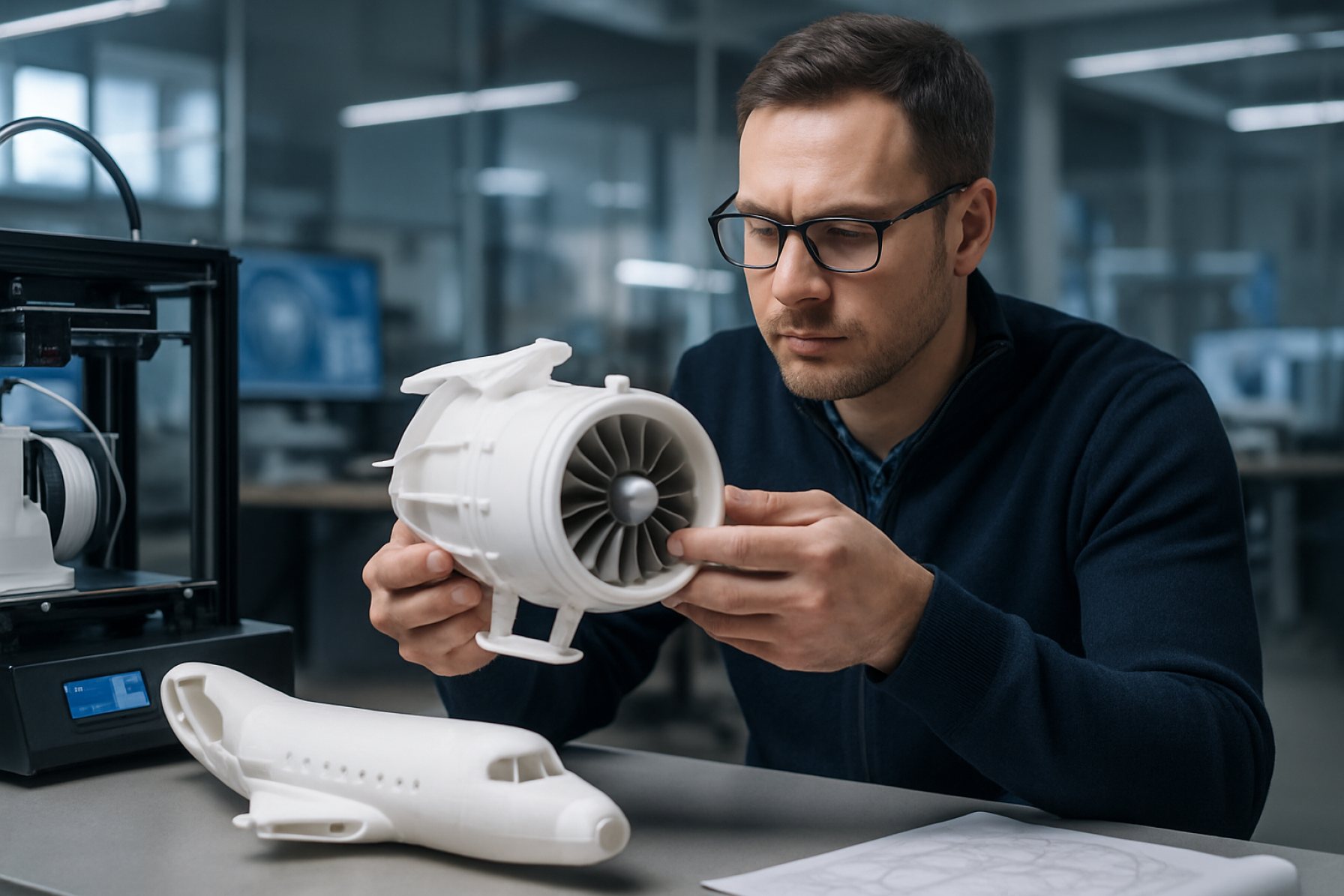
How Rapid Prototyping is Transforming Aerospace Component Development in 2025: Unlocking Faster Innovation, Lower Costs, and a Projected 14% CAGR Through 2029
- Executive Summary: Key Trends and Market Drivers in 2025
- Market Size and Growth Forecast (2025–2029): Quantifying the Opportunity
- Core Technologies: 3D Printing, CNC Machining, and Hybrid Approaches
- Material Innovations: Advanced Alloys, Composites, and Polymers
- Adoption by Leading Aerospace OEMs and Tier 1 Suppliers
- Regulatory and Certification Challenges for Prototyped Components
- Case Studies: Successful Rapid Prototyping in Aircraft and Spacecraft
- Competitive Landscape: Key Players and Strategic Partnerships
- Future Outlook: Emerging Technologies and Market Disruptors
- Recommendations: Strategic Actions for Stakeholders in 2025 and Beyond
- Sources & References
Executive Summary: Key Trends and Market Drivers in 2025
In 2025, rapid prototyping continues to transform the aerospace components sector, driven by the need for accelerated innovation, cost efficiency, and enhanced design flexibility. The adoption of advanced additive manufacturing (AM) technologies, such as selective laser melting (SLM), electron beam melting (EBM), and direct metal laser sintering (DMLS), is enabling aerospace manufacturers to iterate designs quickly and produce complex geometries that were previously unattainable with traditional methods. This shift is particularly evident among leading aerospace OEMs and suppliers, who are leveraging rapid prototyping to reduce development cycles and bring new products to market faster.
Key industry players such as Airbus and Boeing have integrated rapid prototyping into their product development pipelines, using it for both functional testing and the production of flight-ready components. For example, Airbus has reported significant reductions in lead times for complex parts, while Boeing continues to expand its use of AM for lightweight structural components and cabin interior elements. These advancements are supported by collaborations with technology providers such as GE Aerospace, which has pioneered the use of additive manufacturing for critical engine parts, including fuel nozzles and heat exchangers.
The market is also witnessing increased investment in digital design and simulation tools, which complement rapid prototyping by enabling virtual testing and optimization before physical models are produced. Companies like Siemens are providing integrated software solutions that streamline the transition from digital models to physical prototypes, further accelerating the development process and reducing the risk of costly design errors.
Material innovation remains a key driver, with aerospace suppliers such as Honeywell and Safran exploring new high-performance alloys and composites tailored for additive manufacturing. These materials offer improved strength-to-weight ratios and thermal resistance, meeting the stringent requirements of aerospace applications while enabling more efficient prototyping workflows.
Looking ahead, the outlook for rapid prototyping in aerospace is robust. The sector is expected to see continued growth in the adoption of AM technologies, driven by ongoing advancements in machine capabilities, material science, and digital integration. As regulatory bodies such as Federal Aviation Administration and European Space Agency refine certification pathways for additively manufactured components, the transition from prototyping to full-scale production is likely to accelerate, solidifying rapid prototyping as a cornerstone of aerospace innovation through 2025 and beyond.
Market Size and Growth Forecast (2025–2029): Quantifying the Opportunity
The rapid prototyping market for aerospace components is poised for robust growth between 2025 and 2029, driven by accelerating adoption of additive manufacturing (AM), digital design, and advanced materials across both commercial and defense aerospace sectors. As of 2025, the global aerospace industry continues to prioritize rapid prototyping to reduce development cycles, lower costs, and enable the production of complex, lightweight parts that meet stringent regulatory and performance requirements.
Key aerospace manufacturers and suppliers are scaling up investments in rapid prototyping technologies. Boeing and Airbus have both integrated additive manufacturing and rapid prototyping into their product development pipelines, with hundreds of 3D-printed parts now flying on commercial and military platforms. GE Aerospace continues to expand its use of rapid prototyping for jet engine components, leveraging its global network of additive manufacturing facilities. Lockheed Martin and Northrop Grumman are similarly advancing rapid prototyping for both structural and propulsion applications, particularly in next-generation fighter and space systems.
The market opportunity is further underscored by the growing ecosystem of specialized suppliers. Stratasys, a leader in polymer 3D printing, and 3D Systems, which offers both polymer and metal AM solutions, are expanding their aerospace portfolios. Renishaw and EOS are notable for their metal additive manufacturing systems, which are increasingly certified for flight hardware. These companies are collaborating with OEMs and Tier 1 suppliers to accelerate the qualification of new materials and processes, a key enabler for market growth.
Quantitatively, the rapid prototyping segment within aerospace is expected to outpace general industrial AM growth rates, with annual expansion projected in the high single to low double digits through 2029. This is fueled by rising aircraft production rates, the need for faster iteration in design and testing, and the push for sustainability through material efficiency and part consolidation. The defense sector, in particular, is anticipated to be a major driver, as governments invest in agile development and sustainment of advanced air and space platforms.
Looking ahead, the market will benefit from continued advances in digital engineering, automation, and certification standards. The integration of rapid prototyping with digital twins and model-based systems engineering is expected to further compress development timelines and unlock new design possibilities. As aerospace primes and suppliers deepen their adoption of rapid prototyping, the sector is set to capture a growing share of the global additive manufacturing market, solidifying its role as a cornerstone of next-generation aerospace innovation.
Core Technologies: 3D Printing, CNC Machining, and Hybrid Approaches
Rapid prototyping for aerospace components in 2025 is defined by the convergence of advanced 3D printing (additive manufacturing), precision CNC machining, and emerging hybrid manufacturing approaches. These core technologies are enabling faster design iterations, reduced lead times, and the production of complex geometries previously unattainable with traditional methods.
3D Printing (Additive Manufacturing) continues to be a transformative force in aerospace prototyping. Major aerospace OEMs and suppliers are leveraging metal additive manufacturing for both prototyping and end-use parts. GE Aerospace has expanded its use of laser powder bed fusion and electron beam melting to rapidly prototype and validate jet engine components, reducing development cycles from months to weeks. Airbus is similarly utilizing additive manufacturing for structural and cabin components, with a focus on lightweighting and part consolidation. The adoption of high-performance materials such as titanium and Inconel alloys is accelerating, driven by the need for strength-to-weight optimization and thermal resistance.
In 2025, the industry is witnessing the maturation of large-format additive systems, enabling the prototyping of bigger assemblies such as wing ribs and fuselage sections. Stratasys and EOS are among the technology providers advancing multi-material and high-speed printing capabilities, supporting the rapid iteration of both metallic and polymer-based aerospace parts.
CNC Machining remains indispensable for rapid prototyping, especially for high-precision, tight-tolerance components. Aerospace suppliers are investing in 5-axis and multi-tasking CNC machines to accelerate the production of complex prototypes from aerospace-grade alloys. Haas Automation and DMG MORI are prominent manufacturers whose equipment is widely used in aerospace prototyping shops. CNC machining is often employed for post-processing of 3D printed parts, ensuring critical surfaces meet stringent aerospace standards.
Hybrid Manufacturing Approaches—which combine additive and subtractive processes—are gaining traction. These systems allow for the additive build-up of near-net-shape parts, followed by precision CNC finishing. Yamazaki Mazak and TRUMPF are developing hybrid machines that integrate laser metal deposition with CNC milling, enabling the rapid prototyping of complex, high-value aerospace components with reduced material waste and improved mechanical properties.
Looking ahead, the integration of digital design, simulation, and manufacturing workflows is expected to further streamline rapid prototyping. The aerospace sector’s ongoing investment in these core technologies is set to drive even shorter development cycles, greater design freedom, and enhanced performance validation for next-generation aircraft and spacecraft components through 2025 and beyond.
Material Innovations: Advanced Alloys, Composites, and Polymers
Rapid prototyping is transforming the development of aerospace components, with material innovations in advanced alloys, composites, and polymers playing a pivotal role in 2025 and beyond. The aerospace sector’s demand for lighter, stronger, and more heat-resistant materials is driving the adoption of new rapid prototyping techniques, particularly additive manufacturing (AM), which enables the use of these advanced materials in complex geometries previously unattainable through traditional manufacturing.
In 2025, leading aerospace manufacturers are leveraging rapid prototyping to accelerate the design and testing of components made from high-performance alloys such as titanium aluminides and nickel-based superalloys. For example, GE Aerospace continues to expand its use of additive manufacturing for jet engine parts, utilizing proprietary alloys that offer superior strength-to-weight ratios and thermal stability. These materials are critical for next-generation engines, where efficiency and emissions reduction are paramount.
Composites are also at the forefront of rapid prototyping advancements. Companies like Boeing and Airbus are integrating carbon fiber-reinforced polymers (CFRPs) and thermoplastic composites into their prototyping workflows. These materials enable the production of lightweight structural components with high fatigue resistance, essential for both commercial and defense aerospace applications. The use of automated fiber placement (AFP) and 3D printing technologies allows for rapid iteration and customization of composite parts, reducing lead times from months to weeks.
Polymers, particularly high-performance thermoplastics such as PEEK and PEKK, are increasingly used in rapid prototyping for non-structural and semi-structural aerospace components. Stratasys, a leader in polymer additive manufacturing, has collaborated with aerospace suppliers to qualify new materials and processes that meet stringent industry standards for flame, smoke, and toxicity. These advancements are enabling the rapid prototyping of cabin interiors, ducting, and other components where weight savings and regulatory compliance are critical.
Looking ahead, the outlook for rapid prototyping in aerospace is marked by continued material innovation and process integration. The convergence of digital design, advanced materials, and additive manufacturing is expected to further reduce development cycles and enable more agile responses to evolving aerospace requirements. Industry bodies such as SAE International are actively developing standards to support the qualification and certification of rapidly prototyped components, ensuring safety and reliability as adoption accelerates through 2025 and into the latter part of the decade.
Adoption by Leading Aerospace OEMs and Tier 1 Suppliers
The adoption of rapid prototyping technologies by leading aerospace OEMs and Tier 1 suppliers has accelerated markedly in 2025, driven by the need for faster development cycles, cost efficiency, and the increasing complexity of next-generation aircraft and spacecraft. Major industry players are leveraging additive manufacturing (AM), advanced CNC machining, and hybrid prototyping methods to streamline the design-to-production process for critical components.
Airbus continues to expand its use of rapid prototyping across its commercial and defense programs. In 2025, Airbus has integrated advanced metal additive manufacturing for both structural and cabin components, enabling faster iteration and validation of parts such as brackets, air ducts, and even load-bearing elements. The company’s Filton and Hamburg sites have reported reductions in lead times for prototype parts from several weeks to just a few days, supporting agile development for the A320neo and A350 families.
Boeing has similarly scaled up its rapid prototyping capabilities, particularly in support of its ecoDemonstrator and new commercial aircraft initiatives. Boeing’s use of rapid prototyping extends to both polymer and metal AM, with a focus on functional testing and flight-ready hardware. The company’s partnerships with leading AM equipment suppliers and material developers have enabled the production of complex geometries and lightweight structures, which are now being validated for use in both commercial and defense platforms.
Among Tier 1 suppliers, Safran and GE Aerospace are at the forefront of rapid prototyping adoption. Safran has implemented digital thread and rapid prototyping workflows for engine components, landing gear, and avionics housings, resulting in significant reductions in development time and improved design flexibility. GE Aerospace, a pioneer in additive manufacturing for jet engine parts, has expanded its prototyping operations to include hybrid manufacturing and rapid tooling, supporting both new engine programs and aftermarket solutions.
The outlook for the next few years suggests further integration of rapid prototyping into mainstream aerospace manufacturing. OEMs and suppliers are investing in larger-format AM systems, multi-material capabilities, and digital simulation tools to enable end-to-end digital prototyping. Industry bodies such as SAE International are updating standards to reflect the growing role of rapid prototyping in certification and qualification processes. As a result, the aerospace sector is poised to achieve even greater agility, innovation, and cost savings through the continued adoption of rapid prototyping technologies.
Regulatory and Certification Challenges for Prototyped Components
The rapid adoption of prototyping technologies, particularly additive manufacturing (AM), in aerospace is reshaping the regulatory and certification landscape in 2025. As aerospace manufacturers increasingly leverage rapid prototyping for both metallic and polymer components, regulatory bodies and industry stakeholders are working to adapt certification frameworks to ensure safety, reliability, and traceability.
A primary challenge is the alignment of rapid prototyping processes with stringent aerospace certification standards. Traditional certification pathways, such as those defined by the Federal Aviation Administration (FAA) and the European Union Aviation Safety Agency (EASA), were developed for conventional manufacturing methods. These standards require comprehensive documentation, repeatability, and material traceability—areas where rapid prototyping, especially AM, introduces new complexities. For example, the layer-by-layer nature of AM can result in unique microstructures and potential variability between builds, necessitating new approaches to process qualification and part validation.
In 2025, regulatory agencies are actively collaborating with industry leaders to develop and refine guidelines specific to prototyped and additively manufactured components. The FAA continues to update its guidance on AM, focusing on process control, inspection, and data management. Similarly, EASA is working with manufacturers to establish best practices for the certification of AM parts, emphasizing the need for robust quality assurance and digital record-keeping.
Major aerospace OEMs and suppliers, such as Boeing, Airbus, and GE Aerospace, are at the forefront of these efforts. These companies are investing in in-house certification teams and digital infrastructure to streamline the qualification of prototyped components. For instance, GE Aerospace has pioneered the certification of 3D-printed fuel nozzles and continues to work closely with regulators to expand the range of certifiable AM parts.
Industry organizations such as SAE International and ASTM International are also playing a critical role by developing consensus standards for AM processes, materials, and testing protocols. These standards are increasingly referenced by regulators and manufacturers alike to demonstrate compliance and facilitate the certification process.
Looking ahead, the outlook for regulatory and certification frameworks in rapid prototyping is one of cautious optimism. While significant progress has been made, ongoing collaboration between regulators, manufacturers, and standards bodies will be essential to address evolving technologies and ensure that safety and reliability remain paramount as rapid prototyping becomes more deeply integrated into aerospace component development.
Case Studies: Successful Rapid Prototyping in Aircraft and Spacecraft
In recent years, rapid prototyping has become a cornerstone of innovation in the aerospace sector, enabling faster development cycles, cost savings, and enhanced design flexibility. Several high-profile case studies from 2024 and into 2025 illustrate the transformative impact of these technologies on both aircraft and spacecraft component development.
One notable example is the use of additive manufacturing (AM) by Airbus in the production of structural components for commercial aircraft. In 2024, Airbus reported the successful integration of 3D-printed titanium brackets in the A350 XWB, reducing part weight by up to 30% and shortening lead times for component delivery. The company continues to expand its use of rapid prototyping for both metal and polymer parts, with ongoing projects aimed at certifying more complex, load-bearing structures for flight in 2025.
Similarly, Boeing has leveraged rapid prototyping to accelerate the development of critical systems for its next-generation aircraft. In 2024, Boeing’s engineers used advanced 3D printing to prototype and test environmental control system ducts, achieving a 50% reduction in development time compared to traditional methods. The company is also collaborating with suppliers to qualify new high-performance materials for additive manufacturing, with the goal of increasing the proportion of 3D-printed parts in future aircraft models.
In the realm of space exploration, NASA has been at the forefront of rapid prototyping for spacecraft components. The Artemis program, targeting lunar missions in the mid-2020s, has relied heavily on rapid prototyping to iterate designs for rocket engine parts, crew module structures, and life support systems. In 2024, NASA successfully tested a 3D-printed combustion chamber for the RS-25 engine, demonstrating performance parity with conventionally manufactured counterparts while reducing production time from months to weeks.
Private space companies are also embracing rapid prototyping. SpaceX has integrated additive manufacturing into the production of SuperDraco thrusters and other critical components for the Dragon spacecraft. The company’s rapid prototyping capabilities have enabled swift design iterations and accelerated testing cycles, contributing to the reliability and reusability of its launch vehicles.
Looking ahead to 2025 and beyond, the adoption of rapid prototyping in aerospace is expected to intensify, driven by advances in material science, process automation, and digital design tools. Industry leaders are investing in larger-scale additive manufacturing systems and digital twins to further streamline the transition from prototype to certified flight hardware. As regulatory frameworks evolve to accommodate these new technologies, rapid prototyping will remain a key enabler of innovation and competitiveness in the aerospace sector.
Competitive Landscape: Key Players and Strategic Partnerships
The competitive landscape for rapid prototyping in aerospace components is characterized by a dynamic interplay of established aerospace manufacturers, advanced materials suppliers, and specialized additive manufacturing (AM) technology providers. As of 2025, the sector is witnessing intensified collaboration and strategic partnerships aimed at accelerating innovation, reducing lead times, and enhancing the performance of critical components.
Major aerospace OEMs such as Boeing and Airbus continue to invest heavily in rapid prototyping capabilities, both in-house and through alliances. Boeing has expanded its use of additive manufacturing for prototyping and low-rate production, leveraging partnerships with leading AM technology firms to streamline the development of complex parts for commercial and defense platforms. Similarly, Airbus has integrated rapid prototyping into its digital manufacturing ecosystem, collaborating with suppliers to accelerate the qualification of new materials and processes for flight-critical components.
On the technology front, companies like Stratasys and 3D Systems are prominent providers of industrial-grade 3D printing solutions tailored for aerospace applications. Stratasys has established partnerships with aerospace suppliers to deliver high-performance polymer and composite prototypes, while 3D Systems focuses on metal additive manufacturing for functional prototyping and tooling. Both companies are investing in new materials and process certification to meet stringent aerospace standards.
Material innovation is another competitive axis, with firms such as Honeywell and GE Aerospace playing dual roles as both end-users and developers of advanced alloys and composites for rapid prototyping. GE Aerospace has notably advanced the use of additive manufacturing for prototyping jet engine components, often in collaboration with AM specialists and research institutions.
Strategic partnerships are increasingly shaping the sector’s trajectory. For example, Safran has entered into joint development agreements with AM technology providers to co-develop rapid prototyping solutions for propulsion and landing gear systems. Similarly, Rolls-Royce is working with a network of suppliers and technology partners to accelerate the prototyping and validation of next-generation engine parts.
Looking ahead, the competitive landscape is expected to further consolidate around integrated digital manufacturing platforms, with key players leveraging strategic alliances to address supply chain resilience, certification challenges, and the growing demand for sustainable materials. The next few years will likely see increased investment in automation, data-driven design, and cross-industry partnerships, positioning rapid prototyping as a cornerstone of aerospace innovation.
Future Outlook: Emerging Technologies and Market Disruptors
The future of rapid prototyping for aerospace components is poised for significant transformation as emerging technologies and market disruptors reshape the industry landscape in 2025 and beyond. The convergence of advanced additive manufacturing (AM), digital engineering, and new materials is accelerating the pace at which aerospace companies can design, test, and iterate complex parts.
A key driver is the maturation of metal additive manufacturing, particularly laser powder bed fusion (LPBF) and electron beam melting (EBM), which are now being adopted for both prototyping and end-use components. Major aerospace OEMs such as Boeing and Airbus have expanded their in-house AM capabilities, leveraging rapid prototyping to reduce lead times for critical parts and support agile development cycles. For example, Airbus has integrated AM into its digital design-to-production workflow, enabling the rapid validation of new geometries and lightweight structures for next-generation aircraft.
Suppliers like GE Aerospace and Rolls-Royce are also investing in rapid prototyping to accelerate the development of advanced propulsion systems. GE Aerospace has demonstrated the use of AM for prototyping and producing complex engine components, such as fuel nozzles and heat exchangers, which benefit from reduced assembly steps and improved performance. Meanwhile, Rolls-Royce is exploring hybrid manufacturing approaches that combine additive and subtractive processes to optimize both speed and precision.
The adoption of digital twins and simulation-driven design is another disruptive trend. By integrating rapid prototyping with real-time data analytics and virtual testing, companies can iterate designs faster and reduce the number of physical prototypes required. NASA is at the forefront of this approach, using digital engineering to streamline the prototyping of spacecraft components and validate performance under extreme conditions.
Looking ahead, the emergence of new materials—such as high-temperature polymers, advanced ceramics, and functionally graded alloys—will further expand the capabilities of rapid prototyping. Companies like Stratasys and 3D Systems are developing specialized AM platforms tailored for aerospace applications, supporting the production of lightweight, high-strength parts with complex internal features.
As regulatory frameworks evolve to accommodate additive manufacturing and digital certification, the aerospace sector is expected to see broader adoption of rapid prototyping for both commercial and defense applications. The next few years will likely witness increased collaboration between OEMs, suppliers, and technology providers, driving innovation and reducing time-to-market for new aerospace components.
Recommendations: Strategic Actions for Stakeholders in 2025 and Beyond
As rapid prototyping continues to transform aerospace component development, stakeholders must adopt strategic actions to remain competitive and innovative in 2025 and beyond. The following recommendations are tailored for aerospace manufacturers, suppliers, and technology partners seeking to maximize the benefits of rapid prototyping technologies.
- Invest in Advanced Additive Manufacturing Capabilities: Aerospace companies should prioritize investment in state-of-the-art additive manufacturing (AM) systems, such as laser powder bed fusion and electron beam melting, which are increasingly used for prototyping and end-use parts. Leading aerospace OEMs like Airbus and Boeing have expanded their in-house AM capabilities, enabling faster iteration and reduced lead times for complex components.
- Strengthen Supplier Collaboration and Digital Integration: To accelerate prototyping cycles, stakeholders should foster closer collaboration with suppliers and technology partners. Digital platforms and secure data exchange protocols are essential for sharing design files and feedback in real time. Companies such as Safran and GE Aerospace have established digital ecosystems to streamline prototyping and qualification processes across their supply chains.
- Adopt Agile Design and Testing Methodologies: Rapid prototyping enables iterative design and testing, reducing the risk of costly late-stage changes. Aerospace organizations should implement agile development frameworks, integrating simulation, virtual testing, and physical prototyping. Rolls-Royce has demonstrated the value of this approach by using rapid prototyping to validate new engine components before full-scale production.
- Focus on Workforce Upskilling and Talent Development: The adoption of rapid prototyping technologies requires a workforce skilled in digital design, AM processes, and quality assurance. Stakeholders should invest in training programs and partnerships with academic institutions to build expertise in these areas, as seen in initiatives led by Lockheed Martin and NASA.
- Prioritize Certification and Standardization Efforts: As regulatory requirements evolve, stakeholders must engage with industry bodies to develop and adopt standards for rapid prototyping in aerospace. Participation in working groups led by organizations such as SAE International and ANSI will help ensure that new prototyping methods meet safety and quality benchmarks.
By implementing these strategic actions, aerospace stakeholders can harness rapid prototyping to accelerate innovation, reduce costs, and maintain compliance in a rapidly evolving technological landscape through 2025 and the years ahead.
Sources & References
- Airbus
- Boeing
- GE Aerospace
- Siemens
- Honeywell
- European Space Agency
- Lockheed Martin
- Northrop Grumman
- Stratasys
- 3D Systems
- Renishaw
- EOS
- Haas Automation
- DMG MORI
- Yamazaki Mazak
- TRUMPF
- GE Aerospace
- European Union Aviation Safety Agency
- ASTM International
- NASA
- Rolls-Royce
- ANSI