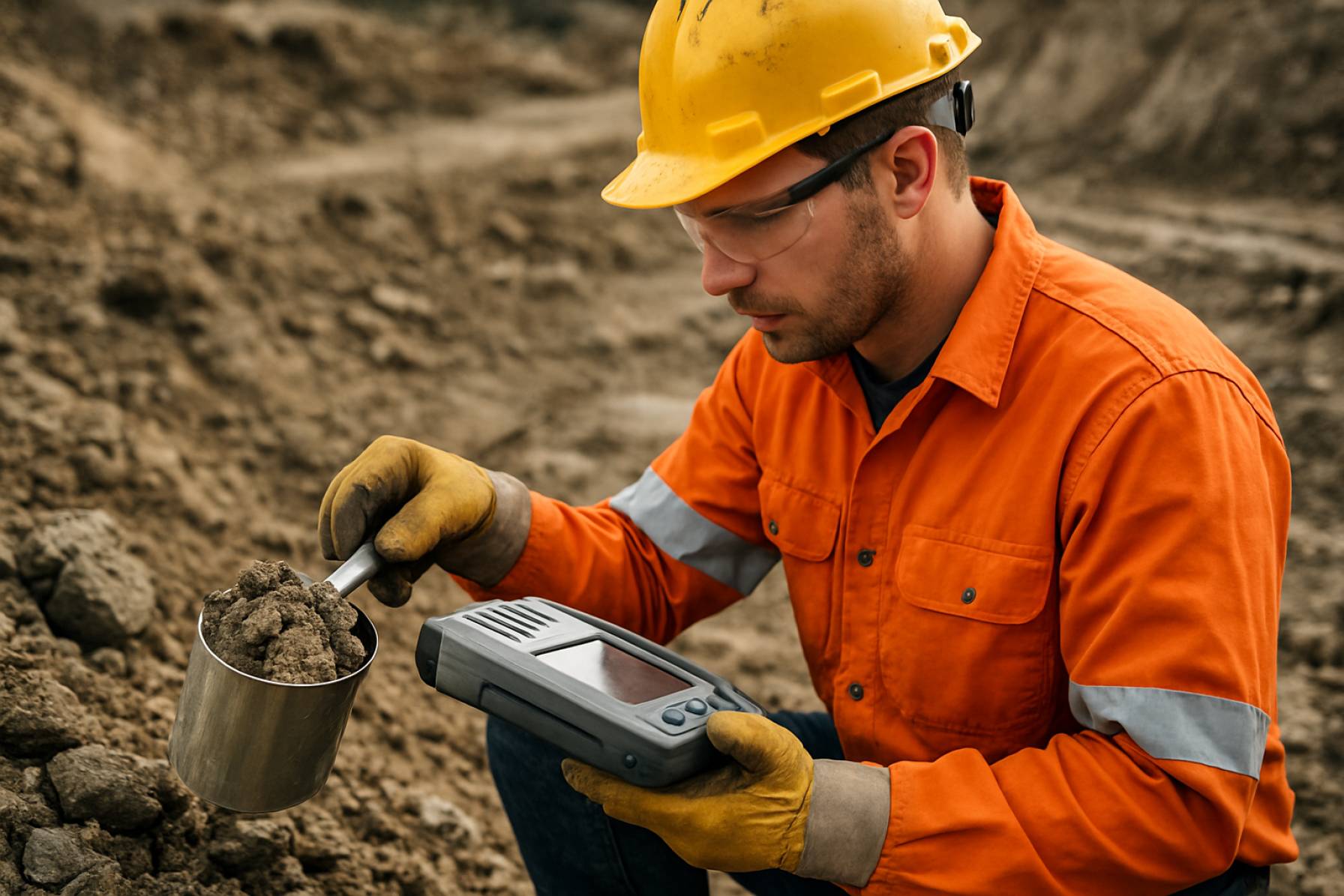
Table of Contents
- Executive Summary: Key Takeaways for 2025 and Beyond
- Market Size & Growth Forecast: 2025–2030 Outlook
- Latest Innovations in Muck Sampling Calibration Tech
- Key Players & Industry Leaders: Who’s Driving Change?
- Adoption Drivers: Mining Efficiency, Compliance, and Cost
- Emerging Automation & Digitalization Solutions
- Challenges: Accuracy, Integration, and Environmental Impact
- Regional Analysis: Global Hotspots & Expansion Opportunities
- Case Studies: Calibration Success Stories from Leading Mines
- Future Outlook: Strategic Recommendations and Disruptive Potential
- Sources & References
Executive Summary: Key Takeaways for 2025 and Beyond
The evolution of muck sampling calibration technologies is set to play a pivotal role in mining operations as the industry intensifies its focus on precision, automation, and digitalization in 2025 and beyond. Muck sampling—critical for on-site ore grade estimation and process optimization—relies on accurate calibration technologies to ensure representative results and informed downstream decisions. Recent years have seen major equipment manufacturers and technology providers advancing their offerings to address longstanding challenges such as sample bias, insufficient granularity, and real-time data integration.
Key developments in 2025 include the integration of advanced sensors, automated sampling systems, and real-time data analytics platforms. Companies like FLSmidth and Thermo Fisher Scientific are expanding their portfolios with on-line elemental analyzers and automated sample cutters, reducing human error and improving calibration repeatability. These solutions are increasingly compatible with digital mine management systems, supporting more agile and data-driven decision-making across the mining value chain.
Data from pilot projects and early adopters indicate that automated calibration technologies can improve sample representativity by up to 20% and reduce analytical turnaround times by 30–50%. The adoption of machine learning for calibration adjustment—pioneered by several OEMs—adds an additional layer of optimization, as real-time feedback loops calibrate equipment based on evolving operational parameters. This is particularly relevant as ore bodies become more complex and operational margins tighten.
Another notable trend is the push for standardization and interoperability. Industry groups such as the Society for Mining, Metallurgy & Exploration are collaborating with technology suppliers to define best practices and calibration protocols that facilitate benchmarking and regulatory compliance worldwide.
Looking ahead, the market outlook for muck sampling calibration technologies is optimistic, driven by heightened demand for resource efficiency, ESG compliance, and digital transformation. The next few years are expected to see increased investments in AI-powered calibration solutions, remote monitoring capabilities, and modular systems that can be tailored to diverse mining environments. Overall, the acceleration of innovation and collaborative standard-setting point toward a future where calibrated muck sampling underpins safer, more sustainable, and more profitable mining operations.
Market Size & Growth Forecast: 2025–2030 Outlook
The global market for muck sampling calibration technologies is poised for steady growth over the 2025–2030 period, driven by increasing demand for precision in ore grade control, automation, and operational efficiency in mining. As mining operations become more complex and the emphasis on resource optimization intensifies, advanced calibration technologies for muck sampling are emerging as critical tools in both underground and surface mining environments.
In 2025, the market landscape is characterized by rising adoption of real-time and automated calibration systems that integrate with digital mine platforms. Key mining equipment manufacturers and technology suppliers are investing in robust solutions that ensure sample integrity and minimize human error. Companies such as Sandvik and Komatsu offer advanced material handling and sampling systems designed for high-accuracy and seamless integration with mine management software, reflecting the sector’s shift toward data-driven decision-making.
Recent developments include the deployment of on-board calibration modules and sensor-based technologies capable of providing immediate feedback on sample quality and consistency. These innovations are being supported by leading sensor suppliers and automation specialists like Siemens, who have expanded their offerings in mine process automation, including calibration and quality assurance systems. The integration of Internet of Things (IoT) connectivity and AI-driven analytics further enhances the reliability of calibration, enabling predictive maintenance and reducing downtime.
Market growth is particularly robust in regions with active investments in new mining projects or where regulatory requirements for ore accounting and environmental compliance are tightening. The push for sustainable mining practices is also a significant growth catalyst, as accurate muck sampling reduces waste and improves resource recovery rates. As a result, suppliers are tailoring calibration solutions for diverse ore bodies and varying operational conditions.
Looking toward 2030, the market is expected to expand at a moderate to strong CAGR, propelled by technological innovation, the proliferation of digital mining tools, and increasing global mineral demand. The entry of new solution providers and ongoing R&D efforts by established players like FLSmidth and Metso Outotec are anticipated to further intensify competition and accelerate adoption. The outlook remains positive, with muck sampling calibration technologies becoming a cornerstone of efficient, sustainable, and profitable mine operations worldwide.
Latest Innovations in Muck Sampling Calibration Tech
Muck sampling calibration technologies have continued to evolve rapidly as the mining industry seeks more accurate, real-time, and automated solutions for grade control and ore tracking. In 2025, several notable innovations are shaping the landscape, focusing on improving sample representativity, reducing human error, and integrating digital workflows for enhanced decision-making.
One of the most significant advances is the wider adoption of automated sampling and calibration systems within underground and open-pit operations. These systems, often mounted on mining equipment or integrated into conveyor lines, provide continuous muck sampling, allowing for real-time analysis and rapid data feedback. Companies like Sandvik are at the forefront, offering solutions that combine automated collection with on-board X-ray fluorescence (XRF) and laser-induced breakdown spectroscopy (LIBS) technologies. This integration facilitates immediate calibration of sampling equipment, reducing turnaround time from hours to minutes in some cases.
Another innovation gaining traction is the use of digital twins and machine learning algorithms to calibrate and predict sampling performance. By using operational data from equipment sensors and laboratory assays, these systems can dynamically adjust calibration settings, ensuring consistent sample quality regardless of variable muck pile conditions. Komatsu and other OEMs have begun partnering with technology providers to embed such intelligence directly into their loaders and haul trucks.
Additionally, the advent of portable, ruggedized analytical devices—capable of withstanding harsh mining environments—is transforming field calibration practices. Devices from manufacturers like Thermo Fisher Scientific now offer user-friendly interfaces that enable on-site calibration checks and adjustments, minimizing the risk of calibration drift and increasing confidence in sample integrity.
In terms of data integration, interoperability standards are being promoted by industry organizations to ensure that calibration data from muck sampling systems can be seamlessly imported into mine planning and management platforms. This connectivity supports more proactive grade control and reconciliation processes, enhancing overall productivity.
Looking ahead to the next few years, expectations are high for further automation, with the potential deployment of fully autonomous muck sampling and calibration units. These would utilize advanced robotics and AI to operate continuously with minimal human intervention, promising further gains in accuracy, safety, and operational efficiency. With ongoing investment from leading mining equipment manufacturers and increasing pressure on mines to deliver reliable grade data, the outlook for muck sampling calibration technology remains robust and innovation-driven.
Key Players & Industry Leaders: Who’s Driving Change?
The landscape of muck sampling calibration technologies is evolving rapidly, driven by industry leaders and specialized technology firms responding to increasing demands for accuracy, automation, and digital integration in mining operations. In 2025, the drive to optimize ore grade control, reduce dilution, and enhance resource recovery is pushing companies to invest in advanced calibration solutions for muck sampling systems.
Key players include established mining equipment manufacturers and niche technology developers. Sandvik continues to integrate smart sensor arrays and automated calibration protocols into its underground mining equipment, enabling real-time sampling data and improved calibration accuracy directly at the muck face. Similarly, Komatsu leverages digital solutions and remote monitoring to ensure that muck sampling instruments remain within calibration tolerances, thereby supporting consistent ore quality tracking.
Automation and robotics firms are also making significant strides. ABB has expanded its mining automation portfolio to include calibration modules for sample collection devices, emphasizing closed-loop feedback systems and predictive maintenance. These systems reduce human error and downtime, contributing to safer and more reliable muck sampling operations.
Analytical technology specialists such as Thermo Fisher Scientific are notable for their portable XRF and LIBS analyzers, which now feature automated calibration routines and connectivity to central data hubs. This enables near real-time calibration verification and adjustment, crucial for dynamic underground environments where muck characteristics can change rapidly.
On the software and data integration front, companies like Hexagon are developing platforms that combine sampling data, calibration status, and geological models. Their solutions allow mine operators to track calibration performance over time and anticipate recalibration needs using predictive analytics.
Looking ahead, the outlook for 2025 and beyond suggests increasing collaboration between equipment manufacturers, analytical tech providers, and digital solution companies. The integration of AI-driven diagnostics, IoT-enabled calibration alerts, and centralized data repositories is expected to further streamline the calibration process, reduce operational risks, and improve decision-making for grade control and resource management. As sustainability and automation become central themes in mining, leaders in muck sampling calibration technology are poised to play a critical role in shaping the industry’s future.
Adoption Drivers: Mining Efficiency, Compliance, and Cost
The adoption of muck sampling calibration technologies in mining is driven by mounting pressures on operational efficiency, regulatory compliance, and cost management. As the mining sector faces increasingly complex ore bodies and heightened environmental scrutiny in 2025 and beyond, precise calibration of muck sampling systems is critical for ensuring reliable ore grade control and minimizing dilution.
Efficiency gains are a primary catalyst for technology uptake. Modern muck sampling calibration solutions integrate automated sensors, digital controls, and real-time analytics to streamline workflows. By providing prompt, accurate feedback on ore quality, these systems enable operators to optimize blast designs, adapt excavation strategies, and reduce unnecessary processing of waste material. Leading suppliers, such as Sandvik and Epiroc, have advanced muck sampling solutions that focus on automation, reducing manual intervention and enhancing productivity across underground and open-pit operations.
Compliance is another pivotal driver as global regulations tighten around ore traceability and environmental impact. Accurate sampling and calibration are fundamental for reporting resource estimates, managing mineral rights, and meeting sustainability standards. Automated calibration technologies help mines maintain consistent, auditable records—an essential factor in jurisdictions with strict reporting requirements. For instance, Metso highlights the role of quality control technologies in supporting regulatory compliance and transparent resource accounting.
Cost management remains a compelling reason for adoption. Poorly calibrated muck sampling can lead to costly errors in ore-waste classification, resulting in significant financial losses through misdirected material or excessive processing. By leveraging advanced calibration tools, mines can minimize sampling errors and optimize recovery rates, translating directly to improved margins. Additionally, integrating calibration technologies reduces labor costs and safety risks by limiting manual sampling in hazardous environments, a benefit emphasized by equipment suppliers such as FLSmidth.
Looking ahead, the proliferation of digital mining, with increasing use of IoT-enabled devices and artificial intelligence in calibration, is expected to further drive adoption. Seamless integration with mine management platforms will enable predictive maintenance and continuous calibration, setting new industry benchmarks for accuracy and efficiency. As competition intensifies and sustainability imperatives grow, investment in muck sampling calibration technologies will remain a strategic priority for mining operators worldwide.
Emerging Automation & Digitalization Solutions
In 2025, muck sampling calibration technologies are experiencing rapid transformation, driven by the mining sector’s shift toward greater automation, digitalization, and real-time quality control. Traditional manual muck sampling methods, known for their labor intensity and variable accuracy, are increasingly supplemented or replaced by automated solutions that leverage sensor integration, data analytics, and connectivity advances. The need for precise ore grade control, especially in underground mining and block caving operations, is pushing mining companies and equipment suppliers to invest in next-generation calibration systems.
One prominent trend is the adoption of automated sampling stations and online analyzers, which enable continuous or high-frequency sample collection and analysis directly on the material handling circuit. These systems often incorporate technologies such as X-ray fluorescence (XRF), laser-induced breakdown spectroscopy (LIBS), and prompt gamma neutron activation analysis (PGNAA) for rapid, non-invasive elemental assessment. Leading equipment manufacturers like Sandvik and Komatsu have begun integrating such sensors into their material handling and mucking equipment, allowing real-time calibration of sampling data with minimal human intervention.
Digital calibration platforms are also gaining traction, with cloud-based data management and machine learning algorithms enhancing the accuracy and reproducibility of muck sample analysis. Companies such as ABB and Siemens offer automation solutions that connect on-site analyzers with centralized mineral processing control systems. This integration enables ongoing calibration, anomaly detection, and correction, thereby reducing sampling errors and improving metallurgical reconciliation.
Emerging pilot projects in 2025 demonstrate the convergence of robotics and digital calibration in muck sampling. For instance, autonomous mucking vehicles equipped with sample collection and in-situ analysis modules are being trialed in large-scale operations, targeting faster decision-making and enhanced safety. The use of digital twins—virtual replicas of physical sampling systems—further supports predictive calibration and optimization of sampling protocols.
Looking ahead, the outlook for muck sampling calibration is marked by increasing adoption of sensor fusion, edge computing, and AI-driven calibration adjustment across global mining operations. As interoperability standards mature and data security protocols strengthen, these advances are expected to deliver more consistent sample quality, lower operational costs, and better compliance with sustainability and traceability requirements. The coming years will likely see further collaboration between mining companies, OEMs, and technology providers to refine and scale these solutions, ultimately reshaping the future of muck sampling and mineral resource management.
Challenges: Accuracy, Integration, and Environmental Impact
Muck sampling calibration technologies are crucial for ensuring accurate ore grade assessment and optimal resource recovery in mining operations. However, as of 2025, several challenges persist in the areas of accuracy, integration, and environmental impact.
Achieving high accuracy in muck sampling calibration remains a technical challenge. Variability in particle size distribution, moisture content, and heterogeneity of muck piles can introduce significant sampling errors. In recent years, advancements in sensor-based technologies, such as X-ray fluorescence (XRF) and Prompt Gamma Neutron Activation Analysis (PGNAA), have improved real-time elemental analysis, but calibration of these instruments against standard reference materials and in situ conditions continues to be a significant hurdle. According to Sandvik, precise calibration protocols are required to mitigate the effects of dust, vibration, and temperature fluctuations commonly encountered in underground and open-pit environments.
Integration of muck sampling calibration technologies into existing mine workflows presents another set of challenges. Many mines operate with legacy data management systems that may not fully support the automated data acquisition and transfer from modern sampling and calibration devices. FLSmidth and Komatsu have highlighted the need for interoperable solutions that can seamlessly connect real-time sampling data with mine planning and fleet management software. Efforts are underway to standardize data protocols and enhance connectivity, but widespread adoption is still in progress, particularly for smaller operators with limited IT infrastructure.
Environmental impact is increasingly scrutinized in muck sampling processes. Traditional grab and scoop methods can generate excess waste and disturbance. Automated and inline sampling systems are being developed to minimize sample volumes and reduce material handling, thereby decreasing the ecological footprint of calibration operations. Companies such as Metso Outotec are investing in closed-loop sampling circuits and dust suppression technologies to address these concerns. Nonetheless, achieving regulatory compliance and meeting sustainability targets remains a complex balancing act, especially as governments introduce stricter environmental standards for mine waste handling and reporting.
Looking ahead, the next few years are likely to see further integration of digital calibration tools, increased automation, and the adoption of greener sampling solutions. Collaboration between mining companies and equipment manufacturers will be essential to overcoming these persistent challenges and ensuring that muck sampling calibration technologies meet the evolving demands of the industry.
Regional Analysis: Global Hotspots & Expansion Opportunities
Muck sampling calibration technologies are gaining strategic importance in mining regions worldwide as companies seek to maximize ore recovery and improve grade control. In 2025, global hotspots for innovation and deployment include Australia, Canada, South Africa, and certain regions of South America, each responding to unique geological and regulatory challenges with tailored calibration solutions.
Australia continues to lead in the adoption of advanced muck sampling calibration, underpinned by its large-scale iron ore and gold operations. Companies such as Rio Tinto and BHP have been integrating automated, real-time calibration systems within their mine-to-mill workflows, enhancing the accuracy of material characterization. The collaboration with technology suppliers and research bodies is setting new industry benchmarks for calibration repeatability and sampling representativity.
In Canada, the focus is on adapting muck sampling calibration to colder climates and polymetallic ore bodies, requiring robust hardware and flexible software calibration protocols. Firms like Teck Resources are working with equipment manufacturers to develop more durable sampling systems and to integrate machine learning algorithms for dynamic calibration adjustments, a trend expected to accelerate through 2025 and beyond.
South Africa’s mining sector, notably in platinum and gold, is prioritizing calibration accuracy due to increasingly complex ore geometries and ore-waste discrimination needs. Companies such as Anglo American are piloting portable calibration rigs and real-time data analytics platforms to improve operational decision-making and regulatory compliance, paving the way for broader adoption across the continent.
In South America, particularly in Chile and Peru, muck sampling calibration is being driven by the copper industry’s demand for precise grade control and environmental accountability. Local operators, including Codelco, are investing in next-generation calibration sensors and digital platforms, often in partnership with global instrumentation providers, to align with both productivity and sustainability targets.
Looking ahead, expansion opportunities are anticipated in emerging mining regions of Central Asia and Africa, where large-scale new projects are being planned. Governments and private sector actors are increasingly recognizing the value of reliable muck sampling calibration for resource estimation and ESG compliance, signaling a broader global diffusion of these technologies in the next few years.
Case Studies: Calibration Success Stories from Leading Mines
In 2025, the mining industry continues to prioritize accurate ore control and grade reconciliation, with muck sampling calibration technologies emerging as a crucial component. Recent case studies from leading mining operations underscore the measurable benefits achieved through the adoption of advanced calibration systems for muck sampling, resulting in enhanced data quality, reduced ore dilution, and improved operational efficiency.
One notable example is the implementation of automated sampling and calibration solutions at large-scale gold and copper mines. Companies such as Sandvik have deployed intelligent loading and hauling equipment integrated with real-time sampling and data transmission capabilities. These systems enable immediate feedback on ore characteristics, allowing mines to dynamically adjust their extraction and blending processes. In 2024, a mid-tier gold mine in Western Australia reported a 12% improvement in grade control accuracy after integrating digitally calibrated muck sampling systems, directly attributing the improvement to minimized human error and consistent sample integrity.
Similarly, Thermo Fisher Scientific has supplied on-site elemental analyzers for continuous calibration of muck samples in several South American copper mines. These analyzers use X-ray fluorescence (XRF) technology to provide rapid, non-destructive analysis of multiple elements. In a 2025 case study, a major Chilean copper producer documented a reduction in assay turnaround time from 48 hours to under 8 hours, resulting in faster decision-making and a 7% decrease in ore misclassification.
Another success story comes from a Canadian underground nickel operation, where the adoption of automated sample preparation and calibration systems supplied by FLSmidth led to significant improvements in sample representativity and traceability. The operation reported a 10% reduction in sample bias and improved compliance with internal QA/QC protocols, enhancing both short-term and life-of-mine resource estimation accuracy.
Looking ahead, the industry outlook for muck sampling calibration technology remains strong. Key players are investing in machine learning algorithms and IoT-enabled sensors to further automate calibration and validation processes. This trend is expected to drive additional case studies in the next few years, with mines reporting higher efficiencies, cost savings, and sustainability gains as a direct result of implementing advanced calibration technologies.
Future Outlook: Strategic Recommendations and Disruptive Potential
The outlook for muck sampling calibration technologies in 2025 and the coming years is characterized by rapid innovation, increasing automation, and a strategic shift towards real-time, data-driven orebody management. Modern mining operations are under growing pressure to improve ore recovery rates, reduce dilution, and maintain compliance with increasingly stringent environmental and regulatory standards. As a result, the demand for accurate, efficient, and automated muck sampling calibration systems is expected to intensify.
Recent years have witnessed a surge in the adoption of automated and sensor-based calibration systems. Technologies such as X-ray fluorescence (XRF), prompt gamma neutron activation analysis (PGNAA), and hyperspectral imaging are increasingly being integrated into muck sampling processes to deliver near real-time compositional analysis. Companies like Sandvik and Epiroc have begun offering advanced automation platforms that facilitate more precise calibration and integration with mine-wide digital ecosystems. These systems are designed to enhance the traceability and quality control of ore and waste streams, minimizing human error and improving decision-making speed.
In parallel, leading suppliers are investing in cloud-based data integration, allowing sampling results to be instantly synchronized with mine planning and fleet management systems. Initiatives from firms such as FLSmidth are paving the way for smarter, connected mining operations, where calibration data is leveraged to optimize blasting, hauling, and processing in real-time. The strategic use of artificial intelligence and machine learning is anticipated to further disrupt traditional calibration methods, enabling predictive analytics for ore grade forecasting and more dynamic process control.
Despite these advances, key challenges remain. Calibration accuracy can be hindered by geological variability, equipment maintenance, and operator training gaps. Mining companies are advised to prioritize robust sensor validation protocols, ongoing personnel training, and close collaboration with technology suppliers to ensure sustained performance gains. Strategic partnerships with OEMs and digital solution providers are recommended to accelerate technology transfer and customization for site-specific requirements.
Looking ahead, regulatory bodies such as the International Council on Mining and Metals are increasingly advocating for transparent reporting and traceable material flows, further incentivizing the deployment of advanced calibration technologies. The disruptive potential of these innovations lies in their ability to transform muck sampling from a periodic, manual process to a continuous, intelligent system—ultimately driving operational excellence and supporting the industry’s transition towards fully autonomous mining.