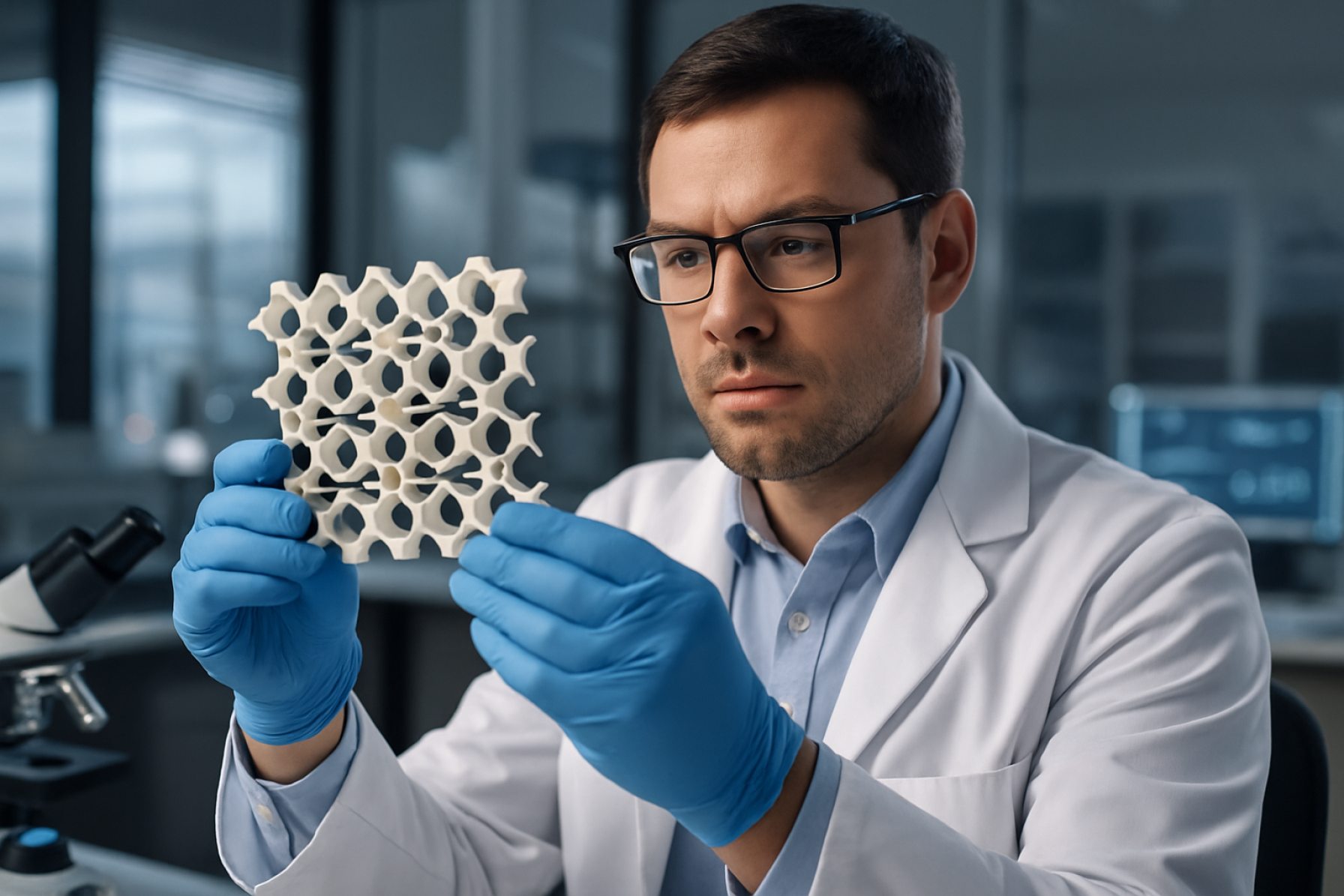
2025년 헥사키랄 메타물질 공학: 차세대 기계 및 음향 성능 개방. 이 혁신적인 기술이 스마트 재료와 산업 혁신의 미래를 어떻게 형성하고 있는지 탐구하십시오.
- 요약: 주요 트렌드와 시장 동향
- 헥사키랄 메타물질: 원리와 독특한 특성
- 2025년 글로벌 헥사키랄 메타물질 시장의 현재 상황
- 주요 산업 플레이어 및 최근 혁신
- 출현하는 응용 분야: 항공우주, 자동차, 그 이상
- 제조 기술 및 확장성 문제
- 시장 예측 및 2030년까지 성장 전망
- 규제 환경과 산업 표준
- 협력, 파트너십 및 학술 연구 이니셔티브
- 미래 전망: 혁신적 가능성과 전략적 기회
- 출처 및 참고 문헌
요약: 주요 트렌드와 시장 동향
헥사키랄 메타물질 공학은 헥사키랄 격자 구조의 독특한 기계적, 음향적 및 전자기적 특성에 힘입어 고급 재료 과학의 변혁적 분야로 빠르게 부상하고 있습니다. 2025년까지 이 분야는 첨단 제조, 계산 설계, 그리고 항공우주, 자동차 및 방위 산업에서 경량 고성능 재료에 대한 수요 증가에 의해 추진되는 연구-상용화 주기를 가속화하고 있습니다.
주요 트렌드는 디지털 디자인 및 시뮬레이션 플랫폼의 통합으로, 음의 포아송 비율(오켈틱 행동), 진동 감쇠 및 충격 저항과 같은 특정 기능에 맞게 헥사키랄 기하학을 정밀하게 조정할 수 있게 합니다. Stratasys 및 3D Systems와 같은 선도적인 적층 제조 회사는 고급 폴리머 및 금속 합금을 사용하여 복잡한 키랄 격자의 제조를 지원하기 위해 포트폴리오를 확장하고 있습니다. 이러한 능력은 특히 중량 감소와 에너지 흡수의 중요성이 큰 분야에서 프로토타입 및 저용량 생산에 필수적입니다.
또 다른 중요한 추진력은 차세대 항공우주 구조에서 헥사키랄 메타물질의 채택입니다. Airbus 및 Boeing과 같은 주요 항공우주 제조업체는 연료 효율성 및 구조적 회복성을 향상시키기 위해 경량 패널에서 변형 가능한 날개 구조에 이르는 응용 분야를 위해 키랄 격자 구성 요소를 적극적으로 탐색하고 있습니다. 방위 분야에서도 헥사키랄 갑옷 및 폭발 완화 솔루션에 대한 투자가 진행되고 있으며, 이러한 구조의 우수한 에너지 분산 특성을 활용하고 있습니다.
음향 및 진동 제어 분야에서 H.B. Fuller와 같은 기업들은 자동차 및 산업 환경에서 소음 감소와 충격 흡수를 위한 헥사키랄 메타물질의 사용을 조사하고 있습니다. 주파수 밴드갭 및 방향성 파동 전파를 설계할 수 있는 능력은 맞춤형 방음 및 진동 차단 제품을 위한 새로운 길을 열고 있습니다.
앞으로의 전망은 헥사키랄 메타물질 공학이 다재다능한 가능성을 가지고 있으며, 다재료 3D 프린팅, 확장 가능한 제조 및 현장 속성 모니터링의 지속적인 발전이 기대됩니다. ASTM International와 같은 연구 기관 및 표준 기구와의 산업 협력은 시험 프로토콜 및 인증 경로 개발을 가속화하여 시장 채택을 더욱 촉진할 것으로 예상됩니다. 디지털 제조 생태계가 성숙해짐에 따라, 향후 몇 년간 헥사키랄 메타물질의 상용화가 고부가가치 부문 전반에 걸쳐 더 광범위하게 이루어질 것으로 보입니다.
헥사키랄 메타물질: 원리와 독특한 특성
헥사키랄 메타물질은 헥사곤 격자에서 키랄(손잡이) 유닛 셀의 주기적인 배열로 특징지어지며, 고급 재료 공학의 중심이 되었습니다. 이들의 독특한 기하학은 음의 포아송 비율(오켈틱성), 향상된 에너지 흡수 및 조정 가능한 이방성 같은 예외적인 기계적 특성을 부여하여 기존 재료에서는 얻을 수 없는 특성을 갖습니다. 2025년 현재, 이 분야의 연구 및 개발은 항공우주, 자동차 및 생명공학 분야에서 경량, 탄력적이며 다기능 재료에 대한 수요로 가속화되고 있습니다.
헥사키랄 메타물질의 근본 원리는 그들의 미세 구조 디자인에 있습니다: 각 유닛 셀은 인접한 링과 연결된 중앙 링으로 구성되며, 링은 키랄(회전 비대칭) 방식으로 배열된 인대에 의해 연결됩니다. 이 구성은 재료가 신축시 측면으로 확장되는 오켈틱 행동을 나타내게 하며, 그 결과 우수한 압흔 저항 및 에너지 분산을 가능하게 합니다. 최근 실험 연구에 따르면 인대와 링의 기하학을 변화시킴으로써 엔지니어들은 강성, 감쇠 및 방향성 강도를 포함한 기계적 응답을 정밀하게 조정할 수 있습니다.
2025년 현재 여러 산업 리더 및 연구 기관이 헥사키랄 메타물질을 위한 확장 가능한 제조 기술을 적극 탐색하고 있습니다. 적층 제조(3D 프린팅)는 복잡한 키랄 구조를 높은 정밀도로 제조할 수 있는 선호 방법이 되었습니다. Stratasys 및 3D Systems와 같은 회사들이 프로토타입 및 기능 테스트를 위한 헥사키랄 구조를 생산할 수 있는 고급 폴리머 및 금속 3D 프린팅 플랫폼을 제공하고 있습니다. 또한, EOS는 실험실 규모 연구에서 상업적 규모 생산으로 전환을 지원하는 산업용 적층 제조 시스템에 특화되어 있습니다.
헥사키랄 메타물질의 독특한 특성은 다양한 응용 분야에서 활용되고 있습니다. 항공우주 산업에서는 그들의 경량 및 충격 저항 특성이 차세대 보호 패널 및 에너지 흡수 구성 요소에 평가되고 있습니다. 생명공학 분야에서는 조정 가능한 기계적 응답이 맞춤형 정형 외과 임플란트 및 보철물에 관심을 끌고 있으며, 여기서는 적응성과 충격 흡수가 중요합니다. 자동차 제조업체들은 충돌 안전 구조 및 진동 감쇄를 위해 이러한 재료를 조사하고 있습니다.
앞으로의 전망은 헥사키랄 메타물질 공학이 유망하다는 것입니다. 재료 과학자, 엔지니어 및 제조업체 간의 지속적인 협력은 새로운 디자인 패러다임과 확장 가능한 생산 방법을 창출할 것으로 기대됩니다. 디지털 디자인 도구와 적층 제조 기술이 계속 발전함에 따라 헥사키랄 메타물질의 상업적 제품 통합은 가속화될 것으로 예상되며, 2027년 이후 여러 산업을 혁신적으로 변화시킬 가능성이 있습니다.
2025년 글로벌 헥사키랄 메타물질 시장의 현재 상황
헥사키랄 메타물질 공학은 경량, 조정 가능, 다기능 재료에 대한 수요에 힘입어 2025년까지 항공우주, 자동차, 방위 및 첨단 제조 분야에서 상당한 발전을 이루었습니다. 헥사키랄 구조—벌집 같은 키랄 격자 기하학으로 특징지어짐—은 음의 포아송 비율(오켈틱성), 향상된 에너지 흡수 및 조정된 파동 전파와 같은 독특한 기계적 특성을 나타내어 차세대 응용 분야에 매력적입니다.
글로벌 헥사키랄 메타물질 시장은 초기이지만 빠르게 발전하는 단계에 있습니다. 주요 산업 플레이어들은 주로 북미, 유럽 및 동아시아에 분포해 있으며, 여기서 첨단 제조 능력과 연구 인프라가 혁신을 지원하고 있습니다. Boeing 및 Airbus와 같은 회사들은 경량 구조 구성 요소 및 충격 저항 패널용으로 설계된 메타물질에 대한 연구를 공개적으로 강조하고 있으며, 헥사키랄 디자인이 그들의 우수한 기계적 응답 및 에너지 분산 성능 덕분에 탐색되고 있습니다. 방위 분야에서는 Lockheed Martin과 같은 조직이 폭발 완화 및 보호 갑옷 시스템을 위한 헥사키랄 격자를 조사하고 있으며, 그들의 오켈틱 행동을 활용하여 회복력을 향상시키고 있습니다.
제조 측면에서 적층 제조(AM) 기술—특히 레이저 파우더 베드 융합 및 직접 에너지 증착—의 채택이 메탈 및 폴리머에서 복잡한 헥사키랄 기하학의 정밀한 제조를 가능하게 하고 있습니다. EOS 및 Stratasys와 같은 기업들이 이 복잡한 구조를 대규모로 생산할 수 있는 AM 플랫폼을 제공하고 있으며, BASF와 같은 재료 공급업체들은 메타물질 성능을 최적화한 고급 원료를 개발하고 있습니다.
최근 산업 컨소시엄 및 표준 기구의 데이터는 헥사키랄 메타물질에 특화된 기술 표준 및 시험 프로토콜의 증가를 나타내고 있으며, 이는 이 분야의 성숙을 반영하고 있습니다. 산업과 학계 간의 협력 이니셔티브는 실험실 규모의 헥사키랄 디자인을 상업 제품으로 전환하는 속도를 가속화하고 있으며, 진동 감쇠, 음향 단열 및 경량 샌드위치 패널에 대한 파일럿 프로젝트가 진행되고 있습니다.
앞으로의 전망은 헥사키랄 메타물질 공학이 강력하다는 것입니다. 시장 채택은 제조 비용이 감소하고 현장 시험에서 수집된 성능 데이터가 확보됨에 따라 가속화될 것으로 예상됩니다. 향후 몇 년간 헥사키랄 메타물질의 항공우주 및 방위 플랫폼에서의 통합이 증가하고 로봇, 의료 기기 및 민간 인프라에 대한 새로운 응용 분야가 모습을 드러낼 것입니다. OEM, AM 기술 제공업체 및 재료 회사 간의 전략적 파트너십은 생산 규모 확대와 새로운 기능 개방에 중요한 역할을 할 것입니다.
주요 산업 플레이어 및 최근 혁신
헥사키랄 메타물질 공학, 즉 키랄 격자 구조의 독특한 기계적 및 음향적 특성을 활용하는 분야는 2025년까지 상당한 산업 참여 및 혁신을 경험하고 있습니다. 이 분야는 기존 고급 재료 기업과 민첩한 스타트업이 혼합되어 있으며, 각자 헥사키랄 메타물질의 설계, 제조 및 응용의 빠른 발전에 기여하고 있습니다.
가장 두드러진 산업 플레이어 중 하나는 Evonik Industries로, 특수 화학물질 및 고급 재료 분야의 글로벌 리더입니다. Evonik은 경량의 고강도 항공우주 및 자동차 응용 분야를 위해 폴리머 기반의 키랄 격자의 개발에 투자하고 있습니다. 최근 항공우주 OEM과의 협력으로 오켈틱 및 조정 가능한 음향 특성을 활용한 프로토타입 패널 및 진동 감쇠 요소가 탄생하였습니다.
또 다른 주요 플레이어는 3D Systems로, 적층 제조 기술로 유명합니다. 3D Systems는 고성능 폴리머 및 금속을 사용하여 복잡한 키랄 격자의 직접 제작을 포함하는 포트폴리오를 확장하고 있습니다. 2024년 이 회사는 여러 유럽 연구 기관과 파트너십을 체결하여 헥사키랄 메타물질 기반의 정형외과 임플란트를 상용화하기 위한 협업을 발표하였습니다.
아시아-태평양 지역에서는 미쓰비시 화학 그룹이 주요 혁신자로 부상하고 있습니다. 이 회사의 R&D 부서는 소비자 전자 제품 및 보호 장비 시장을 목표로 헥사키랄 구조를 생산하기 위한 확장 가능한 공정을 개발하였습니다. 그들의 최신 특허는 충격 저항성이 뛰어난 케이스 및 착용 장치용 유연하고 에너지 흡수층에 집중하고 있습니다.
공급업체 측면에서 Stratasys는 헥사키랄 메타물질의 설계 및 신속한 프로토타입화를 위해 최적화된 새로운 인쇄 물질 및 소프트웨어 도구를 출시하였습니다. 그들의 개방형 플랫폼 접근 방식은 연구 기관 및 산업 파트너들이 격자 기하학 및 재료 조합을 반복하여 기능적 프로토타입으로의 개념 전환을 가속화할 수 있도록 하고 있습니다.
앞으로의 몇 년 동안 헥사키랄 메타물질이 주류 제조에 통합될 것으로 예상되며, 특히 디지털 디자인 및 시뮬레이션 도구가 성숙해짐에 따라 더욱 그렇습니다. 산업 분석가들은 재료 공급업체, OEM 및 최종 사용자 간의 협력이 항공 우주, 의료 기기 및 첨단 로봇 분야에서 이러한 구조의 채택을 촉진할 것이라고 예상하고 있습니다. 지속 가능성과 경량화에 대한 지속적인 관심은 헥사키랄 솔루션의 수요를 더욱 증대시켜 2027년 이후 강력한 성장을 이룰 것입니다.
출현하는 응용 분야: 항공우주, 자동차, 그 이상
헥사키랄 메타물질 공학은 실험실 연구에서 실생활 응용으로 빠르게 전환되고 있으며, 2025년은 항공 우주, 자동차 등 고급 분야로 통합되는 중대한 해가 되고 있습니다. 헥사키랄 구조—독특한 벌집 같은 기하학과 회전 대칭성을 갖춘—은 음의 포아송 비율(오켈틱), 높은 에너지 흡수 및 조정 가능한 강도를 포함한 예외적인 기계적 특성을 제공합니다. 이러한 특성은 경량, 탄력적이며 다기능성 재료를 찾고 있는 산업에 점점 더 매력적이 되고 있습니다.
항공 우주 산업에서는 낮은 중량과 높은 충격 저항 및 진동 감쇠를 조합한 소재에 대한 수요가 헥사키랄 메타물질의 채택을 촉진하고 있습니다. Airbus 및 Boeing과 같은 기업들은 차세대 항공기 및 내부 구성 요소를 위한 고급 격자 구조를 적극 탐색하고 있습니다. 헥사키랄 디자인은 충격 저항성이 개선되고 소음 전파가 줄어드는 잠재성을 평가받고 있으며, 2025년에는 프로토타입 패널과 샌드위치 구조의 테스트가 진행되고 있습니다. 선택적 레이저 소결 및 전자빔 용융과 같은 적층 제조의 통합은 항공우주 등급 합금 및 복합재료에서 복잡한 헥사키랄 기하학의 생산을 가능하게 하고 있습니다.
자동차 산업도 승객 안전 및 차량 효율성을 높이기 위한 관심이 급증하고 있습니다. BMW와 테슬라는 에너지 흡수 크럼플 존, 경량 섀시 구성 요소 및 적응형 내부 구조를 위해 헥사키랄 메타물질을 조사하는 자동차 제조업체 중 하나입니다. 재료 공급업체 및 3D 프린팅 전문가와의 초기 협력이 확장 가능 생산 방법 및 기존 차량 플랫폼 통합에 집중되고 있습니다. 헥사키랄 격자의 독특한 변형 메커니즘은 기존의 폼이나 벌집보다 충격 에너지를 더 효과적으로 분산시키는 구성 요소 설계에 활용되고 있습니다.
항공우주 및 자동차를 넘어 헥사키랄 메타물질은 로봇 공학, 보호 장비 및 토목 공학에서도 응용되고 있습니다. Boston Dynamics와 같은 회사들은 경량 및 유연한 로봇 팔다리 및 그립퍼용으로 이들 재료를 탐색하고 있으며, 스포츠 및 산업 안전 장비 제조업체들은 충격 흡수가 향상된 차세대 헬멧 및 패딩을 개발하고 있습니다. 토목 공학에서는 헥사키랄 패널이 내진 구조 및 진동 격리 시스템에 사용되기 위해 테스트되고 있습니다.
앞으로의 전망은 헥사키랄 메타물질 공학이 매우 유망하다는 것입니다. 컴퓨테이셔널 디자인, 디지털 제조 및 재료 과학의 지속적인 발전이 상용화를 가속화할 것으로 기대됩니다. 2025년 및 향후 몇 년 간의 산업 파트너십 및 파일럿 프로젝트는 최초의 대규모 배포를 가져올 것으로 예상되며, 고성능 여러 분야에서의 넓은 채택을 위한 기초를 마련할 것입니다.
제조 기술 및 확장성 문제
헥사키랄 메타물질은 독특한 키랄 격자 구조와 오켈틱 기계 응답으로 특징지어지며, 2025년 첨단 재료 공학의 최전선에 있습니다. 이 설계된 재료의 제조는 특히 항공우주, 생체 기반 기기 및 유연한 전자 기기와 같은 분야에서 수요가 증가함에 따라 많은 기회를 제공하지만 확장성의 문제도 주목할 만합니다.
적층 제조(AM)는 연구 및 상업적 규모 모두에서 헥사키랄 메타물질을 제작하는 주요 기술입니다. 금속의 경우 선택적 레이저 소결(SLS) 및 직접 금속 레이저 소결(DMLS)이 광범위하게 채택되고 있으며, 폴리머의 경우 스테레오리소그래피(SLA) 및 디지털 광 처리(DLP)가 선호되고 있습니다. EOS GmbH 및 Stratasys와 같은 회사들은 높은 정밀도로 복잡한 키랄 기하학을 생산할 수 있는 산업급 AM 플랫폼을 개발했습니다. 이러한 시스템은 전통적인 절삭 방법으로는 달성할 수 없는 복잡한 유닛 셀과 격자 구조의 실현을 가능하게 합니다.
이러한 발전에도 불구하고, 확장성은 여전히 중요한 문제입니다. AM 프로세스의 층별 특성은 대형 영역 또는 고용량 생산에 대해 내재적으로 처리량을 제한합니다. 표면 마감 및 해상도 또한 중요한 요소로, 헥사키랄 메타물질의 기계적 특성은 기하학적 일관성에 매우 민감합니다. 이러한 문제를 해결하기 위해 제조업체들은 다중 레이저 시스템 및 병렬 인쇄 배열에 투자하고 있습니다. 예를 들어, 3D Systems는 설계된 재료의 빌드 속도를 증가시키기 위한 다중 헤드 프린터를 도입했습니다.
재료 선택은 확장성을 더욱 복잡하게 만듭니다. 폴리머는 상대적으로 가공이 편리하지만, 고성능 응용 분야에 필요한 금속이나 세라믹으로의 헥사키랄 디자인 전환은 고급 파우더 취급 및 후처리 기술을 요구합니다. Renishaw와 같은 기업들은 반복 가능성과 구조적 무결성을 보증하기 위해 폐쇄형 품질 제어 및 현장 모니터링 시스템을 개발하고 있습니다.
앞으로의 전망은 하이브리드 제조 접근 방식이 확산되고 있습니다. 이러한 방식은 AM과 전통적인 제조 공정인 사출 성형 또는 롤 투 롤 제조를 결합하여 키랄 구조의 대량 생산을 가능하게 합니다. 산업 및 연구 기관 간의 협력 노력이 확장 가능한 공정 개발을 가속화하고 있으며, 2026-2027년까지 파일럿 라인 및 데모가 성숙해질 것으로 예상됩니다. 전망은 긍정적입니다. 디지털 디자인 및 제조 생태계가 발전함에 따라 헥사키랄 메타물질 생산의 비용 및 복잡성 장벽이 감소할 것으로 기대되며, 이는 더 넓은 산업 채택의 길을 열 것입니다.
시장 예측 및 2030년까지 성장 전망
헥사키랄 메타물질 공학은 독특한 키랄 격자 구조로 특징지어지는 설계된 재료의 하위 집합으로, 2030년까지 상당한 시장 확장이 예상됩니다. 2025년 현재 상황은 항공우주, 자동차, 방위 및 첨단 제조와 같은 분야에서 연구-상용화 활동의 급증으로 특징지어집니다. 이러한 재료는 음의 포아송 비율(오켈틱성), 높은 에너지 흡수, 조정 가능한 음향 및 진동 감쇠 기능 등으로 인하여 높은 가치가 있습니다.
주요 산업 플레이어는 실험실 규모 시연에서 확장 가능한 생산으로의 전환을 가속화하고 있습니다. Airbus 및 Boeing와 같은 기업들은 차세대 항공기 및 우주선의 경량 충격 저항 부품으로 헥사키랄 메타물질을 적극 탐색하고 있습니다. 이들의 R&D 부서는 이러한 구조를 동체 패널, 내부 구성 요소 및 보호 케이스에 통합하기 위해 고급 재료 공급업체 및 학술 기관과 협력하고 있으며, 안전성과 성능을 향상하면서 중량을 줄이는 것을 목표로 하고 있습니다.
자동차 산업에서는 BMW Group 및 Tesla, Inc.와 같은 제조업체들이 전기차의 추돌 에너지 관리 및 소음 감소를 위해 헥사키랄 격자의 사용을 조사하고 있습니다. 미세 구조 수준에서 기계적 응답을 조정할 수 있는 능력은 이러한 재료에 대한 관심을 높이고 있으며, 실제 조건에서의 성능을 검증하기 위한 파일럿 프로젝트가 진행 중입니다.
방위 산업도 또 다른 주요 사용자로, Lockheed Martin 및 Northrop Grumman와 같은 조직들이 헥사키랄 메타물질 기반의 갑옷 및 폭발 완화 시스템 개발에 투자하고 있습니다. 이러한 노력은 인력 및 차량을 위한 차세대 보호 솔루션을 위한 정부 자금 지원 연구 프로그램에 의해 지원받고 있습니다.
제조 관점에서 고급 적층 제조(AM) 기술의 확산은 헥사키랄 메타물질의 상업적 실현 가능성을 위한 핵심 요소입니다. Stratasys 및 3D Systems는 복잡한 키랄 기하학을 대규모로 제조할 수 있는 고정밀 AM 시스템을 포함하는 포트폴리오를 확장하고 있으며, 이는 비용 절감과 새로운 시장 기회를 열 것으로 기대됩니다.
앞으로의 예측은 헥사키랄 메타물질 공학의 글로벌 시장이 2030년까지 두 자릿수의 연평균 성장률(CAGR)을 경험할 것이라는 것입니다. 이는 고부가가치 산업 전반에 걸쳐 경량 다기능 재료에 대한 수요 증가에 의해 추진됩니다. 표준화 노력이 성숙해짐에 따라 공급망이 적응함에 따라 헥사키랄 메타물질의 채택이 가속화될 것으로 예상되며, 북미, 유럽 및 동아시아가 주요 성장 지역으로 부상할 것입니다. 향후 몇 년 동안 프로토타입에서 광범위한 배치로의 전환이 이루어져 헥사키랄 메타물질이 고급 공학 솔루션의 초석으로 자리 잡을 것입니다.
규제 환경과 산업 표준
헥사키랄 메타물질 공학에 관한 규제 환경과 산업 표준은 기술이 성숙하고 항공우주, 자동차, 민간 공학 및 첨단 제조와 같은 분야에서 응용되면서 신속하게 발전하고 있습니다. 2025년 현재, 헥사키랄 메타물질을 직접 규제하는 통일된 글로벌 표준은 없지만, 여러 설립된 프레임워크와 조직들이 규제 환경을 형성하고 있습니다.
유럽연합 내에서 유럽 표준화 위원회 (CEN)와 유럽 전기 표준화 위원회 (CENELEC)는 헥사키랄 아키텍처를 포함한 새로운 재료가 안전성, 환경 및 성능 요구 사항을 준수하는지 모니터링하고 있습니다. 이들 기관은 헥사키랄 구조가 중요한 인프라 및 교통 응용 분야에 적합하도록 기존 고급 재료 및 구조적 구성 요소에 대한 표준에 통합되고 있습니다.
미국에서는 ASTM International과 미국 기계 공학회 (ASME)가 헥사키랄 메타물질을 제작하는 데 자주 사용되는 기계 시험, 재료 특성화 및 적층 제조 프로세스에 관련된 표준을 개발하는 주요 기관입니다. ASTM의 적층 제조 기술 위원회 F42는 특히 관련성이 큽니다. 많은 헥사키랄 구조가 고급 3D 프린팅 기술을 사용하여 생산되기 때문입니다. 이러한 표준은 반복 가능성, 기계적 무결성 및 품질 보증 등과 같은 문제를 다룹니다.
< EOS GmbH 및 Stratasys Ltd. 같은 산업 선두주자들은 자신의 장비 및 프로세스가 신흥 규제 요구 사항을 충족하는 헥사키랄 메타물질을 신뢰할 수 있게 생산할 수 있도록 표준 기구와 협력하고 있습니다. 이들 회사는 또한 실세계 조건에서 메타물질 기반 구성 요소의 성능을 검증하기 위한 파일럿 프로그램 및 컨소시엄에 참여하고 있습니다.
앞으로의 몇 년 동안 헥사키랄 유형을 포함한 메타물질 전용 표준의 공식화가 이루어질 것으로 예상됩니다. 국제 표준화 기구 (ISO)가 글로벌 표준 통합에 중심적인 역할을 할 것으로 보이며, 특히 국경 간 공급망 및 인증 프로세스가 더 중요해짐에 따라 그 역할이 더욱 커질 것입니다. 또한, 항공 및 민간 공학 분야의 규제 기관은 헥사키랄 메타물질의 사용에 대한 특정 가이드를 발행할 가능성이 높으며, 여기에 생애주기 평가, 재활용 가능성 및 장기 내구성에 중점을 둘 것입니다.
전반적으로, 규제 프레임워크는 아직 개발 중에 있지만, 표준화 기구와 주요 제조업체의 적극적인 참여가 헥사키랄 메타물질 공학에 대한 강력하고 국제적으로 인정받는 지침을 향한 경로를 가속화하고 있습니다.
협력, 파트너십 및 학술 연구 이니셔티브
헥사키랄 메타물질 공학은 특히 2025년까지 이 분야가 성숙해감에 따라 협력, 파트너십 및 학술 연구 이니셔티브의 네트워크를 통해 빠르게 발전하고 있습니다. 헥사키랄 구조의 독특한 기계적 및 음향적 특성—예를 들어 음의 포아송 비율 및 조정 가능한 밴드갭—은 이들 재료를 차세대 응용 분야로 활용하고자 하는 학술 기관 및 산업 리더들의 관심을 끌고 있습니다.
최근 몇 년 동안 여러 저명한 대학교들이 키랄 및 오켈틱 메타물질에 초점을 맞춘 전담 연구 그룹을 설립하였습니다. 예를 들어, 케임브리지 대학교 및 임페리얼 칼리지 런던은 헥사키랄 격자의 컴퓨터 설계 및 적층 제조를 탐색하는 진행 중인 프로젝트를 진행하며, 종종 산업 이해관계자와의 파트너십을 통해 이루어집니다. 이러한 협력은 기본 연구와 확장 가능한 생산 간의 격차를 해소하기 위해 국가 자금 지원 기관 및 유럽 컨소시엄의 지원을 받고 있습니다.
산업 측면에서, 첨단 재료 및 적층 제조 전문 회사들은 헥사키랄 메타물질 상용화를 가속화하기 위해 점점 더 학술 파트너와 협력하고 있습니다. EOS GmbH, 산업 3D 프린팅의 선두주자는 선택적 레이저 소결 및 직접 금属 레이저 소결을 통해 복잡한 키랄 기하학의 제작 최적화를 위한 공동 연구에 참여하고 있습니다. 마찬가지로 Stratasys는 경량 및 충격 저항 부품을 위한 새로운 폴리머 기반 헥사키랄 구조 개발을 위해 연구 기관과 협력하고 있습니다.
국제적으로는 NASA와 유럽 우주국 (ESA)가 모두 항공우주 응용 분야를 위한 키랄 메타물질 연구에 자금을 지원하여 그들의 진동 감쇠 및 구조 건강 모니터링 잠재력을 인정하였습니다. 이들 기관은 종종 재료 과학자, 기계 엔지니어 및 계산 모델러들을 모으는 다기관 프로젝트를 촉진합니다.
향후 몇 년 간의 전망은 학계와 산업 간의 심화된 통합이 이루어질 것으로 예상되며, 테스트 프로토콜 표준화 및 생산 방법 확대에 집중할 것입니다. 키랄 격자 디자인의 오픈 액세스 데이터베이스와 기계적 특성화를 위한 공유 시험대와 같은 이니셔티브가 출현함으로써 혁신이 더욱 가속화될 것입니다. 지식 재산 포트폴리오가 성장하고 파일럿 프로젝트가 상업 제품으로 전환됨에 따라 헥사키랄 메타물질 공학을 둘러싼 협력 생태계는 2020년대 후반까지 여러 분야에 걸쳐 실질적인 영향을 미칠 준비가 되어 있습니다.
미래 전망: 혁신적 가능성과 전략적 기회
헥사키랄 메타물질 공학은 2025년과 이후 여러 산업에서 변화의 힘이 될 것으로 기대됩니다. 그 독특한 기계적 특성——예를 들어 음의 포아송 비율, 높은 에너지 흡수 및 조정 가능한 강도——이 이를 견인하고 있습니다. 실험실 규모의 시연에서 확장 가능한 제조로의 지속적인 전환이 가속화되고 있으며, 여러 주요 플레이어 및 연구 기관이 산업화와 응용 특화 맞춤화에 초점을 맞추고 있습니다.
항공 우주 및 방위 분야에서는 경량 및 충격 저항 구조에 대한 수요가 헥사키랄 메타물질의 채택을 촉진시키고 있습니다. Airbus와 Boeing은 차세대 공항 및 내부 구성 요소를 위한 고급 격자 구조를 적극 탐색하고 있으며, 이는 연료 효율성 및 충돌 안전성을 향상시키는 것을 목표로 하고 있습니다. 헥사키랄 디자인의 샌드위치 패널 및 에너지 흡수층 통합은 2026년까지 프로토타입에서 초기 배치로 진행될 것으로 예상되며, 적층 제조 능력이 성숙해짐에 따라 이루어질 것입니다.
자동차 산업에서는 BMW Group 및 Tesla와 같은 주요 제조업체들이 헥사키랄 메타물질을 경량 섀시 구성 요소 및 고급 충돌 보호 시스템에 사용하고 있습니다. 이들은 이러한 재료의 오켈틱 행동을 활용하여 차량 질량을 줄이는 동시에 탑승자 안전을 향상시키는 데 초점을 맞추고 있으며, 이는 업계의 전기화 및 지속 가능성 목표에 부합합니다.
의료 기기 산업은 헥사키랄 구조의 또 다른 전선으로, Smith+Nephew 및 Stryker와 같은 기업들이 정형외과 임플란트 및 보철물의 헥사키랄 스캐폴드를 탐색하고 있습니다. 기계적 반응을 조정하고 조직 통합을 촉진할 수 있는 능력은 향상된 수명과 환자 결과를 가진 차세대 임플란트를 생산할 것으로 기대됩니다. 초기 임상 시험 및 규제 제출 또한 향후 2~3년 내에 있을 것으로 예상됩니다.
전략적으로, 헥사키랄 메타물질의 혁신적 가능성은 주문형 사용자 맞춤화 및 디지털 제조 역량에 있습니다. 3D Systems 및 Stratasys와 같은 기업들은 복잡한 키랄 기하학을 지원하기 위해 적층 제조 플랫폼을 확장하고 있으며, 이는 신속한 프로토타입화 및 지역 생산을 가능하게 합니다. 이는 소비자 전자 기기, 스포츠 장비 및 보호 장비와 같은 분야에서 성능 차별화가 중요한 산업에 대한 진입 장벽을 낮출 것으로 기대됩니다.
앞으로, 컴퓨터 설계, 첨단 재료 및 디지털 제조의 융합은 새로운 비즈니스 모델 및 공급망 효율성을 열어줄 것입니다. ASTM International와 같은 조직의 표준화 노력이 진행됨에 따라 헥사키랄 메타물질 구성 요소의 더 넓은 채택 및 인증이 가능해지며, 2020년대 후반까지의 광범위한 상용화를 위한 길이 열릴 것입니다.
출처 및 참고 문헌
- Stratasys
- 3D Systems
- Airbus
- Boeing
- H.B. Fuller
- ASTM International
- EOS
- Lockheed Martin
- BASF
- Evonik Industries
- Renishaw
- Northrop Grumman
- 유럽 표준화 위원회 (CEN)
- 미국 기계 공학회 (ASME)
- 국제 표준화 기구 (ISO)
- 케임브리지 대학교
- 임페리얼 칼리지 런던
- NASA
- 유럽 우주국 (ESA)
- Smith+Nephew