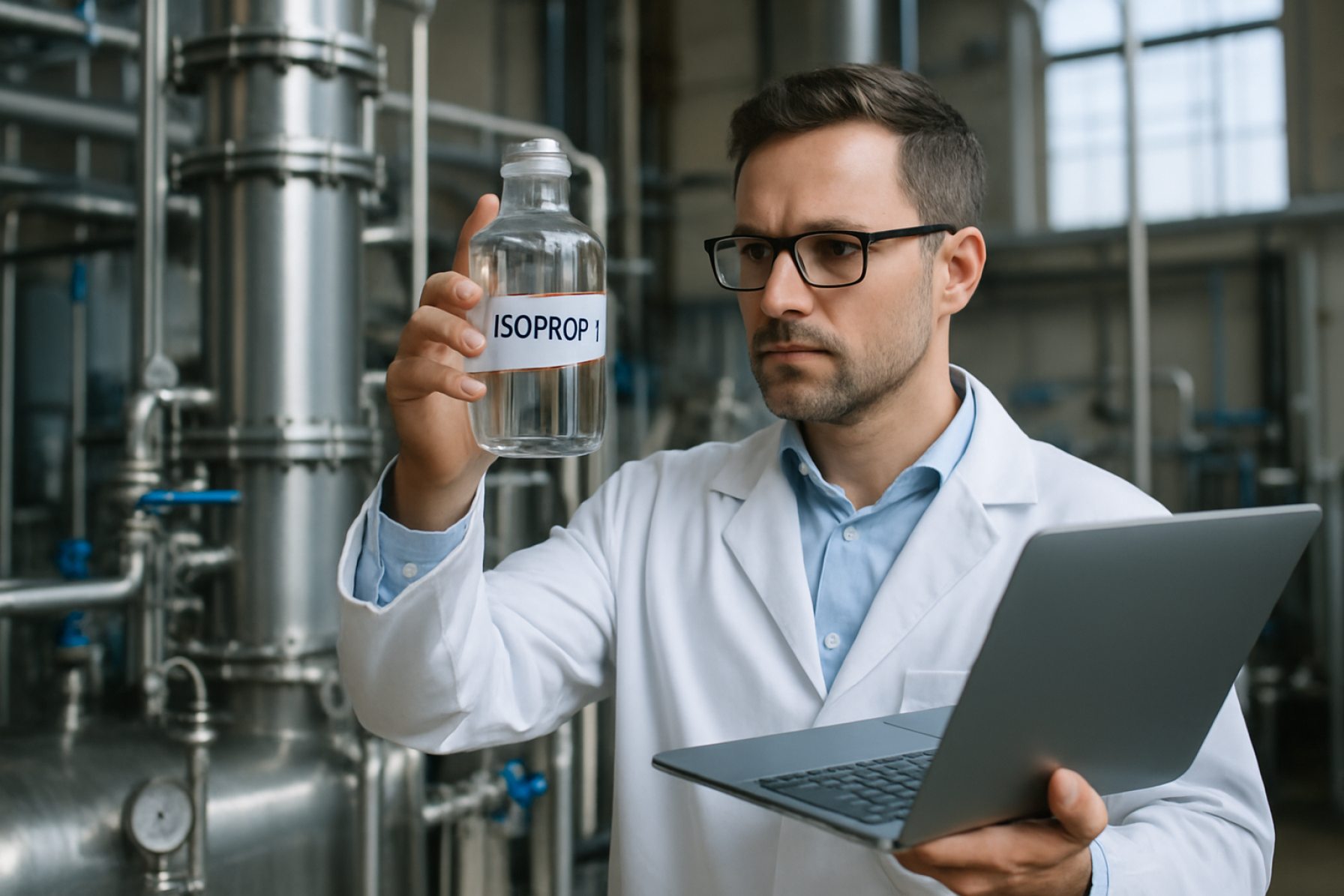
Table of Contents
- Executive Summary: Key 2025 Insights & Market Drivers
- Market Size & Growth Forecasts Through 2030
- Emerging Technologies Revolutionizing Solvent Recovery
- Regulatory & Environmental Landscape: 2025 and Beyond
- Competitive Analysis: Leading Manufacturers & Innovators
- End-User Industries: Trends in Pharmaceuticals, Electronics, and Chemicals
- Cost-Benefit Analysis: ROI and Operational Efficiencies
- Sustainability & Circular Economy Initiatives
- Regional Hotspots: North America, Europe, and Asia-Pacific Outlook
- Future Outlook: Challenges, Opportunities, and Innovation Roadmap
- Sources & References
Executive Summary: Key 2025 Insights & Market Drivers
The isopropyl-based solvent recovery systems market is poised for significant momentum in 2025 and the immediate years ahead, driven by tightening environmental regulations, rising costs of virgin solvents, and an industry-wide push for sustainable manufacturing practices. Isopropyl alcohol (IPA) is central to critical sectors such as pharmaceuticals, electronics, and specialty chemicals, where its recovery and reuse are essential for cost savings and compliance with evolving environmental standards.
In 2025, regulatory authorities across North America, Europe, and Asia are intensifying oversight of solvent emissions and hazardous waste, urging manufacturers to adopt advanced recovery technologies. For instance, the United States Environmental Protection Agency (EPA) and the European Chemicals Agency (ECHA) are mandating stricter reporting and control over volatile organic compound (VOC) emissions, directly shaping procurement decisions in solvent-heavy industries. This regulatory landscape is boosting demand for high-efficiency solvent recovery systems capable of achieving purity levels suitable for reuse in sensitive processes.
Manufacturers such as BÜCHI Labortechnik AG, KAISER GmbH & Co. KG, and Dürr AG are at the forefront, offering distillation units and turnkey recovery systems specifically designed for isopropyl alcohol. These systems often feature advanced automation, energy recovery, and remote monitoring to meet the operational efficiency and traceability requirements of 2025’s manufacturing landscape. Additionally, solvent recyclers like Veolia Environnement S.A. are expanding capabilities to service closed-loop recovery for large industrial clients, supporting circular economy models and reducing overall solvent consumption.
Data from leading system providers indicate a shift toward modular, scalable recovery units that can be rapidly deployed and integrated within existing production lines. This trend addresses increasing demand from small and mid-sized enterprises seeking to enhance sustainability credentials without major capital investment. Furthermore, the adoption of digital controls and real-time analytics is enabling predictive maintenance, minimizing downtime, and ensuring compliance with stricter reporting obligations.
Looking forward, the isopropyl-based solvent recovery market is expected to continue its robust growth, underpinned by the dual imperatives of cost containment and environmental stewardship. As more regions introduce landfill bans and solvent recycling mandates, the adoption of high-performance recovery solutions is likely to accelerate across diverse manufacturing sectors. With established players and new entrants focusing on innovation, the competitive landscape is fostering technology advancements that improve recovery rates, energy consumption, and user experience.
Market Size & Growth Forecasts Through 2030
The global market for isopropyl-based solvent recovery systems is poised for notable growth through 2030, driven by increasingly stringent environmental regulations, rising waste management costs, and the chemical industry’s focus on circular economy principles. As of 2025, demand is being propelled particularly in sectors such as pharmaceuticals, specialty chemicals, and electronics manufacturing—industries where isopropyl alcohol (IPA) is widely used for cleaning, extraction, and as a process solvent.
Leading equipment manufacturers and solution providers are reporting robust order books and expansion plans to meet projected increases in customer requirements. For instance, KAESER KOMPRESSOREN and ROSS Controls have both highlighted solvent recovery as a strategic growth area within their broader industrial process solutions portfolios. Meanwhile, Dürr AG—a major player in sustainable production technologies—has reported ongoing investments in solvent recovery system design, with a particular focus on modular and scalable units tailored for IPA recovery.
North America and Europe remain the dominant markets for isopropyl-based solvent recovery systems in 2025, owing to well-established regulatory frameworks such as the EU Industrial Emissions Directive (IED) and the U.S. Environmental Protection Agency’s Resource Conservation and Recovery Act (RCRA). However, rapid industrialization and stricter environmental enforcement in Asia-Pacific—especially in China and India—are expected to drive the fastest growth rates over the next five years. Recognized suppliers such as Veolia and GEM Srl have expanded their presence in these regions to capture emerging opportunities.
- By 2025, the market size for isopropyl-based solvent recovery systems is estimated (by industry manufacturers) to reach a value in the high hundreds of millions USD, with compound annual growth rates (CAGR) widely projected in the range of 5-8% through 2030, according to supplier communications and published business outlooks.
- Driving factors include increased adoption by small and mid-sized enterprises, innovation in energy-efficient distillation and condensation technologies, and integration with digital monitoring for process optimization.
- Product development is trending toward turnkey, automated systems with enhanced safety and compliance features, as reported by leading solution providers.
Looking forward, the solvent recovery systems market—particularly for isopropyl-based applications—will likely see continued investment in R&D from established industrial technology groups. Partnerships between equipment manufacturers, end-users, and environmental service providers are expected to further stimulate adoption and create new business models around solvent recycling as a service. With regulatory and cost pressures intensifying, the outlook for the sector remains positive through 2030.
Emerging Technologies Revolutionizing Solvent Recovery
The landscape of isopropyl-based solvent recovery systems is undergoing significant transformation as emerging technologies align with industry demands for sustainability, efficiency, and regulatory compliance. As of 2025, the adoption of advanced distillation, membrane separation, and integrated process automation is accelerating, driven by both environmental regulations and the cost pressures of solvent-intensive industries such as pharmaceuticals, electronics, and chemicals.
One of the most notable developments is the integration of modular, automated distillation units specifically designed to recover and purify isopropyl alcohol (IPA) from waste streams. These systems leverage real-time process analytics and adaptive control algorithms to optimize energy consumption and maximize solvent yield. Notably, manufacturers like BÜCHI Labortechnik AG are enhancing their solvent recovery lines with energy-efficient condensers and programmable logic controllers, enabling continuous operation and reducing manual intervention.
Membrane-based separation technologies are also gaining traction. Innovations in solvent-resistant membranes now allow for the selective removal of water and contaminants from IPA mixtures, minimizing the need for thermal input and reducing the overall carbon footprint of the recovery process. Companies such as GEA Group are advancing hybrid systems that combine membrane filtration with vacuum distillation, achieving higher recovery rates while maintaining product purity.
Another emerging trend is the implementation of digital monitoring and predictive maintenance in solvent recovery operations. Utilizing Industrial Internet of Things (IIoT) platforms, operators can monitor system performance, solvent quality, and key parameters in real time, facilitating proactive maintenance and minimizing unplanned downtime. Industry leaders like Alfa Laval are equipping their solvent recovery systems with smart sensors and data analytics, which are especially valuable for pharmaceutical and electronics manufacturers seeking to meet stringent purity standards.
Looking ahead, the outlook for isopropyl-based solvent recovery is shaped by stricter environmental regulations and corporate sustainability targets. With the European Union and other jurisdictions tightening rules on solvent emissions and waste, demand for closed-loop, high-efficiency recovery systems is expected to surge over the next few years. Furthermore, the circular economy initiatives of major chemical producers and end-users are likely to accelerate investment in next-generation recovery technologies, positioning the sector for robust innovation and growth.
Regulatory & Environmental Landscape: 2025 and Beyond
The regulatory and environmental landscape for isopropyl-based solvent recovery systems in 2025 is shaped by tightening industrial emissions standards, escalating waste management costs, and ambitious sustainability targets across multiple sectors. Regulatory bodies in North America, Europe, and Asia-Pacific are intensifying oversight on volatile organic compound (VOC) emissions and hazardous waste disposal, directly impacting facilities that utilize or recover isopropyl alcohol (IPA) solvents.
In the United States, the Environmental Protection Agency (EPA) continues to enforce the National Emission Standards for Hazardous Air Pollutants (NESHAP), which includes strict limits on VOC emissions from industrial processes involving solvents like IPA. These regulations are encouraging chemical manufacturers, pharmaceutical companies, and electronics producers to invest in advanced recovery systems that can reduce emissions and recycle solvents on-site. The EPA’s Resource Conservation and Recovery Act (RCRA) also influences solvent management by classifying spent IPA as hazardous waste, further incentivizing recovery over disposal (Environmental Protection Agency).
In Europe, the Industrial Emissions Directive (IED) and the Registration, Evaluation, Authorisation and Restriction of Chemicals (REACH) framework are pushing manufacturers to adopt closed-loop solvent management, including IPA recovery, to minimize environmental impact. These regulations are complemented by national efforts—such as Germany’s TA Luft air quality standards—which are being updated to include lower permissible VOC thresholds, likely coming into effect in the next few years. This is anticipated to drive upgrades in recovery system efficiencies and adoption rates across the continent (European Chemicals Agency).
The Asia-Pacific region, particularly China and Japan, is witnessing rapid adoption of solvent recycling technologies due to growing environmental enforcement and government incentives. China’s Ministry of Ecology and Environment continues to enact stricter controls on industrial VOC emissions, promoting the deployment of on-site IPA recovery units in electronics, automotive, and pharmaceutical sectors (Ministry of Ecology and Environment of the People's Republic of China).
Industry response is robust, with leading equipment manufacturers advancing modular, automated, and energy-efficient IPA recovery solutions that align with the latest regulatory demands. Companies such as 3M, DuPont, and Merck KGaA are supporting end-users with turnkey systems and compliance support, reflecting a broader trend toward greener manufacturing.
Looking ahead, the next few years are expected to bring even more stringent emission and waste minimization requirements globally. This will likely accelerate the integration of isopropyl-based solvent recovery systems, not only as a compliance measure but as a core component of corporate sustainability strategies. Continuous advancements in system automation, recovery rates, and energy efficiency will further support regulatory alignment and environmental stewardship for industries reliant on IPA solvents.
Competitive Analysis: Leading Manufacturers & Innovators
The competitive landscape for isopropyl-based solvent recovery systems in 2025 is shaped by increasing industrial demand for sustainable solvent management and stricter environmental regulations. Key manufacturers are investing in advanced technologies to improve recovery rates, energy efficiency, and system automation, which are critical differentiators in the current market.
Established players such as Veolia and Kaeser Kompressoren continue to expand their portfolios with modular and scalable solvent recovery units, targeting sectors like pharmaceuticals, specialty chemicals, and electronics. These companies leverage decades of engineering expertise and global service networks, facilitating adoption among large-scale manufacturers seeking reliable, compliant solutions.
Innovation in isopropyl solvent recovery is increasingly driven by mid-sized specialists. Onsite Solvent Recycling Systems and IST America have introduced compact, automated recovery units tailored for smaller batch operations and localized recovery. Their systems often feature real-time monitoring and closed-loop technology, which minimize emissions and operational downtime—features especially valued by laboratories and high-mix, low-volume manufacturers.
Technological advancements in distillation and membrane separation are also defining the competitive edge. Companies such as ROSS Controls are integrating smart sensors and IoT connectivity for predictive maintenance and process optimization, while Stilmas is focusing on energy-efficient distillation columns that reduce operating costs and carbon footprint.
Geographically, North America and Europe lead in the adoption of advanced isopropyl recovery systems due to stringent regulatory frameworks and the presence of major end-users. However, increased investment in electronics and pharmaceutical manufacturing across Asia is driving regional players to enhance their offerings and expand capacity. This has spurred collaboration between global technology suppliers and local system integrators to adapt solutions for diverse operational requirements and regulatory standards.
Looking ahead, the competitive outlook is marked by ongoing R&D in solvent purification and digital process control, with industry participants anticipating stronger demand for customizable, plug-and-play systems. Partnerships between equipment manufacturers, chemical producers, and industrial end-users are expected to accelerate the development and deployment of next-generation solvent recovery equipment, further raising the bar for performance, sustainability, and compliance in the sector.
End-User Industries: Trends in Pharmaceuticals, Electronics, and Chemicals
The adoption and evolution of isopropyl-based solvent recovery systems are being significantly shaped by the dynamic needs and regulatory landscapes within the pharmaceuticals, electronics, and chemicals industries as of 2025 and looking ahead. These sectors are under continual pressure to enhance sustainability, reduce costs, and comply with increasingly stringent environmental regulations, all of which are catalyzing investments in advanced solvent recovery technologies.
In the pharmaceutical industry, the drive toward greener manufacturing is pronounced. Isopropyl alcohol (IPA) is widely used as a solvent for synthesis, cleaning, and formulation processes. With the rise in regulatory expectations for solvent waste minimization, pharmaceutical manufacturers are progressively implementing on-site recovery systems to recycle IPA, thus reducing raw material costs and hazardous waste disposal. Leading technology providers such as BUCHI and Labconco Corporation are actively supplying modular and scalable solvent recovery units tailored for pharma cleanroom environments, emphasizing automation and closed-loop safety to meet Good Manufacturing Practice (GMP) standards. As new production facilities come online in regions like North America, Europe, and Asia, the adoption of these systems is expected to accelerate further through 2025 and beyond.
The electronics sector is another significant consumer of isopropyl alcohol, particularly for wafer cleaning, degreasing, and precision surface preparation. With the ongoing miniaturization of components and the transition to advanced semiconductor nodes, the purity requirements for recovered solvents are increasingly stringent. Major manufacturers such as EquipNet and KAESER KOMPRESSOREN are responding by delivering solvent recovery systems capable of achieving high-purity outputs suitable for electronics-grade applications, while also integrating real-time monitoring and process analytics. As chip manufacturers expand capacity and invest in greener operations, solvent recovery is becoming an integral part of sustainability initiatives across Asia-Pacific and North America.
Within the chemicals industry, isopropyl-based solvent recovery is driven by both economic and environmental imperatives. Chemical processors are increasingly upgrading from basic distillation units to advanced, energy-efficient recovery systems to address escalating energy costs and regulatory requirements. Companies like Koch Industries are providing large-scale, customizable solvent recovery solutions for bulk chemical production and specialty chemical operations. The focus is on reducing emissions and maximizing solvent reuse, with digital integration for process optimization.
Looking forward, as regulatory frameworks such as the EU’s Industrial Emissions Directive and US EPA standards continue to tighten, end-user industries are expected to further accelerate investments in high-efficiency isopropyl-based solvent recovery systems, underpinning a trend toward circular manufacturing and operational resilience.
Cost-Benefit Analysis: ROI and Operational Efficiencies
The adoption of isopropyl-based solvent recovery systems is increasingly driven by a rigorous cost-benefit analysis, particularly as industries face mounting pressure to enhance sustainability and reduce operating expenses in 2025 and beyond. The return on investment (ROI) for these systems is shaped by several factors, including solvent purchase costs, waste disposal fees, energy usage, and regulatory compliance.
A key driver of ROI is the substantial reduction in recurring raw material expenses. Isopropyl alcohol (IPA) is widely used in pharmaceuticals, electronics, and specialty chemicals, where its recovery and reuse can offset the need for fresh solvent purchases by up to 90% in optimized systems. For example, manufacturers offering automated distillation and solvent recycling units report that users can achieve payback periods as short as 12 to 24 months, owing to both the high recovery rates and the value of reclaimed IPA (KAESER KOMPRESSOREN).
Operational efficiencies are realized through streamlined solvent management. Automated recovery units integrated into production lines minimize manual handling and reduce the risk of occupational exposure, which can translate into fewer workplace incidents and lower insurance costs. Advanced systems often feature energy-efficient designs and programmable controls, ensuring that both energy consumption and labor input are minimized. Some manufacturers highlight the ability of their systems to decrease total solvent-related operational costs by 30-50%, especially when factoring in the reduction of hazardous waste disposal (Veolia).
Regulatory compliance is another significant contributor to the economic rationale for solvent recovery. In 2025, stricter environmental regulations continue to raise the cost of solvent waste disposal and require companies to demonstrate solvent recycling initiatives. By recovering and reusing IPA in-house, organizations can not only avoid surcharges but may also qualify for green incentives or certifications that enhance brand reputation and market competitiveness (Veolia).
Looking ahead, the outlook for isopropyl-based solvent recovery systems remains positive. As system costs decrease due to technological improvements and increased manufacturing scale, even small and medium enterprises are expected to see accessible ROI horizons. The convergence of sustainability goals, operational efficiency, and regulatory demands ensures that solvent recovery will remain a financially and strategically sound investment across multiple process industries in the next few years (KAESER KOMPRESSOREN).
Sustainability & Circular Economy Initiatives
As sustainability becomes a central driver in industrial decision-making, isopropyl-based solvent recovery systems are advancing both in adoption and technological sophistication through 2025 and the coming years. These systems play a critical role in supporting the circular economy by enabling the reuse and recycling of isopropyl alcohol (IPA), which is widely utilized across pharmaceuticals, electronics, and specialty chemicals manufacturing. The recovery process typically involves distillation and purification, allowing spent IPA to be reclaimed and reintroduced into production cycles, thereby reducing both raw material demand and hazardous waste generation.
Several leading equipment manufacturers and chemical suppliers are foregrounding solvent recovery in their sustainability initiatives. For instance, BÜCHI Labortechnik AG, a major provider of laboratory and industrial evaporation systems, highlights the environmental and cost benefits of closed-loop solvent recovery technology. These systems are designed to minimize emissions, reduce energy usage, and help companies meet increasingly stringent environmental standards. Similarly, StillDragon and Deantares are among companies offering modular and scalable solvent recovery solutions tailored for industrial clients, emphasizing adaptability and high-efficiency operation.
Industry-wide, the movement toward circularity is being reinforced by global initiatives and regulatory frameworks. The BASF and Dow groups, for example, are publicizing their commitment to solvent recovery and chemical recycling as part of broader climate action and resource efficiency strategies. These corporations report measurable progress in reducing Scope 1 and Scope 3 emissions, with solvent recycling contributing directly to these goals by lowering the lifecycle carbon footprint of IPA and associated products.
Data from recent years suggests a marked increase in solvent recovery system installations, driven both by environmental compliance and the economic imperative to reduce solvent purchasing costs. The trend is expected to continue sharply upward through 2025 and beyond as more companies pursue zero-waste targets and embrace green chemistry principles. Furthermore, the development of intelligent automation, remote monitoring, and improved distillation column designs is making recovery systems more accessible and effective for a wider range of applications.
Looking ahead, the outlook for isopropyl-based solvent recovery is robust. With ongoing investments from major chemical players and continued tightening of environmental regulations, such systems are poised to become standard across solvent-intensive industries. The rapid evolution of recovery technology and the integration of digital process controls will further enhance system efficiency and traceability, supporting industry-wide sustainability and circular economy objectives.
Regional Hotspots: North America, Europe, and Asia-Pacific Outlook
The market for isopropyl-based solvent recovery systems is experiencing significant momentum across North America, Europe, and the Asia-Pacific (APAC) region in 2025, driven by regulatory pressure, sustainability targets, and growth in end-user industries. In North America, the United States and Canada are seeing increased adoption of solvent recovery solutions due to stringent environmental regulations from agencies such as the U.S. Environmental Protection Agency, which encourage hazardous waste minimization and solvent recycling in sectors like pharmaceuticals, electronics, and specialty chemicals. Major system manufacturers such as Kaeser Kompressoren and Veolia are active in supplying turnkey recovery systems and services, emphasizing circular economy principles and cost savings for industrial clients.
Europe continues to be a regional leader in the deployment of isopropyl-based solvent recovery systems due to robust regulatory frameworks such as the EU Industrial Emissions Directive and the push for net-zero emissions by 2050. Countries including Germany, France, and the United Kingdom are investing in advanced recovery technologies to comply with strict waste management and emissions standards. Leading providers in the region, for example, Deco Industries, focus on high-efficiency distillation units that enable chemical manufacturers and processors to recover and reuse isopropyl alcohol at scale, reducing disposal costs and raw material consumption. The European market outlook through 2025 and beyond is characterized by rising demand for modular, automated, and energy-efficient recovery systems, with adoption extending to smaller manufacturing operations as well.
The Asia-Pacific region is emerging as a key growth engine for isopropyl-based solvent recovery systems, propelled by rapid industrialization and expanding pharmaceutical, electronics, and automotive sectors in China, India, Japan, and South Korea. Governments in the region are strengthening environmental compliance and promoting sustainable industrial practices, leading to greater investment in recovery infrastructure. Notably, companies such as Toshiba and Mitsubishi Chemical Group are engaged in developing and integrating solvent recovery solutions as part of broader efforts to reduce environmental footprints and align with global sustainability standards.
Across all three regions, the outlook for the next several years points to continued technology advancements—such as automation, real-time process monitoring, and improved solvent purification rates—alongside growing partnerships between equipment manufacturers and major end-users. The confluence of regulation, sustainability objectives, and economic incentives is expected to sustain robust growth for isopropyl-based solvent recovery systems well beyond 2025.
Future Outlook: Challenges, Opportunities, and Innovation Roadmap
The future of isopropyl-based solvent recovery systems is shaped by a convergence of regulatory, technological, and market-driven forces. In 2025 and the next few years, several challenges and opportunities are expected to direct the innovation roadmap for these systems, particularly as industrial sectors seek to enhance sustainability, reduce costs, and comply with tightening environmental mandates.
A primary challenge for solvent recovery operators remains the increasing stringency of environmental regulations concerning volatile organic compounds (VOCs) and hazardous air pollutants. Regulators in North America, the European Union, and Asia-Pacific have progressively tightened emissions limits, placing pressure on manufacturers to implement more efficient recovery and purification processes. Companies such as 3M and DuPont, both of which are heavily involved in specialty chemicals and process optimization, have highlighted the need for advanced, closed-loop solvent recovery systems that minimize environmental impact while maintaining operational efficiency.
Technological innovation is accelerating to meet these requirements. Recent years have seen the introduction of modular, automated recovery units capable of real-time monitoring and process optimization. Leading equipment manufacturers like Kaeser Kompressoren and system integrators are focusing on energy-efficient distillation columns, novel membrane separations, and digital controls that allow for adaptive process management. These innovations enable higher purity recovery of isopropyl alcohol (IPA), reduce energy consumption, and lower total cost of ownership, enhancing the economic appeal for end users in pharmaceuticals, electronics, and coatings production.
On the opportunity side, the circular economy paradigm is gaining traction among global manufacturers. Closed-loop solvent management not only addresses compliance but also reduces raw material costs and waste generation. Companies such as BASF are investing in research and development to extend solvent lifecycles and facilitate integration of recovery systems into existing process lines, signaling a strategic commitment to resource efficiency and sustainability.
Looking ahead, the innovation roadmap is likely to emphasize data-driven operations, modularity, and integration with broader plant automation platforms. As digitalization advances, remote monitoring and predictive maintenance will become standard features, further improving system uptime and performance. Industry stakeholders anticipate that, by the late 2020s, widespread adoption of next-generation recovery systems will not only ensure compliance but also deliver measurable returns through resource conservation and enhanced operational resilience. Collaboration between chemical manufacturers, equipment suppliers, and industrial end-users will be crucial in overcoming technical and economic barriers, driving the sector toward a more sustainable and profitable future.
Sources & References
- BÜCHI Labortechnik AG
- Dürr AG
- Veolia Environnement S.A.
- ROSS Controls
- GEM Srl
- BÜCHI Labortechnik AG
- GEA Group
- Alfa Laval
- European Chemicals Agency
- Ministry of Ecology and Environment of the People's Republic of China
- DuPont
- IST America
- Stilmas
- Labconco Corporation
- Koch Industries
- StillDragon
- BASF
- Toshiba
- Mitsubishi Chemical Group