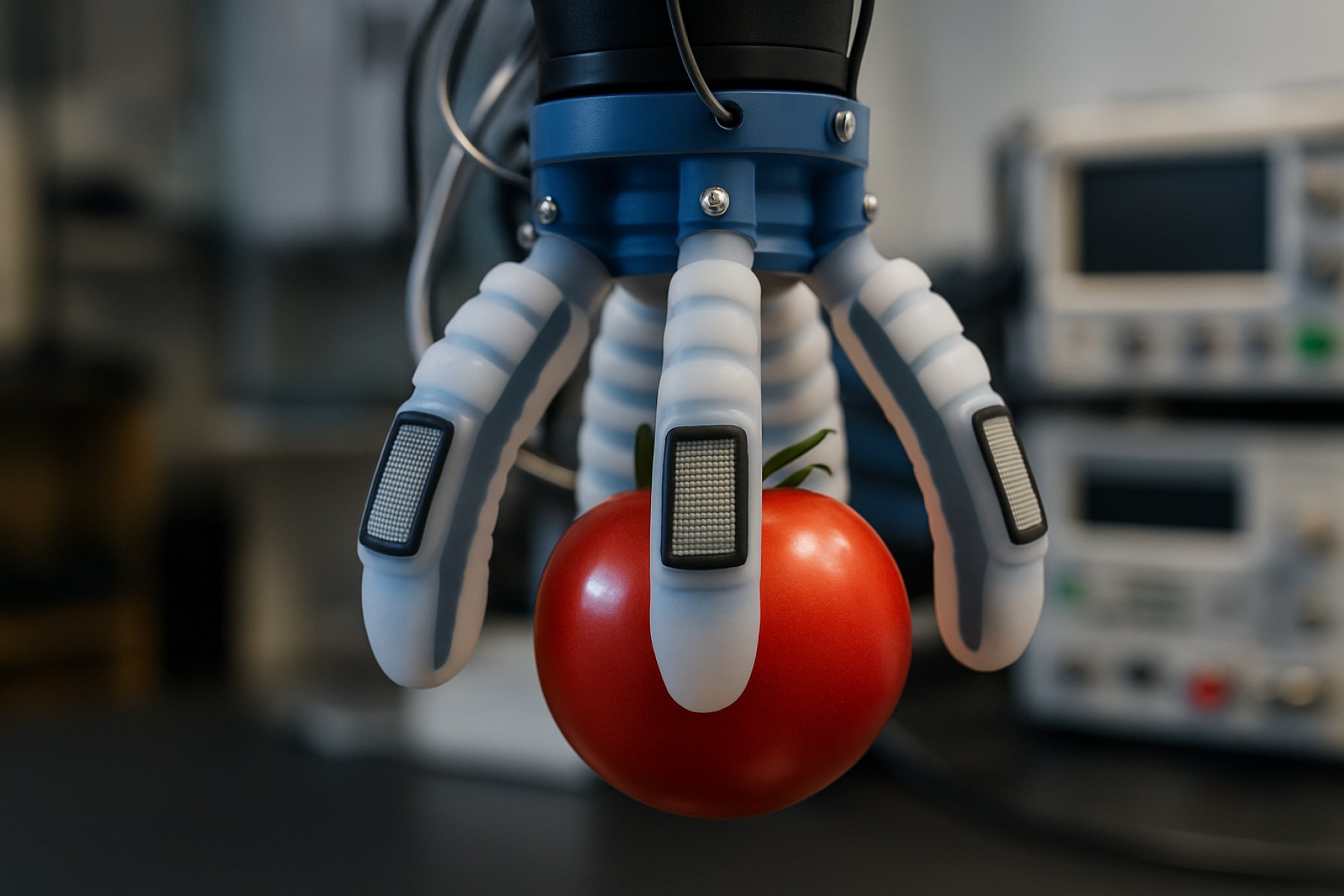
Unlocking the Future of Soft Robotics: How Tactile Sensing Components Will Transform Automation in 2025 and Beyond. Explore Market Growth, Breakthrough Technologies, and Strategic Opportunities.
- Executive Summary: 2025 Market Outlook and Key Takeaways
- Market Size, Growth Rate, and Forecasts Through 2030
- Core Technologies: Capacitive, Piezoelectric, and Optical Tactile Sensors
- Emerging Materials and Flexible Electronics for Soft Robotics
- Key Industry Players and Strategic Partnerships (e.g., synaptics.com, onrobot.com, softroboticsinc.com)
- Application Landscape: Healthcare, Manufacturing, and Service Robotics
- Regional Analysis: North America, Europe, Asia-Pacific Trends
- Challenges: Integration, Durability, and Cost Barriers
- Future Outlook: AI Integration and Next-Gen Sensing Capabilities
- Strategic Recommendations for Stakeholders and Investors
- Sources & References
Executive Summary: 2025 Market Outlook and Key Takeaways
The market for tactile sensing components in soft robotics is poised for significant growth in 2025, driven by rapid advancements in material science, sensor miniaturization, and the increasing adoption of soft robotics across industries such as healthcare, logistics, and consumer electronics. Tactile sensors—enabling robots to perceive pressure, texture, and force—are becoming essential for applications requiring delicate manipulation and human-robot interaction. The integration of these sensors is transforming soft robots from simple actuators into intelligent systems capable of nuanced, adaptive responses.
Key industry players are accelerating innovation in tactile sensing technologies. Tekscan, a leader in flexible pressure mapping sensors, continues to expand its product lines for robotics, offering ultra-thin, customizable sensor arrays that can be embedded into soft robotic grippers and surfaces. 3M is leveraging its expertise in advanced materials to develop stretchable, conformable sensor substrates, supporting the next generation of wearable and soft robotic devices. Meanwhile, ams OSRAM is advancing optical and capacitive sensor technologies, focusing on high-resolution tactile feedback for precision tasks.
In 2025, the healthcare sector remains a primary driver, with soft robotic devices increasingly used in rehabilitation, prosthetics, and minimally invasive surgery. Tactile sensors are critical for providing real-time feedback, improving safety and efficacy. Companies such as SMC Corporation are integrating tactile sensing into pneumatic soft actuators, enhancing dexterity and control for medical and industrial automation applications. Additionally, ABB and Festo are investing in research and partnerships to embed tactile intelligence into their robotic platforms, targeting collaborative robots (cobots) that can safely interact with humans and fragile objects.
The outlook for the next few years suggests continued convergence of tactile sensing with artificial intelligence and edge computing, enabling real-time data processing and adaptive control. The emergence of scalable manufacturing techniques for flexible electronics is expected to reduce costs and accelerate adoption. Industry standards for sensor interoperability and data protocols are also under development, which will further facilitate integration across diverse robotic systems.
In summary, 2025 marks a pivotal year for tactile sensing components in soft robotics, with robust growth anticipated as technology matures and new applications emerge. The sector is characterized by strong collaboration between sensor manufacturers, robotics companies, and end-users, setting the stage for widespread deployment and transformative impact across multiple industries.
Market Size, Growth Rate, and Forecasts Through 2030
The market for tactile sensing components in soft robotics is poised for robust growth through 2030, driven by accelerating adoption in sectors such as healthcare, logistics, consumer electronics, and advanced manufacturing. As of 2025, the global market size for tactile sensors—encompassing force, pressure, and stretch sensors specifically engineered for integration into soft robotic systems—is estimated to be in the low single-digit billions (USD), with a compound annual growth rate (CAGR) projected in the range of 15–20% over the next five years. This expansion is underpinned by the increasing demand for robots capable of delicate manipulation, human-robot interaction, and adaptive grasping, all of which require sophisticated tactile feedback.
Key industry players are investing heavily in the development and commercialization of advanced tactile sensing technologies. Tekscan, a leading provider of flexible pressure and force sensors, continues to expand its product lines for robotics and wearable applications, reporting increased demand from both OEMs and research institutions. ATI Industrial Automation, known for its force/torque sensors, is also seeing growth in orders from soft robotics integrators, particularly in the medical and collaborative robotics sectors. Meanwhile, ams OSRAM is advancing optoelectronic tactile sensor solutions, leveraging its expertise in miniaturized sensor components for integration into soft, flexible substrates.
The Asia-Pacific region is expected to lead market growth, fueled by significant investments in robotics R&D and manufacturing infrastructure in countries such as China, Japan, and South Korea. European and North American markets are also expanding, with strong activity in medical robotics and automation for logistics and e-commerce. The proliferation of soft grippers and wearable robotic devices is further stimulating demand for high-resolution, durable, and cost-effective tactile sensors.
Looking ahead to 2030, the tactile sensing component market is forecast to surpass USD 5 billion, with growth driven by ongoing advances in materials science (e.g., stretchable electronics, conductive polymers), sensor miniaturization, and the integration of artificial intelligence for real-time tactile data interpretation. Industry collaborations and standardization efforts are expected to accelerate commercialization and interoperability. Companies such as Tekscan, ATI Industrial Automation, and ams OSRAM are well-positioned to capitalize on these trends, while new entrants and academic spin-offs continue to bring novel sensing technologies to market.
Core Technologies: Capacitive, Piezoelectric, and Optical Tactile Sensors
Tactile sensing is a cornerstone of soft robotics, enabling machines to interact safely and adaptively with their environments. As of 2025, three core technologies—capacitive, piezoelectric, and optical tactile sensors—are at the forefront of innovation, each offering unique advantages for integration into soft, compliant robotic systems.
Capacitive tactile sensors are widely adopted due to their high sensitivity, flexibility, and ease of integration with soft materials. These sensors operate by detecting changes in capacitance caused by mechanical deformation, making them ideal for applications requiring gentle touch and pressure mapping. Companies such as Tekscan and 3M have developed flexible capacitive sensor arrays that can be embedded into soft robotic skins, providing high-resolution tactile feedback. Recent advancements focus on stretchable electrode materials and micro-patterned dielectric layers, which enhance durability and conformability—key requirements for next-generation soft robots.
Piezoelectric tactile sensors leverage materials that generate an electric charge in response to applied mechanical stress. This technology is particularly valued for its fast response times and ability to detect dynamic forces, such as vibrations or slip events, which are critical for dexterous manipulation. TDK Corporation and Murata Manufacturing are prominent suppliers of piezoelectric films and modules, with ongoing research into flexible and stretchable piezoelectric polymers. In 2025, the integration of these sensors into soft robotic grippers and wearable devices is accelerating, driven by the need for real-time feedback in delicate handling tasks.
Optical tactile sensors utilize changes in light transmission or reflection within soft, transparent materials to sense deformation. These sensors offer immunity to electromagnetic interference and can achieve high spatial resolution. Oshino Lamps and Hamamatsu Photonics are among the companies advancing optical sensor modules suitable for soft robotics. Recent developments include the use of embedded optical fibers and elastomeric waveguides, enabling robust, multi-point tactile mapping even under significant stretching or bending.
Looking ahead, the convergence of these core technologies is expected to yield hybrid tactile sensors that combine the strengths of each approach—such as the sensitivity of capacitive sensors, the dynamic range of piezoelectrics, and the robustness of optical systems. Industry collaborations and material innovations are anticipated to further reduce sensor thickness, increase stretchability, and improve integration with soft actuators. As a result, the next few years will likely see a proliferation of highly capable tactile sensing components, empowering soft robots to perform more complex, nuanced tasks in healthcare, manufacturing, and service applications.
Emerging Materials and Flexible Electronics for Soft Robotics
Tactile sensing components are rapidly advancing as a cornerstone technology for soft robotics, enabling machines to interact safely and adaptively with their environments. As of 2025, the field is witnessing a convergence of novel materials, flexible electronics, and scalable manufacturing techniques, all aimed at mimicking or surpassing the sensitivity and versatility of biological skin.
A key trend is the integration of stretchable and conformable sensors based on materials such as silicone elastomers, hydrogels, and conductive polymers. These materials allow sensors to maintain performance under significant deformation, a necessity for soft robotic applications. Companies like DuPont are actively developing stretchable conductive inks and films, which are being adopted in flexible printed circuit boards and sensor arrays for robotic skins. Similarly, 3M is leveraging its expertise in adhesives and flexible substrates to support the assembly of multi-layered tactile sensors.
Capacitive, piezoresistive, and piezoelectric sensing modalities remain dominant, but recent years have seen a surge in the use of optical and magnetic tactile sensors. For instance, Tekscan continues to supply thin, flexible force and pressure sensors that are widely used in both research and commercial soft robotic grippers. Meanwhile, companies such as ams OSRAM are advancing miniaturized optical sensor modules that can be embedded into soft materials, providing high-resolution touch and proximity data.
The push for scalable, cost-effective manufacturing is also shaping the sector. Roll-to-roll printing and laser patterning are being adopted to mass-produce sensor arrays with fine spatial resolution. DuPont and 3M are both investing in these manufacturing capabilities, aiming to meet the growing demand from robotics and wearable electronics markets.
Looking ahead, the next few years are expected to bring further integration of tactile sensors with embedded processing and wireless communication, enabling distributed “skin” systems for robots. The development of self-healing and biodegradable sensor materials is also on the horizon, with research collaborations between industry and academia accelerating commercialization. As soft robots move from laboratories to real-world applications in healthcare, logistics, and consumer products, the role of robust, high-fidelity tactile sensing components will only become more critical.
Key Industry Players and Strategic Partnerships (e.g., synaptics.com, onrobot.com, softroboticsinc.com)
The landscape of tactile sensing components for soft robotics in 2025 is shaped by a dynamic interplay of established sensor manufacturers, robotics innovators, and strategic partnerships aimed at advancing the field. As soft robotics continues to gain traction in sectors such as manufacturing, healthcare, and logistics, the demand for sophisticated tactile sensors—capable of mimicking the nuanced sense of touch found in biological systems—has intensified.
Among the key industry players, Synaptics Incorporated stands out for its expertise in human interface solutions, including advanced touch and force sensors. While traditionally focused on consumer electronics, Synaptics has expanded its portfolio to address the needs of robotics, leveraging its capacitive and force-sensing technologies to enable more sensitive and responsive robotic grippers and manipulators.
In the realm of end-of-arm tooling, OnRobot A/S is a prominent supplier of plug-and-play robotic grippers and tactile sensors. The company’s products, such as the HEX force/torque sensor, are widely adopted in collaborative robotics (cobots) for applications requiring delicate handling and precise force feedback. OnRobot’s open platform approach facilitates integration with a variety of robot brands, making its tactile sensing solutions accessible to a broad market.
Another significant contributor is Soft Robotics Inc., which specializes in adaptive, soft robotic grippers equipped with embedded tactile sensing. Their mGripAI platform combines soft grippers with machine vision and tactile feedback, enabling robots to handle variable and fragile items in food processing and e-commerce fulfillment. The company’s strategic collaborations with major automation integrators and food industry leaders underscore the growing importance of tactile sensing in real-world deployments.
Strategic partnerships are a defining trend in 2025, as companies seek to combine complementary technologies. For example, sensor manufacturers are teaming up with AI and machine learning firms to enhance the interpretation of tactile data, while robotics companies are collaborating with material science experts to develop new sensor-embedded elastomers. These alliances are accelerating the commercialization of next-generation tactile sensors that offer higher sensitivity, durability, and integration flexibility.
Looking ahead, the industry is expected to see further consolidation and cross-sector partnerships, particularly as tactile sensing becomes a critical enabler for autonomous manipulation and human-robot collaboration. The ongoing investments by leading players such as Synaptics, OnRobot, and Soft Robotics Inc. signal a robust outlook for innovation and market expansion in tactile sensing components for soft robotics through 2025 and beyond.
Application Landscape: Healthcare, Manufacturing, and Service Robotics
Tactile sensing components are rapidly transforming the application landscape of soft robotics, particularly in healthcare, manufacturing, and service robotics. As of 2025, the integration of advanced tactile sensors is enabling soft robots to interact more safely and effectively with humans and delicate objects, a critical requirement across these sectors.
In healthcare, tactile sensing is pivotal for applications such as minimally invasive surgery, rehabilitation, and patient care. Soft robotic grippers equipped with high-resolution tactile sensors can now mimic the sensitivity of human touch, allowing for safer manipulation of tissues and medical instruments. Companies like Tekscan are at the forefront, offering flexible, thin-film tactile sensors that are being integrated into surgical tools and prosthetics. Similarly, Xsens provides sensor technologies that contribute to motion capture and haptic feedback systems, enhancing the precision and safety of medical robots.
In manufacturing, the demand for automation that can handle fragile or irregularly shaped items is driving the adoption of soft robotics with tactile feedback. Tactile sensors enable robots to adjust grip force dynamically, reducing product damage and improving efficiency. SCHUNK, a global leader in gripping systems, has developed tactile sensor-equipped end effectors for industrial robots, facilitating more adaptive and intelligent handling in assembly lines. Festo is also advancing soft robotic grippers with integrated tactile sensing, targeting applications in electronics, food processing, and packaging.
Service robotics is another area witnessing significant growth in tactile sensing adoption. Robots designed for personal assistance, hospitality, and logistics require the ability to interact safely with humans and navigate unstructured environments. Soft Robotics Inc. specializes in soft, adaptive grippers with embedded tactile sensors, enabling robots to handle a wide variety of objects in dynamic settings. Shadow Robot Company offers advanced robotic hands with tactile feedback, supporting research and commercial deployments in service and collaborative robotics.
Looking ahead, the next few years are expected to see further miniaturization, increased sensitivity, and improved durability of tactile sensors. The convergence of materials science, flexible electronics, and AI-driven signal processing will likely expand the capabilities and adoption of tactile sensing in soft robotics. As these components become more affordable and robust, their deployment across healthcare, manufacturing, and service sectors is set to accelerate, driving new levels of automation, safety, and human-robot collaboration.
Regional Analysis: North America, Europe, Asia-Pacific Trends
The global landscape for tactile sensing components in soft robotics is rapidly evolving, with North America, Europe, and Asia-Pacific each demonstrating distinct trends and strategic priorities as of 2025 and looking ahead. These regions are driving innovation, commercialization, and adoption of tactile sensors, leveraging their respective strengths in research, manufacturing, and application domains.
North America remains a leader in the development and early adoption of advanced tactile sensing technologies for soft robotics. The United States, in particular, benefits from a robust ecosystem of research universities, startups, and established technology firms. Companies such as 3M and Analog Devices are actively involved in sensor innovation, focusing on flexible, high-resolution tactile arrays and integration with artificial intelligence for enhanced perception. The region’s emphasis on healthcare robotics, collaborative robots (cobots), and automation in logistics is fueling demand for sensitive, reliable tactile sensors. Government funding and partnerships with institutions like MIT and Stanford further accelerate the translation of laboratory advances into commercial products.
Europe is distinguished by its strong focus on collaborative research and standardization, with the European Union supporting cross-border projects aimed at developing next-generation tactile sensors for soft robotics. Germany, the UK, and France are at the forefront, with companies such as Bosch and Schneider Electric investing in sensor miniaturization and energy efficiency. The region’s automotive and industrial automation sectors are key application areas, driving the need for robust, durable tactile components. European initiatives also emphasize sustainability and recyclability in sensor materials, aligning with broader environmental goals.
Asia-Pacific is experiencing the fastest growth in both production and adoption of tactile sensing components for soft robotics. Japan, South Korea, and China are leading the charge, leveraging their advanced manufacturing capabilities and strong robotics industries. Companies like Omron Corporation and Panasonic are pioneering the integration of tactile sensors into consumer electronics, medical devices, and service robots. The region’s focus on cost-effective mass production and rapid prototyping is making tactile sensing technologies more accessible. Government-backed initiatives in China and Japan are further accelerating R&D, with a particular emphasis on healthcare, eldercare, and smart manufacturing.
Looking forward, all three regions are expected to intensify their investments in tactile sensing for soft robotics, with North America and Europe focusing on high-performance, application-specific solutions, while Asia-Pacific drives scale and affordability. Cross-regional collaborations and standardization efforts are likely to shape the global market, ensuring interoperability and accelerating the deployment of tactile-enabled soft robots across industries.
Challenges: Integration, Durability, and Cost Barriers
The integration of tactile sensing components into soft robotics faces several persistent challenges as of 2025, with durability, seamless integration, and cost remaining at the forefront. Soft robots, by their nature, require sensors that are flexible, stretchable, and capable of withstanding repeated deformation. However, achieving robust performance under these conditions is a significant technical hurdle.
One of the primary challenges is the mechanical durability of tactile sensors. Many current solutions rely on thin-film electronics, conductive polymers, or nanomaterial composites, which can suffer from fatigue, delamination, or loss of sensitivity after repeated cycles of stretching and compression. Companies such as Tekscan and Interlink Electronics have developed flexible force and pressure sensors, but ensuring long-term reliability in highly dynamic soft robotic applications remains a work in progress. The need for encapsulation to protect sensitive elements from environmental factors (moisture, dust, chemicals) can further complicate integration and reduce sensor flexibility.
Integration is another major barrier. Tactile sensors must conform to complex, often non-planar surfaces of soft robots without impeding their movement or altering their mechanical properties. This requires advances in materials science and manufacturing techniques, such as stretchable electronics and 3D-printed sensor arrays. Companies like Xsens and 3M are exploring new materials and form factors, but large-scale, reliable integration into soft robotic systems is still limited by issues such as wiring complexity, signal noise, and the need for robust data acquisition systems.
Cost is a further limiting factor for widespread adoption. High-performance tactile sensors often rely on advanced materials (e.g., graphene, carbon nanotubes, or custom elastomers) and complex fabrication processes, driving up production costs. While some suppliers, including 3M and Tekscan, offer scalable sensor solutions, the price point for high-resolution, durable, and flexible tactile arrays remains prohibitive for many commercial applications. This is particularly true for applications requiring large-area coverage or high-density sensor networks.
Looking ahead to the next few years, the industry is expected to focus on developing more robust materials, scalable manufacturing methods, and modular sensor architectures to address these challenges. Collaborative efforts between sensor manufacturers, material suppliers, and robotics companies will be crucial in overcoming integration and durability barriers, while ongoing research into cost-effective materials and processes may help bring advanced tactile sensing within reach for broader soft robotics applications.
Future Outlook: AI Integration and Next-Gen Sensing Capabilities
The integration of artificial intelligence (AI) with tactile sensing components is poised to redefine the landscape of soft robotics in 2025 and the years immediately following. As soft robots increasingly move from research labs into real-world applications—ranging from healthcare and logistics to precision agriculture—the demand for advanced tactile sensors capable of nuanced perception and adaptive interaction is accelerating. AI-driven data processing is central to this evolution, enabling robots to interpret complex tactile information in real time and respond with human-like dexterity.
Leading sensor manufacturers and robotics companies are actively developing next-generation tactile sensing solutions that leverage AI for enhanced performance. For instance, Tekscan continues to expand its portfolio of flexible, high-resolution tactile sensors, which are being integrated with machine learning algorithms to improve object recognition, grip adjustment, and texture discrimination. Similarly, USHIO is advancing optical tactile sensors that, when combined with AI, can deliver rapid, high-fidelity feedback for soft robotic grippers and manipulators.
In 2025, the convergence of AI and tactile sensing is expected to yield several key advancements:
- Self-learning and adaptive control: AI models embedded within tactile sensor systems will enable soft robots to autonomously refine their manipulation strategies based on sensory feedback, reducing the need for manual programming and calibration.
- Multimodal sensor fusion: Companies such as ABB are exploring the integration of tactile, visual, and force sensors, with AI algorithms fusing these data streams to provide a holistic understanding of the robot’s environment and tasks.
- Miniaturization and scalability: Advances in materials science and microfabrication, led by firms like ZEISS, are enabling the production of compact, robust tactile sensors that can be embedded throughout soft robotic structures, with AI facilitating distributed sensing and decision-making.
Looking ahead, the synergy between AI and tactile sensing is expected to unlock new capabilities for soft robots, such as delicate handling of fragile objects, real-time adaptation to unpredictable environments, and safe human-robot collaboration. As industry leaders and innovators continue to push the boundaries of sensor technology and AI integration, the next few years will likely see rapid commercialization and deployment of intelligent tactile sensing systems across diverse sectors.
Strategic Recommendations for Stakeholders and Investors
The tactile sensing components market for soft robotics is poised for significant evolution in 2025 and the coming years, driven by rapid advancements in material science, sensor miniaturization, and integration with artificial intelligence. Stakeholders and investors should consider several strategic recommendations to capitalize on emerging opportunities and mitigate associated risks.
- Prioritize Partnerships with Leading Sensor Manufacturers: Collaborations with established sensor technology companies are essential. Firms such as Tekscan and ATI Industrial Automation are recognized for their high-resolution tactile sensors and force/torque sensing solutions, which are increasingly being adapted for soft robotic applications. Strategic alliances can accelerate product development and ensure access to cutting-edge components.
- Invest in Flexible and Stretchable Electronics: The demand for conformable, skin-like sensors is growing, with companies like Xsensio and ZEISS exploring advanced materials and microfabrication techniques. Investors should monitor startups and established players working on flexible substrates, as these are critical for next-generation soft robotic grippers and wearable robots.
- Support Integration with AI and Edge Computing: The value of tactile sensors is amplified when combined with real-time data processing and machine learning. Companies such as ABB and Festo are integrating tactile feedback with AI-driven control systems, enabling more adaptive and intelligent soft robots. Stakeholders should prioritize investments in platforms that facilitate seamless sensor-data integration and analytics.
- Monitor Regulatory and Standardization Developments: As tactile sensors become more prevalent in medical, industrial, and consumer robotics, compliance with safety and interoperability standards will be crucial. Engagement with industry bodies and standards organizations will help anticipate regulatory shifts and ensure product readiness for global markets.
- Explore Application-Specific Customization: The requirements for tactile sensing vary widely across sectors such as healthcare, logistics, and manufacturing. Companies like Shadow Robot Company are developing highly customized tactile solutions for dexterous manipulation. Investors should seek out firms with the capability to tailor sensor arrays and integration strategies to specific end-user needs.
Looking ahead, the tactile sensing ecosystem for soft robotics is expected to benefit from cross-industry collaboration, increased R&D funding, and the maturation of flexible electronics manufacturing. Stakeholders who proactively engage with technology leaders, invest in scalable and adaptable sensor platforms, and remain agile in response to regulatory and market trends will be best positioned to capture value in this dynamic sector.
Sources & References
- Tekscan
- ams OSRAM
- SMC Corporation
- ABB
- ATI Industrial Automation
- Murata Manufacturing
- Hamamatsu Photonics
- DuPont
- ams OSRAM
- Synaptics Incorporated
- OnRobot A/S
- Soft Robotics Inc.
- Xsens
- SCHUNK
- Shadow Robot Company
- Analog Devices
- Bosch
- Interlink Electronics
- USHIO
- ZEISS
- Xsensio