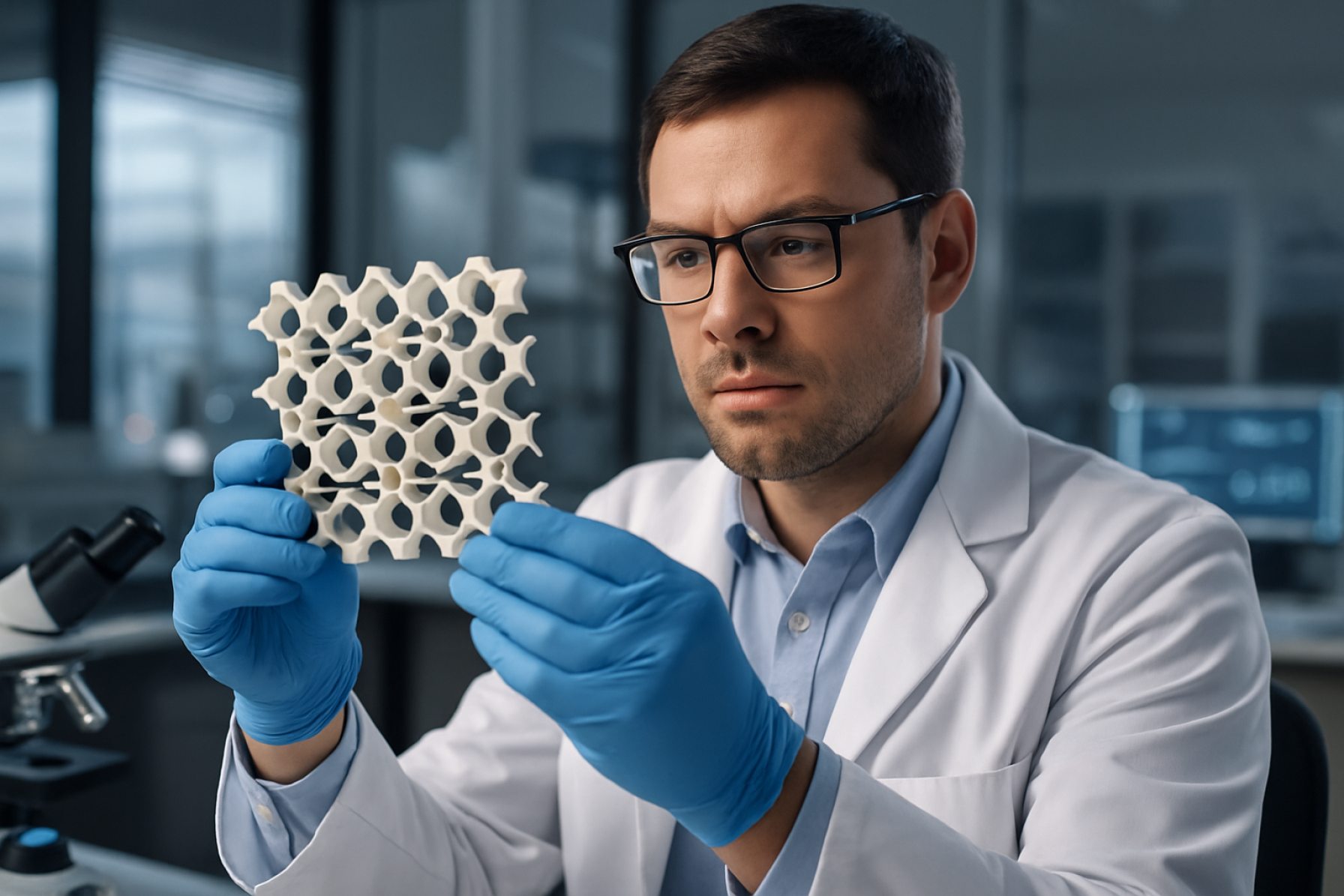
Hexachiral Metamaterial Engineering in 2025: Unlocking Next-Gen Mechanical and Acoustic Performance. Explore How This Breakthrough Technology Is Shaping the Future of Smart Materials and Industrial Innovation.
- Executive Summary: Key Trends and Market Drivers
- Hexachiral Metamaterials: Principles and Unique Properties
- Current State of the Global Hexachiral Metamaterial Market (2025)
- Major Industry Players and Recent Innovations
- Emerging Applications: Aerospace, Automotive, and Beyond
- Manufacturing Techniques and Scalability Challenges
- Market Forecasts and Growth Projections Through 2030
- Regulatory Landscape and Industry Standards
- Collaborations, Partnerships, and Academic Research Initiatives
- Future Outlook: Disruptive Potential and Strategic Opportunities
- Sources & References
Executive Summary: Key Trends and Market Drivers
Hexachiral metamaterial engineering is rapidly emerging as a transformative field within advanced materials science, driven by the unique mechanical, acoustic, and electromagnetic properties of hexachiral lattice structures. As of 2025, the sector is witnessing accelerated research-to-commercialization cycles, propelled by the convergence of additive manufacturing, computational design, and growing demand for lightweight, high-performance materials in aerospace, automotive, and defense industries.
A key trend is the integration of digital design and simulation platforms, enabling precise tailoring of hexachiral geometries for specific functionalities such as negative Poisson’s ratio (auxetic behavior), vibration damping, and impact resistance. Leading additive manufacturing companies, including Stratasys and 3D Systems, are expanding their portfolios to support the fabrication of complex chiral lattices using advanced polymers and metal alloys. These capabilities are critical for prototyping and low-volume production, particularly in sectors where weight reduction and energy absorption are paramount.
Another significant driver is the adoption of hexachiral metamaterials in next-generation aerospace structures. Major aerospace manufacturers such as Airbus and Boeing are actively exploring chiral lattice components for applications ranging from lightweight panels to morphing wing structures, aiming to enhance fuel efficiency and structural resilience. The defense sector is also investing in hexachiral armor and blast mitigation solutions, leveraging the superior energy dissipation characteristics of these architectures.
In the realm of acoustics and vibration control, companies like H.B. Fuller are investigating the use of hexachiral metamaterials for noise reduction and shock absorption in automotive and industrial environments. The ability to engineer frequency bandgaps and directional wave propagation is opening new avenues for custom soundproofing and vibration isolation products.
Looking ahead, the outlook for hexachiral metamaterial engineering is robust, with continued advancements expected in multi-material 3D printing, scalable manufacturing, and in-situ property monitoring. Industry collaborations with research institutions and standards bodies, such as ASTM International, are anticipated to accelerate the development of testing protocols and certification pathways, further facilitating market adoption. As digital manufacturing ecosystems mature, the next few years are likely to see broader commercialization of hexachiral metamaterials across high-value sectors, underpinned by ongoing innovation and cross-industry partnerships.
Hexachiral Metamaterials: Principles and Unique Properties
Hexachiral metamaterials, characterized by their periodic arrangement of chiral (handed) unit cells in a hexagonal lattice, have emerged as a focal point in advanced materials engineering. Their unique geometry imparts exceptional mechanical properties, such as negative Poisson’s ratio (auxeticity), enhanced energy absorption, and tunable anisotropy, which are unattainable in conventional materials. As of 2025, research and development in this field is accelerating, driven by the demand for lightweight, resilient, and multifunctional materials in sectors such as aerospace, automotive, and biomedical engineering.
The fundamental principle behind hexachiral metamaterials lies in their microstructural design: each unit cell consists of a central ring connected to neighboring rings via ligaments arranged in a chiral (rotationally asymmetric) fashion. This configuration enables the material to exhibit auxetic behavior—expanding laterally when stretched—resulting in superior indentation resistance and energy dissipation. Recent experimental studies have demonstrated that by varying the geometry of the ligaments and rings, engineers can precisely tailor the mechanical response, including stiffness, damping, and directional strength.
In 2025, several industry leaders and research institutions are actively exploring scalable manufacturing techniques for hexachiral metamaterials. Additive manufacturing (3D printing) has become the preferred method, allowing for the fabrication of complex chiral architectures with high precision. Companies such as Stratasys and 3D Systems are at the forefront, offering advanced polymer and metal 3D printing platforms capable of producing hexachiral structures for prototyping and functional testing. Additionally, EOS specializes in industrial-grade additive manufacturing systems, supporting the transition from laboratory-scale research to commercial-scale production.
The unique properties of hexachiral metamaterials are being harnessed in a range of applications. In aerospace, their lightweight and impact-resistant nature is being evaluated for next-generation protective panels and energy-absorbing components. In the biomedical sector, the tunable mechanical response is of interest for custom orthopedic implants and prosthetics, where conformability and shock absorption are critical. Automotive manufacturers are also investigating these materials for crashworthy structures and vibration damping.
Looking ahead, the outlook for hexachiral metamaterial engineering is promising. Ongoing collaborations between material scientists, engineers, and manufacturers are expected to yield new design paradigms and scalable production methods. As digital design tools and additive manufacturing technologies continue to advance, the integration of hexachiral metamaterials into commercial products is anticipated to accelerate, potentially transforming multiple industries by 2027 and beyond.
Current State of the Global Hexachiral Metamaterial Market (2025)
Hexachiral metamaterial engineering, a subfield of architected materials, has seen significant advancements as of 2025, driven by the demand for lightweight, tunable, and multifunctional materials in aerospace, automotive, defense, and advanced manufacturing sectors. Hexachiral structures—characterized by their honeycomb-like, chiral lattice geometry—exhibit unique mechanical properties such as negative Poisson’s ratio (auxeticity), enhanced energy absorption, and tailored wave propagation, making them attractive for next-generation applications.
The global market for hexachiral metamaterials remains in an early but rapidly evolving stage. Key industry players are primarily concentrated in North America, Europe, and East Asia, where advanced manufacturing capabilities and research infrastructure support innovation. Companies such as Boeing and Airbus have publicly highlighted ongoing research into architected metamaterials for lightweight structural components and impact-resistant panels, with hexachiral designs being explored for their superior mechanical response and energy dissipation. In the defense sector, organizations like Lockheed Martin are investigating hexachiral lattices for blast mitigation and protective armor systems, leveraging their auxetic behavior to improve resilience.
On the manufacturing side, the adoption of additive manufacturing (AM) technologies—especially laser powder bed fusion and direct energy deposition—has enabled the precise fabrication of complex hexachiral geometries in metals and polymers. Companies such as EOS and Stratasys are supplying AM platforms capable of producing these intricate structures at scale, while materials suppliers like BASF are developing advanced feedstocks optimized for metamaterial performance.
Recent data from industry consortia and standards bodies, including ASTM International, indicate a growing number of technical standards and testing protocols specific to architected metamaterials, reflecting the sector’s maturation. Collaborative initiatives between industry and academia are accelerating the translation of laboratory-scale hexachiral designs into commercial products, with pilot projects underway in vibration damping, acoustic insulation, and lightweight sandwich panels.
Looking ahead, the outlook for hexachiral metamaterial engineering is robust. Market adoption is expected to accelerate as manufacturing costs decrease and performance data from field trials become available. The next few years will likely see increased integration of hexachiral metamaterials in aerospace and defense platforms, as well as emerging applications in robotics, medical devices, and civil infrastructure. Strategic partnerships between OEMs, AM technology providers, and materials companies will be critical in scaling production and unlocking new functionalities.
Major Industry Players and Recent Innovations
Hexachiral metamaterial engineering, a field leveraging the unique mechanical and acoustic properties of chiral lattice structures, has seen significant industrial engagement and innovation as of 2025. The sector is characterized by a blend of established advanced materials companies and agile startups, each contributing to the rapid evolution of design, manufacturing, and application of hexachiral metamaterials.
Among the most prominent industry players is Evonik Industries, a global leader in specialty chemicals and advanced materials. Evonik has invested in the development of polymer-based chiral lattices, focusing on lightweight, high-strength components for aerospace and automotive applications. Their recent collaborations with aerospace OEMs have resulted in prototype panels and vibration-damping elements that exploit the auxetic and tunable acoustic properties of hexachiral structures.
Another key player is 3D Systems, renowned for its additive manufacturing technologies. 3D Systems has expanded its portfolio to include the direct fabrication of complex chiral lattices using high-performance polymers and metals. In 2024, the company announced a partnership with several European research institutes to commercialize hexachiral metamaterial-based orthopedic implants, aiming to improve load distribution and patient comfort.
In the Asia-Pacific region, Mitsubishi Chemical Group has emerged as a significant innovator. The company’s R&D division has developed scalable processes for producing hexachiral structures in thermoplastic composites, targeting the consumer electronics and protective equipment markets. Their recent patents focus on impact-resistant casings and flexible, energy-absorbing layers for wearable devices.
On the supplier side, Stratasys has introduced new print materials and software tools specifically optimized for the design and rapid prototyping of chiral metamaterials. Their open platform approach has enabled research institutions and industrial partners to iterate on lattice geometries and material combinations, accelerating the path from concept to functional prototype.
Looking ahead, the next few years are expected to bring further integration of hexachiral metamaterials into mainstream manufacturing, particularly as digital design and simulation tools mature. Industry analysts anticipate that collaborations between material suppliers, OEMs, and end-users will drive the adoption of these structures in sectors such as aerospace, medical devices, and advanced robotics. The ongoing focus on sustainability and lightweighting is likely to further boost demand for hexachiral solutions, positioning the field for robust growth through 2027 and beyond.
Emerging Applications: Aerospace, Automotive, and Beyond
Hexachiral metamaterial engineering is rapidly transitioning from laboratory research to real-world applications, with 2025 marking a pivotal year for its integration into advanced sectors such as aerospace, automotive, and beyond. Hexachiral structures—characterized by their unique honeycomb-like geometry and rotational symmetry—offer exceptional mechanical properties, including negative Poisson’s ratio (auxeticity), high energy absorption, and tunable stiffness. These features are increasingly attractive for industries seeking lightweight, resilient, and multifunctional materials.
In aerospace, the demand for materials that combine low weight with high impact resistance and vibration damping is driving the adoption of hexachiral metamaterials. Companies like Airbus and Boeing are actively exploring advanced lattice structures for next-generation airframes and interior components. Hexachiral designs are being evaluated for their potential to improve crashworthiness and reduce noise transmission, with prototype panels and sandwich structures undergoing testing in 2025. The integration of additive manufacturing, particularly selective laser sintering and electron beam melting, is enabling the production of complex hexachiral geometries in aerospace-grade alloys and composites.
The automotive sector is also witnessing a surge in interest, as manufacturers seek to enhance occupant safety and vehicle efficiency. BMW and Tesla are among the automakers investigating hexachiral metamaterials for energy-absorbing crumple zones, lightweight chassis components, and adaptive interior structures. Early-stage collaborations with material suppliers and 3D printing specialists are focusing on scalable production methods and integration with existing vehicle platforms. The unique deformation mechanisms of hexachiral lattices are being leveraged to design components that can dissipate impact energy more effectively than conventional foams or honeycombs.
Beyond aerospace and automotive, hexachiral metamaterials are finding applications in robotics, protective equipment, and civil engineering. Companies such as Boston Dynamics are exploring these materials for lightweight, flexible robotic limbs and grippers, while manufacturers of sports and industrial safety gear are developing next-generation helmets and padding with enhanced shock absorption. In civil engineering, hexachiral panels are being tested for use in seismic-resistant structures and vibration isolation systems.
Looking ahead, the outlook for hexachiral metamaterial engineering is highly promising. Ongoing advances in computational design, digital manufacturing, and material science are expected to accelerate commercialization. Industry partnerships and pilot projects in 2025 and the following years will likely yield the first large-scale deployments, setting the stage for broader adoption across multiple high-performance sectors.
Manufacturing Techniques and Scalability Challenges
Hexachiral metamaterials, characterized by their unique chiral lattice structures and auxetic mechanical responses, are at the forefront of advanced material engineering in 2025. The manufacturing of these architected materials presents both significant opportunities and notable scalability challenges, particularly as demand grows in sectors such as aerospace, biomedical devices, and flexible electronics.
Additive manufacturing (AM) remains the primary technique for fabricating hexachiral metamaterials at both research and commercial scales. Selective Laser Sintering (SLS) and Direct Metal Laser Sintering (DMLS) are widely adopted for metals, while Stereolithography (SLA) and Digital Light Processing (DLP) are preferred for polymers. Companies such as EOS GmbH and Stratasys have developed industrial-grade AM platforms capable of producing complex chiral geometries with high precision. These systems enable the realization of intricate unit cells and lattice architectures that are otherwise unachievable with traditional subtractive methods.
Despite these advances, scalability remains a central challenge. The layer-by-layer nature of AM processes inherently limits throughput, especially for large-area or high-volume production. Surface finish and resolution are also critical, as the mechanical properties of hexachiral metamaterials are highly sensitive to geometric fidelity. To address these issues, manufacturers are investing in multi-laser systems and parallelized printing arrays. For example, 3D Systems has introduced multi-head printers aimed at increasing build rates for architected materials.
Material selection further complicates scalability. While polymers are relatively easy to process, the translation of hexachiral designs into metals or ceramics—necessary for high-performance applications—requires advanced powder handling and post-processing techniques. Companies like Renishaw are developing closed-loop quality control and in-situ monitoring systems to ensure repeatability and structural integrity at scale.
Looking ahead, hybrid manufacturing approaches are gaining traction. These combine AM with traditional processes such as injection molding or roll-to-roll fabrication to enable mass production of chiral structures. Collaborative efforts between industry and research institutions are accelerating the development of scalable processes, with pilot lines and demonstrators expected to mature by 2026–2027. The outlook is optimistic: as digital design and manufacturing ecosystems evolve, the cost and complexity barriers for hexachiral metamaterial production are expected to decrease, paving the way for broader industrial adoption.
Market Forecasts and Growth Projections Through 2030
Hexachiral metamaterial engineering, a subset of architected materials characterized by their unique chiral lattice structures, is poised for significant market expansion through 2030. The current landscape in 2025 is marked by a surge in research-to-commercialization activities, particularly in sectors such as aerospace, automotive, defense, and advanced manufacturing. These materials are valued for their exceptional mechanical properties, including negative Poisson’s ratio (auxeticity), high energy absorption, and tunable acoustic and vibration damping capabilities.
Key industry players are accelerating the transition from laboratory-scale demonstrations to scalable production. Companies such as Airbus and Boeing are actively exploring hexachiral metamaterials for lightweight, impact-resistant components in next-generation aircraft and spacecraft. Their R&D divisions are collaborating with advanced materials suppliers and academic institutions to integrate these structures into fuselage panels, interior components, and protective casings, aiming to reduce weight while enhancing safety and performance.
In the automotive sector, manufacturers like BMW Group and Tesla, Inc. are investigating the use of hexachiral lattices for crash energy management and noise reduction in electric vehicles. The ability to tailor mechanical responses at the microstructural level is driving interest in these materials for both structural and functional applications, with pilot projects underway to validate their performance in real-world conditions.
The defense industry is another major adopter, with organizations such as Lockheed Martin and Northrop Grumman investing in the development of hexachiral metamaterial-based armor and blast mitigation systems. These efforts are supported by government-funded research programs focused on next-generation protective solutions for personnel and vehicles.
From a manufacturing perspective, the proliferation of advanced additive manufacturing (AM) technologies is a critical enabler for the commercial viability of hexachiral metamaterials. Companies like Stratasys and 3D Systems are expanding their portfolios to include high-precision AM systems capable of fabricating complex chiral geometries at scale, which is expected to drive down costs and open new market opportunities.
Looking ahead, the global market for hexachiral metamaterial engineering is projected to experience double-digit compound annual growth rates (CAGR) through 2030, fueled by increasing demand for lightweight, multifunctional materials across high-value industries. As standardization efforts mature and supply chains adapt, adoption is expected to accelerate, with North America, Europe, and East Asia emerging as key growth regions. The next few years will likely see a shift from prototyping to widespread deployment, positioning hexachiral metamaterials as a cornerstone of advanced engineering solutions.
Regulatory Landscape and Industry Standards
The regulatory landscape and industry standards for hexachiral metamaterial engineering are rapidly evolving as the technology matures and finds applications in sectors such as aerospace, automotive, civil engineering, and advanced manufacturing. As of 2025, there is no single, unified global standard specifically governing hexachiral metamaterials; however, several established frameworks and organizations are shaping the regulatory environment.
In the European Union, the European Committee for Standardization (CEN) and the European Committee for Electrotechnical Standardization (CENELEC) are actively monitoring the integration of metamaterials into existing standards for advanced materials and structural components. These bodies are working to ensure that new materials, including hexachiral architectures, comply with safety, environmental, and performance requirements, particularly in critical infrastructure and transportation applications.
In the United States, the ASTM International and the American Society of Mechanical Engineers (ASME) are the primary organizations developing standards relevant to mechanical testing, material characterization, and additive manufacturing processes that are often used to fabricate hexachiral metamaterials. ASTM’s Committee F42 on Additive Manufacturing Technologies is particularly relevant, as many hexachiral structures are produced using advanced 3D printing techniques. These standards address issues such as repeatability, mechanical integrity, and quality assurance.
Industry leaders such as EOS GmbH and Stratasys Ltd., both prominent in additive manufacturing, are collaborating with standards bodies to ensure that their equipment and processes can reliably produce hexachiral metamaterials that meet emerging regulatory requirements. These companies are also participating in pilot programs and consortia aimed at validating the performance of metamaterial-based components in real-world conditions.
Looking ahead, the next few years are expected to see the formalization of dedicated standards for metamaterials, including hexachiral types, as their adoption increases in safety-critical applications. The International Organization for Standardization (ISO) is anticipated to play a central role in harmonizing global standards, particularly as cross-border supply chains and certification processes become more important. Additionally, regulatory agencies in sectors such as aviation and civil engineering are likely to issue specific guidance on the use of hexachiral metamaterials, focusing on lifecycle assessment, recyclability, and long-term durability.
Overall, while the regulatory framework is still in development, the active involvement of standards organizations and leading manufacturers is accelerating the path toward robust, internationally recognized guidelines for hexachiral metamaterial engineering.
Collaborations, Partnerships, and Academic Research Initiatives
Hexachiral metamaterial engineering is rapidly advancing through a network of collaborations, partnerships, and academic research initiatives, particularly as the field matures into 2025. The unique mechanical and acoustic properties of hexachiral structures—such as negative Poisson’s ratio and tunable bandgaps—have attracted the attention of both academic institutions and industry leaders seeking to leverage these materials for next-generation applications in aerospace, automotive, and civil engineering.
In recent years, several prominent universities have established dedicated research groups focused on chiral and auxetic metamaterials. For example, the University of Cambridge and Imperial College London have ongoing projects exploring the computational design and additive manufacturing of hexachiral lattices, often in partnership with industrial stakeholders. These collaborations are supported by national funding agencies and European consortia, aiming to bridge the gap between fundamental research and scalable production.
On the industry side, companies specializing in advanced materials and additive manufacturing are increasingly engaging with academic partners to accelerate the commercialization of hexachiral metamaterials. EOS GmbH, a leader in industrial 3D printing, has been involved in joint research with universities to optimize the fabrication of complex chiral geometries using selective laser sintering and direct metal laser sintering. Similarly, Stratasys is collaborating with research institutions to develop new polymer-based hexachiral structures for lightweight, impact-resistant components.
Internationally, the National Aeronautics and Space Administration (NASA) and the European Space Agency (ESA) have both funded research into chiral metamaterials for aerospace applications, recognizing their potential for vibration damping and structural health monitoring. These agencies often facilitate multi-institutional projects that bring together material scientists, mechanical engineers, and computational modelers.
Looking ahead to the next few years, the trend is toward deeper integration between academia and industry, with a focus on standardizing testing protocols and scaling up production methods. Initiatives such as open-access databases of chiral lattice designs and shared testbeds for mechanical characterization are expected to emerge, further accelerating innovation. As intellectual property portfolios grow and pilot projects transition to commercial products, the collaborative ecosystem surrounding hexachiral metamaterial engineering is poised to deliver tangible impacts across multiple sectors by the late 2020s.
Future Outlook: Disruptive Potential and Strategic Opportunities
Hexachiral metamaterial engineering is poised to become a transformative force across multiple industries in 2025 and the coming years, driven by its unique mechanical properties such as negative Poisson’s ratio, high energy absorption, and tunable stiffness. The ongoing shift from laboratory-scale demonstrations to scalable manufacturing is accelerating, with several key players and research institutions focusing on industrialization and application-specific customization.
In aerospace and defense, the demand for lightweight, impact-resistant structures is catalyzing the adoption of hexachiral metamaterials. Companies like Airbus and Boeing are actively exploring advanced lattice structures for next-generation airframes and interior components, aiming to enhance fuel efficiency and crashworthiness. The integration of hexachiral designs into sandwich panels and energy-absorbing layers is expected to move from prototyping to early-stage deployment by 2026, as additive manufacturing capabilities mature.
In the automotive sector, leading manufacturers such as BMW Group and Tesla are investigating the use of hexachiral metamaterials for lightweight chassis components and advanced crash protection systems. The focus is on leveraging the auxetic behavior of these materials to improve occupant safety while reducing vehicle mass, aligning with the industry’s electrification and sustainability goals.
The medical device industry is another frontier, with companies like Smith+Nephew and Stryker exploring hexachiral scaffolds for orthopedic implants and prosthetics. The ability to tailor mechanical response and promote tissue integration is expected to yield next-generation implants with enhanced longevity and patient outcomes. Early clinical trials and regulatory submissions are anticipated within the next two to three years.
Strategically, the disruptive potential of hexachiral metamaterials lies in their capacity for on-demand customization and digital manufacturing. Firms such as 3D Systems and Stratasys are expanding their additive manufacturing platforms to support complex chiral geometries, enabling rapid prototyping and localized production. This is expected to lower barriers for entry in sectors like consumer electronics, sports equipment, and protective gear, where performance differentiation is critical.
Looking ahead, the convergence of computational design, advanced materials, and digital manufacturing is set to unlock new business models and supply chain efficiencies. As standardization efforts by organizations such as ASTM International progress, broader adoption and certification of hexachiral metamaterial components are likely, paving the way for widespread commercialization by the late 2020s.
Sources & References
- Stratasys
- 3D Systems
- Airbus
- Boeing
- H.B. Fuller
- ASTM International
- EOS
- Lockheed Martin
- BASF
- Evonik Industries
- Renishaw
- Northrop Grumman
- European Committee for Standardization (CEN)
- American Society of Mechanical Engineers (ASME)
- International Organization for Standardization (ISO)
- University of Cambridge
- Imperial College London
- National Aeronautics and Space Administration (NASA)
- European Space Agency (ESA)
- Smith+Nephew