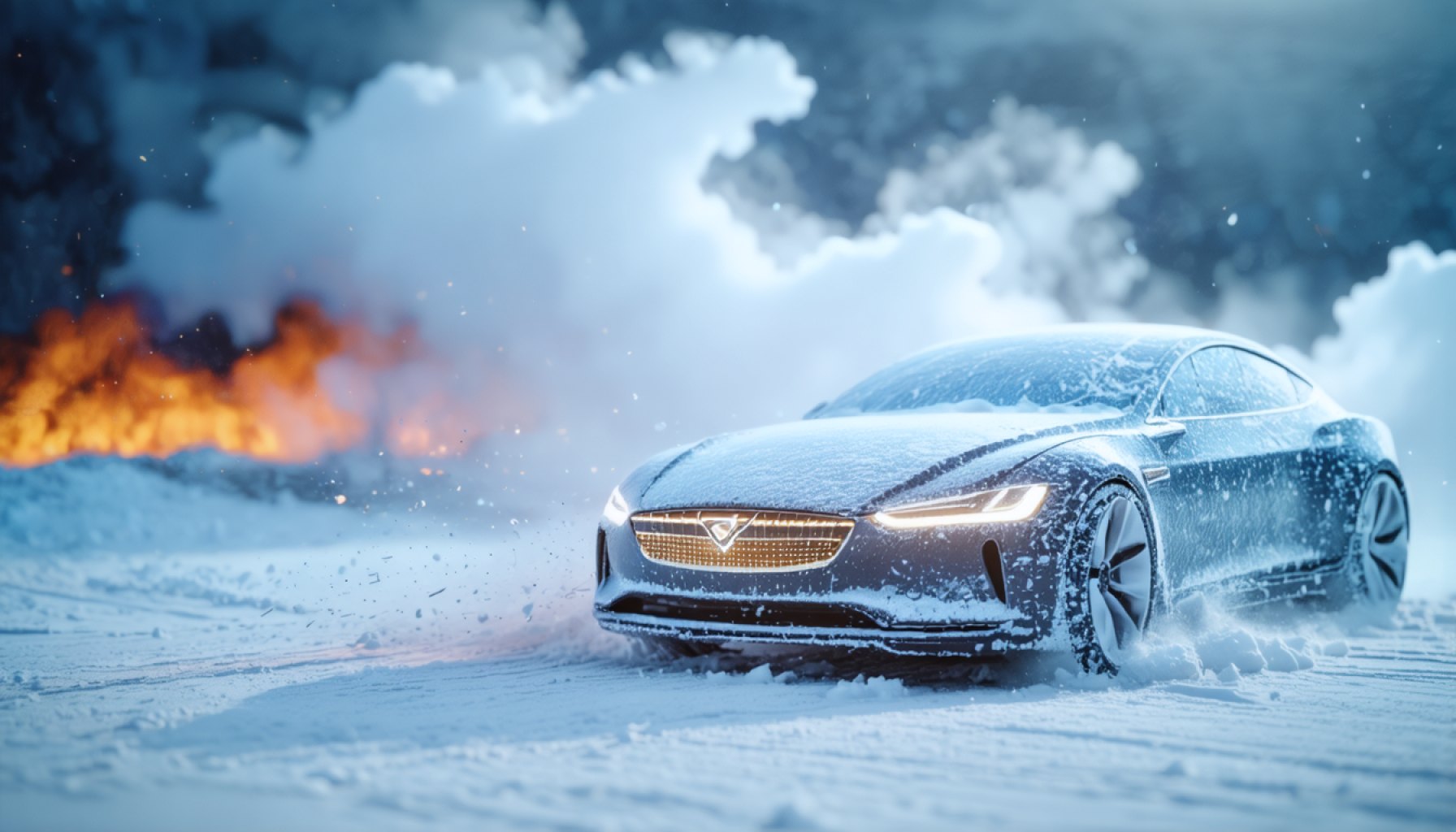
- Thermal interface materials (TIMs) are evolving from simple heat conductors to essential components in electric vehicle (EV) design, emphasizing both efficiency and safety.
- TIMs play a critical role in protecting against localized overheating, mechanical stress, and fire hazards in high-energy EV batteries.
- Modern TIMs function as vibration dampers and structural gap fillers, enhancing battery integration, as seen in technologies like Tesla’s 4680 and BYD’s Blade Battery.
- TIMs infused with flame-retardant materials and phase change properties are pivotal in preventing thermal runaway chain reactions.
- Challenges in producing high-performance TIMs include ensuring thermal conductivity and adaptability to vibrations and temperature shifts.
- Strategic partnerships and innovations, like graphene-infused gels and AI-driven production, are driving advancements in TIM technology.
- TIMs are integral to the future of sustainable mobility, with companies’ success in the EV market hinging on these emerging technologies.
In the ever-evolving landscape of electric vehicles (EVs), a quiet transformation is taking place—one that centers on materials most people rarely contemplate: thermal interface materials (TIMs). Commonly seen as mere conduits for dissipating heat, these innovative compounds are now emerging as linchpins in the design and safety of EVs, pushing beyond traditional constraints and embracing multifaceted roles.
At first glance, TIMs were simple bridges, enhancing conductivity between heat-generating components and heat sinks in electronics. Their duty seemed unremarkable, a mere facilitator in the world of thermal management. Yet, today’s cutting-edge TIMs stand as symbols of ingenuity. They are key players in the burgeoning field of electric vehicular design, harmonizing the need for efficiency with the pursuit of safety.
The surge in the energy density of EV batteries and the norm of fast-charging have introduced challenges—localized overheating and the potential for mechanical stress within tightly packed battery cells. TIMs are stepping up, acting as guardians against these threats. Researchers have started to see these materials not just as thermal bridges but as vital components ensuring safety and durability.
TIMs in modern EVs are more complex than their predecessors. They act as vibration dampers, compensate for structural gaps, and, most critically, form barriers against fire hazards. In designs like Tesla’s 4680 cell architecture or BYD’s Blade Battery, TIMs ensure optimal integration of battery cells with cooling plates, maintaining integrity even under thermal cycling.
Protecting against thermal runaway—where a single faulty cell triggers a cascade of failures—is becoming a top priority. TIMs infused with flame-retardant materials, or employing phase change characteristics, are being refined to halt these destructive chain reactions. Studies reveal ceramic-filled and boron nitride composites delay thermal escalations, showcasing their dual role as both heat absorbers and electrical insulators.
These capabilities underscore a new chapter in battery safety. TIMs, inconspicuous yet effective, form a discreet layer of defense, preserving the integrity and safety of EV battery packs.
Balancing flexibility with efficiency remains a formidable hurdle. EV battery packs require materials that convey high thermal conductivity while weathering continuous vibration and temperature shifts. New-age TIMs like graphene-infused gels and nano-structured composites herald advancements in maintaining performance under stress, foreshadowing a future where both thermal pathways and mechanical resilience coexist.
The path to these innovations isn’t without obstacles. Large-scale production of high-performance TIMs presents complexities such as ensuring filler homogeneity and eliminating air pockets. Automation in battery assembly demands precision that traditional materials often lack, prompting startups to turn to AI and 3D printing for tailored solutions.
Strategic alliances and acquisitions are becoming critical as demand for multifunctional TIMs soars. Industry stalwarts like Henkel and emerging players like Fujipoly are collaborating with battery manufacturers, innovating to meet rigorous safety standards. These partnerships not only drive research and development but also quicken the real-world testing phase, ensuring TIMs can evolve alongside market needs.
The adoption of TIMs mimics the silent revolution of electric mobility itself—subtle but profound. These materials are quietly reshaping the narrative, stepping into roles that blend heat management with structural support and safety measures. They exemplify ingenuity’s power to redefine once-static concepts.
As the world veers towards an electrified future, understanding and harnessing the nuanced capabilities of TIMs may very well determine which companies lead in the sustainable mobility race. Investing in these emerging technologies isn’t just a business choice; it’s a necessary step towards a safer, more efficient electric age.
Unlocking the Secret Components Powering Electric Vehicles: The Role of Thermal Interface Materials
The Evolution and Impact of Thermal Interface Materials in EVs
Electric vehicles (EVs) are shaping the future of mobility with groundbreaking technologies, with one of the less highlighted yet critical aspects being thermal interface materials (TIMs). Once relegated to the background, TIMs are now pivotal to EV design and safety, playing multifaceted roles in the thermal management landscape.
Deep Dive: Advanced Roles of TIMs in Modern EVs
1. Efficiency and Safety in Battery Systems
As EV batteries grow in energy density and fast charging becomes standard, TIMs are evolving beyond traditional thermal conduction roles. They now serve as vibration dampers and fire barriers, key to preventing hazards like thermal runaway—a phenomenon where a malfunctioning cell causes catastrophic chain failures.
Studies emphasize the transformative role of materials like ceramic-filled and boron nitride composites, which offer dual benefits as heat absorbers and electrical insulators, delaying thermal escalations and boosting safety ([source](https://www.chemicals.tn.gov.in)).
2. Overcoming Design Challenges
The push for more efficient EVs demands TIMs that balance thermal conductivity with resilience against vibrations and thermal shifts. Advanced materials such as graphene-infused gels and nano-structured composites offer promising solutions by maintaining performance under stress ([source](https://www.pcmag.com)).
3. Real-World Applications and Innovations
In architectures like Tesla’s 4680 cells and BYD’s Blade Battery, TIMs ensure optimal integration with cooling systems, maintaining the battery’s structural integrity through thermal cycling. Furthermore, innovations such as AI-driven and 3D-printed TIMs are emerging to address production complexities, ensuring filler uniformity and minimizing air pockets.
Strategic Market Movements: Trends and Collaborations
The market for TIMs is vibrant, driven by strategic partnerships and innovations. Major companies like Henkel and newcomers such as Fujipoly are joining forces with battery manufacturers to create highly specialized TIMs, accelerating research and enhancing real-world application testing ([source](https://www.henkel.com)).
Pressing Questions and Insights for Readers
What are the Future Trends in TIMs for EVs?
– Expect increased use of AI and automation in TIM production, improving consistency and performance while reducing costs.
– The market for TIMs is projected to grow substantially, driven by the need for safer and more efficient EV solutions ([source](https://www.idtechex.com)).
How Can Manufacturers Ensure TIM Safety and Efficiency?
– Manufacturers are advised to invest in cutting-edge materials and collaborate with tech startups to innovate and enhance TIM characteristics effectively.
– By employing innovative manufacturing solutions, companies can address current production challenges, ensuring the future robustness of EV battery systems.
Conclusion: Actionable Recommendations
As the EV market continues to expand, leveraging advanced TIMs becomes crucial for every stakeholder in the electric mobility space. Companies should focus on:
– Investing in the latest TIM research and development to secure a competitive edge.
– Collaborating with technology partners to pioneer safer, more efficient solutions.
– Adopting smart manufacturing techniques to overcome production challenges.
Understanding TIMs’ evolving role will be key to harnessing their full potential in the race towards sustainable, electrified transportation.
For more on the latest in material technology and innovation, visit Automotive News or Electrical Evolution.