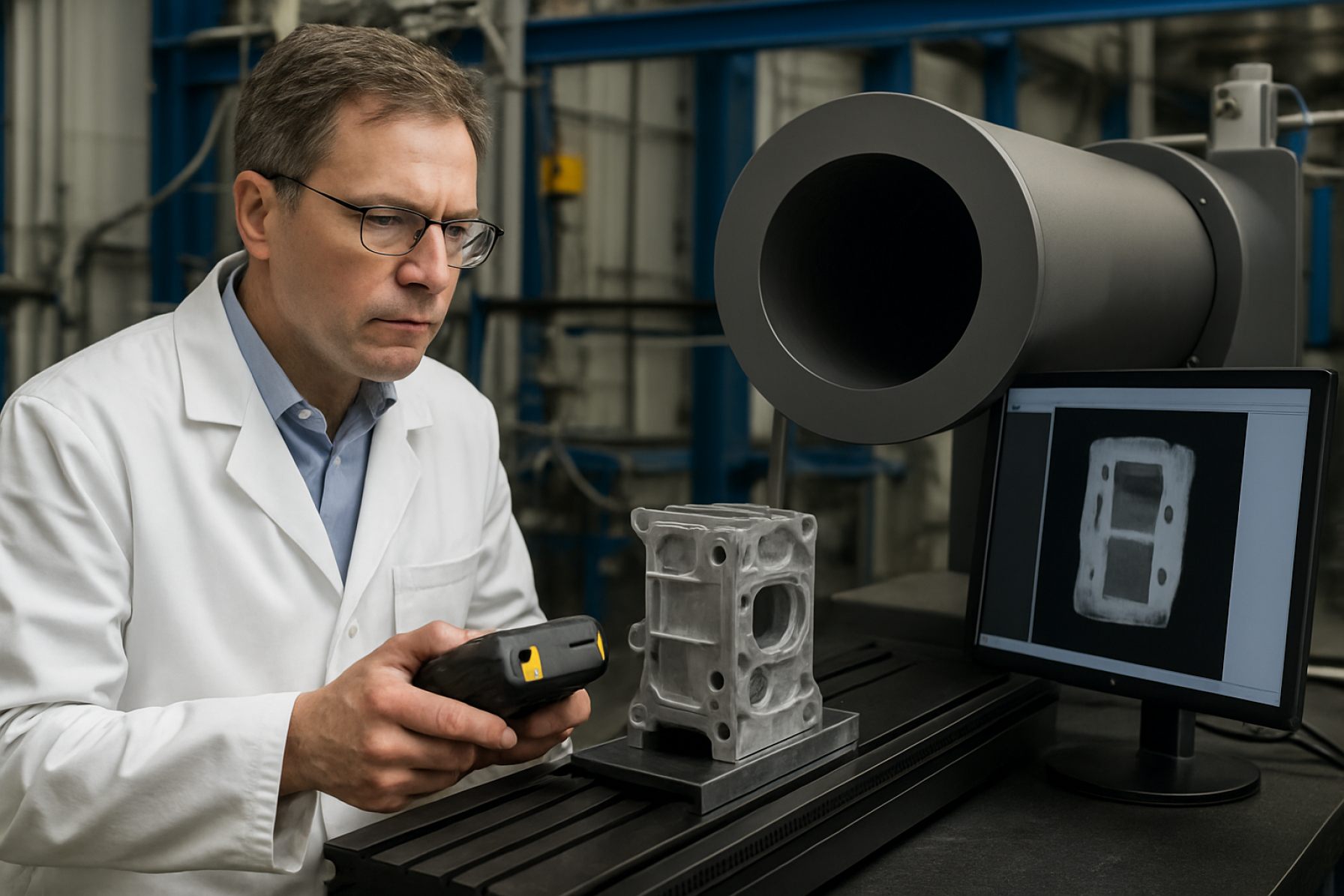
Neutron Radiography Inspection Systems in 2025: Transforming Non-Destructive Testing with Unmatched Clarity. Explore Market Growth, Technological Breakthroughs, and Strategic Opportunities Shaping the Next Five Years.
- Executive Summary: 2025 Market Overview & Key Insights
- Market Size, Growth Rate, and 2025–2030 Forecasts
- Core Technologies: Advances in Neutron Imaging & Detection
- Key Applications: Aerospace, Defense, Energy, and Industrial Use Cases
- Competitive Landscape: Leading Manufacturers & Innovators
- Regulatory Standards and Industry Guidelines
- Emerging Trends: Digitalization, Automation, and AI Integration
- Regional Analysis: North America, Europe, Asia-Pacific, and Rest of World
- Challenges, Barriers, and Risk Factors
- Future Outlook: Strategic Opportunities and Investment Priorities
- Sources & References
Executive Summary: 2025 Market Overview & Key Insights
Neutron radiography inspection systems are gaining strategic importance in non-destructive testing (NDT) across industries such as aerospace, automotive, nuclear energy, and advanced manufacturing. As of 2025, the global market is characterized by a combination of technological advancements, increased regulatory scrutiny, and a growing need for high-precision internal imaging—especially for complex assemblies and critical safety components.
Key industry players, including GE Vernova (formerly part of GE Inspection Technologies), Shimadzu Corporation, and Toshiba Corporation, are actively developing and supplying neutron radiography systems tailored for both research and industrial applications. These companies are focusing on enhancing detector sensitivity, automating image analysis, and integrating digital workflows to improve throughput and reliability. For example, Shimadzu Corporation continues to expand its portfolio of advanced NDT solutions, including neutron imaging, to meet the evolving demands of aerospace and nuclear sectors.
The adoption of neutron radiography is being propelled by its unique ability to detect light elements (such as hydrogen) and differentiate between materials that are otherwise indistinguishable using X-ray or gamma-ray techniques. This capability is particularly valuable for inspecting turbine blades, fuel cells, composite structures, and sealed assemblies. In 2025, regulatory agencies and industry standards bodies are increasingly mandating neutron-based inspection for certain high-risk components, further driving market growth.
Regionally, North America, Europe, and East Asia remain the primary markets, supported by robust R&D infrastructure and established nuclear industries. Notably, government-backed research institutions and national laboratories in these regions are collaborating with commercial suppliers to advance system capabilities and expand application areas. For instance, Toshiba Corporation is involved in partnerships with research reactors and nuclear facilities to deploy next-generation neutron imaging solutions.
Looking ahead, the market outlook for neutron radiography inspection systems through the late 2020s is positive. Continued investment in nuclear power, the rise of hydrogen technologies, and the push for higher safety standards in aerospace manufacturing are expected to sustain demand. Additionally, ongoing R&D into compact neutron sources and digital imaging technologies is likely to lower operational barriers and broaden adoption beyond traditional sectors.
- Technological innovation and automation are central to competitive differentiation.
- Regulatory requirements and safety standards are key market drivers.
- Collaborations between industry and research institutions are accelerating system development.
- Expansion into new application areas, such as battery and hydrogen storage inspection, is anticipated.
Market Size, Growth Rate, and 2025–2030 Forecasts
The global market for neutron radiography inspection systems is experiencing a period of renewed growth, driven by increasing demand for advanced non-destructive testing (NDT) solutions in sectors such as aerospace, defense, nuclear energy, and advanced manufacturing. As of 2025, the market is estimated to be valued in the low hundreds of millions USD, with a compound annual growth rate (CAGR) projected in the range of 6–8% through 2030, according to industry consensus and company statements. This growth is underpinned by the unique capabilities of neutron radiography—such as its ability to detect light elements (e.g., hydrogen, lithium) and image through dense metals—making it indispensable for applications where traditional X-ray or gamma radiography fall short.
Key players in the neutron radiography inspection systems market include Toshiba Energy Systems & Solutions Corporation, which supplies neutron radiography equipment for nuclear power plant maintenance and fuel inspection, and Curtiss-Wright Corporation, whose nuclear division provides neutron radiography services and systems for both commercial and government clients. Helmholtz Association in Germany, through its research centers, is also a significant contributor to the development and deployment of advanced neutron imaging facilities, supporting both industrial and scientific applications.
Recent years have seen increased investment in neutron imaging infrastructure, particularly in Europe, North America, and parts of Asia. For example, new and upgraded neutron sources at research reactors and spallation facilities are expanding the availability of high-resolution neutron radiography, enabling more widespread industrial adoption. The trend toward digital neutron imaging—replacing film with advanced detector arrays and real-time imaging software—is further accelerating market growth, as it reduces inspection times and improves data analysis capabilities.
Looking ahead to 2030, the market outlook remains positive. The ongoing decommissioning and maintenance of aging nuclear reactors, the rise of hydrogen fuel technologies, and the growing complexity of aerospace components are expected to sustain demand for neutron radiography inspection systems. Additionally, collaborative initiatives between industry and research institutions are likely to yield further technological advancements, such as higher throughput systems and portable neutron sources, broadening the addressable market. As regulatory standards for safety and quality assurance continue to tighten, neutron radiography is poised to play an increasingly critical role in global NDT strategies.
Core Technologies: Advances in Neutron Imaging & Detection
Neutron radiography inspection systems are experiencing significant technological advancements as of 2025, driven by the demand for non-destructive testing (NDT) solutions in aerospace, automotive, nuclear, and advanced manufacturing sectors. Unlike X-ray imaging, neutron radiography offers unique sensitivity to light elements (such as hydrogen, lithium, and boron) and can penetrate heavy metals, making it invaluable for inspecting complex assemblies, fuel cells, turbine blades, and nuclear fuel rods.
Recent years have seen the deployment of more compact, high-flux neutron sources, including accelerator-driven systems and advanced research reactors. These developments are reducing facility size and operational costs, broadening accessibility beyond national laboratories. For example, Toshiba Corporation has developed portable neutron radiography systems for field inspection, while Canon Inc. is investing in compact neutron generators for industrial applications. These systems are increasingly automated, integrating robotic sample handling and AI-driven image analysis to enhance throughput and reliability.
Digital neutron imaging is rapidly replacing traditional film-based methods. State-of-the-art detectors, such as scintillator-based flat panels and microchannel plate (MCP) detectors, now deliver higher spatial resolution and faster acquisition times. Companies like SCK CEN (Belgian Nuclear Research Centre) and Helmholtz Association in Germany are at the forefront of developing and deploying these digital systems, supporting both research and industrial inspection needs.
Integration with computed tomography (CT) is another major trend. Neutron CT enables 3D visualization of internal structures, complementing X-ray CT and providing critical insights for quality assurance in additive manufacturing and energy storage. Facilities such as the Paul Scherrer Institute in Switzerland and National Institute of Standards and Technology (NIST) in the US are expanding their neutron imaging capabilities, offering advanced inspection services to industry partners.
Looking ahead, the next few years are expected to bring further miniaturization of neutron sources, improved detector sensitivity, and greater integration with automated data analytics. The push for sustainable energy and electrification is likely to drive demand for neutron radiography in battery and hydrogen storage system inspection. As regulatory standards evolve, especially in aerospace and nuclear sectors, adoption of advanced neutron radiography systems is set to accelerate, with leading manufacturers and research institutes playing a pivotal role in shaping the market landscape.
Key Applications: Aerospace, Defense, Energy, and Industrial Use Cases
Neutron radiography inspection systems are increasingly recognized as critical non-destructive testing (NDT) tools across several high-value sectors, notably aerospace, defense, energy, and advanced industrial manufacturing. As of 2025, the adoption of neutron radiography is accelerating, driven by its unique ability to visualize light elements (such as hydrogen) and distinguish between materials with similar densities—capabilities that surpass conventional X-ray imaging in specific applications.
In the aerospace sector, neutron radiography is essential for inspecting turbine blades, composite structures, and bonded assemblies. The technique enables detection of water ingress, corrosion, and adhesive bond quality, which are otherwise challenging to assess. Major aerospace manufacturers and maintenance organizations are integrating neutron imaging into their quality assurance protocols to meet stringent safety and reliability standards. Companies such as Boeing and Airbus have shown interest in advanced NDT methods, including neutron radiography, to support the inspection of critical components and ensure airworthiness.
In the defense industry, neutron radiography is employed for the inspection of munitions, pyrotechnics, and complex assemblies where the presence and distribution of low atomic number elements are crucial. National laboratories and defense contractors utilize neutron imaging to verify the integrity of energetic materials and to detect voids, cracks, or foreign objects within sealed systems. Organizations such as NASA and Lockheed Martin have ongoing research and operational programs leveraging neutron radiography for both component development and failure analysis.
The energy sector—particularly nuclear power—relies on neutron radiography for the inspection of fuel rods, control assemblies, and reactor internals. The technique’s sensitivity to hydrogen makes it invaluable for detecting water ingress, corrosion, and hydride formation in zirconium alloys. Utilities and nuclear technology providers, including Westinghouse Electric Company and Framatome, are investing in neutron imaging systems to enhance plant safety and extend component lifetimes.
In industrial manufacturing, neutron radiography is used for quality control of advanced materials, such as ceramics, polymers, and battery components. The automotive and electronics industries are exploring neutron imaging for the inspection of fuel cells, lithium batteries, and encapsulated electronics, where internal features are otherwise invisible to X-rays. Equipment suppliers like Toshiba and Hitachi are developing compact neutron sources and turnkey inspection systems to meet growing demand.
Looking ahead, the next few years are expected to see broader deployment of neutron radiography systems, driven by advances in compact neutron sources, digital imaging detectors, and automation. As regulatory frameworks evolve and the cost of neutron sources decreases, adoption is likely to expand beyond research institutions to mainstream industrial settings, further cementing neutron radiography’s role in critical inspection workflows.
Competitive Landscape: Leading Manufacturers & Innovators
The competitive landscape for neutron radiography inspection systems in 2025 is characterized by a small but highly specialized group of manufacturers and technology innovators, primarily concentrated in North America, Europe, and Asia. These companies are at the forefront of developing advanced neutron imaging solutions for applications in aerospace, nuclear energy, defense, and advanced manufacturing.
One of the most prominent players is General Electric (GE), whose Inspection Technologies division has a long-standing reputation for non-destructive testing (NDT) solutions, including neutron radiography systems. GE’s systems are widely used in the aerospace sector for inspecting turbine blades and composite structures, leveraging their expertise in both hardware and digital imaging software.
In Europe, TÜV NORD GROUP is notable for its integration of neutron radiography into industrial inspection services, particularly for the automotive and energy sectors. Their facilities in Germany are equipped with state-of-the-art neutron imaging stations, supporting both R&D and routine quality assurance.
Japan’s Hitachi is another key innovator, offering neutron radiography systems tailored for both research institutions and industrial clients. Hitachi’s systems are recognized for their high spatial resolution and integration with automated analysis platforms, making them suitable for high-throughput inspection environments.
Emerging players include Centre for Energy Research (Hungary), which has developed modular neutron imaging systems for both stationary and mobile applications. Their collaborations with European research reactors have enabled the deployment of flexible inspection solutions for on-site and remote analysis.
On the supplier side, Oxford Instruments provides critical components such as neutron detectors and imaging plates, supporting OEMs and end-users in system upgrades and custom builds. Their advancements in detector sensitivity and digital readout technologies are driving improvements in image quality and throughput.
Looking ahead, the competitive landscape is expected to evolve as demand grows for automated, high-resolution neutron radiography in battery manufacturing, additive manufacturing, and nuclear decommissioning. Companies are investing in AI-driven image analysis, remote operation capabilities, and compact neutron sources to address market needs for portability and safety. Strategic partnerships between system manufacturers, research institutes, and end-users are likely to accelerate innovation and expand the adoption of neutron radiography inspection systems globally.
Regulatory Standards and Industry Guidelines
Neutron radiography inspection systems are subject to a complex framework of regulatory standards and industry guidelines, reflecting their critical role in sectors such as aerospace, defense, nuclear energy, and advanced manufacturing. As of 2025, regulatory oversight is intensifying, driven by both technological advancements and heightened safety requirements. The International Organization for Standardization (ISO) continues to play a central role, with ISO 19232 and ISO 6224 providing foundational requirements for image quality and operational procedures in neutron radiography. These standards are regularly updated to accommodate new detector technologies and digital imaging methods, ensuring that inspection systems remain both effective and safe.
In the United States, the U.S. Nuclear Regulatory Commission (NRC) maintains strict controls over the use of neutron sources, particularly in non-destructive testing (NDT) applications. NRC regulations require licensing, personnel training, and periodic audits for facilities operating neutron radiography systems, especially those utilizing isotopic sources such as californium-252 or research reactors. The American Society for Nondestructive Testing (ASNT) also provides recommended practices and personnel certification programs, which are widely adopted by industry to ensure operator competency and procedural consistency.
In Europe, the Euratom framework and national nuclear safety authorities oversee the deployment and operation of neutron radiography systems, with a focus on radiation protection, source security, and environmental impact. The European Committee for Standardization (CEN) is actively harmonizing standards with ISO, aiming to facilitate cross-border collaboration and equipment interoperability. Notably, the adoption of digital neutron imaging is prompting revisions to existing guidelines, as digital detectors introduce new calibration and data management requirements.
Leading manufacturers such as SCK CEN (Belgium), which operates the BR2 research reactor and provides neutron imaging services, and Toshiba Energy Systems & Solutions Corporation (Japan), a supplier of advanced neutron radiography equipment, are closely involved in standardization efforts. These companies often participate in working groups and pilot projects to validate new protocols and ensure compliance with evolving regulations.
Looking ahead, regulatory bodies are expected to further refine standards to address cybersecurity in digital radiography systems, lifecycle management of neutron sources, and the integration of artificial intelligence in image analysis. The ongoing transition from film-based to digital neutron radiography will likely accelerate the adoption of updated guidelines, with industry stakeholders collaborating to ensure both safety and innovation in inspection practices.
Emerging Trends: Digitalization, Automation, and AI Integration
Neutron radiography inspection systems are undergoing significant transformation as digitalization, automation, and artificial intelligence (AI) become increasingly integrated into non-destructive testing (NDT) workflows. As of 2025, these trends are reshaping both the capabilities and the accessibility of neutron radiography, which is valued for its unique ability to image light elements and complex assemblies, especially in aerospace, defense, and energy sectors.
Digitalization is a primary driver, with leading system manufacturers transitioning from analog film-based imaging to high-resolution digital detectors. This shift enables real-time image acquisition, improved data storage, and streamlined sharing of inspection results. Companies such as SCK CEN and FRM II are at the forefront, operating advanced neutron imaging facilities that support digital workflows and remote collaboration. The adoption of digital detectors also facilitates integration with other NDT modalities, allowing for multi-modal inspection and more comprehensive analysis.
Automation is another key trend, with robotic sample handling and automated scanning systems reducing human intervention and increasing throughput. For instance, SCK CEN has implemented automated positioning systems to enhance the repeatability and efficiency of inspections. Automated data processing pipelines are also being developed, enabling rapid analysis and reducing the potential for human error.
AI integration is emerging as a transformative force in neutron radiography. Machine learning algorithms are being trained to identify defects, classify materials, and optimize imaging parameters. This not only accelerates the inspection process but also improves accuracy and consistency. Research collaborations, such as those involving Paul Scherrer Institut and National Institute of Standards and Technology (NIST), are exploring AI-driven image reconstruction and defect recognition, with pilot projects demonstrating promising results in automating complex interpretation tasks.
Looking ahead, the next few years are expected to see further convergence of these trends. The deployment of cloud-based platforms for data management and remote analysis is anticipated, enabling global access to neutron radiography expertise. Additionally, the integration of digital twins and predictive maintenance models, powered by AI, is likely to enhance the value proposition of neutron radiography in industrial settings. As regulatory frameworks adapt to these technological advances, broader adoption across sectors such as additive manufacturing, automotive, and nuclear energy is expected.
In summary, the digitalization, automation, and AI integration underway in neutron radiography inspection systems are poised to deliver higher efficiency, improved reliability, and expanded application scope, positioning the technology for significant growth and innovation through 2025 and beyond.
Regional Analysis: North America, Europe, Asia-Pacific, and Rest of World
The global market for neutron radiography inspection systems is experiencing notable regional dynamics, with North America, Europe, and Asia-Pacific emerging as key centers of activity in 2025 and the near future. These regions are distinguished by their advanced research infrastructure, robust aerospace and defense sectors, and increasing investments in non-destructive testing (NDT) technologies.
North America remains a leader in neutron radiography, driven by the presence of major aerospace, defense, and nuclear research organizations. The United States, in particular, benefits from the ongoing modernization of its nuclear facilities and the adoption of advanced NDT methods for critical component inspection. National laboratories and research centers, such as those operated by Oak Ridge National Laboratory and Sandia National Laboratories, continue to invest in neutron imaging capabilities. Additionally, private sector players like General Atomics are involved in the development and supply of neutron sources and related inspection systems, supporting both government and commercial applications.
Europe is characterized by a strong collaborative research environment and a focus on high-precision industrial applications. Countries such as Germany, France, and Switzerland are home to leading neutron research facilities, including the Paul Scherrer Institute and the French Alternative Energies and Atomic Energy Commission (CEA). These institutions are at the forefront of developing advanced neutron radiography techniques for sectors ranging from automotive to energy. European aerospace manufacturers and nuclear operators are increasingly integrating neutron radiography into their quality assurance protocols, reflecting a broader trend toward digitalization and automation in inspection processes.
Asia-Pacific is witnessing rapid growth, fueled by expanding nuclear power programs, rising investments in aerospace manufacturing, and government-backed research initiatives. Japan and China are particularly active, with organizations such as Japan Atomic Energy Agency (JAEA) and China Institute of Atomic Energy advancing neutron imaging technologies. The region’s industrial base is increasingly adopting neutron radiography for the inspection of complex assemblies and safety-critical components, with a focus on improving reliability and compliance with international standards.
Rest of World regions, including parts of the Middle East and South America, are gradually entering the neutron radiography landscape, primarily through partnerships with established research institutions and technology providers. While adoption rates remain modest, ongoing infrastructure development and the localization of nuclear and aerospace industries are expected to drive incremental demand in the coming years.
Overall, the outlook for neutron radiography inspection systems is positive across all major regions, with continued advancements in neutron source technology, digital imaging, and automation expected to further expand the scope and efficiency of inspection applications through 2025 and beyond.
Challenges, Barriers, and Risk Factors
Neutron radiography inspection systems, while offering unique imaging capabilities for non-destructive testing (NDT), face several significant challenges and barriers as of 2025 and looking ahead. One of the primary obstacles is the high cost and complexity associated with neutron source generation. Most industrial neutron radiography systems rely on nuclear reactors or compact accelerator-based sources, both of which require substantial capital investment, specialized infrastructure, and stringent regulatory compliance. The limited number of operational research reactors worldwide further constrains accessibility, with only a handful of facilities—such as those operated by National Institute of Standards and Technology and Technische Universität München—offering neutron radiography services at scale.
Another barrier is the regulatory environment. Neutron sources, especially those based on nuclear reactors, are subject to rigorous safety and security regulations, which can delay project timelines and increase operational costs. The need for highly trained personnel to operate and maintain these systems adds to the challenge, as does the ongoing requirement for compliance with evolving international standards set by organizations such as the International Atomic Energy Agency.
Technical limitations also persist. While neutron radiography excels at imaging light elements and complex assemblies (such as hydrogenous materials in aerospace or nuclear fuel rods), its spatial resolution and throughput often lag behind advanced X-ray and computed tomography (CT) systems. This can limit its adoption in industries where high-speed, high-resolution imaging is critical. Furthermore, the development of digital neutron imaging detectors, though progressing, still faces hurdles in terms of sensitivity, durability, and cost-effectiveness compared to established X-ray detector technologies.
Supply chain risks are another concern. The specialized components required for neutron radiography—such as scintillator screens, neutron collimators, and shielding materials—are produced by a limited number of manufacturers, including SCK CEN and Helmholtz Zentrum München. Disruptions in the supply of these components, whether due to geopolitical factors or manufacturing bottlenecks, can impact system availability and maintenance.
Looking forward, the sector’s outlook is shaped by ongoing efforts to develop compact, accelerator-driven neutron sources and more robust digital imaging technologies. However, widespread adoption will depend on overcoming the intertwined challenges of cost, regulation, and technical performance. The industry’s progress will likely hinge on collaborations between research institutions, equipment manufacturers, and end-user industries to address these barriers and mitigate associated risks.
Future Outlook: Strategic Opportunities and Investment Priorities
The future outlook for neutron radiography inspection systems in 2025 and the coming years is shaped by a convergence of technological advancements, regulatory drivers, and strategic investments across critical industries. As sectors such as aerospace, nuclear energy, defense, and advanced manufacturing increasingly demand non-destructive testing (NDT) solutions capable of revealing internal structures with high precision, neutron radiography is emerging as a complementary or superior alternative to traditional X-ray and gamma-ray methods.
Key industry players are intensifying their focus on expanding neutron imaging capabilities. GE Vernova, through its Inspection Technologies division, continues to invest in R&D for advanced neutron radiography systems, targeting applications in turbine blade inspection and composite material analysis. Similarly, Shimadzu Corporation is leveraging its expertise in analytical instrumentation to develop next-generation neutron imaging solutions, with a particular emphasis on automated, high-throughput systems for industrial quality assurance.
Government-backed research institutions and nuclear facilities are also pivotal in driving innovation and adoption. The International Atomic Energy Agency (IAEA) is actively supporting the deployment of neutron radiography infrastructure in member states, recognizing its value for nuclear fuel inspection, cultural heritage conservation, and security screening. In the United States, the Oak Ridge National Laboratory and Argonne National Laboratory are expanding their neutron imaging beamlines, offering collaborative access to industry partners for prototyping and validation of new inspection systems.
Strategic opportunities are emerging in the miniaturization and portability of neutron sources, with companies such as Adelphi Technology developing compact accelerator-based neutron generators. These innovations are expected to lower barriers to entry for smaller manufacturers and enable on-site inspections in aerospace maintenance, pipeline integrity, and additive manufacturing.
Investment priorities for 2025 and beyond are likely to focus on:
- Enhancing detector sensitivity and spatial resolution to meet the demands of advanced materials and complex assemblies.
- Integrating artificial intelligence and machine learning for automated defect recognition and data analytics.
- Expanding international collaborations to standardize protocols and facilitate technology transfer, as promoted by the IAEA and national laboratories.
- Developing environmentally sustainable neutron sources to address regulatory and operational challenges associated with traditional reactor-based systems.
Overall, the neutron radiography inspection systems market is poised for robust growth, with strategic investments in R&D, infrastructure, and cross-sector partnerships expected to unlock new applications and drive adoption through 2025 and the following years.
Sources & References
- GE Vernova
- Shimadzu Corporation
- Toshiba Corporation
- Helmholtz Association
- Toshiba Corporation
- Canon Inc.
- Paul Scherrer Institute
- National Institute of Standards and Technology
- Boeing
- Airbus
- NASA
- Lockheed Martin
- Framatome
- Hitachi
- General Electric
- TÜV NORD GROUP
- Centre for Energy Research
- Oxford Instruments
- American Society for Nondestructive Testing
- FRM II
- Oak Ridge National Laboratory
- Sandia National Laboratories
- General Atomics
- Japan Atomic Energy Agency (JAEA)
- International Atomic Energy Agency
- Helmholtz Zentrum München