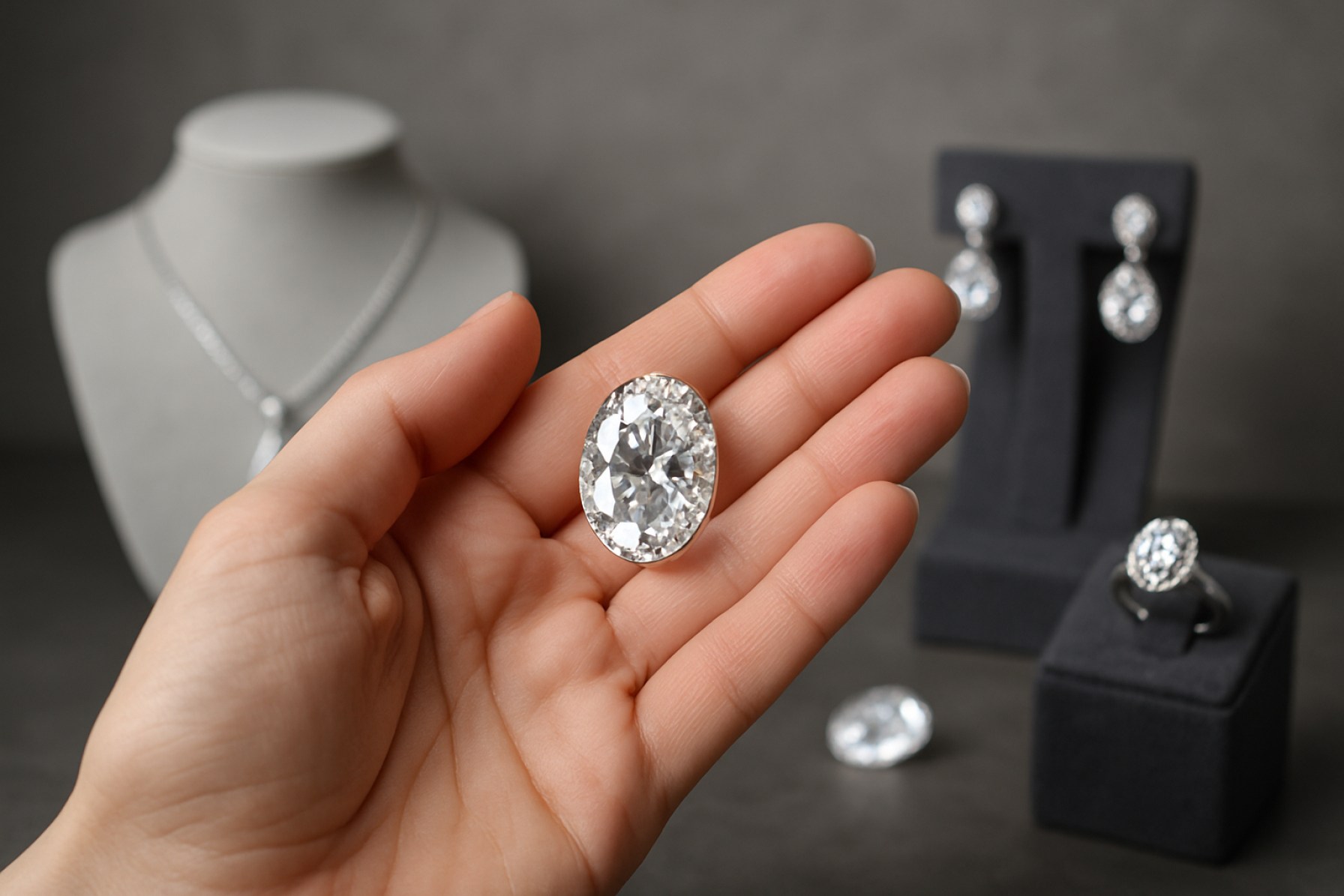
Table of Contents
- Executive Summary: 2025 Snapshot & Key Takeaways
- Introduction to Zirconia-Based High-Precision Jewelry Fabrication
- Technological Innovations Shaping the Industry
- Major Players and Official Industry Initiatives
- 2025 Market Size, Growth Drivers, and Forecasts to 2030
- Applications: From Luxury to Industrial Jewelry
- Supply Chain, Sourcing, and Sustainability Initiatives
- Competitive Landscape and Key Strategic Moves
- Challenges, Regulatory Considerations, and Risk Factors
- Future Outlook: Trends, Opportunities, and What’s Next
- Sources & References
Executive Summary: 2025 Snapshot & Key Takeaways
The global landscape for zirconia-based high-precision industrial jewelry fabrication in 2025 is marked by robust technological advancements and growing adoption across luxury and industrial segments. Zirconia, notably yttria-stabilized zirconia (YSZ), continues to gain traction as a premier alternative to traditional gemstones and metals, owing to its superior mechanical properties, high fracture toughness, biocompatibility, and the capacity for intricate, repeatable manufacturing processes.
A significant trend in 2025 is the integration of advanced Computer-Aided Design (CAD) and Computer-Aided Manufacturing (CAM) solutions within leading jewelry production houses. Companies such as Hoben International and Tosoh Corporation have expanded their specialized zirconia offerings, supplying raw materials and engineered powders tailored for precision sintering and additive manufacturing techniques. These developments facilitate the creation of highly detailed, custom jewelry pieces with consistent quality, fueling demand among both designers and end consumers.
Manufacturers are leveraging state-of-the-art sintering and injection molding processes to produce zirconia components with minimal tolerances and exceptional surface finishes. For example, CeramTec and 3DCeram have highlighted their ability to deliver complex, miniaturized forms for watch components and high-end jewelry, underscoring zirconia’s relevance in both decorative and functional roles.
Sustainability and ethical sourcing are also shaping procurement strategies in 2025. Zirconia’s synthetic production eliminates the environmental and ethical concerns associated with mined gemstones, aligning with industry pledges for responsible manufacturing. Industry bodies like the Gemological Institute of America (GIA) are strengthening certification and traceability standards for synthetic materials, further legitimizing zirconia products in global markets.
Looking ahead, the outlook for zirconia-based jewelry fabrication remains highly positive. The sector is expected to witness continued investment in automation, quality control, and innovative finishing techniques through 2027. End-user industries, particularly luxury watchmaking and bespoke jewelry, are poised to accelerate adoption as consumers increasingly value both the performance attributes and sustainability credentials of precision zirconia components.
- Rapid adoption of CAD/CAM and additive manufacturing for precision zirconia jewelry.
- Expanded supply of engineered zirconia powders and components from leading manufacturers.
- Heightened emphasis on sustainability and certification, with support from industry bodies.
- Strong growth prospects in luxury, bespoke, and industrial jewelry segments through 2027.
Introduction to Zirconia-Based High-Precision Jewelry Fabrication
Zirconia (zirconium dioxide, ZrO₂) has rapidly advanced from its origins as a refractory and dental material to a premier choice for high-precision industrial jewelry fabrication. Its adoption is driven by a combination of outstanding physical properties—exceptional hardness, chemical stability, and a diamond-like optical appearance—making it both an aesthetic and durable alternative to natural gemstones and traditional metals. In 2025, the jewelry sector is experiencing a notable shift toward engineered ceramics, with zirconia at the forefront, largely due to its ability to meet the demands for sustainability, precision, and consumer customization.
The fabrication of zirconia-based jewelry leverages advanced industrial processes, including high-pressure sintering, precision CNC machining, and laser micro-engraving. Companies such as Tosoh Corporation and CeramTec supply stabilized zirconia powders and blanks, which serve as the foundational material for these processes. The industry’s move towards digital design and additive manufacturing further improves design complexity, surface finish, and repeatability, critical for luxury and bespoke jewelry markets.
Precision in zirconia jewelry fabrication is now enabled by technologies commonly used in the dental and medical device sectors. For instance, Ivoclar and 3M have adapted isostatic pressing and CAD/CAM milling systems for jewelry applications, allowing micro-level tolerance and intricate geometric patterns previously unattainable with traditional metals or gemstones. This results in pieces that not only mimic the brilliance and clarity of diamonds or sapphires but also offer superior wear resistance and hypoallergenic properties.
The current outlook for zirconia-based high-precision jewelry fabrication is highly positive. Sustainability pressures and consumer demand for ethical alternatives to mined gemstones are propelling zirconia’s popularity. Leading jewelry brands and manufacturers, including Swarovski, are increasingly highlighting zirconia in their high-end collections, capitalizing on its eco-friendly profile and technical versatility. As process automation and digital manufacturing mature, costs are expected to decrease, making high-quality zirconia jewelry more accessible. The next few years are anticipated to see further integration of AI-driven design and additive manufacturing, expanding the creative boundaries and market reach for zirconia-based industrial jewelry fabrication.
Technological Innovations Shaping the Industry
The landscape of high-precision industrial jewelry fabrication is being rapidly transformed by advanced zirconia-based technologies, with significant innovations expected to shape the sector through 2025 and beyond. Zirconia, particularly yttria-stabilized zirconia (YSZ), has gained traction due to its superior mechanical strength, optical properties, and biocompatibility, offering a compelling alternative to traditional precious stones and metals in jewelry manufacturing.
Recent years have seen the industrial jewelry sector adopt advanced computer-aided design and manufacturing (CAD/CAM) solutions for zirconia component production. Companies such as Ivoclar have developed high-purity zirconia blanks that allow for intricate milling, enabling the creation of complex, highly detailed jewelry pieces with micron-level precision. The integration of 5-axis CNC milling machines and additive manufacturing techniques further enhances the accuracy and repeatability of intricate designs, supporting mass customization and reducing material wastage.
Laser sintering and digital light processing (DLP) 3D printing are also beginning to impact zirconia jewelry fabrication. These technologies permit the direct fabrication of both prototypes and final pieces from zirconia powders, accelerating product development cycles and expanding design possibilities. CeramTec has highlighted the potential of advanced ceramics, including zirconia, for precision applications, citing ongoing investments in manufacturing capabilities that facilitate rapid, high-volume production for decorative and functional jewelry components.
Coloration and surface finishing are further areas of innovation. Companies are introducing dopant technologies to achieve a spectrum of hues and persistent brilliance in zirconia gems, rivaling the appearance of natural stones. Stuller, a leading jewelry manufacturer and supplier, has expanded its offerings of lab-created zirconia stones with enhanced optical clarity and customized coloration, catering to diverse market trends and consumer preferences.
Looking ahead, the industry is poised for continued advancements in precision fabrication, with a focus on sustainability and scalability. Automated quality control systems, including AI-driven visual inspection, are expected to be more widely deployed to ensure flawless zirconia pieces at industrial scale. As consumer demand for ethically sourced and innovative jewelry rises, zirconia-based technologies are likely to play an increasingly central role in defining quality, design, and production efficiency in the sector through the next several years.
Major Players and Official Industry Initiatives
The landscape of zirconia-based high-precision industrial jewelry fabrication is increasingly defined by the involvement of established materials manufacturers, specialized technology providers, and vertically integrated jewelry brands. As of 2025, several major players are leading innovation, production scale-up, and the development of standards in this specialized sector.
One prominent company is Tosoh Corporation, a global leader in advanced ceramics, whose zirconia powders and technical ceramics are widely used in precision applications, including jewelry manufacturing. Their consistent material quality and ongoing research into fine-grained yttria-stabilized zirconia have facilitated more intricate and durable jewelry designs.
On the industrial fabrication technology front, 3D Systems has expanded its portfolio to include high-resolution additive manufacturing solutions tailored for ceramics, including zirconia. The company’s direct collaboration with material suppliers and jewelry producers has accelerated the adoption of digital workflows for the creation of complex zirconia-based jewelry pieces, emphasizing both precision and scalability.
In Europe, CeramTec stands out as a major supplier of technical ceramics for precision applications. Their expertise in shaping, sintering, and finishing zirconia components has enabled partnerships with luxury jewelry brands seeking high wear resistance, biocompatibility, and brilliant aesthetics in their product lines.
Among jewelry brands, Bulgari has been notable for its investment in advanced ceramic jewelry collections, leveraging high-purity zirconia for both structural and decorative functions. Their collaboration with ceramics manufacturers and adoption of precision processes are influencing broader industry adoption, especially for high-value and limited-edition pieces.
Industry-wide initiatives are also emerging. The American Ceramic Society has, as of 2025, established working groups focused on standardizing zirconia ceramics for jewelry, aiming to harmonize material properties, testing protocols, and labeling to support both manufacturers and consumers. Such standardization is expected to enhance market transparency and foster further innovation.
Looking ahead, these collaborations between materials suppliers, technological innovators, and luxury brands, coupled with formalized industry standards, are expected to drive further growth and diversification in zirconia-based high-precision jewelry fabrication over the next several years.
2025 Market Size, Growth Drivers, and Forecasts to 2030
The global market for zirconia-based high-precision industrial jewelry fabrication is expected to experience robust growth in 2025, with a positive outlook through 2030. Zirconia, particularly cubic zirconia (CZ), has established itself as a leading synthetic gemstone in the jewelry industry due to its superior hardness, optical clarity, and cost-effectiveness compared to natural diamonds. As of 2025, leading manufacturers report sustained demand from both fashion and fine jewelry sectors, driven by evolving consumer preferences and advancements in manufacturing technologies.
Key growth drivers include the increasing adoption of computer-aided design (CAD) and advanced manufacturing techniques such as CNC milling and laser cutting, which enable the production of intricate, high-precision zirconia jewelry components. Ganoksin Project highlights the pivotal role of CAD/CAM systems in transforming gemstone setting and metalworking processes, allowing for greater customization and repeatability in high-volume production. Leading zirconia producers such as Element Six and Helios Gem continue to invest in R&D to enhance material purity, color consistency, and resistance to abrasion, further strengthening the appeal of zirconia-based jewelry.
The market’s expansion is also underpinned by growing consumer awareness of sustainable and ethical sourcing. Synthetic zirconia offers an attractive alternative to mined gemstones, aligning with the corporate social responsibility objectives of major brands. According to Swatch Group, the use of advanced ceramics, including zirconia, in watchmaking and jewelry not only supports sustainability goals but also introduces new aesthetic and functional possibilities.
Regionally, the Asia-Pacific market—driven by China and India—continues to dominate zirconia jewelry production, supported by a well-established supply chain and skilled labor force. Gemesis and other gemstone manufacturers in the region are expanding their capacity to meet global demand, leveraging both traditional craftsmanship and state-of-the-art machinery.
Looking ahead to 2030, the market trajectory is expected to remain positive, with annual growth rates projected in the high single digits. Innovations in material science, such as the development of nanostructured zirconia and hybrid composites, are poised to unlock new applications in luxury and technical jewelry. Strategic partnerships between zirconia producers, jewelry houses, and technology providers are anticipated to further accelerate market penetration and product diversification, ensuring that zirconia-based high-precision industrial jewelry fabrication remains at the forefront of the industry’s evolution.
Applications: From Luxury to Industrial Jewelry
In 2025, zirconia-based materials are asserting a prominent role in the transformation of high-precision industrial jewelry fabrication, bridging luxury aesthetics with advanced manufacturing for both premium and functional jewelry segments. Zirconia, especially cubic zirconia (CZ) and yttria-stabilized zirconia (YSZ), is renowned for its diamond-like brilliance, exceptional hardness, and chemical stability, making it a preferred choice for modern jewelry applications beyond mere ornamentation.
The integration of computer-aided design (CAD) and computer-aided manufacturing (CAM) into jewelry production lines has enabled unprecedented precision in shaping and setting zirconia stones. Leading technology providers such as SISMA and 3D Systems are supplying industrial-grade 3D printing and laser micro-welding systems that are compatible with zirconia and its composites, supporting intricate custom designs and rapid prototyping for both high-end and industrial jewelry applications.
On the materials front, companies like Tosoh Corporation are expanding their supply of advanced zirconia powders and ceramics, ensuring consistent quality and scalability for jewelry manufacturers. These developments are pivotal for the rising trend of integrating zirconia components in “smart jewelry,” where electronic functionality (such as sensors or RFID chips) is embedded into luxury items requiring robust, non-conductive, biocompatible housings.
Sustainability and ethical sourcing continue to drive zirconia’s appeal over natural gemstones. Manufacturers such as Stuller, Inc. highlight their use of lab-created zirconia stones, which eliminate the environmental and social concerns associated with traditional mining, while meeting the increasing demand for traceability and responsible sourcing in the jewelry industry.
Looking ahead, industry forecasts indicate that the adoption of zirconia-based fabrication will accelerate over the next few years, fueled by further advancements in additive manufacturing, increased customization, and the convergence of decorative and functional jewelry. As digital manufacturing and advanced ceramics continue to evolve, zirconia is expected to play a central role in both luxury and industrial jewelry markets, offering designers and engineers new possibilities in precision, durability, and sustainable innovation.
Supply Chain, Sourcing, and Sustainability Initiatives
The supply chain for zirconia-based high-precision industrial jewelry fabrication is undergoing significant transformation in 2025, driven by a combination of technological advancements, shifting sourcing strategies, and the increasing emphasis on sustainability. Zirconia, especially in its stabilized cubic zirconia form, has become a principal material for high-precision jewelry due to its hardness, optical properties, and versatility. Sourcing high-quality zirconia relies on established mineral suppliers and advanced material manufacturers, who are now under growing pressure to ensure responsible extraction and processing. Companies such as Tosoh Corporation and 3M are recognized for their production of stabilized zirconia powders and ceramics that serve as the foundation for precision-cut stones and components in the jewelry industry.
In recent years, there has been a concerted industry effort to verify the origin of raw materials and minimize environmental impact through certifications and transparent supply chain tracking. For instance, manufacturers like Swarovski have increasingly emphasized traceability protocols and environmentally conscious sourcing, pledging to reduce their carbon footprint and integrate recycled materials wherever feasible. This includes investments in closed-loop manufacturing systems for zirconia, energy-efficient kilns, and water recycling technology at production sites.
Supply chain resilience is a key focus in 2025, with companies diversifying their supplier base to mitigate risks related to geopolitical instability or resource scarcity. The COVID-19 pandemic underscored vulnerabilities in global logistics, prompting major zirconia users and jewelry houses to form closer partnerships with local and regional zirconia processors. Organizations such as the World Jewellery Confederation (CIBJO) continue to update industry guidance on responsible sourcing and environmental stewardship, encouraging members to adopt best practices in material traceability, labor standards, and waste reduction.
Looking ahead, the integration of digital platforms for supply chain monitoring is expected to expand, allowing real-time tracking of zirconia from mine to finished jewelry. Sustainability remains central, with a growing number of brands committing to third-party environmental certifications and reporting frameworks. Initiatives such as the Responsible Jewellery Council certification are increasingly sought after as a mark of supply chain integrity and eco-ethical sourcing. As regulatory frameworks tighten and consumer demand for responsible luxury intensifies, the zirconia-based jewelry sector is poised to prioritize not only the precision and quality of its products, but also the transparency and sustainability of its entire value chain in the years ahead.
Competitive Landscape and Key Strategic Moves
The competitive landscape in zirconia-based high-precision industrial jewelry fabrication is characterized by a confluence of advanced ceramic manufacturers, established jewelry houses, and precision technology integrators. As of 2025, leading players are leveraging proprietary zirconia processing techniques to deliver superior aesthetics and mechanical performance, responding to increasing demand for hypoallergenic and durable luxury jewelry.
Notably, Tosoh Corporation, a global leader in advanced ceramics, continues to strengthen its presence in the jewelry sector by supplying high-purity yttria-stabilized zirconia (YSZ) powders optimized for laser and CNC micro-machining. Their collaborations with specialized jewelry fabricators are driving innovations in translucency and color stability, essential for mimicking natural gemstones in fine jewelry settings.
On the manufacturing front, CeramTec GmbH and KYOCERA Corporation have made strategic investments in digital fabrication technologies, including multi-axis CNC milling and additive manufacturing, to offer custom zirconia components with micron-level tolerances. These advancements enable the production of intricate jewelry elements—such as pavé-set bezels and complex lattice motifs—with consistency previously unattainable in ceramic materials.
In terms of strategic alliances, leading European jewelry brands have begun forging direct supply agreements with zirconia specialists to secure access to colored and ultra-high purity formulations. For example, Pandora A/S has introduced new zirconia-based collections, emphasizing the stone’s environmental credentials and longevity, aligning with consumer preferences for sustainable luxury.
Supplier innovation is further evidenced by Zircomet Limited, which has focused R&D on improving the sintering process to yield zirconia with enhanced fracture toughness and minimal porosity, directly addressing the market’s need for both durability and intricate, lightweight designs.
Looking ahead, the competitive landscape is expected to intensify as additional luxury and tech-forward brands enter the zirconia jewelry space. The ongoing refinement of CAD/CAM integration and surface finishing techniques is anticipated to lower production costs and expand design possibilities. Moreover, strategic moves such as vertical integration—where jewelry houses acquire or partner with zirconia material producers—are likely to shape the sector’s trajectory through 2026 and beyond, ensuring stability in supply chains and enabling rapid response to evolving fashion and engineering trends.
Challenges, Regulatory Considerations, and Risk Factors
Zirconia-based high-precision industrial jewelry fabrication faces a range of challenges, regulatory considerations, and risk factors as the sector evolves in 2025 and beyond. One of the principal challenges is the technical complexity associated with the processing and machining of zirconia ceramics. Although zirconia offers exceptional hardness and wear resistance, these very properties make it difficult to shape and finish, necessitating advanced CNC equipment, laser sintering, and specialized diamond tooling. Such requirements elevate capital costs and can lead to increased production times, especially during prototyping and small-batch manufacturing. For instance, 3M emphasizes the need for precision tools and abrasive technologies when working with zirconia-based jewelry, underlining the sector’s dependency on continuous technological investment.
Regulatory frameworks for zirconia jewelry are also in flux. Zirconia is generally recognized as biocompatible, making it suitable for skin-contact applications. However, as more advanced processing additives and surface treatments are introduced to enhance luster or color, manufacturers must navigate evolving guidelines related to chemical safety and trace elements. The European REACH regulation and U.S. Consumer Product Safety Commission (CPSC) standards on heavy metals and allergenic substances remain central. Leading suppliers, such as Tosoh Corporation, actively monitor compliance with these standards in their product documentation, which is crucial for downstream jewelry manufacturers aiming for international market access.
Another risk factor in 2025 is the growing scrutiny over supply chain transparency and the provenance of raw materials. The traceability of zirconia powders—often originating from a handful of global producers—requires robust documentation to assure both quality and ethical sourcing. Disruptions in the supply chain, whether from geopolitical instability or environmental regulations affecting mining and refining, can impact production timelines and costs. Companies like Kyocera Corporation highlight their integrated supply chains and traceability protocols as risk mitigation strategies.
An additional consideration is market risk: as high-precision zirconia jewelry grows in popularity, there is potential for market saturation, price competition, and the entry of counterfeit products. This risk underscores the importance of certification, branding, and continuous innovation—such as the development of proprietary zirconia blends or hybrid materials—to maintain differentiation and consumer trust. Looking ahead, the sector’s resilience will depend on its ability to balance regulatory compliance, technical advancement, and sustainable, transparent sourcing practices.
Future Outlook: Trends, Opportunities, and What’s Next
Looking ahead to 2025 and beyond, zirconia-based high-precision industrial jewelry fabrication is poised for significant advances, driven by converging trends in materials science, digital manufacturing, and consumer preferences. The combination of zirconia’s exceptional properties—such as high hardness, chemical stability, and diamond-like appearance—with advanced fabrication methods positions it as a material of choice for both luxury and mass-market jewelry segments.
One major trend is the integration of digital design and additive manufacturing technologies. Leading providers of jewelry manufacturing equipment, such as 3D Systems, are expanding their portfolio to include systems compatible with ceramic and zirconia-based materials, enabling unparalleled design freedom, complex geometries, and precise customization. This digital approach not only improves production efficiency but also aligns with the growing demand for personalized and bespoke jewelry pieces.
Zirconia’s biocompatibility and hypoallergenic nature are also gaining prominence, especially as consumers become more aware of skin sensitivities and ethical considerations. Companies like Ceralink are exploring innovative sintering and finishing techniques to produce zirconia jewelry with enhanced surface quality and durability, minimizing the risk of irritation and ensuring long-term wearability.
Sustainability is another driving factor shaping the future of zirconia jewelry fabrication. Unlike traditional gemstone mining, zirconia can be synthesized with lower environmental impact and consistent quality. Industry initiatives, such as those by Element Six, are focusing on responsible sourcing and greener production processes for advanced ceramics, including zirconia, responding to both regulatory pressures and consumer expectations for sustainable luxury.
Market data from sector leaders suggest rising adoption rates of zirconia-based jewelry, especially in regions where affordability and ethical sourcing are prioritized. For example, The Swatch Group has expanded its use of zirconia ceramics in watch cases and accessories, citing their superior scratch resistance and visual appeal as key differentiators.
Over the next few years, continued R&D investment is expected to further enhance the color range, translucency, and mechanical properties of zirconia, broadening its application scope. Strategic collaborations between jewelry brands and advanced ceramics manufacturers are likely to accelerate, fostering innovation in both design and manufacturing. As a result, zirconia-based high-precision jewelry is set to capture an increasingly significant share of the global market, balancing aesthetics, performance, and sustainability.