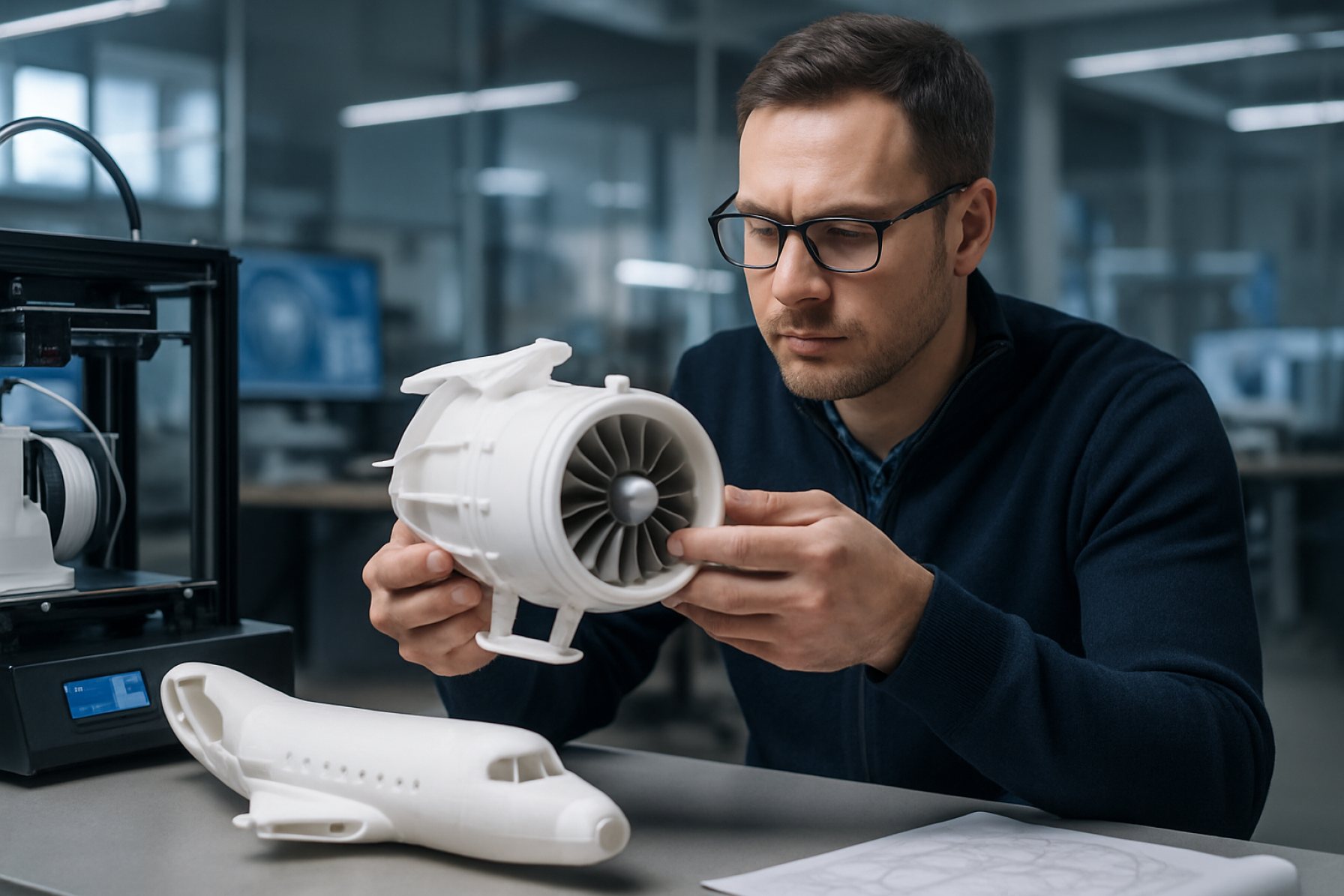
Wie Rapid Prototyping die Entwicklung von Luftfahrtkomponenten im Jahr 2025 transformiert: Schnellere Innovationen, geringere Kosten und ein prognostiziertes CAGR von 14% bis 2029 freischalten
- Zusammenfassung: Wichtige Trends und Markttreiber im Jahr 2025
- Marktgröße und Wachstumsprognose (2025–2029): Quantifizierung der Gelegenheit
- Kerntechnologien: 3D-Druck, CNC-Bearbeitung und hybride Ansätze
- Materialinnovationen: Hochleistungslegierungen, Verbundwerkstoffe und Polymere
- Übernahme durch führende Luftfahrt-OEMs und Tier-1-Zulieferer
- Regulatorische und Zertifizierungsherausforderungen für prototypisierte Komponenten
- Fallstudien: Erfolgreiches Rapid Prototyping in Flugzeugen und Raumfahrzeugen
- Wettbewerbsumfeld: Hauptakteure und strategische Partnerschaften
- Zukünftige Ausblicke: Neue Technologien und Marktentwicklungen
- Empfehlungen: Strategische Maßnahmen für Akteure im Jahr 2025 und darüber hinaus
- Quellen & Referenzen
Zusammenfassung: Wichtige Trends und Markttreiber im Jahr 2025
Im Jahr 2025 transformiert Rapid Prototyping weiterhin den Sektor der Luftfahrtkomponenten, angetrieben von der Notwendigkeit beschleunigter Innovation, Kosteneffizienz und verbesserter Designflexibilität. Der Einsatz fortschrittlicher Technologien der additiven Fertigung (AM), wie z. B. selektives Laserschmelzen (SLM), Elektronenstrahlschmelzen (EBM) und direktes Metallschichtsintern (DMLS), ermöglicht es Herstellern in der Luftfahrt, Designs schnell zu überarbeiten und komplexe Geometrien zu produzieren, die zuvor mit traditionellen Methoden nicht möglich waren. Diese Verschiebung ist besonders deutlich bei führenden Luftfahrt-OEMs und -Zulieferern zu erkennen, die Rapid Prototyping nutzen, um Entwicklungszyklen zu verkürzen und neue Produkte schneller auf den Markt zu bringen.
Wichtige Akteure der Branche wie Airbus und Boeing haben Rapid Prototyping in ihre Produktentwicklungspipelines integriert und nutzen es für sowohl funktionale Tests als auch die Produktion flugbereiter Komponenten. Zum Beispiel hat Airbus signifikante Verkürzungen der Lieferzeiten für komplexe Teile gemeldet, während Boeing weiterhin seine Nutzung von AM für leichte Strukturkomponenten und Kabinenelemente ausbaut. Diese Fortschritte werden durch Kooperationen mit Technologieanbietern wie GE Aerospace unterstützt, die den Einsatz von additive Manufacturing für kritische Triebwerksbestandteile, einschließlich Brennerdüsen und Wärmetauschern, vorangetrieben haben.
Der Markt verzeichnet auch zunehmende Investitionen in digitale Design- und Simulationswerkzeuge, die Rapid Prototyping ergänzen, indem sie virtuelle Tests und Optimierungen ermöglichen, bevor physische Modelle produziert werden. Unternehmen wie Siemens bieten integrierte Softwarelösungen an, die den Übergang von digitalen Modellen zu physischen Prototypen straffen, was den Entwicklungsprozess weiter beschleunigt und das Risiko kostspieliger Konstruktionsfehler verringert.
Materialinnovationen bleiben ein wichtiger Treiber, wobei Luftfahrtzulieferer wie Honeywell und Safran neue Hochleistungslegierungen und Verbundwerkstoffe erforschen, die auf additive Fertigung zugeschnitten sind. Diese Materialien bieten verbesserte Festigkeits-Gewicht-Verhältnisse und Wärmebeständigkeit und erfüllen die strengen Anforderungen an Luftfahrtanwendungen, während sie effizientere Prototyping-Workflows ermöglichen.
Mit Blick auf die Zukunft ist der Ausblick für Rapid Prototyping in der Luftfahrt robust. Der Sektor wird voraussichtlich ein weiteres Wachstum bei der Übernahme von AM-Technologien erleben, angetrieben durch fortlaufende Fortschritte in den Maschinenfähigkeiten, der Materialwissenschaft und der digitalen Integration. Mit der Verfeinerung der Zertifizierungspfad von Regulierungsbehörden wie der Federal Aviation Administration und der Europäischen Raumfahrtagentur für additiv gefertigte Komponenten wird die Übergang von Prototyping zur Serienproduktion voraussichtlich beschleunigt, was Rapid Prototyping als Grundpfeiler der Luftfahrtinnovation bis 2025 und darüber hinaus festigt.
Marktgröße und Wachstumsprognose (2025–2029): Quantifizierung der Gelegenheit
Der Markt für Rapid Prototyping von Luftfahrtkomponenten steht zwischen 2025 und 2029 vor robustem Wachstum, angetrieben durch die beschleunigte Übernahme von additiver Fertigung (AM), digitalem Design und fortschrittlichen Materialien in den kommerziellen und militärischen Luftfahrtsektoren. Ab 2025 priorisiert die globale Luftfahrtindustrie weiterhin Rapid Prototyping, um Entwicklungszyklen zu verkürzen, Kosten zu senken und die Produktion komplexer, leichter Teile zu ermöglichen, die strengen regulatorischen und Leistungsanforderungen entsprechen.
Wichtige Luftfahrt-/Hersteller und -zulieferer erhöhen ihre Investitionen in Rapid Prototyping-Technologien. Boeing und Airbus haben beide die additive Fertigung und Rapid Prototyping in ihre Produktentwicklungspipelines integriert, wobei heute Hunderte von 3D-gedruckten Teilen auf kommerziellen und militärischen Plattformen im Einsatz sind. GE Aerospace erweitert weiterhin seine Nutzung von Rapid Prototyping für jettriebwerkskomponenten und nutzt dabei sein globales Netzwerk an Anlagen der additiven Fertigung. Lockheed Martin und Northrop Grumman treiben ebenfalls Rapid Prototyping sowohl für strukturelle als auch für Antriebstechnik voran, insbesondere bei Systemen für nächste Generation von Kämpferflugzeugen und Raumfahrt.
Die Marktchancen werden durch das wachsende Ökosystem von spezialisierten Zulieferern weiter unterstrichen. Stratasys, ein führendes Unternehmen im Bereich von Polymer-3D-Druck, und 3D Systems, das sowohl Polymer- als auch Metall-AM-Lösungen anbietet, erweitern ihre Luftfahrtportfolios. Renishaw und EOS sind bemerkenswert für ihre metallischen additiven Fertigungssysteme, die zunehmend für Flughardware zertifiziert werden. Diese Unternehmen arbeiten mit OEMs und Tier-1-Zulieferern zusammen, um die Qualifizierung neuer Materialien und Prozesse zu beschleunigen, was ein entscheidender Voraussetzung für das Marktwachstum ist.
Quantitativ wird erwartet, dass das Segment Rapid Prototyping in der Luftfahrt die allgemeinen industriellen AM-Wachstumsraten übertreffen wird, wobei ein jährliches Wachstum im hohen einstelligen bis niedrigen zweistelligen Bereich bis 2029 prognostiziert wird. Dies wird durch steigende Flugzeugproduktionsraten, die Notwendigkeit schnellerer Iterationen im Design und Testen und den Drang nach Nachhaltigkeit durch Materialeffizienz und Teilekonsolidierung vorangetrieben. Der Verteidigungssektor wird dabei voraussichtlich einen wesentlichen Antrieb darstellen, da Regierungen in agile Entwicklungen und die Aufrechterhaltung fortschrittlicher Luft- und Raumfahrtplattformen investieren.
Mit Blick auf die Zukunft wird der Markt von fortlaufenden Fortschritten in digitalem Engineering, Automatisierung und Zertifizierungsstandards profitieren. Die Integration von Rapid Prototyping mit digitalen Zwillingen und modellbasierten Systemingenieuren wird voraussichtlich die Entwicklungszeiten weiter verkürzen und neue Designmöglichkeiten eröffnen. Da Luftfahrt-OEMs und -Zulieferer ihre Übernahme von Rapid Prototyping vertiefen, hat der Sektor die Chance, einen wachsend Anteil am globalen Markt für additive Fertigung zu erfassen und seine Rolle als Grundpfeiler der nächsten Generation von Luftfahrtinnovation zu festigen.
Kerntechnologien: 3D-Druck, CNC-Bearbeitung und hybride Ansätze
Rapid Prototyping für Luftfahrtkomponenten im Jahr 2025 wird durch die Konvergenz von fortschrittlichem 3D-Druck (additive Fertigung), präziser CNC-Bearbeitung und aufkommenden hybriden Fertigungsansätzen definiert. Diese Kerntechnologien eröffnen schnellere Designiteration, reduzierte Lieferzeiten und die Produktion komplexer Geometrien, die zuvor mit traditionellen Methoden nicht möglich waren.
3D-Druck (Additive Fertigung) bleibt eine transformative Kraft im Prototyping der Luftfahrt. Haupt-Luftfahrt-OEMs und -Zulieferer nutzen metallische additive Fertigung sowohl für Prototypen als auch für Endverwendungsprodukte. GE Aerospace hat seine Nutzung von Laserpulverbettfusion und Elektronenstrahlschmelzen ausgeweitet, um schnell jettriebwerkskomponenten zu prototypisieren und zu validieren, wobei die Entwicklungszyklen von Monaten auf Wochen verkürzt werden. Airbus nutzt ebenfalls additive Fertigung für strukturelle und Kabinenkomponenten, mit einem Fokus auf Gewichtsreduktion und Teilekonsolidierung. Die Übernahme von Hochleistungsmaterialien wie Titan und Inconel-Legierungen beschleunigt sich, angetrieben durch die Notwendigkeit der Optimierung des Verhältnisses von Festigkeit zu Gewicht und Wärmebeständigkeit.
Im Jahr 2025 erlebt die Branche die Reifung von großformatigen additiven Systemen, die es ermöglichen, größere Baugruppen wie Triebwerksträger und Rumpfabschnitte zu prototypisieren. Stratasys und EOS sind unter den Technologieanbietern, die Mehrmaterial- und Hochdruckdruckfähigkeiten vorantreiben und die schnelle Iteration sowohl von metallischen als auch von polymerbasierten Luftfahrzeugen unterstützen.
CNC-Bearbeitung bleibt für Rapid Prototyping unverzichtbar, insbesondere für hochpräzise, enge Toleranzkomponenten. Luftfahrtzulieferer investieren in 5-Achsen- und Mehrzweck-CNC-Maschinen, um die Produktion komplexer Prototypen aus Luftfahrtlegierungen zu beschleunigen. Haas Automation und DMG MORI sind prominente Hersteller, deren Geräte in Luftfahrt-Prototypenwerkstätten weit verbreitet sind. CNC-Bearbeitung wird häufig für die Nachbearbeitung von 3D-gedruckten Teilen eingesetzt, um sicherzustellen, dass kritische Oberflächen strengen Luftfahrtstandards entsprechen.
Hybride Fertigungsansätze, die additive und subtraktive Prozesse kombinieren, gewinnen an Bedeutung. Diese Systeme ermöglichen den additiven Aufbau von fast netto-formteiligen Teilen, gefolgt von präziser CNC-Finishing. Yamazaki Mazak und TRUMPF entwickeln hybride Maschinen, die laserbasiertes Metalldeposition mit CNC-Fräsen integrieren und das schnelle Prototyping komplexer, wertvoller Luftfahrtkomponenten mit reduziertem Materialabfall und verbesserten mechanischen Eigenschaften ermöglichen.
Mit Blick auf die Zukunft wird die Integration von digitalem Design, Simulation und Fertigungsabläufen voraussichtlich das Rapid Prototyping weiter straffen. Die fortlaufende Investition des Luftfahrtsektor in diese Kerntechnologien wird dazu beitragen, noch kürzere Entwicklungszyklen, größere Designfreiheit und eine verbesserte Validierung der Leistungsfähigkeit für Luft- und Raumfahrtkomponenten der nächsten Generation bis 2025 und darüber hinaus zu fördern.
Materialinnovationen: Hochleistungslegierungen, Verbundwerkstoffe und Polymere
Rapid Prototyping transformiert die Entwicklung von Luftfahrtkomponenten, wobei Materialinnovationen in hochleistungsfähigen Legierungen, Verbundwerkstoffen und Polymeren eine zentrale Rolle im Jahr 2025 und darüber hinaus spielen. Die Nachfrage des Luftfahrtsektors nach leichteren, stärkeren und wärmeresistenten Materialien treibt die Übernahme neuer Rapid Prototyping-Techniken voran, insbesondere der additiven Fertigung (AM), die die Verwendung dieser fortschrittlichen Materialien in komplexen Geometrien ermöglicht, die zuvor durch traditionelle Fertigung nicht erreichbar waren.
Im Jahr 2025 nutzen führende Luftfahrt-Hersteller Rapid Prototyping, um das Design und die Prüfung von Komponenten aus Hochleistungslegierungen wie Titanaluminiden und nickelbasierten Superlegierungen zu beschleunigen. Zum Beispiel hat GE Aerospace seine Nutzung von additiver Fertigung für Teile von jettriebwerken ausgeweitet und dabei proprietäre Legierungen verwendet, die überlegene Festigkeits-Gewicht-Verhältnisse und thermische Stabilität bieten. Diese Materialien sind entscheidend für zukünftige Triebwerke, bei denen Effizienz und Emissionsreduzierung von größter Bedeutung sind.
Verbundwerkstoffe befinden sich ebenfalls an der Spitze der Fortschritte beim Rapid Prototyping. Unternehmen wie Boeing und Airbus integrieren kohlenstofffaserverstärkte Polymere (CFRPs) und thermoplastische Verbundwerkstoffe in ihre Prototyping-Workflows. Diese Materialien ermöglichen die Produktion von leichten Strukturkomponenten mit hoher Ermüdungsbeständigkeit, die für kommerzielle und militärische Luftfahrtanwendungen entscheidend sind. Der Einsatz automatisierter Faserplatzierung (AFP) und 3D-Drucktechnologien ermöglicht eine schnelle Iteration und Anpassung von Verbundteilen, wodurch die Lieferzeiten von Monaten auf Wochen verkürzt werden.
Polymere, insbesondere Hochleistungs-Thermoplasten wie PEEK und PEKK, werden zunehmend im Rapid Prototyping für nicht-strukturelle und halbstrukturelle Luftfahrtkomponenten verwendet. Stratasys, ein führendes Unternehmen für Polymer-Additive-Fertigung, hat mit Luftfahrtzulieferern zusammengearbeitet, um neue Materialien und Prozesse zu qualifizieren, die strengen Branchenstandards für Flamme, Rauch und Toxizität entsprechen. Diese Fortschritte ermöglichen das Rapid Prototyping von Kabineninneneinrichtungen, Lüftungsleitungen und anderen Komponenten, bei denen Gewichtsersparnis und die Einhaltung von Vorschriften entscheidend sind.
Mit Blick auf die Zukunft ist der Ausblick für Rapid Prototyping in der Luftfahrt durch fortlaufende Materialinnovationen und Prozessintegration gekennzeichnet. Die Konvergenz von digitalem Design, fortschrittlichen Materialien und additiver Fertigung wird voraussichtlich die Entwicklungszyklen weiter verkürzen und agilere Reaktionen auf sich entwickelnde Anforderungen im Luftfahrtsektor ermöglichen. Industrieverbände wie SAE International entwickeln aktiv Standards, um die Qualifizierung und Zertifizierung von schnell prototypisierten Komponenten zu unterstützen und somit Sicherheit und Zuverlässigkeit zu gewährleisten, während die Übernahme bis 2025 und in die spätere Dekade beschleunigt wird.
Übernahme durch führende Luftfahrt-OEMs und Tier-1-Zulieferer
Die Übernahme von Rapid Prototyping-Technologien durch führende Luftfahrt-OEMs und Tier-1-Zulieferer hat im Jahr 2025 erheblich zugenommen, angetrieben von der Notwendigkeit schnellerer Entwicklungszyklen, Kosteneffizienz und der zunehmenden Komplexität von Luftfahrzeugen und Raumfahrzeugen der nächsten Generation. Wichtige Branchenakteure nutzen additive Fertigung (AM), fortschrittliche CNC-Bearbeitung und hybride Prototyping-Methoden, um den Design-zu-Produktion-Prozess kritischer Komponenten zu optimieren.
Airbus erweitert weiterhin die Nutzung von Rapid Prototyping in seinen kommerziellen und militärischen Programmen. Im Jahr 2025 hat Airbus die fortschrittliche metallische additive Fertigung für sowohl strukturelle als auch Kabinenkomponenten integriert, was schnellere Iterationen und Validierungen von Teilen wie Halterungen, Luftkanälen und sogar tragenden Elementen ermöglicht. Die Standorte in Filton und Hamburg haben berichtet, dass die Lieferzeiten für Prototypen von mehreren Wochen auf nur wenige Tage verkürzt wurden, was die agile Entwicklung für die Familien A320neo und A350 unterstützt.
Boeing hat ebenfalls seine Rapid Prototyping-Fähigkeiten skaliert, insbesondere zur Unterstützung seiner ecoDemonstrator- und neuer kommerzieller Luftfahrzeuge. Die Nutzung von Rapid Prototyping durch Boeing erstreckt sich sowohl auf Polymer- als auch auf Metall-AM, mit einem Fokus auf funktionale Tests und flugbereite Hardware. Die Partnerschaften des Unternehmens mit führenden AM-Ausrüstungsanbietern und Materialentwicklern haben die Produktion komplexer Geometrien und leichter Strukturen ermöglicht, die nun für die Nutzung in kommerziellen und militärischen Plattformen validiert werden.
Unter den Tier-1-Zulieferern sind Safran und GE Aerospace führend bei der Übernahme von Rapid Prototyping. Safran hat digitale Thread- und Rapid Prototyping-Workflows für Triebwerkskomponenten, Fahrwerke und Avionikgehäuse implementiert, was zu erheblichen Verkürzungen der Entwicklungszeit und einer verbesserten Designflexibilität geführt hat. GE Aerospace, ein Pionier in der additiven Fertigung von jettriebwerkskomponenten, hat seine Prototyping-Operationen um hybride Fertigung und schnelles Werkzeuging erweitert, um sowohl neue Triebwerksprogramme als auch Lösungen für den Aftermarket zu unterstützen.
Die Aussichten für die nächsten Jahre deuten auf eine weitere Integration von Rapid Prototyping in die mainstream Luftfahrtfertigung hin. OEMs und Zulieferer investieren in größere AM-Systeme, Mehrmaterialfähigkeiten und digitale Simulationswerkzeuge, um end-to-end digitale Prototypen zu ermöglichen. Branchenverbände wie SAE International aktualisieren Standards, um die wachsende Rolle des Rapid Prototyping in Zertifizierungs- und Qualifizierungsprozessen widerzuspiegeln. Infolgedessen steht der Luftfahrtsektor vor der Möglichkeit, durch die fortgesetzte Übernahme von Rapid Prototyping-Technologien noch größere Agilität, Innovation und Kosteneinsparungen zu erreichen.
Regulatorische und Zertifizierungsherausforderungen für prototypisierte Komponenten
Die rasante Übernahme von Prototyping-Technologien, insbesondere der additiven Fertigung (AM), in der Luftfahrt verändert 2025 die regulatorische und Zertifizierungslandschaft. Da Luftfahrt-Hersteller zunehmend Rapid Prototyping für sowohl metallische als auch polymerische Komponenten nutzen, arbeiten Regulierungsbehörden und Branchenakteure daran, Zertifizierungsrahmen anzupassen, um Sicherheit, Zuverlässigkeit und Rückverfolgbarkeit zu gewährleisten.
Eine der zentralen Herausforderungen ist die Ausrichtung der Rapid Prototyping-Prozesse auf strenge Luftfahrtzertifizierungsstandards. Traditionelle Zertifizierungspfade, wie sie von der Federal Aviation Administration (FAA) und der Europäischen Agentur für Flugsicherheit (EASA) definiert sind, wurden für konventionelle Fertigungsmethoden entwickelt. Diese Standards erfordern umfassende Dokumentation, Wiederholbarkeit und Material-Rückverfolgbarkeit – Bereiche, in denen Rapid Prototyping, insbesondere AM, neue Komplexität einführt. Zum Beispiel kann die Schicht-für-Schicht-Natur von AM zu einzigartigen Mikrostukturen und potenzieller Variabilität zwischen Builds führen, was neue Ansätze zur Prozessqualifizierung und Teilevalidierung erfordert.
Im Jahr 2025 arbeiten regulatorische Agenturen aktiv mit Branchengrößen zusammen, um spezifische Richtlinien für prototypisierte und additiv gefertigte Komponenten zu entwickeln und zu verfeinern. Die FAA aktualisiert weiterhin ihre Richtlinien zu AM und konzentriert sich auf Prozesskontrolle, Inspektion und Datenmanagement. Ebenso arbeitet die EASA mit Herstellern zusammen, um bewährte Verfahren für die Zertifizierung von AM-Teilen zu etablieren und betont die Notwendigkeit robuster Qualitätskontrolle und digitaler Aufzeichnungen.
Wichtige Luftfahrt-OEMs und -Zulieferer wie Boeing, Airbus und GE Aerospace sind Vorreiter dieser Bemühungen. Diese Unternehmen investieren in interne Zertifizierungsteams und digitale Infrastrukturen, um die Qualifizierung von prototypisierten Komponenten zu straffen. So hat GE Aerospace die Zertifizierung von 3D-gedruckten Brennerdüsen vorangetrieben und arbeitet weiterhin eng mit Regulierungsbehörden zusammen, um die Palette zertifizierbarer AM-Teile zu erweitern.
Branchensorganisationen wie SAE International und ASTM International spielen ebenfalls eine entscheidende Rolle, indem sie Konsensstandards für AM-Prozesse, Materialien und Testprotokolle entwickeln. Diese Standards werden zunehmend von Regulierungsbehörden und Herstellern zitiert, um die Konformität zu demonstrieren und den Zertifizierungsprozess zu erleichtern.
Mit Blick in die Zukunft ist der Ausblick für regulatorische und Zertifizierungsrahmen im Rapid Prototyping von vorsichtiger Optimismus geprägt. Während erhebliche Fortschritte erzielt wurden, wird eine fortlaufende Zusammenarbeit zwischen Regulierungsbehörden, Herstellern und Normungsstellen unerlässlich sein, um aufstrebende Technologien zu berücksichtigen und sicherzustellen, dass Sicherheit und Zuverlässigkeit weiterhin oberste Priorität haben, während Rapid Prototyping immer stärker in die Entwicklung von Luftfahrtkomponenten integriert wird.
Fallstudien: Erfolgreiches Rapid Prototyping in Flugzeugen und Raumfahrzeugen
In den letzten Jahren ist Rapid Prototyping zu einem Grundpfeiler der Innovation im Luftfahrtsektor geworden, der schnellere Entwicklungszyklen, Kosteneinsparungen und verbesserte Designflexibilität ermöglicht. Mehrere hochkarätige Fallstudien aus 2024 bis 2025 verdeutlichen den transformativen Einfluss dieser Technologien auf die Entwicklung von Komponenten sowohl für Flugzeuge als auch für Raumfahrzeuge.
Ein bemerkenswertes Beispiel ist die Nutzung der additiven Fertigung (AM) durch Airbus bei der Produktion von Strukturkomponenten für Verkehrsflugzeuge. Im Jahr 2024 meldete Airbus die erfolgreiche Integration von 3D-gedruckten Titan-Halterungen im A350 XWB, wodurch das Gewicht des Teils um bis zu 30 % reduziert und die Lieferzeiten für Komponenten verkürzt wurden. Das Unternehmen erweitert weiterhin seine Nutzung von Rapid Prototyping sowohl für Metall- als auch für Polymerteile, mit laufenden Projekten, die darauf abzielen, komplexere, tragende Strukturen für Flüge im Jahr 2025 zu zertifizieren.
Ebenso hat Boeing Rapid Prototyping genutzt, um die Entwicklung kritischer Systeme für seine nächste Flugzeuggeneration zu beschleunigen. 2024 verwendeten die Ingenieure von Boeing fortgeschrittenen 3D-Druck, um Luftkanäle des Klimakontrollsystems zu prototypisieren und zu testen, was zu einer 50%igen Reduzierung der Entwicklungszeit im Vergleich zu traditionellen Methoden führte. Das Unternehmen arbeitet auch mit Zulieferern zusammen, um neue Hochleistungsmaterialien für die additive Fertigung zu qualifizieren, mit dem Ziel, den Anteil der 3D-gedruckten Teile in zukünftigen Flugzeugmodellen zu erhöhen.
Im Bereich der Raumfahrttechnologie ist NASA führend im Rapid Prototyping von Raumfahrzeugkomponenten. Das Artemis-Programm, das auf Mondmissionen in der Mitte der 2020er Jahre abzielt, hat stark auf Rapid Prototyping gesetzt, um Designs für Teile von Raketentriebwerken, Crewmodule-Strukturen und Lebenserhaltungssysteme zu iterieren. 2024 testete NASA erfolgreich eine 3D-gedruckte Brennkammer für das RS-25-Triebwerk und demonstrierte die Leistungsgleichheit mit konventionell gefertigten Gegenstücken, während die Produktionszeit von Monaten auf Wochen verkürzt wurde.
Private Raumfahrtunternehmen übernehmen ebenfalls Rapid Prototyping. SpaceX hat additive Fertigung in die Produktion von SuperDraco-Triebwerken und anderen kritischen Komponenten für das Dragon-Raumschiff integriert. Die Rapid Prototyping-Fähigkeiten des Unternehmens ermöglichen schnelle Designiteration und beschleunigte Testzyklen, was zur Zuverlässigkeit und Wiederverwendbarkeit seiner Trägerraketen beiträgt.
Mit Blick auf 2025 und darüber hinaus wird erwartet, dass die Übernahme von Rapid Prototyping in der Luftfahrt zunehmen wird, angetrieben durch Fortschritte in der Materialwissenschaft, Prozessautomatisierung und digitalen Designwerkzeugen. Branchenführer investieren in umfangreiche additive Fertigungssysteme und digitale Zwillinge, um den Übergang von Prototyp zu zertifizierten Flughardware weiter zu optimieren. Während sich regulatorische Rahmenbedingungen weiterentwickeln, wird Rapid Prototyping ein wichtiger Enabler von Innovation und Wettbewerbsfähigkeit im Luftfahrtsektor bleiben.
Wettbewerbsumfeld: Hauptakteure und strategische Partnerschaften
Das Wettbewerbsumfeld für Rapid Prototyping im Luftfahrtsektor ist durch ein dynamisches Zusammenspiel etablierter Luftfahrt-Hersteller, fortschrittlicher Materialzulieferer und spezialisierter Anbieter von additiver Fertigung (AM)-Technologie gekennzeichnet. Im Jahr 2025 erlebt der Sektor eine intensivierte Zusammenarbeit und strategische Partnerschaften, die darauf abzielen, Innovationen zu beschleunigen, Lieferzeiten zu verkürzen und die Leistung kritischer Komponenten zu verbessern.
Haupt-Luftfahrt-OEMs wie Boeing und Airbus investieren weiterhin stark in Rapid Prototyping-Fähigkeiten, sowohl intern als auch durch Allianzen. Boeing hat seine Nutzung von additiver Fertigung für Prototypisierung und Kleinserienproduktion ausgeweitet und Partnerschaften mit führenden AM-Technologiefirmen genutzt, um die Entwicklung komplexer Teile für kommerzielle und militärische Plattformen zu optimieren. Ebenso hat Airbus Rapid Prototyping in sein digitales Fertigungssystem integriert und arbeitet mit Zulieferern zusammen, um die Qualifizierung neuer Materialien und Prozesse für flugkritische Komponenten zu beschleunigen.
Technologisch sind Unternehmen wie Stratasys und 3D Systems bedeutende Anbieter von industriellen 3D-Drucklösungen, die speziell für Luftfahrtanwendungen entwickelt wurden. Stratasys hat Partnerschaften mit Luftfahrtzulieferern etabliert, um hochleistungsfähige Polymer- und Verbundprototypen bereitzustellen, während 3D Systems sich auf metallische additive Fertigung für funktionsgerechte Prototypen und Werkzeuge konzentriert. Beide Unternehmen investieren in neue Materialien und Prozesszertifizierungen, um strengen Luftfahrtstandards gerecht zu werden.
Materialinnovation ist ein weiterer Wettbewerbsfaktor, wobei Firmen wie Honeywell und GE Aerospace sowohl als Endbenutzer als auch als Entwickler fortschrittlicher Legierungen und Verbundwerkstoffe für Rapid Prototyping tätig sind. GE Aerospace hat bemerkenswerte Fortschritte in der Nutzung der additiven Fertigung für die Prototypisierung von Triebwerkskomponenten erzielt, häufig in Zusammenarbeit mit AM-Spezialisten und Forschungseinrichtungen.
Strategische Partnerschaften gestalten zunehmend den Verlauf des Sektors. Beispielsweise hat Safran gemeinsame Entwicklungsvereinbarungen mit AM-Technologieanbietern geschlossen, um Rapid Prototyping-Lösungen für Antrieb und Fahrwerksysteme gemeinsam zu entwickeln. In ähnlicher Weise arbeitet Rolls-Royce mit einem Netzwerk von Zulieferern und Technologiepartnern zusammen, um die Prototypisierung und Validierung von Triebwerkskomponenten der nächsten Generation zu beschleunigen.
Mit Blick auf die Zukunft wird erwartet, dass sich das Wettbewerbsumfeld weiter um integrierte digitale Fertigungsplattformen konsolidiert, wobei bedeutende Akteure strategische Allianzen nutzen, um Lieferkettenresilienz, Zertifizierungsherausforderungen und die wachsende Nachfrage nach nachhaltigen Materialien anzugehen. In den nächsten Jahren wird es voraussichtlich zu einer Steigerung der Investitionen in Automatisierung, datengestützte Designs und Branchenübergreifende Partnerschaften kommen, wodurch Rapid Prototyping zu einem Grundpfeiler der Luftfahrtinnovation wird.
Zukünftige Ausblicke: Neue Technologien und Marktentwicklungen
Die Zukunft des Rapid Prototyping für Luftfahrtkomponenten ist durch bedeutende Transformationen geprägt, da aufkommende Technologien und Marktentwicklungen die Branchenlandschaft im Jahr 2025 und darüber hinaus umgestalten. Die Konvergenz von fortschrittlicher additive Fertigung (AM), digitalem Engineering und neuen Materialien beschleunigt das Tempo, mit dem Luftfahrtunternehmen komplexe Teile entwerfen, testen und iterieren können.
Ein zentraler Treiber ist die Reifung der metallischen additiven Fertigung, insbesondere der Laserpulverbettfusion (LPBF) und dem Elektronenstrahlschmelzen (EBM), die nun sowohl für Prototypen als auch für Endverwendungsprodukte eingesetzt werden. Haupt-Luftfahrt-OEMs wie Boeing und Airbus haben ihre internen AM-Fähigkeiten ausgeweitet und nutzen Rapid Prototyping, um die Lieferzeiten für kritische Teile zu reduzieren und agile Entwicklungszyklen zu unterstützen. So hat Airbus AM in seinen digitalen Design-zu-Produktion-Workflow integriert, um die schnelle Validierung neuer Geometrien und leichterer Strukturen für Flugzeuge der nächsten Generation zu ermöglichen.
Zulieferer wie GE Aerospace und Rolls-Royce investieren ebenfalls in Rapid Prototyping, um die Entwicklung fortschrittlicher Antriebssysteme zu beschleunigen. GE Aerospace hat die Nutzung von AM zur Prototypisierung und Produktion komplexer Triebwerkskomponenten wie Brennerdüsen und Wärmetauschern gezeigt, die von reduzierten Montageschritten und verbesserter Leistung profitieren. In der Zwischenzeit untersucht Rolls-Royce hybride Fertigungsansätze, die additive und subtraktive Prozesse kombinieren, um sowohl Geschwindigkeit als auch Präzision zu optimieren.
Die Übernahme von digitalen Zwillingen und simulationsgesteuerten Designs ist ein weiterer disruptiver Trend. Indem Unternehmen Rapid Prototyping mit Echtzeitdatenanalysen und virtuellen Tests integrieren, können sie Entwürfe schneller iterieren und die Anzahl physischer Prototypen verringern. NASA ist führend in diesem Ansatz, indem sie digitales Engineering verwendet, um das Prototyping von Raumfahrzeugkomponenten zu rationalisieren und die Leistung unter extremen Bedingungen zu validieren.
Mit Blick auf die Zukunft wird das Aufkommen neuer Materialien, wie z. B. Hochtemperaturpolymere, fortschrittliche Keramiken und funktionell gradierte Legierungen, die Möglichkeiten des Rapid Prototyping weiter erweitern. Unternehmen wie Stratasys und 3D Systems entwickeln spezialisierte AM-Plattformen, die auf Luftfahrtanwendungen abgestimmt sind und die Produktion von leichten, hochfesten Teilen mit komplexen inneren Strukturen unterstützen.
Da sich regulatorische Rahmenbedingungen weiterentwickeln, um die additive Fertigung und digitale Zertifizierungen zu berücksichtigen, wird im Luftfahrtsektor mit einer breiteren Übernahme von Rapid Prototyping sowohl für kommerzielle als auch für militärische Anwendungen gerechnet. In den nächsten Jahren wird voraussichtlich eine verstärkte Zusammenarbeit zwischen OEMs, Zulieferern und Technologieanbietern stattfinden, was die Innovation vorantreibt und die Markteinführungszeit neuer Luftfahrtkomponenten verkürzt.
Empfehlungen: Strategische Maßnahmen für Akteure im Jahr 2025 und darüber hinaus
Da Rapid Prototyping weiterhin die Entwicklung von Luftfahrtkomponenten transformiert, müssen Akteure strategische Maßnahmen ergreifen, um wettbewerbsfähig und innovativ im Jahr 2025 und darüber hinaus zu bleiben. Die folgenden Empfehlungen sind auf Luftfahrt-Hersteller, Zulieferer und Technologiepartner abgestimmt, die die Vorteile der Rapid Prototyping-Technologien maximieren möchten.
- In fortschrittliche additive Fertigungsfähigkeiten investieren: Luftfahrtunternehmen sollten Investitionen in hochmoderne additive Fertigungssysteme priorisieren, wie z. B. Laserpulverbettfusion und Elektronenstrahlschmelzen, die zunehmend für Prototypen und Endverwendungsprodukte genutzt werden. Führende Luftfahrt-OEMs wie Airbus und Boeing haben ihre internen AM-Fähigkeiten ausgebaut, um schnellere Iterationen und verkürzte Lieferzeiten für komplexe Komponenten zu ermöglichen.
- Zulieferer-Kooperation und digitale Integration stärken: Um Prototyping-Zyklen zu beschleunigen, sollten Akteure eine engere Zusammenarbeit mit Zulieferern und Technologiepartnern fördern. Digitale Plattformen und sichere Datenübertragungsprotokolle sind unerlässlich für den Austausch von Entwurfsdateien und Feedback in Echtzeit. Unternehmen wie Safran und GE Aerospace haben digitale Ökosysteme eingerichtet, um Prototyping- und Qualifizierungsprozesse in ihren Lieferketten zu optimieren.
- Agile Design- und Testmethoden übernehmen: Rapid Prototyping ermöglicht iterative Designs und Tests, wodurch das Risiko kostspieliger Änderungen in der späteren Phase verringert wird. Luftfahrtorganisationen sollten agile Entwicklungsrahmen implementieren, die Simulation, virtuelle Tests und physisches Prototyping integrieren. Rolls-Royce hat den Wert dieses Ansatzes demonstriert, indem es Rapid Prototyping genutzt hat, um neue Triebwerkskomponenten vor der Serienproduktion zu validieren.
- Priorität auf Weiterbildung und Talententwicklung setzen: Die Übernahme von Rapid Prototyping-Technologien erfordert eine kompetente Belegschaft, die in digitalem Design, AM-Prozessen und Qualitätssicherung geschult ist. Akteure sollten in Schulungsprogramme und Partnerschaften mit akademischen Institutionen investieren, um Fachkenntnisse in diesen Bereichen aufzubauen, wie es in Initiativen von Lockheed Martin und NASA zu sehen ist.
- Zertifizierungs- und Standardisierungsbemühungen priorisieren: Da sich die regulatorischen Anforderungen weiterentwickeln, müssen die Akteure mit Branchenverbänden zusammenarbeiten, um Standards für Rapid Prototyping in der Luftfahrt zu entwickeln und zu übernehmen. Die Teilnahme an Arbeitsgruppen, die von Organisationen wie SAE International und ANSI geleitet werden, wird dazu beitragen, sicherzustellen, dass neue Prototyping-Methoden Sicherheits- und Qualitätsstandards erfüllen.
Durch die Umsetzung dieser strategischen Maßnahmen können sich Luftfahrtakteure Rapid Prototyping zunutze machen, um Innovationen zu beschleunigen, Kosten zu senken und die Compliance in einer sich schnell entwickelnden technologischen Landschaft bis 2025 und in den kommenden Jahren aufrechtzuerhalten.
Quellen & Referenzen
- Airbus
- Boeing
- GE Aerospace
- Siemens
- Honeywell
- Europäische Raumfahrtagentur
- Lockheed Martin
- Northrop Grumman
- Stratasys
- 3D Systems
- Renishaw
- EOS
- Haas Automation
- DMG MORI
- Yamazaki Mazak
- TRUMPF
- GE Aerospace
- Europäische Agentur für Flugsicherheit
- ASTM International
- NASA
- Rolls-Royce
- ANSI