders and supports, as well as energy-efficient sintering technologies. For example, Tosoh Corporation is developing processes to reduce carbon emissions during powder production, while CeramTec is piloting the use of renewable energy in its manufacturing plants.
Looking ahead, the zirconia AM sector is expected to see further vertical integration, with printer manufacturers, powder producers, and end-users forming strategic partnerships to secure supply and drive innovation. The push for greener manufacturing and transparent sourcing is likely to intensify, with industry bodies such as the American Ceramic Society promoting best practices and sustainability standards. As demand for high-performance ceramics grows, the supply chain will need to balance scalability, quality, and environmental responsibility to ensure the long-term viability of zirconia ceramic additive manufacturing.
Regulatory Landscape and Industry Standards (e.g., ISO, ASTM)
The regulatory landscape and industry standards for zirconia ceramic additive manufacturing (AM) are evolving rapidly as the technology matures and adoption increases across sectors such as dental, medical, and industrial applications. As of 2025, the industry is witnessing a concerted effort to harmonize standards and ensure the reliability, safety, and performance of zirconia AM parts.
Key international standards organizations, notably the International Organization for Standardization (ISO) and ASTM International, have been instrumental in developing frameworks that address the unique challenges of ceramic AM. ISO/ASTM 52900 provides general terminology for additive manufacturing, while ISO/ASTM 52921 and ISO/ASTM 52922 address design and qualification guidelines, respectively. However, specific standards for technical ceramics like zirconia are still under development, with working groups focusing on powder characterization, process qualification, and part validation.
In the dental sector, regulatory requirements are particularly stringent. Zirconia AM components intended for dental restorations must comply with ISO 6872 (dentistry—ceramic materials) and ISO 13356 (implants—ceramic materials based on yttria-stabilized tetragonal zirconia). Leading dental AM system providers such as 3D Systems and CeramTec are actively engaged in aligning their processes and materials with these standards, ensuring biocompatibility and mechanical integrity.
In the industrial sector, companies like XJet and Lithoz are collaborating with standards bodies to establish best practices for powder handling, sintering, and post-processing of zirconia parts. These efforts are crucial for applications in aerospace, electronics, and energy, where component reliability is paramount.
Looking ahead, the next few years are expected to bring further standardization, particularly as more end-use applications emerge and regulatory agencies increase oversight. The European Union’s Medical Device Regulation (MDR) and the U.S. Food and Drug Administration (FDA) are anticipated to issue more detailed guidance on AM ceramics, including zirconia, especially for patient-specific implants and critical components. Industry consortia and technical committees are also working to address traceability, reproducibility, and quality assurance, which will be essential for broader adoption.
In summary, while foundational standards exist, the regulatory landscape for zirconia ceramic additive manufacturing is in a phase of active development. Ongoing collaboration between manufacturers, standards organizations, and regulatory bodies will be key to ensuring safe, high-quality, and widely accepted zirconia AM products in the coming years.
Innovation Pipeline: R&D, Patents, and Next-Gen Materials
The innovation pipeline for zirconia ceramic additive manufacturing (AM) is intensifying in 2025, with a surge in R&D, patent activity, and the emergence of next-generation materials. Zirconia’s unique combination of high strength, fracture toughness, and biocompatibility continues to drive research, particularly for medical, dental, and high-performance engineering applications.
Leading manufacturers are investing heavily in the development of advanced zirconia powders and printable feedstocks. 3D Systems and XJet are notable for their proprietary processes—such as binder jetting and NanoParticle Jetting™—which enable the production of dense, complex zirconia parts with fine feature resolution. XJet in particular has expanded its portfolio to include new zirconia formulations with improved translucency and mechanical properties, targeting dental crowns and bridges.
In Europe, Lithoz continues to lead in lithography-based ceramic manufacturing (LCM), with recent patents focusing on multi-material printing and enhanced green part strength. Their LCM technology is being refined to allow for the co-printing of zirconia with other ceramics, opening pathways for functionally graded materials and multi-phase components. Lithoz’s collaborations with academic and industrial partners are accelerating the translation of lab-scale innovations to commercial production.
Asian manufacturers are also ramping up R&D. Tosoh Corporation, a major global supplier of zirconia powders, is developing next-generation nano-zirconia materials optimized for AM, focusing on improved sinterability and reduced shrinkage. These efforts are expected to yield powders tailored for specific AM platforms, enhancing part quality and process reliability.
Patent filings in 2024–2025 reflect a focus on process optimization, such as in-situ monitoring, support-free printing, and post-processing techniques to minimize defects and maximize density. The integration of AI-driven process control is emerging as a key trend, with several companies seeking IP protection for machine learning algorithms that predict and correct print anomalies in real time.
Looking ahead, the innovation pipeline is expected to deliver zirconia AM materials with higher translucency for dental aesthetics, improved toughness for load-bearing implants, and hybrid compositions for electronic and energy applications. The next few years will likely see the commercialization of multi-material zirconia parts and the expansion of AM into new sectors, driven by ongoing R&D from industry leaders and material suppliers.
Future Outlook: Opportunities, Challenges, and Market Growth Projections (CAGR 2025–2030: ~18%)
The outlook for zirconia ceramic additive manufacturing (AM) from 2025 through 2030 is marked by robust growth prospects, technological advancements, and evolving market dynamics. Industry consensus projects a compound annual growth rate (CAGR) of approximately 18% for this segment, driven by increasing adoption in high-value sectors such as dental, medical, aerospace, and electronics.
Key players are expanding their portfolios and production capacities to meet surging demand. 3D Systems and Stratasys are investing in ceramic-compatible AM platforms, while XJet continues to refine its NanoParticle Jetting™ technology, enabling high-density, complex zirconia parts. Lithoz, a specialist in ceramic 3D printing, is scaling up its LCM (Lithography-based Ceramic Manufacturing) systems, which are widely used for dental and biomedical zirconia components. CeramTec and Tosoh—major global suppliers of advanced ceramics—are collaborating with AM technology providers to optimize zirconia powders for additive processes, ensuring consistent quality and performance.
Opportunities abound in the dental sector, where zirconia’s biocompatibility and aesthetics are driving the shift from traditional milling to additive manufacturing for crowns, bridges, and implants. The medical field is also seeing increased adoption for patient-specific implants and surgical tools, leveraging the design freedom and rapid prototyping capabilities of AM. Aerospace and electronics industries are exploring zirconia AM for lightweight, high-strength components and advanced insulators, respectively.
However, challenges remain. Achieving defect-free, fully dense zirconia parts with reliable mechanical properties is a persistent technical hurdle. Post-processing requirements, such as debinding and sintering, add complexity and cost. Material qualification and standardization are ongoing concerns, particularly for regulated industries. Leading organizations, including CeramTec and Tosoh, are actively engaged in R&D to address these issues, working alongside AM equipment manufacturers to refine process parameters and material formulations.
Looking ahead, the market is expected to benefit from continued innovation in multi-material printing, automation, and digital workflow integration. Strategic partnerships between ceramic producers, AM technology developers, and end-users will be crucial in accelerating adoption and scaling production. As cost barriers decrease and process reliability improves, zirconia ceramic additive manufacturing is poised for significant expansion, with the Asia-Pacific region and Europe emerging as key growth markets.
Sources & References
- 3D Systems
- Stratasys
- Lithoz
- XJet
- CeramTec
- ExOne
- BASF
- 3DCeram
- Lithoz
- XJet
- Admatec
- CeramTec
- GE
- Toshiba
- Rio Tinto
- 3DCeram
- American Ceramic Society
- International Organization for Standardization (ISO)
- ASTM International