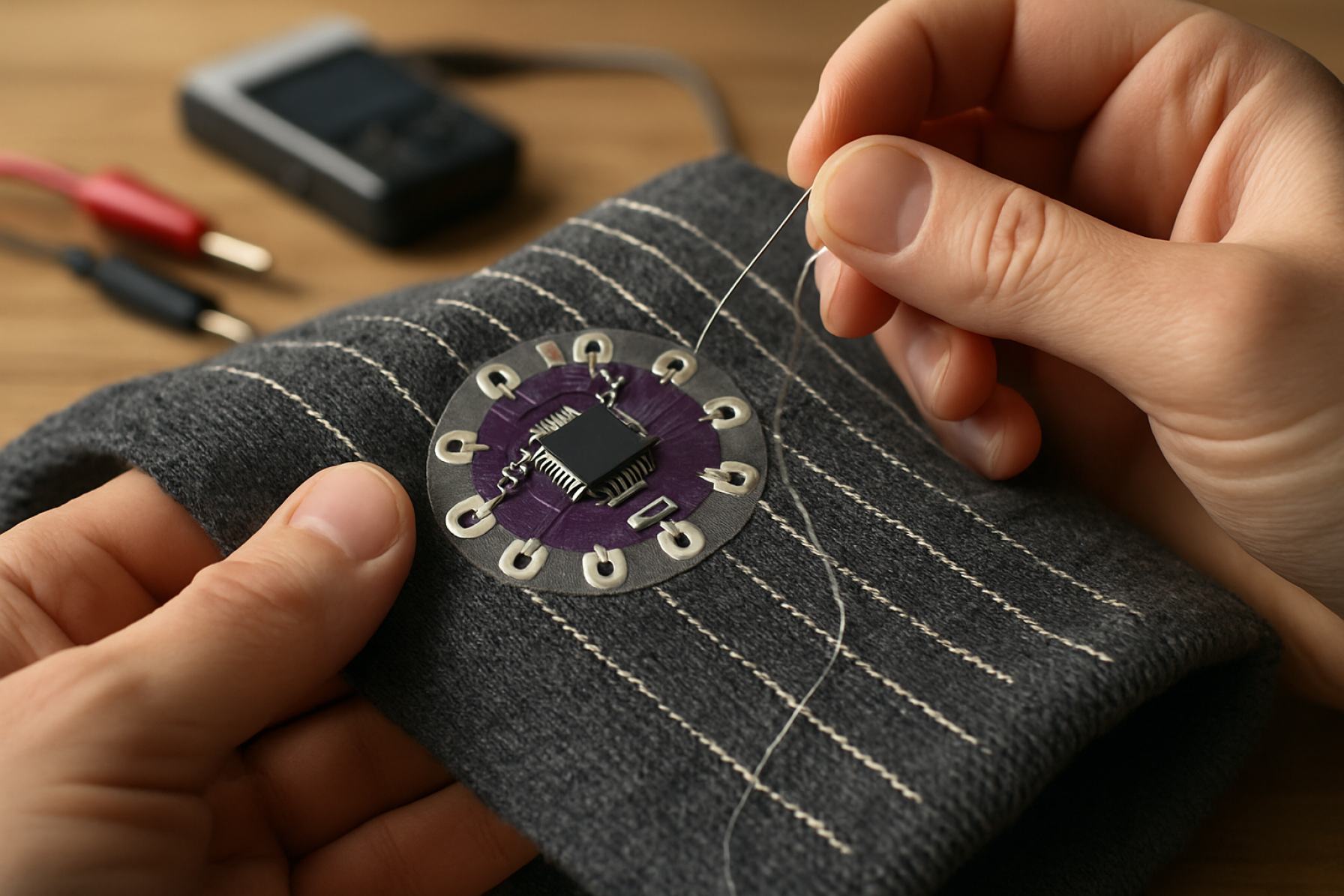
Revolutionizing Wearables and Beyond: How Conductive Textile Development in 2025 Is Accelerating Innovation Across Industries. Explore Market Growth, Breakthrough Technologies, and the Road Ahead.
- Executive Summary: Key Trends and Market Drivers in Conductive Textiles
- Market Size and Forecast (2025–2030): Growth Projections and CAGR Analysis
- Emerging Applications: Wearables, Medical, Automotive, and Industrial Uses
- Material Innovations: Advances in Fibers, Yarns, and Coatings
- Manufacturing Techniques: From Traditional Weaving to Advanced Printing
- Competitive Landscape: Leading Companies and Strategic Partnerships
- Regulatory Standards and Industry Certifications
- Sustainability and Environmental Impact in Conductive Textile Production
- Challenges and Barriers: Technical, Economic, and Supply Chain Issues
- Future Outlook: Disruptive Technologies and Long-Term Market Opportunities
- Sources & References
Executive Summary: Key Trends and Market Drivers in Conductive Textiles
The development of conductive textiles is accelerating in 2025, driven by advances in materials science, growing demand for wearable electronics, and the integration of smart functionalities into everyday fabrics. Conductive textiles—fabrics that can conduct electricity—are being engineered using a variety of methods, including the incorporation of metallic fibers, conductive polymers, and nanomaterials such as graphene and carbon nanotubes. These innovations are enabling new applications in healthcare, sports, military, and consumer electronics.
Major industry players are investing heavily in research and development to enhance the performance, durability, and washability of conductive textiles. Toray Industries, a global leader in advanced materials, continues to expand its portfolio of conductive fibers and fabrics, focusing on applications ranging from wearable sensors to flexible circuits. Teijin Limited is similarly advancing its aramid and polyester-based conductive textiles, targeting both industrial and consumer markets. European manufacturers such as TITV Greiz are pioneering textile integration techniques, including embroidery and coating processes, to embed conductivity without compromising fabric comfort or flexibility.
In 2025, the sector is witnessing a shift toward scalable production methods and eco-friendly materials. Companies like Laird Performance Materials are developing roll-to-roll processing techniques for conductive coatings, aiming to reduce costs and improve throughput. Meanwhile, Shieldex is expanding its range of silver-plated textiles, which are widely used for electromagnetic shielding and medical applications due to their antimicrobial properties.
The integration of conductive textiles into smart garments and e-textiles is a key trend, with collaborations between textile manufacturers and electronics companies becoming more common. For example, Textronics specializes in textile-based sensors for fitness and health monitoring, while Schoeller Textiles is developing fabrics with embedded heating and lighting elements. These partnerships are expected to accelerate commercialization and adoption in the coming years.
Looking ahead, the outlook for conductive textile development remains robust. Industry bodies such as the Advanced Textiles Association are forecasting continued growth, driven by the proliferation of smart devices and the need for lightweight, flexible electronic components. As standards for durability and safety evolve, and as manufacturing costs decrease, conductive textiles are poised to become integral to next-generation wearable technology, medical devices, and connected environments through 2025 and beyond.
Market Size and Forecast (2025–2030): Growth Projections and CAGR Analysis
The global conductive textile market is poised for robust growth between 2025 and 2030, driven by expanding applications in wearable electronics, medical devices, automotive interiors, and military gear. As of 2025, the market is characterized by increasing demand for flexible, lightweight, and durable materials that can integrate electronic functionalities without compromising comfort or aesthetics. Key industry players are scaling up production capacities and investing in advanced manufacturing techniques to meet this demand.
Major manufacturers such as Toray Industries, Inc., a leader in advanced fibers and textiles, and Teijin Limited, known for its high-performance materials, are at the forefront of innovation. Both companies have announced ongoing investments in research and development to enhance the conductivity, washability, and integration of their textile products. Toray Industries, Inc. continues to expand its product portfolio with new conductive fiber offerings, while Teijin Limited is focusing on smart textile solutions for healthcare and sports applications.
In Europe, NV Bekaert SA stands out as a prominent supplier of metal-coated fibers and yarns, catering to both industrial and consumer markets. The company’s ongoing collaborations with electronics manufacturers and automotive suppliers are expected to further boost market penetration of conductive textiles in the coming years. Similarly, Laird Performance Materials (now part of DuPont) is leveraging its expertise in electromagnetic shielding and thermal management to develop next-generation conductive fabrics for electronic devices and automotive applications.
The market outlook for 2025–2030 is underpinned by several factors:
- Rising adoption of wearable health monitoring devices, which require reliable and skin-friendly conductive fabrics.
- Automotive industry trends toward smart interiors and integrated sensor systems, driving demand for conductive textiles in seats, steering wheels, and dashboards.
- Military modernization programs emphasizing lightweight, multifunctional uniforms with embedded communication and sensing capabilities.
- Growing consumer interest in smart clothing and interactive fashion, supported by collaborations between textile manufacturers and technology firms.
While precise market size figures for 2025 and CAGR projections through 2030 vary by source, industry consensus points to a high single-digit to low double-digit annual growth rate, reflecting both expanding end-use applications and ongoing material innovations. The entry of new players and the scaling up of production by established companies such as Toray Industries, Inc., Teijin Limited, and NV Bekaert SA are expected to intensify competition and accelerate market expansion over the next five years.
Emerging Applications: Wearables, Medical, Automotive, and Industrial Uses
The development of conductive textiles is accelerating rapidly in 2025, driven by surging demand across wearables, medical, automotive, and industrial sectors. These textiles, which integrate conductive fibers or coatings into fabrics, enable electronic functionality such as sensing, heating, and data transmission while maintaining flexibility and comfort.
In the wearables market, conductive textiles are foundational to next-generation smart clothing and accessories. Companies like Textronics, Inc.—a pioneer in electro-textile technology—continue to expand their product lines, integrating sensors for fitness tracking, biometric monitoring, and gesture control. Similarly, Interactive Wear AG is advancing textile-based solutions for sports and outdoor apparel, focusing on seamless integration of electronics for real-time health and activity monitoring.
Medical applications are a major growth area, with conductive textiles enabling continuous, non-invasive patient monitoring. Schoeller Textiles AG is collaborating with healthcare device manufacturers to develop fabrics that can monitor vital signs such as heart rate and respiration, supporting remote patient care and early detection of health issues. The integration of silver-coated fibers and conductive polymers is enhancing both the sensitivity and durability of these medical textiles.
In the automotive sector, conductive textiles are being adopted for in-seat heating, occupant sensing, and touch-responsive interiors. Seiren Co., Ltd., a global leader in automotive textiles, is investing in the development of conductive fabric solutions that improve passenger comfort and enable advanced human-machine interfaces. These innovations are expected to become standard features in electric and autonomous vehicles over the next few years.
Industrial uses are also expanding, with conductive textiles being deployed for electromagnetic shielding, anti-static workwear, and flexible wiring in environments where traditional cables are impractical. NV Bekaert SA, a major supplier of metal fiber-based textiles, is scaling up production to meet demand from electronics manufacturing and aerospace industries, where lightweight, robust conductive materials are critical.
Looking ahead, the outlook for conductive textile development is robust. Advances in nanomaterials, such as graphene and carbon nanotubes, are expected to further enhance conductivity, washability, and integration with traditional textile processes. Industry collaborations and standardization efforts are likely to accelerate commercialization, with leading companies investing in scalable manufacturing and sustainable materials. As a result, conductive textiles are poised to become ubiquitous across multiple sectors by the late 2020s.
Material Innovations: Advances in Fibers, Yarns, and Coatings
The development of conductive textiles is accelerating in 2025, driven by advances in fibers, yarns, and coatings that enable integration of electronic functionality into fabrics without compromising flexibility or comfort. The sector is witnessing a convergence of material science and textile engineering, with a focus on scalable manufacturing and enhanced durability for applications in wearables, medical devices, automotive interiors, and smart home products.
A key trend is the refinement of conductive fibers and yarns. Companies such as Toray Industries and Teijin Limited are leveraging their expertise in synthetic fibers to produce yarns coated or embedded with conductive materials like silver, copper, and carbon nanotubes. These fibers are engineered for high conductivity, washability, and resistance to mechanical stress, addressing previous limitations in durability and performance. For example, Toray Industries has expanded its portfolio of conductive textiles for use in wearable sensors and flexible circuits, emphasizing scalable production methods.
Coating technologies are also advancing rapidly. Thüringisches Institut für Textil- und Kunststoff-Forschung e.V. (TITK) in Germany is pioneering the use of polymer-based coatings infused with metallic nanoparticles, which can be applied to a variety of textile substrates. These coatings provide uniform conductivity while maintaining the fabric’s tactile properties. Similarly, Shinkong Synthetic Fibers Corporation is developing proprietary coating processes that enhance the adhesion and longevity of conductive layers on polyester and nylon fabrics, targeting both consumer electronics and industrial applications.
Hybrid approaches are gaining traction, combining conductive fibers with printed or sprayed electronic inks. DuPont is a leader in this space, offering conductive inks and pastes that can be integrated into textile manufacturing lines, enabling the creation of complex circuits and sensors directly on fabric surfaces. This approach supports the mass production of smart garments and e-textiles with embedded sensing, lighting, or heating functions.
Looking ahead, the outlook for conductive textile development is robust. Industry collaborations are intensifying, with textile manufacturers partnering with electronics companies to standardize materials and processes. The focus is on improving recyclability, biocompatibility, and environmental impact, as well as meeting the stringent requirements of medical and automotive sectors. As material innovations continue to mature, conductive textiles are expected to move from niche applications to mainstream adoption across multiple industries by the late 2020s.
Manufacturing Techniques: From Traditional Weaving to Advanced Printing
The development of conductive textiles has accelerated rapidly in recent years, driven by the convergence of traditional textile manufacturing and advanced electronic integration. As of 2025, the sector is witnessing a shift from conventional weaving and knitting methods toward innovative techniques such as advanced printing, coating, and hybrid fabrication, enabling the scalable production of smart fabrics with enhanced electrical properties.
Traditional weaving and knitting remain foundational for integrating conductive fibers—such as silver-coated yarns or stainless steel threads—directly into textile structures. Companies like Statex Produktions- und Vertriebs GmbH have long specialized in silver-plated textiles, leveraging established weaving processes to produce fabrics for medical, military, and industrial applications. Similarly, NV Bekaert SA manufactures stainless steel fibers and yarns, which are incorporated into woven and knitted fabrics to impart conductivity while maintaining flexibility and durability.
However, the limitations of traditional methods—such as challenges in achieving fine patterning and uniform conductivity—have spurred the adoption of advanced manufacturing techniques. Screen printing and inkjet printing of conductive inks are gaining traction, allowing for precise deposition of materials like silver nanoparticles, carbon nanotubes, or conductive polymers onto textile substrates. DuPont, a major materials science company, has developed specialized conductive inks compatible with textile printing, enabling the creation of flexible circuits and sensors directly on fabrics. These printing techniques support high-throughput production and customization, which are critical for applications in wearable electronics and smart garments.
Coating and lamination processes are also being refined. For instance, Toray Industries, Inc. is advancing polymer-based coatings that impart conductivity while preserving the textile’s tactile qualities. These methods are particularly relevant for large-area applications, such as heated garments and electromagnetic shielding.
Looking ahead, hybrid approaches that combine fiber integration with surface printing or coating are expected to dominate the market. This convergence allows manufacturers to balance conductivity, mechanical performance, and scalability. The integration of automated, roll-to-roll processing lines is anticipated to further reduce costs and increase throughput, making conductive textiles more accessible for mass-market applications.
Industry bodies such as the Associazione Italiana di Tecnologia Alimentare (AITA) and the Textile Institute are actively promoting research and standardization in this field, supporting collaboration between textile manufacturers and electronics companies. As the demand for smart textiles in healthcare, sports, and consumer electronics continues to rise, the next few years are likely to see significant advancements in both the performance and manufacturability of conductive textiles.
Competitive Landscape: Leading Companies and Strategic Partnerships
The competitive landscape of conductive textile development in 2025 is characterized by a dynamic interplay of established textile manufacturers, electronics giants, and innovative startups, all vying for leadership in a rapidly expanding market. The sector is witnessing a surge in strategic partnerships, mergers, and technology licensing agreements, as companies seek to accelerate product development and scale manufacturing capabilities.
Among the most prominent players, Toray Industries, Inc. continues to leverage its expertise in advanced fibers and materials, focusing on integrating conductive properties into textiles for applications ranging from wearable electronics to automotive interiors. Toray’s collaborations with electronics manufacturers and research institutions have enabled the company to refine its proprietary conductive yarns and fabrics, positioning it as a key supplier for next-generation smart textiles.
Similarly, Teijin Limited has intensified its efforts in the development of high-performance conductive fibers, targeting both healthcare and industrial markets. Teijin’s recent joint ventures with sensor technology firms underscore a broader industry trend: the convergence of textile engineering and digital electronics. These partnerships are expected to yield new product lines with enhanced sensing, heating, and data transmission capabilities over the next few years.
In Europe, TITV Greiz, a leading research institute and manufacturer, has been instrumental in advancing textile-integrated electronics. The organization’s collaborations with both SMEs and multinational corporations have resulted in several commercialized conductive textile solutions, particularly for medical monitoring and protective clothing. TITV Greiz’s open innovation model is fostering a networked ecosystem, accelerating the translation of laboratory breakthroughs into market-ready products.
On the electronics side, Samsung Electronics has expanded its smart textile initiatives, investing in R&D and forming alliances with textile producers to embed sensors and conductive pathways directly into fabrics. Samsung’s focus on wearable health monitoring and connected apparel is expected to drive significant demand for advanced conductive textiles through 2025 and beyond.
Startups and specialized firms, such as Textronics, Inc., are also making notable contributions, particularly in the development of stretchable and washable conductive fabrics. These companies often serve as innovation partners for larger brands, supplying proprietary materials or co-developing end-use products.
Looking ahead, the competitive landscape is likely to see further consolidation, with leading players forming cross-sector alliances to address technical challenges and regulatory requirements. The integration of sustainable materials and scalable manufacturing processes will be key differentiators, as companies strive to meet the growing demand for high-performance, eco-friendly conductive textiles in consumer, medical, and industrial applications.
Regulatory Standards and Industry Certifications
The regulatory landscape for conductive textiles is evolving rapidly as the sector matures and applications proliferate in medical, automotive, military, and consumer electronics. In 2025, the focus is on harmonizing standards to ensure safety, reliability, and interoperability of conductive textile products across global markets. Key regulatory frameworks are being shaped by both international and regional bodies, with active participation from leading manufacturers and industry consortia.
One of the most significant developments is the ongoing revision of the IEC 62899 series, which addresses printed electronics, including conductive textiles. The International Electrotechnical Commission (International Electrotechnical Commission) is working to expand these standards to cover durability, washability, and electrical performance specific to textile substrates. This is particularly relevant for companies like Toray Industries and Teijin Limited, both of which are major suppliers of advanced fibers and have invested in smart textile R&D.
In the European Union, the CE marking remains a critical requirement for conductive textiles entering the market, especially those intended for medical or personal protective equipment (PPE) applications. The European Committee for Standardization (CEN) and the European Committee for Electrotechnical Standardization (CENELEC) are collaborating to update EN standards to address the unique challenges of integrating electronics into flexible fabrics. This includes new test protocols for biocompatibility and electromagnetic compatibility (EMC), which are essential for products developed by companies such as Schoeller Textiles AG and W. L. Gore & Associates.
In the United States, the American Association of Textile Chemists and Colorists (AATCC) and ASTM International (ASTM International) are leading efforts to establish standardized test methods for conductivity, durability, and safety of e-textiles. These standards are being adopted by manufacturers such as DuPont, which produces conductive inks and fibers, and Textronics, Inc., a pioneer in wearable textile electronics.
Looking ahead, industry certifications such as OEKO-TEX® Standard 100 and ISO 9001 are increasingly being sought by conductive textile producers to demonstrate product safety and quality management. The next few years are expected to see the introduction of new certification schemes tailored specifically for smart and conductive textiles, reflecting the sector’s growing complexity and the need for traceability in supply chains. As regulatory requirements tighten, collaboration between manufacturers, standards bodies, and end-users will be crucial to ensure that conductive textiles meet both performance and compliance expectations worldwide.
Sustainability and Environmental Impact in Conductive Textile Production
The development of conductive textiles in 2025 is increasingly shaped by sustainability imperatives and environmental considerations. As the demand for smart textiles grows across sectors such as healthcare, automotive, and consumer electronics, manufacturers are under pressure to minimize the ecological footprint of both materials and processes. Traditional conductive textiles often rely on metal-based coatings or synthetic polymers, which can pose challenges in terms of recyclability and resource consumption. In response, industry leaders are investing in greener alternatives and circular production models.
One notable trend is the adoption of bio-based and recycled fibers as substrates for conductive coatings. Companies like Toray Industries and Teijin Limited—both major global textile manufacturers—have announced initiatives to integrate recycled polyester and plant-derived fibers into their advanced textile lines, including those intended for electronic applications. These efforts are complemented by research into biodegradable conductive polymers and inks, which aim to reduce the persistence of e-waste in landfills.
The environmental impact of metallization processes is also under scrutiny. Traditional methods such as electroplating and sputtering can be energy-intensive and generate hazardous byproducts. In 2025, companies like Kuraray Co., Ltd. are piloting water-based and low-temperature deposition techniques to reduce emissions and chemical usage. Additionally, Lenzing AG, known for its sustainable cellulosic fibers, is collaborating with electronics partners to develop conductive textiles that leverage their closed-loop production systems, which recycle water and solvents.
Industry bodies such as the Textile Exchange are playing a pivotal role by establishing standards and certification schemes for sustainable textile production, including criteria specific to smart and functional fabrics. These frameworks encourage transparency in sourcing, processing, and end-of-life management, pushing the sector toward more responsible practices.
Looking ahead, the outlook for sustainable conductive textile development is promising. The convergence of regulatory pressure, consumer demand for eco-friendly products, and technological innovation is expected to accelerate the adoption of green materials and cleaner manufacturing processes. Companies that can demonstrate reduced carbon footprints, recyclability, and non-toxicity in their conductive textile offerings are likely to gain a competitive edge as the market matures over the next several years.
Challenges and Barriers: Technical, Economic, and Supply Chain Issues
The development of conductive textiles—fabrics integrated with electrically conductive materials—faces a complex array of challenges and barriers as the sector moves through 2025 and into the coming years. These obstacles span technical, economic, and supply chain domains, each influencing the pace and scale of innovation and commercialization.
Technical Challenges remain at the forefront. Achieving reliable conductivity while maintaining the flexibility, durability, and comfort expected of textiles is a persistent hurdle. Many conductive textiles rely on coatings or embedded fibers of metals such as silver, copper, or stainless steel. However, these materials can degrade with repeated washing, flexing, or exposure to environmental factors, leading to diminished performance over time. Companies like Toray Industries and Shin Kong Textile are actively researching advanced fiber blends and coating techniques to address these issues, but scalable solutions that balance conductivity, washability, and wearability remain elusive.
Another technical barrier is the integration of conductive elements with traditional textile manufacturing processes. Standard weaving, knitting, and finishing equipment are often not optimized for handling conductive fibers or coatings, leading to production inefficiencies and quality control issues. W. L. Gore & Associates, known for its expertise in functional fabrics, is among the companies investing in process innovation to enable more seamless integration of conductive materials.
Economic Barriers are equally significant. The cost of high-purity conductive materials, especially silver, remains elevated and volatile, impacting the price competitiveness of conductive textiles compared to conventional fabrics. While some manufacturers are exploring alternatives such as carbon-based or polymeric conductors, these often present trade-offs in terms of conductivity or durability. The need for specialized manufacturing equipment and quality assurance protocols further increases capital and operational expenditures, making it challenging for smaller firms to enter the market or scale production.
Supply Chain Issues have become more pronounced in the wake of global disruptions. Sourcing consistent, high-quality conductive fibers or coatings is complicated by limited supplier bases and geopolitical uncertainties. For example, Laird Performance Materials and Bekaert are among the few established suppliers of specialty conductive yarns and fibers, leading to potential bottlenecks. Additionally, the need for traceability and compliance with environmental and safety standards adds further complexity to the supply chain.
Looking ahead, overcoming these challenges will require coordinated efforts across the value chain. Industry leaders are expected to invest in R&D for more robust materials, foster partnerships to streamline manufacturing, and diversify supplier networks. As regulatory and consumer demands for sustainable and high-performance smart textiles grow, addressing these barriers will be critical for the sector’s expansion through 2025 and beyond.
Future Outlook: Disruptive Technologies and Long-Term Market Opportunities
The development of conductive textiles is poised for significant transformation in 2025 and the years immediately following, driven by advances in materials science, manufacturing processes, and integration with digital technologies. Conductive textiles—fabrics embedded or coated with conductive materials such as silver, carbon, or conductive polymers—are increasingly central to the evolution of smart wearables, medical devices, and next-generation automotive interiors.
A key driver of innovation is the ongoing refinement of fiber-level integration techniques. Companies like Toray Industries, a global leader in advanced materials, are investing in scalable methods to embed conductive elements directly into fibers, rather than relying solely on surface coatings. This approach enhances durability, washability, and electrical performance, addressing longstanding barriers to mass adoption in consumer and industrial applications.
In 2025, the convergence of conductive textiles with flexible electronics is expected to accelerate, enabling seamless integration of sensors, energy storage, and communication modules into garments and soft furnishings. Teijin Limited, another major Japanese materials innovator, is actively developing textile platforms that combine high conductivity with comfort and mechanical resilience, targeting both healthcare monitoring and sports performance markets.
Automotive and mobility sectors are also emerging as significant growth areas. Seiren Co., Ltd., a Japanese manufacturer specializing in functional textiles, is collaborating with automotive OEMs to develop seat fabrics and interior panels with embedded heating, lighting, and touch-sensitive controls. These innovations are expected to reach commercial maturity by 2026, aligning with broader trends toward connected and personalized vehicle interiors.
On the supply side, companies such as Laird Performance Materials are expanding their portfolios of conductive yarns and coatings, focusing on electromagnetic shielding and signal transmission for high-reliability applications. The push for sustainable and recyclable conductive textiles is also gaining momentum, with industry leaders exploring bio-based polymers and environmentally friendly metallization processes.
Looking ahead, the next few years will likely see disruptive advances in large-scale, cost-effective manufacturing of conductive textiles, supported by automation and digital quality control. The integration of artificial intelligence for real-time monitoring of textile performance is anticipated to further enhance product reliability and open new market opportunities, particularly in medical diagnostics and adaptive clothing.
- Fiber-level integration and advanced coatings will drive durability and performance.
- Healthcare, automotive, and sportswear are key near-term growth sectors.
- Sustainability and recyclability are becoming central to R&D efforts.
- AI and digital manufacturing will underpin future scalability and customization.
Sources & References
- Teijin Limited
- TITV Greiz
- Laird Performance Materials
- Schoeller Textiles
- NV Bekaert SA
- Interactive Wear AG
- Seiren Co., Ltd.
- Shinkong Synthetic Fibers Corporation
- DuPont
- Associazione Italiana di Tecnologia Alimentare (AITA)
- Textile Institute
- CEN
- CENELEC
- W. L. Gore & Associates
- AATCC
- ASTM International
- Kuraray Co., Ltd.
- Lenzing AG
- Textile Exchange