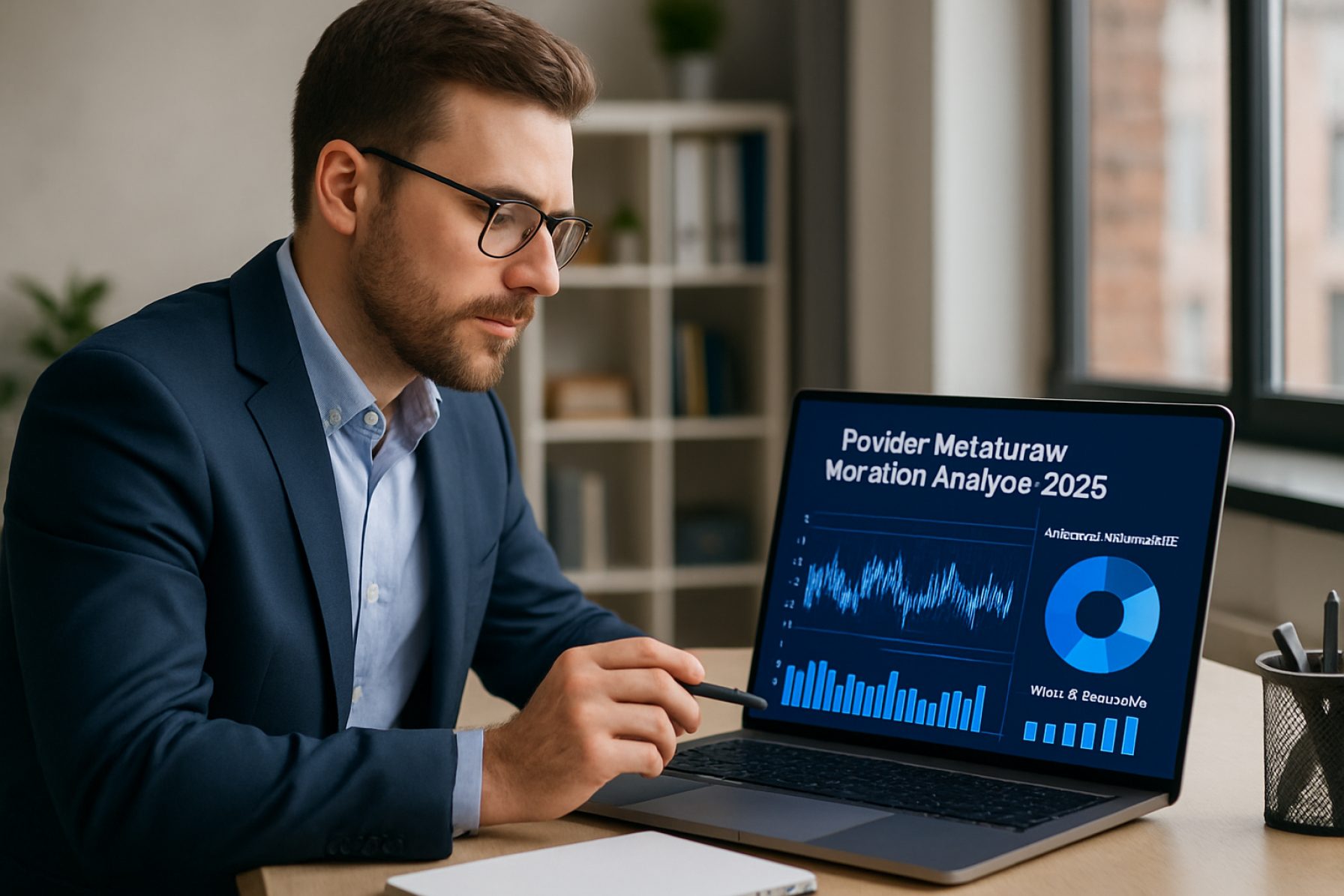
Table of Contents
- Executive Summary: Key Insights for 2025–2030
- Powder Metallurgy Vibration Analysis: Technology Overview
- Global Market Size & Growth Forecasts (2025–2030)
- Emerging Innovations: Sensors, AI, and Real-Time Monitoring
- Leading Industry Players & Strategic Partnerships
- Critical Applications: Automotive, Aerospace, and Beyond
- Regulatory Trends & Industry Standards
- Competitive Landscape & Market Share Analysis
- Challenges, Risks, and Future Opportunities
- Outlook: What’s Next for Powder Metallurgy Vibration Analysis?
- Sources & References
Executive Summary: Key Insights for 2025–2030
Powder metallurgy (PM) continues to gain traction across automotive, aerospace, and industrial sectors, with vibration analysis emerging as a critical tool for quality assurance and predictive maintenance. As of 2025, leading manufacturers are integrating advanced vibration analysis to monitor pressing, sintering, and finishing stages, ensuring component integrity and reducing downtime. This approach addresses the increasing demand for high-performance, lightweight materials and precision-engineered parts, particularly in electric mobility and renewable energy applications.
Recent advancements show that real-time vibration monitoring systems are being embedded into powder compaction presses and sintering furnaces. For example, GKN Powder Metallurgy has implemented smart manufacturing solutions that include vibration diagnostics to enhance process stability and minimize defect rates. Similarly, Höganäs AB is investing in digitalization, leveraging in-line sensors to detect anomalies that could affect density uniformity and mechanical properties of PM parts.
Industry data from 2024–2025 reveals a marked reduction in unplanned maintenance events—by up to 30%—in plants that have adopted vibration-based condition monitoring. Sinteris reports improvements in both equipment lifespan and yield quality, attributing these gains to the early detection of misalignment, wear, and process deviations through vibration analytics. Furthermore, suppliers like AMES Group are collaborating with sensor manufacturers to tailor vibration monitoring for diverse PM equipment, from compactors to sintering ovens.
Looking ahead to 2030, the integration of artificial intelligence with vibration analysis is poised to further revolutionize PM production. Predictive analytics will enable fully automated, self-correcting processes, minimizing human intervention and maximizing throughput. Industry consortia, such as the Metal Powder Industries Federation, are actively developing standards for vibration-based quality control, fostering wider adoption and interoperability.
In summary, the next five years will see vibration analysis become indispensable in powder metallurgy, underpinning efforts to meet stringent quality, sustainability, and efficiency goals. Companies that embrace these technologies are projected to achieve a competitive edge through reduced costs, higher product reliability, and faster adaptation to evolving market requirements.
Powder Metallurgy Vibration Analysis: Technology Overview
Powder metallurgy (PM) vibration analysis represents a niche yet increasingly vital area in the optimization of powder-based manufacturing processes. As the industry moves toward higher component complexity, tighter tolerances, and greater demand for quality assurance, vibration analysis technologies are gaining traction in both process monitoring and equipment maintenance. In 2025, the landscape is shaped by advanced sensor integration, real-time data analytics, and the emergence of predictive maintenance protocols tailored to PM production lines.
Modern PM presses and compaction equipment are now frequently equipped with vibration sensors and accelerometers. These devices, often integrated directly into the press frames or tooling, enable continuous monitoring of dynamic behavior during the compaction cycle. For example, GKN Powder Metallurgy has highlighted the use of vibration analysis to detect anomalies such as misalignment, uneven powder distribution, or tooling wear, which can significantly affect part quality and machine longevity. Real-time vibration data helps maintenance teams address issues proactively, reducing unplanned downtime and scrap rates.
A noteworthy trend in 2025 is the application of machine learning algorithms to vibration datasets. Companies like A. Alfing Maschinenfabrik are leveraging artificial intelligence to distinguish between normal process variations and early signs of mechanical failure. This approach is particularly important in high-volume automotive and aerospace PM production, where even minor deviations can propagate into costly defects. Additionally, advancements in wireless sensor networks allow for scalable implementation across multiple machines in a facility, enhancing overall process transparency.
Industry bodies such as Metal Powder Industries Federation (MPIF) and European Powder Metallurgy Association (EPMA) are actively disseminating best practices and technical guidelines for vibration monitoring specific to powder metallurgy applications. Their publications and technical sessions emphasize the critical role of vibration analysis in achieving Industry 4.0 readiness—enabling data-driven decision-making and integrated manufacturing intelligence.
Looking forward to the next few years, the outlook for vibration analysis in PM is strongly positive. As sustainability requirements and efficiency targets become more stringent, manufacturers are expected to invest further in smart monitoring systems. Integration with digital twins and cloud-based analytics platforms is anticipated, allowing real-time feedback loops for process optimization. Collaborative initiatives between equipment manufacturers, sensor suppliers, and powder producers will likely accelerate the adoption of standardized vibration analysis protocols, further cementing its role in the evolution of powder metallurgy manufacturing.
Global Market Size & Growth Forecasts (2025–2030)
The global market for powder metallurgy (PM) vibration analysis is poised for significant growth between 2025 and 2030, driven by the increasing adoption of advanced diagnostic and quality assurance solutions in the PM sector. As manufacturers prioritize precision and reliability in components produced via powder metallurgy, the demand for sophisticated vibration analysis systems is accelerating. This trend is particularly prominent in the automotive, aerospace, and industrial machinery segments, where PM components are subject to stringent performance and durability standards.
Current industry data suggest that the integration of vibration analysis methods with PM processes is expanding, supported by investments in automation, digitalization, and predictive maintenance. Leading PM equipment suppliers such as GKN Powder Metallurgy and Höganäs AB are increasingly incorporating advanced monitoring and analytics capabilities to enhance product quality and process efficiency. These companies are focusing on developing sensors and software platforms that allow for real-time vibration monitoring during compaction, sintering, and post-processing stages, ensuring early detection of anomalies and minimizing production downtime.
In 2025, the market size for vibration analysis solutions specifically tailored for powder metallurgy operations is estimated to reach several hundred million USD, with a projected compound annual growth rate (CAGR) in the high single to low double digits through 2030. This growth is bolstered by the adoption of Industry 4.0 principles and the expansion of digital twins and predictive maintenance frameworks, as evidenced by initiatives from organizations like the Metal Powder Industries Federation (MPIF), which actively promotes the integration of smart manufacturing technologies across the PM value chain.
Regionally, Asia-Pacific is expected to lead market expansion, fueled by robust automotive and electronics manufacturing bases in China, Japan, South Korea, and India. North America and Europe follow closely, as established PM component producers in these regions invest in upgrading legacy systems with high-precision vibration analysis for process optimization and compliance with increasingly stringent quality standards. Companies such as Sinteris are actively exploring collaborations with sensor and automation firms to accelerate the deployment of vibration monitoring solutions in their manufacturing environments.
Looking ahead, the outlook for the powder metallurgy vibration analysis market remains optimistic as the sector embraces data-driven manufacturing. The convergence of PM and advanced vibration diagnostics is set to play a crucial role in achieving higher yield, improved safety, and reduced operational costs by 2030.
Emerging Innovations: Sensors, AI, and Real-Time Monitoring
In 2025, powder metallurgy (PM) manufacturers are rapidly adopting advanced technologies for vibration analysis, notably integrating smart sensors, artificial intelligence (AI), and real-time monitoring to optimize quality and efficiency. Vibration analysis is critical in PM due to the need to monitor machinery for early detection of faults, ensuring consistent material properties and reducing downtime during pressing and sintering processes.
A key innovation is the deployment of wireless and embedded sensor systems designed for harsh PM environments. These sensors continuously capture high-resolution vibration data from compaction presses, mixers, and sintering furnaces. Companies such as Schaeffler and Sandvik have developed robust sensor platforms capable of monitoring machine health in real time, supporting predictive maintenance and minimizing unscheduled stoppages.
AI-driven analysis is another transformative trend. Machine learning algorithms are being applied to vibration datasets to identify subtle patterns associated with tool wear, material inconsistencies, or misalignments. For example, Bosch Rexroth has enhanced its IoT-enabled machinery with AI modules that alert operators to anomalies well before conventional threshold-based systems would. This approach not only reduces variability in PM parts but also extends equipment life and lowers maintenance costs.
Beyond machine health, real-time vibration monitoring is enabling process optimization. Live dashboards, such as those developed by Siemens, provide operators with actionable insights during critical PM steps—such as compaction—where vibration signatures directly correlate with powder flow and density distribution. Real-time adjustments informed by sensor data are improving part uniformity and reducing defect rates.
Outlook for the coming years is promising. Industry alliances and open standards, championed by organizations like European Powder Metallurgy Association (EPMA), are expected to accelerate the adoption of interoperable sensor and analytics solutions across the PM value chain. With the continuous decline in sensor costs and advancements in edge computing, even small- and medium-sized PM producers will be able to deploy sophisticated vibration analysis systems by 2027. This convergence of sensors, AI, and real-time monitoring is set to usher in a new era of reliability, traceability, and efficiency for powder metallurgy production worldwide.
Leading Industry Players & Strategic Partnerships
In 2025, the powder metallurgy (PM) sector continues to witness increased attention toward vibration analysis, reflecting the industry’s focus on quality control and equipment reliability. Vibration analysis is deemed critical for assessing the health of sintering furnaces, compaction presses, and other specialized machinery used in powder metallurgy processes. Several leading industry players are integrating advanced vibration monitoring solutions as part of their digitalization and predictive maintenance strategies.
Key powder metallurgy equipment manufacturers, such as GKN Powder Metallurgy and Höganäs AB, have invested in digital transformation initiatives that include the deployment of smart sensors and condition monitoring systems. These systems are designed to capture and analyze vibration signatures, enabling early detection of mechanical faults, misalignments, or wear in production lines. Such capabilities are vital for reducing downtime, minimizing scrap, and optimizing process control.
Strategic partnerships are shaping the competitive landscape. For example, Höganäs AB has collaborated with automation and sensor technology firms to co-develop predictive maintenance platforms tailored for PM applications. Their partnerships focus on integrating vibration analysis with real-time data analytics, contributing to more precise process monitoring and extended equipment lifespans. Similarly, Sandvik—with its established PM division—has worked closely with industrial automation providers to embed vibration analysis capabilities into its powder processing equipment, emphasizing the role of digital twin technology and remote diagnostics.
Automation and control specialists are also playing a pivotal role. Siemens and ABB supply advanced vibration monitoring solutions and software that are increasingly adopted by PM producers for both new installations and retrofits. These technologies are often offered as part of broader Industry 4.0 initiatives, with cloud-based data aggregation and machine learning-based anomaly detection.
Looking ahead, industry players are expected to deepen collaborations with sensor manufacturers and software developers to refine vibration analysis for complex PM operations, including additive manufacturing. The goal is to achieve real-time, in-line process optimization and to further reduce unplanned maintenance events. As a result, the integration of vibration analysis into powder metallurgy is anticipated to become a standard practice, supported by ongoing alliances and co-innovation among equipment OEMs, automation leaders, and digital solution providers through 2025 and beyond.
Critical Applications: Automotive, Aerospace, and Beyond
Powder metallurgy (PM) components are increasingly deployed in sectors where vibration performance is crucial, notably automotive and aerospace. In 2025, this trend is accelerating as manufacturers seek lighter, high-performance parts with predictable damping and fatigue resistance, driving innovation in vibration analysis methods specific to PM materials.
In the automotive sector, vibration analysis of PM gears, structural supports, and engine components is vital to meet stringent NVH (Noise, Vibration, and Harshness) standards. For instance, GKN Powder Metallurgy reports ongoing development of PM-based transmission and drivetrain parts, emphasizing the role of vibration analysis in optimizing porosity, grain structure, and material blends for maximum damping and durability. The integration of sensor-equipped test benches and AI-driven simulation software in 2025 allows for in-situ vibration measurement during prototype testing, directly correlating PM microstructures with dynamic load responses. This data-centric approach supports rapid optimization cycles and faster deployment of PM components in new vehicle models, particularly electric vehicles where vibration control is essential for passenger comfort.
In aerospace, the adoption of powder metallurgy for lightweight, complex components—such as brackets, turbine parts, and housings—is expanding. Vibration analysis is central for qualifying these parts against fatigue and resonance risks in harsh environments. Höganäs AB, a leading PM supplier, collaborates with aerospace OEMs to refine powder blends and compaction techniques, using advanced vibration testing (modal analysis, fatigue life prediction) to ensure reliability under cyclic loads. The rapid growth of additive manufacturing (AM) with PM feedstocks in aerospace further intensifies the need for precise vibration characterization, as AM parts often exhibit unique internal geometries and anisotropies affecting dynamic response.
Beyond automotive and aerospace, PM vibration analysis is finding relevance in robotics, industrial automation, and energy applications. For example, Sandvik offers PM solutions tailored for vibration-critical environments, such as electric motor housings and high-speed rotating machinery, leveraging vibration analysis to meet operational safety and lifespan requirements.
Looking ahead, the outlook for PM vibration analysis is robust. Industry initiatives aim to standardize test protocols and digital twins for PM parts, integrating real-world vibration data into design software. Companies like GKN Powder Metallurgy and Höganäs AB are expected to expand their efforts in AI-enhanced predictive modeling, while new sensor technologies promise finer-grain insights into in-service vibration behavior. These advances will support broader adoption of PM components in critical, vibration-sensitive applications through the next several years.
Regulatory Trends & Industry Standards
The regulatory landscape and industry standards for vibration analysis in powder metallurgy (PM) have been evolving rapidly, reflecting the increasing adoption of advanced quality control and predictive maintenance practices. In 2025, attention to vibration analysis has intensified as manufacturers strive for higher precision, reliability, and safety in PM processes, particularly in automotive, aerospace, and medical component production. Regulatory authorities and standardization bodies are emphasizing robust monitoring of mechanical systems, including presses, mixers, and sintering equipment, to mitigate risks associated with equipment wear, misalignment, and product inconsistency.
The ASTM International continues to play a leading role by updating standards such as ASTM E2984, which outlines methods for vibration monitoring of powder processing equipment. These updates integrate new sensor technologies and digital analytics, encouraging manufacturers to adopt real-time vibration diagnostics. The International Organization for Standardization (ISO) is also active, with ISO 10816 and ISO 20816 series being referenced more frequently in PM plants for machinery vibration measurement and evaluation. These standards are being revised to align with the proliferation of Industry 4.0 solutions, enabling more precise data collection and remote condition monitoring.
In 2025, regulatory agencies in Europe and North America, including the Occupational Safety and Health Administration (OSHA) and the European Agency for Safety and Health at Work, are increasingly advocating for mandatory vibration monitoring in PM facilities to reduce risks of mechanical failure and worker exposure to harmful vibrations. Enforcement of these guidelines is expected to intensify, especially as more facilities pursue certifications such as ISO 45001 (occupational health and safety management) and IATF 16949 (automotive sector quality management), both of which now often require traceable machine condition data, including vibration trends.
Industry groups such as the Metal Powder Industries Federation (MPIF) and the European Powder Metallurgy Association (EPMA) are collaborating with equipment manufacturers to harmonize guidelines for vibration analysis, aiming to reduce downtime and improve product consistency. These bodies are also piloting best-practice frameworks for integrating vibration monitoring with AI-based predictive maintenance systems. Leading PM equipment suppliers, including GKN Powder Metallurgy and Höganäs AB, are embedding advanced vibration sensors and analytics into their machinery, encouraging their widespread adoption as a de facto industry standard.
Looking ahead, the next few years are likely to witness further tightening of regulatory requirements for vibration analysis in PM, especially as digital twin and IIoT technologies become standard in process monitoring. The convergence of stricter regulations, updated standards, and digital transformation is set to drive continuous improvements in safety, quality, and operational efficiency across the powder metallurgy sector.
Competitive Landscape & Market Share Analysis
The competitive landscape of the powder metallurgy vibration analysis market in 2025 is shaped by a dynamic interplay between established solution providers, emerging technology innovators, and end-user industries such as automotive, aerospace, and precision tooling. As powder metallurgy (PM) components become increasingly complex and integral to high-performance applications, the demand for advanced vibration analysis tools—critical for quality assurance and predictive maintenance—continues to grow.
Major players in the vibration analysis segment include instrument manufacturers and automation specialists that have tailored their offerings to the specific requirements of PM processes. For instance, Schenck RoTec has expanded its portfolio of balancing and vibration analysis systems, emphasizing solutions that integrate seamlessly with powder metallurgy production lines for real-time monitoring. Similarly, Brüel & Kjær offers advanced vibration and acoustic measurement systems, with recent developments focusing on automated, AI-driven diagnostics to address the precision needs of sintered and additively manufactured components.
From a market share perspective, European and Japanese companies continue to hold leading positions due to their long-standing expertise in both PM and industrial metrology. Companies such as KOMAGE Gellner Maschinenfabrik and Sintokogio, Ltd. have introduced integrated process monitoring and vibration analysis modules within their powder compaction and sintering equipment, driving further vertical integration.
North America remains a strong market, especially as automotive OEMs and Tier 1 suppliers invest in digital transformation and smart manufacturing. GE Digital and ABB are notable for providing industrial IoT platforms that enable data-driven vibration analysis, supporting condition-based monitoring of PM machinery. These platforms are increasingly being adopted by PM part manufacturers to reduce downtime and ensure product consistency.
The competitive outlook for the next few years suggests intensifying collaboration between PM machinery manufacturers and digital analytics firms to develop bespoke vibration analysis solutions. Partnerships are expected to accelerate, especially as standards for predictive maintenance in PM lines are formalized and as end-users demand more plug-and-play systems. Additionally, the integration of cloud-based analytics and machine learning algorithms will further differentiate market leaders as they offer actionable insights for process optimization and defect prevention.
Overall, the sector is poised for moderate growth, with key players leveraging proprietary technologies, strategic collaborations, and end-to-end service offerings to capture greater market share in the evolving landscape of powder metallurgy vibration analysis.
Challenges, Risks, and Future Opportunities
The field of powder metallurgy (PM) vibration analysis is experiencing both significant challenges and emerging opportunities as we enter 2025 and look ahead. A primary concern remains the inherent sensitivity of PM components to vibration-induced stresses, which can lead to microcracking or premature fatigue failure, especially in high-performance automotive and aerospace applications. The complexity of sintered materials—often featuring variable porosity and anisotropic grain structures—further complicates predictive vibration analysis, requiring advanced modeling and real-time monitoring solutions.
One notable challenge is the integration of digital twins and sensor technologies for in-situ vibration monitoring. Although companies like GE and Sandvik are developing advanced sensor and analytics platforms, the adaptation of these systems to the unique properties of PM components—such as their damping characteristics and surface roughness—remains an active area of research. The lack of standardized testing protocols for vibration analysis in PM parts introduces additional variability and uncertainty across manufacturers, impacting the reliability of comparative data.
Risks are also associated with the acceleration of electrification trends in transportation and industrial equipment. Electric motors subject PM gears and structural components to distinct vibration spectra compared to internal combustion systems, exposing gaps in current material qualification processes. As manufacturers such as GKN Powder Metallurgy and Höganäs expand their PM offerings for electric vehicles, there is a pressing need to refine vibration analysis methodologies to account for new operational profiles and regulatory demands.
Nevertheless, several promising opportunities are emerging. The integration of machine learning and artificial intelligence with vibration analysis tools holds the potential to greatly enhance defect detection and predict component lifespan, leveraging large datasets collected from operational environments. Furthermore, the advent of additive manufacturing in PM—pioneered by organizations such as Sandvik—enables the design of parts with optimized vibration damping features that were previously unattainable via conventional pressing and sintering.
Looking forward, industry-wide collaboration is anticipated to address the lack of harmonized standards. Initiatives led by bodies like the Metal Powder Industries Federation aim to establish more rigorous vibration testing guidelines specific to powder metallurgy. Over the next few years, as digitalization and electrification reshape manufacturing, the ability to accurately analyze and mitigate vibration risks in PM components will be a key differentiator for suppliers and OEMs investing in advanced monitoring and simulation capabilities.
Outlook: What’s Next for Powder Metallurgy Vibration Analysis?
The outlook for powder metallurgy (PM) vibration analysis in 2025 and the coming years is shaped by rapid digitalization, increasing automation, and a growing emphasis on process optimization and quality assurance. As manufacturers seek to unlock higher productivity and minimize material waste, advanced vibration analysis is becoming a cornerstone for monitoring and improving PM processes.
A key trend is the integration of Industry 4.0 technologies, such as real-time sensor arrays and machine learning algorithms, into PM production lines. Leading equipment suppliers and powder metallurgy companies are rolling out systems capable of capturing high-frequency vibration data from presses, sintering furnaces, and compaction tools. This data, when analyzed using predictive analytics, can preemptively identify anomalies like tool wear, misalignment, or powder flow inconsistencies, minimizing downtime and preventing costly defects. For example, GKN Powder Metallurgy is investing in smart manufacturing solutions, including vibration monitoring, to enhance process control and reduce variability in critical components.
Automotive and aerospace sectors, major consumers of PM components, are driving demand for tighter tolerances and enhanced reliability. In response, PM manufacturers are implementing vibration analysis not just for machine health monitoring, but also as an in-process quality control tool. Real-time vibration feedback is increasingly used to adjust compaction parameters or stop production if abnormal signatures are detected, ensuring consistent part density and mechanical properties. Companies like Höganäs AB are exploring digital tools to monitor and optimize the entire PM process chain, with vibration data as a critical input for feedback loops.
Looking forward, the development of multi-sensor fusion platforms—combining vibration, acoustic, and thermal data—promises even more robust diagnostics. The adoption of cloud-based analytics platforms by PM equipment suppliers, such as SACMI, is expected to accelerate, enabling remote monitoring and benchmarking across global production sites. Furthermore, the rise of electrification and e-mobility applications is pushing PM producers to demonstrate even higher levels of quality, further strengthening the role of vibration analysis in certification and traceability.
In summary, as powder metallurgy continues to evolve alongside digital manufacturing, vibration analysis will expand from a maintenance tool to a comprehensive process and quality control solution. The next few years are set to see broader adoption of AI-driven diagnostics, more granular sensor networks, and tighter integration of vibration data within the PM value chain, as industry leaders seek to meet rising standards for performance, efficiency, and traceability.
Sources & References
- AMES Group
- Metal Powder Industries Federation
- A. Alfing Maschinenfabrik
- European Powder Metallurgy Association (EPMA)
- Schaeffler
- Sandvik
- Bosch Rexroth
- Siemens
- ASTM International
- International Organization for Standardization (ISO)
- European Agency for Safety and Health at Work
- Schenck RoTec
- Brüel & Kjær
- KOMAGE Gellner Maschinenfabrik
- GE Digital
- SACMI