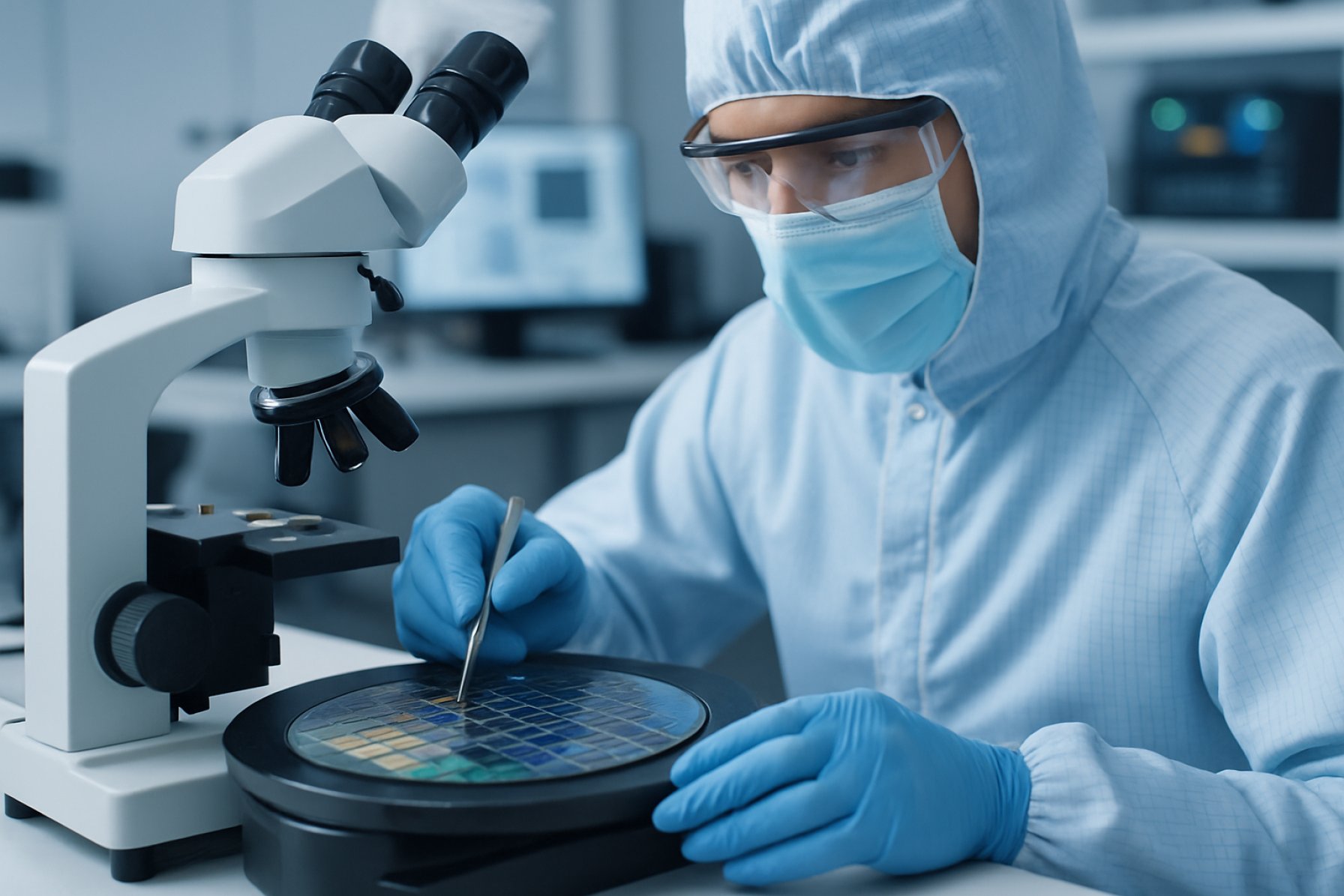
Avalanche Photodiode Manufacturing in 2025: Unleashing Next-Gen Photonics for High-Speed Sensing and Communications. Explore How Innovation and Expanding Applications Are Reshaping the Industry Landscape.
- Executive Summary: Key Trends and 2025 Outlook
- Market Size, Growth Rate, and Forecasts (2025–2030)
- Technological Innovations in Avalanche Photodiode Design
- Key Manufacturers and Global Supply Chain Overview
- Emerging Applications: Telecom, LIDAR, Medical, and Quantum Sensing
- Competitive Landscape and Strategic Partnerships
- Regional Analysis: North America, Europe, Asia-Pacific, and Rest of World
- Challenges: Manufacturing Complexity, Cost, and Reliability
- Sustainability and Regulatory Developments
- Future Outlook: Disruptive Technologies and Long-Term Market Opportunities
- Sources & References
Executive Summary: Key Trends and 2025 Outlook
Avalanche photodiode (APD) manufacturing is entering a pivotal phase in 2025, driven by surging demand from optical communication, LiDAR, medical imaging, and quantum technology sectors. The global transition to high-speed 5G/6G networks and the proliferation of data centers are intensifying requirements for high-sensitivity photodetectors, positioning APDs as a critical component in next-generation optoelectronic systems. Leading manufacturers are scaling up production and investing in advanced fabrication processes to meet these evolving needs.
Key industry players such as Hamamatsu Photonics, First Sensor AG (a TE Connectivity company), and Excelitas Technologies are expanding their APD portfolios, focusing on silicon and InGaAs-based devices to address both visible and near-infrared applications. Hamamatsu Photonics continues to lead in high-volume manufacturing, leveraging proprietary wafer processing and packaging technologies to enhance device reliability and performance. First Sensor AG is emphasizing modular APD arrays for automotive LiDAR and industrial sensing, while Excelitas Technologies is targeting medical and scientific instrumentation with custom APD solutions.
In 2025, the industry is witnessing a shift toward larger wafer sizes (6-inch and above) and the adoption of automated, high-throughput assembly lines to improve yield and reduce costs. There is also a notable trend toward monolithic integration of APDs with transimpedance amplifiers (TIAs) and other readout electronics, streamlining system design and boosting signal-to-noise ratios. These advances are supported by investments in cleanroom infrastructure and process automation, particularly in Asia-Pacific manufacturing hubs.
Supply chain resilience remains a priority, with manufacturers diversifying sourcing of critical materials such as high-purity silicon and III-V semiconductors. Environmental and regulatory considerations are prompting the adoption of greener manufacturing practices, including waste reduction and energy-efficient production lines.
Looking ahead, the APD manufacturing sector is expected to maintain robust growth through 2025 and beyond, propelled by the expansion of fiber-optic networks, the scaling of autonomous vehicle technologies, and the emergence of quantum communication systems. Strategic collaborations between device manufacturers, system integrators, and research institutions are anticipated to accelerate innovation, particularly in the development of low-noise, high-gain APDs for emerging applications.
Overall, the outlook for avalanche photodiode manufacturing in 2025 is characterized by technological advancement, capacity expansion, and a strong alignment with the needs of rapidly evolving photonics markets.
Market Size, Growth Rate, and Forecasts (2025–2030)
The global avalanche photodiode (APD) manufacturing sector is poised for robust growth from 2025 through 2030, driven by expanding applications in optical communication, medical imaging, LIDAR, and industrial automation. As of 2025, the market is characterized by increasing demand for high-speed, high-sensitivity photodetectors, particularly in fiber-optic networks and advanced sensing systems. The proliferation of 5G infrastructure and the ongoing transition to 6G, alongside the rapid adoption of autonomous vehicles and industrial robotics, are expected to be key growth drivers.
Major manufacturers such as Hamamatsu Photonics, a global leader in optoelectronic components, and First Sensor AG (now part of TE Connectivity), continue to expand their production capacities and invest in R&D to enhance APD performance, reliability, and integration capabilities. Excelitas Technologies and onsemi are also prominent players, supplying APDs for a range of applications from medical diagnostics to automotive LIDAR. These companies are focusing on innovations such as silicon and InGaAs APDs, which offer improved quantum efficiency and lower noise, catering to the evolving needs of telecom and sensing markets.
In terms of regional dynamics, Asia-Pacific remains the largest and fastest-growing market, fueled by the presence of major electronics manufacturers and the rapid expansion of telecommunications infrastructure in countries like China, Japan, and South Korea. European and North American markets are also witnessing steady growth, supported by investments in research, defense, and healthcare sectors.
Looking ahead to 2030, the APD manufacturing market is expected to maintain a healthy compound annual growth rate (CAGR), with industry estimates from leading manufacturers suggesting mid-to-high single-digit percentage growth annually. This outlook is underpinned by the increasing integration of APDs in next-generation optical modules, quantum communication systems, and advanced driver-assistance systems (ADAS). The push for miniaturization and integration of APDs into photonic integrated circuits (PICs) is anticipated to further accelerate market expansion, as companies like Hamamatsu Photonics and onsemi invest in advanced packaging and wafer-level manufacturing technologies.
- 2025: Market driven by telecom, LIDAR, and medical imaging demand.
- 2026–2028: Growth accelerates with 6G rollout and autonomous vehicle adoption.
- 2029–2030: Integration with PICs and quantum technologies becomes mainstream, supporting sustained market expansion.
Overall, the avalanche photodiode manufacturing sector is set for significant growth through 2030, with leading companies investing in innovation and capacity to meet the evolving demands of high-speed, high-sensitivity photodetection across diverse industries.
Technological Innovations in Avalanche Photodiode Design
Avalanche photodiode (APD) manufacturing is undergoing significant technological innovation in 2025, driven by the demand for higher sensitivity, faster response times, and integration with advanced optoelectronic systems. The core of these innovations lies in material engineering, device architecture, and scalable fabrication processes.
One of the most notable trends is the shift towards silicon carbide (SiC) and indium gallium arsenide (InGaAs) materials for APD fabrication. These materials offer superior performance in terms of quantum efficiency and noise reduction, especially for applications in the near-infrared and visible spectrum. Hamamatsu Photonics, a global leader in photonic devices, has expanded its portfolio of InGaAs APDs, focusing on low dark current and high gain-bandwidth products suitable for LIDAR and optical communication systems. Similarly, First Sensor AG (now part of TE Connectivity) continues to develop custom APD arrays using advanced silicon and InGaAs processes, targeting medical imaging and industrial automation.
Manufacturing innovations are also being realized through the adoption of monolithic integration techniques. This approach allows APDs to be fabricated alongside readout electronics on a single chip, reducing parasitic capacitance and improving signal integrity. onsemi has been at the forefront of this trend, leveraging its expertise in CMOS-compatible APD manufacturing to deliver compact, high-performance sensors for automotive and consumer electronics markets.
Another area of advancement is the implementation of wafer-level packaging (WLP) and 3D stacking technologies. These methods enhance device miniaturization and thermal management, which are critical for high-density APD arrays used in time-of-flight (ToF) and photon-counting applications. Lumentum Holdings and Excelitas Technologies are investing in automated WLP lines to scale up production while maintaining stringent quality standards required for telecom and defense sectors.
Looking ahead, the outlook for APD manufacturing is shaped by the convergence of photonics and semiconductor fabrication. The integration of APDs with silicon photonics platforms is expected to accelerate, enabling new functionalities in quantum communication and advanced sensing. Industry collaborations and investments in 200mm and 300mm wafer fabs are anticipated to further reduce costs and improve yield, making high-performance APDs more accessible across diverse applications.
In summary, 2025 marks a pivotal year for avalanche photodiode manufacturing, characterized by material innovation, integration with electronics, and scalable packaging solutions. Leading manufacturers such as Hamamatsu Photonics, onsemi, Lumentum Holdings, and Excelitas Technologies are setting the pace for the next generation of APD devices, with a strong focus on performance, reliability, and manufacturability.
Key Manufacturers and Global Supply Chain Overview
The global supply chain for avalanche photodiode (APD) manufacturing in 2025 is characterized by a combination of established photonics leaders, specialized semiconductor foundries, and a growing network of regional suppliers. APDs, essential for high-sensitivity optical detection in telecommunications, LiDAR, medical imaging, and scientific instrumentation, require advanced fabrication processes and stringent quality control, making the supply chain both technologically intensive and geographically diverse.
Key manufacturers in the APD sector include several multinational corporations with vertically integrated production capabilities. Hamamatsu Photonics of Japan remains a dominant force, leveraging decades of expertise in optoelectronic device fabrication and a broad product portfolio spanning from discrete APDs to multi-pixel arrays. The company’s global distribution network and in-house wafer processing ensure a stable supply to both OEMs and research institutions.
In Europe, First Sensor AG (a part of TE Connectivity) continues to play a significant role, particularly in automotive and industrial applications. Their focus on custom APD solutions and close collaboration with system integrators has enabled them to maintain a strong presence in the high-reliability segment. Meanwhile, Excelitas Technologies, with manufacturing sites in North America, Europe, and Asia, offers a wide range of APDs and modules, supporting both standard and application-specific requirements.
The United States is home to several important APD suppliers, including Lumentum and onsemi. Lumentum is notable for its role in supplying APDs for optical networking and 3D sensing, while onsemi provides silicon-based APDs for automotive LiDAR and industrial automation. Both companies benefit from robust R&D pipelines and established relationships with major technology integrators.
The supply chain for APDs is also influenced by the presence of specialized wafer foundries and packaging houses, particularly in East Asia. Companies such as OSRAM Opto Semiconductors (now part of ams OSRAM) contribute to the ecosystem by providing advanced photonic integration and scalable manufacturing for high-volume markets.
Looking ahead, the APD manufacturing landscape is expected to see increased investment in automation, wafer-level packaging, and the integration of APDs with complementary metal-oxide-semiconductor (CMOS) technologies. This trend is driven by the growing demand for compact, high-performance sensors in automotive, consumer electronics, and quantum communication. Supply chain resilience remains a priority, with manufacturers diversifying sourcing and expanding regional production to mitigate geopolitical and logistical risks.
Emerging Applications: Telecom, LIDAR, Medical, and Quantum Sensing
Avalanche photodiodes (APDs) are experiencing a surge in demand across several high-growth sectors, driven by their superior sensitivity and fast response times. As of 2025, manufacturers are scaling up production and refining fabrication techniques to meet the stringent requirements of emerging applications in telecommunications, LIDAR, medical imaging, and quantum sensing.
In telecommunications, APDs are integral to high-speed optical receivers, particularly in fiber-optic networks supporting 5G and beyond. The need for higher bandwidth and lower latency has prompted companies like Hamamatsu Photonics and Lumentum Holdings to invest in advanced APD arrays optimized for dense wavelength division multiplexing (DWDM) and coherent detection systems. These manufacturers are focusing on improving quantum efficiency and reducing noise, which are critical for long-haul and metro network performance.
LIDAR systems, essential for autonomous vehicles and industrial automation, rely on APDs for precise time-of-flight measurements. The automotive sector, in particular, is driving innovation in large-area and multi-pixel APD arrays. First Sensor AG (now part of TE Connectivity) and onsemi are notable for their scalable manufacturing of silicon-based APDs tailored for LIDAR modules. These companies are addressing challenges such as uniformity across arrays and integration with CMOS electronics, which are vital for cost-effective, high-volume deployment.
In medical imaging, APDs are increasingly used in positron emission tomography (PET) scanners and other photon-counting applications. The trend toward digital and compact imaging systems has led to the adoption of APD arrays with enhanced gain stability and low dark current. Excelitas Technologies and Hamamatsu Photonics are at the forefront, supplying custom APD modules for OEMs in the medical device industry. Their focus is on reliability, miniaturization, and compliance with stringent medical standards.
Quantum sensing represents a frontier application, with APDs enabling single-photon detection for quantum communication and computing. Manufacturers are developing APDs with ultra-low noise and high timing resolution, essential for quantum key distribution (QKD) and photon correlation experiments. ID Quantique and Laser Components are recognized for their specialized APD modules targeting research and early-stage commercial quantum systems.
Looking ahead, the APD manufacturing landscape is expected to evolve rapidly, with increased automation, wafer-level packaging, and the adoption of new materials such as InGaAs for extended wavelength sensitivity. Strategic partnerships between device manufacturers and system integrators are likely to accelerate innovation, ensuring that APDs remain at the core of next-generation photonic technologies.
Competitive Landscape and Strategic Partnerships
The competitive landscape of avalanche photodiode (APD) manufacturing in 2025 is characterized by a blend of established photonics giants, specialized semiconductor firms, and emerging players leveraging advanced materials and integration techniques. The sector is witnessing intensified competition driven by the rapid expansion of applications in optical communication, LiDAR, medical imaging, and quantum technologies.
Key industry leaders such as Hamamatsu Photonics and First Sensor AG (now part of TE Connectivity) continue to dominate the high-performance APD segment, benefiting from decades of expertise in silicon and InGaAs APD fabrication. Hamamatsu Photonics maintains a strong global presence, supplying APDs for telecommunications, scientific instrumentation, and industrial automation, while also investing in next-generation APD arrays for LiDAR and medical diagnostics.
In North America, Lumentum Holdings and onsemi are prominent, with Lumentum Holdings focusing on high-speed APDs for optical networks and datacenter interconnects. onsemi leverages its semiconductor manufacturing scale to supply APDs for automotive LiDAR and industrial sensing, emphasizing cost-effective, high-volume production.
Strategic partnerships and collaborations are increasingly shaping the APD manufacturing landscape. For instance, Hamamatsu Photonics has engaged in joint development projects with automotive OEMs and LiDAR system integrators to tailor APD arrays for advanced driver-assistance systems (ADAS). Similarly, First Sensor AG collaborates with European research institutes and photonics clusters to accelerate the adoption of APDs in quantum communication and medical imaging.
Emerging players in Asia, such as LG Electronics and Samsung Electronics, are investing in APD R&D, particularly for integration into consumer electronics and next-generation imaging modules. These companies benefit from robust semiconductor fabrication infrastructure and are expected to drive down costs through economies of scale.
Looking ahead, the competitive environment is likely to intensify as demand for high-sensitivity, low-noise APDs grows across sectors. Strategic alliances—such as foundry partnerships, co-development agreements, and vertical integration—will be critical for companies seeking to secure supply chains and accelerate innovation. The entry of new players from the broader semiconductor and photonics ecosystem is anticipated, further diversifying the market and fostering technological advancements in APD manufacturing.
Regional Analysis: North America, Europe, Asia-Pacific, and Rest of World
The global landscape for avalanche photodiode (APD) manufacturing in 2025 is characterized by distinct regional strengths, driven by technological expertise, end-user demand, and supply chain dynamics. North America, Europe, and Asia-Pacific remain the primary hubs, while the Rest of World region is gradually emerging, albeit at a slower pace.
North America continues to be a leader in APD innovation, particularly in the United States, where a strong ecosystem of photonics research, defense applications, and telecommunications infrastructure supports domestic manufacturing. Companies such as Hamamatsu Photonics (with significant US operations) and Lumentum are prominent players, supplying APDs for LiDAR, medical imaging, and high-speed optical networks. The region benefits from robust R&D funding and close collaboration between industry and research institutions, which is expected to sustain growth through 2025 and beyond.
Europe maintains a competitive edge in specialty APD manufacturing, with a focus on automotive, industrial, and scientific applications. Germany, France, and the UK host key manufacturers such as First Sensor (now part of TE Connectivity) and Excelitas Technologies, both of which have expanded their APD portfolios to address growing demand in autonomous vehicles and quantum technologies. The European Union’s emphasis on semiconductor sovereignty and investment in photonics R&D is expected to further bolster the region’s manufacturing capabilities in the coming years.
Asia-Pacific is the fastest-growing region for APD manufacturing, led by Japan, China, and South Korea. Japanese firms like Hamamatsu Photonics and Mitsubishi Electric are global leaders, leveraging advanced fabrication processes and strong integration with downstream electronics. In China, domestic manufacturers are rapidly scaling up production to meet surging demand in 5G, data centers, and consumer electronics, supported by government initiatives to localize semiconductor supply chains. South Korea’s focus on optoelectronic components for automotive and mobile devices is also driving investment in APD technology.
Rest of World regions, including parts of Latin America, the Middle East, and Africa, currently play a limited role in APD manufacturing. However, increasing investments in telecommunications infrastructure and scientific research may gradually stimulate local assembly and packaging activities, particularly as global supply chains diversify.
Looking ahead, regional dynamics in APD manufacturing will be shaped by ongoing investments in photonics R&D, government policies on semiconductor self-sufficiency, and the evolving needs of end-user industries such as automotive, telecommunications, and healthcare. Strategic partnerships and technology transfers are likely to further blur regional boundaries, fostering a more interconnected global supply network.
Challenges: Manufacturing Complexity, Cost, and Reliability
Avalanche photodiode (APD) manufacturing in 2025 faces a set of persistent and evolving challenges centered on process complexity, cost control, and device reliability. The APD’s unique internal gain mechanism, which amplifies weak optical signals, requires precise control over semiconductor material quality, doping profiles, and microfabrication steps. This complexity is heightened by the need for high-performance devices in applications such as fiber-optic communications, LIDAR, and medical imaging.
One of the primary manufacturing challenges is the stringent requirement for material purity and defect control. APDs are typically fabricated from silicon for visible and near-infrared detection, or from III-V compound semiconductors such as InGaAs for longer wavelengths. The epitaxial growth of these materials must be tightly controlled to avoid dislocations and impurities that can lead to premature breakdown or excessive dark current, both of which degrade device performance and reliability. Leading manufacturers such as Hamamatsu Photonics and Excelitas Technologies have invested heavily in advanced epitaxy and wafer processing technologies to address these issues.
Device miniaturization and integration with other photonic or electronic components further complicate the manufacturing process. As demand grows for compact, multi-channel APD arrays—especially for automotive LIDAR and high-speed optical networks—manufacturers must ensure uniformity across large wafer areas and maintain tight tolerances in device parameters. This often necessitates the use of advanced lithography, plasma etching, and passivation techniques, which increase both capital and operational costs.
Cost remains a significant barrier to wider APD adoption, particularly in price-sensitive markets. The need for cleanroom environments, high-precision equipment, and rigorous testing protocols drives up production expenses. Companies like First Sensor (a part of TE Connectivity) and onsemi are actively working to streamline manufacturing flows and improve yield, but the inherent complexity of APD structures limits the extent of cost reductions achievable through economies of scale.
Reliability is another critical concern, especially for automotive and aerospace applications where long-term stability under varying environmental conditions is essential. APDs are sensitive to temperature fluctuations, voltage transients, and radiation, all of which can induce performance degradation or catastrophic failure. To address this, manufacturers are developing robust packaging solutions and implementing stringent burn-in and qualification procedures. Hamamatsu Photonics and Excelitas Technologies have published data on extended lifetime testing and environmental screening to demonstrate compliance with industry reliability standards.
Looking ahead, the APD manufacturing sector is expected to continue investing in process automation, in-line metrology, and defect detection to improve yields and reduce costs. However, the fundamental trade-offs between performance, complexity, and reliability will remain central challenges for the industry over the next several years.
Sustainability and Regulatory Developments
Sustainability and regulatory considerations are increasingly shaping the landscape of avalanche photodiode (APD) manufacturing as the industry moves through 2025 and into the coming years. The production of APDs, which are critical components in optical communication, LiDAR, and medical imaging, involves materials and processes that are subject to growing scrutiny regarding environmental impact and compliance with international standards.
A key sustainability challenge in APD manufacturing is the use of semiconductor materials such as silicon, indium gallium arsenide (InGaAs), and other III-V compounds. The extraction and processing of these materials can have significant environmental footprints, prompting manufacturers to adopt greener sourcing and recycling initiatives. Leading APD producers, including Hamamatsu Photonics and Excelitas Technologies, have publicly committed to reducing waste and energy consumption in their facilities, aligning with broader corporate sustainability goals. For example, Hamamatsu Photonics has outlined environmental management systems that address chemical handling, emissions, and resource efficiency across its manufacturing sites.
Regulatory developments are also influencing APD manufacturing. The European Union’s RoHS (Restriction of Hazardous Substances) directive and REACH (Registration, Evaluation, Authorisation and Restriction of Chemicals) regulations continue to drive the reduction of hazardous substances in photonic devices. Manufacturers supplying to global markets must ensure compliance, which often requires reformulation of materials and changes in supply chain management. First Sensor, a subsidiary of TE Connectivity, highlights its adherence to these regulations, ensuring that its APD products meet stringent environmental and safety standards.
In addition, the push for carbon neutrality is prompting APD manufacturers to invest in renewable energy and carbon offset programs. Companies such as Hamamatsu Photonics and onsemi are increasingly reporting on their greenhouse gas emissions and setting targets for reduction, reflecting a broader industry trend toward transparent sustainability reporting.
Looking ahead, the outlook for sustainability in APD manufacturing is shaped by both regulatory pressure and customer demand for environmentally responsible products. As governments introduce stricter environmental policies and as end-users in sectors like automotive and telecommunications prioritize green procurement, APD manufacturers are expected to further innovate in eco-friendly materials, energy-efficient production, and closed-loop recycling. The next few years will likely see increased collaboration between manufacturers, suppliers, and regulatory bodies to establish best practices and industry standards for sustainable photonics manufacturing.
Future Outlook: Disruptive Technologies and Long-Term Market Opportunities
The future of avalanche photodiode (APD) manufacturing is poised for significant transformation as disruptive technologies and evolving market demands shape the industry landscape through 2025 and beyond. APDs, critical for high-sensitivity photodetection in applications such as optical communication, LiDAR, medical imaging, and quantum technologies, are experiencing a surge in innovation driven by both material science advancements and integration trends.
One of the most notable technological shifts is the transition from traditional silicon-based APDs to those utilizing compound semiconductors such as indium gallium arsenide (InGaAs) and germanium. These materials offer superior performance in the near-infrared spectrum, which is essential for next-generation fiber-optic networks and emerging quantum communication systems. Leading manufacturers like Hamamatsu Photonics and Excelitas Technologies are actively expanding their portfolios to include InGaAs APDs, targeting high-speed and low-noise applications.
Another disruptive trend is the integration of APDs with complementary metal-oxide-semiconductor (CMOS) technology. This enables the development of compact, cost-effective, and scalable photonic devices suitable for mass-market applications such as automotive LiDAR and consumer electronics. Companies such as onsemi are investing in CMOS-compatible APD arrays, aiming to deliver high-performance sensors that can be seamlessly integrated into existing electronic systems.
The push towards miniaturization and system-level integration is also fostering the adoption of wafer-level packaging and 3D integration techniques. These approaches not only reduce manufacturing costs but also enhance device reliability and performance. Hamamatsu Photonics and First Sensor AG (a part of TE Connectivity) are at the forefront of these developments, leveraging advanced packaging to meet the stringent requirements of automotive and industrial markets.
Looking ahead, the APD market is expected to benefit from the rapid expansion of 5G/6G networks, autonomous vehicles, and quantum information systems. The demand for high-speed, low-noise, and wavelength-flexible photodetectors will drive further investment in research and manufacturing capacity. Strategic collaborations between device manufacturers, foundries, and system integrators are likely to accelerate the commercialization of disruptive APD technologies.
In summary, the next few years will see avalanche photodiode manufacturing characterized by material innovation, integration with mainstream semiconductor processes, and advanced packaging. These trends are set to unlock new market opportunities and position APDs as a cornerstone technology in the evolving photonics ecosystem.
Sources & References
- Hamamatsu Photonics
- First Sensor AG
- Hamamatsu Photonics
- First Sensor AG
- Lumentum Holdings
- OSRAM Opto Semiconductors
- ID Quantique
- Laser Components
- LG Electronics
- Mitsubishi Electric