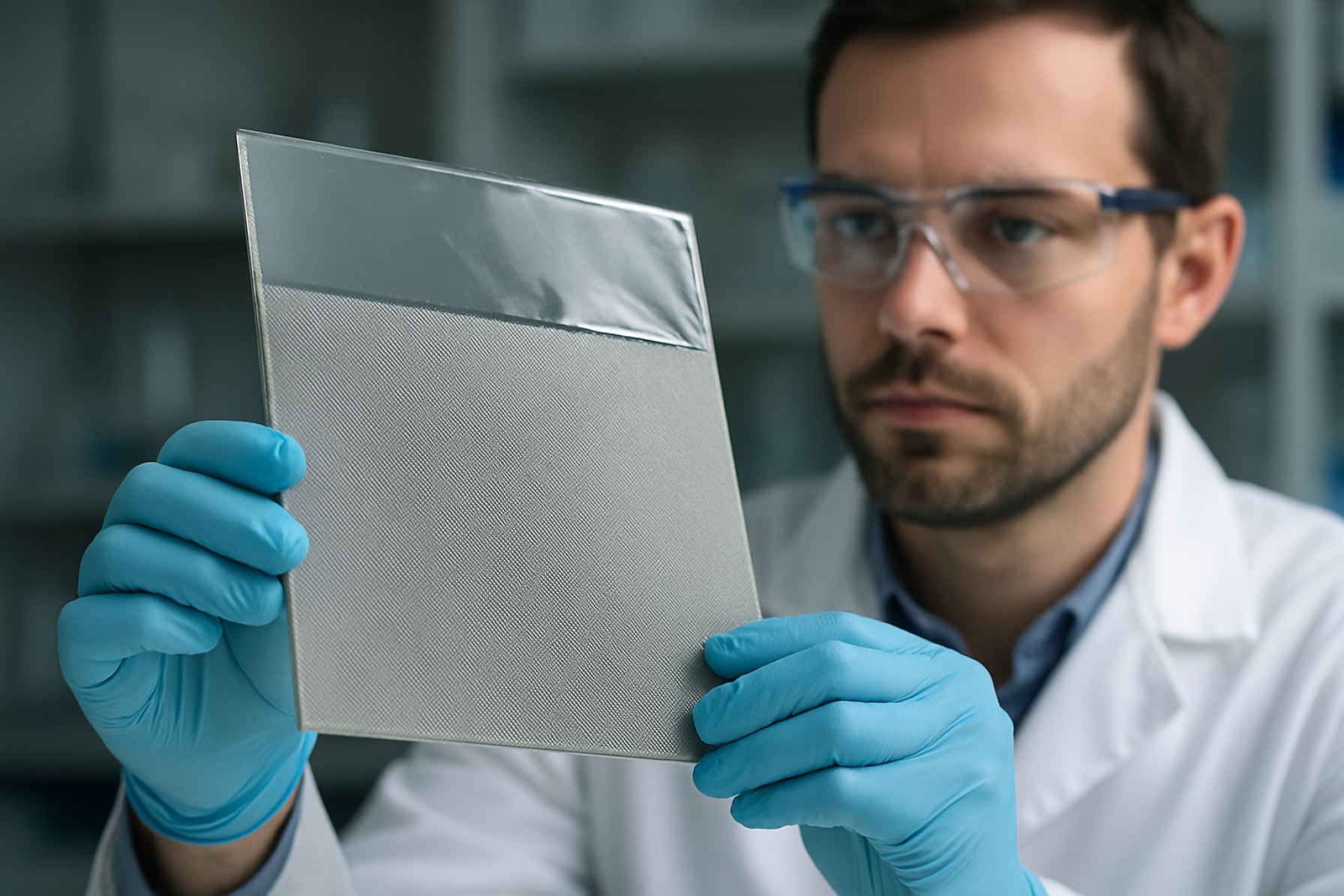
Table of Contents
- Executive Summary: 2025 Market Snapshot and Growth Projections
- Core Fouling Mechanisms and Engineering Solutions
- Key Players and Innovators: Company Profiles and Strategies
- Emerging Materials and Coatings: Next-Gen Fouling Resistance
- Critical Applications: Water Treatment, Energy, Bioprocessing, and More
- 2025–2030 Market Forecasts: Demand, Revenues, and Regional Trends
- Regulatory Drivers and Industry Standards (e.g., ASTM, ISO, IWA)
- R&D Pipeline: Academic and Corporate Innovation Hotspots
- Barriers to Adoption and Commercialization Challenges
- Future Outlook: Disruptive Opportunities and Investment Landscape
- Sources & References
Executive Summary: 2025 Market Snapshot and Growth Projections
Fouling-resistant membrane engineering is emerging as a vital segment within the global filtration and separation market, driven by escalating industrial, municipal, and environmental demands for efficient, low-maintenance water and wastewater treatment solutions. In 2025, the market for advanced anti-fouling membranes is set to see robust growth, propelled by regulatory pressures for sustainability, operational cost reduction, and the necessity for higher membrane longevity and reliability, particularly in sectors such as desalination, pharmaceuticals, food & beverage, and industrial water reuse.
Recent years have witnessed significant advancements in membrane materials and surface modification technologies, including hydrophilic coatings, zwitterionic polymers, and nanocomposite layers designed to minimize organic, inorganic, and biological fouling. Companies such as GE Vernova and Dow are investing in the development and commercialization of next-generation reverse osmosis (RO), ultrafiltration (UF), and nanofiltration (NF) membranes with enhanced fouling resistance and operational efficiency. Notably, Toray Industries and Lenntech continue to expand their portfolios with new anti-fouling membrane modules tailored for challenging feedwaters and demanding applications, leveraging proprietary surface chemistries and advanced fabrication techniques.
In 2025, the industry is witnessing a marked shift toward membranes incorporating sustainable materials and green manufacturing processes, aligning with broader ESG goals. The adoption of bio-inspired and biomimetic surfaces, as explored by SUEZ and Kubota Corporation, is anticipated to offer further performance gains, particularly in municipal wastewater and industrial effluent treatment. Meanwhile, membrane manufacturers are addressing the growing demand for chemically robust, chlorine-tolerant, and abrasion-resistant products to serve expanding markets in Asia-Pacific and the Middle East.
Market projections for 2025 and beyond indicate continued double-digit growth in fouling-resistant membrane sales, with Asia-Pacific leading adoption due to rapid urbanization and water scarcity challenges. Pilot projects and full-scale implementations by utilities and private operators are expected to validate cost savings from reduced cleaning frequency and longer membrane lifespans. Looking ahead, strategic partnerships between technology developers, system integrators, and end-users—alongside ongoing regulatory tightening—will further accelerate innovation and deployment in this segment, positioning fouling-resistant membrane engineering as a cornerstone of next-generation water and process treatment infrastructure.
Core Fouling Mechanisms and Engineering Solutions
Membrane fouling, the undesirable accumulation of particles, colloids, organic matter, and microorganisms on membrane surfaces, remains a primary challenge in water treatment, bioprocessing, and industrial separations. As of 2025, the industry focus is intensifying on engineering advanced fouling-resistant membranes to improve operational efficiency, reduce cleaning frequency, and extend membrane lifespan. Core fouling mechanisms include organic fouling, biofouling, scaling (inorganic fouling), and particulate fouling, each driven by complex interactions between membrane material properties and feed composition.
Recent advancements center on surface modification and material innovation. Hydrophilic coating strategies—using polymers such as poly(ethylene glycol) (PEG) or zwitterionic materials—are being scaled for commercial production, as these coatings reduce adhesion of foulants by forming robust hydration layers. Companies like Toray Industries and DuPont are actively developing and marketing membranes with antifouling surfaces, leveraging both chemical grafting and surface patterning to hinder foulant deposition.
Inorganic nanomaterials, such as titanium dioxide (TiO2) and silver nanoparticles, are also integrated into membrane matrices to impart antimicrobial and anti-adhesive properties, especially relevant in biofouling control. For instance, Lenntech supplies membranes incorporating such nanomaterials to serve high-fouling applications in municipal and industrial settings. Additionally, dynamic membranes—where a sacrificial, easily removed surface layer traps foulants—are entering pilot projects, particularly for wastewater reclamation.
Emerging in 2025, biomimetic approaches draw inspiration from nature, such as fish slime or lotus leaf structures, to design superhydrophilic or patterned surfaces with reduced fouling propensity. While these are largely in the prototype and scale-up phase, select startups and established membrane manufacturers are announcing pilot-scale deployments and collaborative research with academic partners.
From a systems engineering perspective, integration of real-time fouling monitoring is gaining traction. Membrane modules equipped with sensors can detect pressure drops or changes in permeate quality, enabling predictive maintenance and dynamic cleaning schedules. Major suppliers, including SUEZ and Kubota Corporation, are embedding such digital features in their latest membrane product lines.
Looking ahead to the next few years, industry experts anticipate continued convergence of material innovation, process optimization, and digital monitoring. The goal is to achieve membranes that can operate longer between cleanings and handle increasingly challenging water and wastewater streams. Such developments are expected to underpin the expansion of membrane-based solutions in water-scarce regions and in energy-efficient industrial separations.
Key Players and Innovators: Company Profiles and Strategies
The landscape of fouling-resistant membrane engineering in 2025 is shaped by an array of pioneering companies and organizations actively driving innovation and commercialization. The sector continues to witness rapid evolution, propelled by escalating demands for reliable water treatment, sustainable industrial processes, and the minimization of operational costs related to fouling and maintenance.
Key Industry Leaders
- DuPont remains a global leader in membrane technology, leveraging its extensive R&D capabilities to develop advanced reverse osmosis (RO) and ultrafiltration membranes with enhanced anti-fouling surfaces. Their ongoing work involves integrating hydrophilic coatings and novel polymer blends to mitigate organic and biological fouling in municipal and industrial applications (DuPont).
- SUEZ Water Technologies & Solutions continues to invest in next-generation fouling-resistant membranes, with particular emphasis on nanocomposite coatings and bio-inspired surface modifications that reduce microbial adhesion. Their ZeeWeed hollow-fiber ultrafiltration membranes are widely adopted in both water and wastewater treatment plants, with ongoing upgrades aimed at further fouling control (SUEZ).
- Pall Corporation (a subsidiary of Danaher) is recognized for its robust filtration and separation solutions, actively developing new module designs and membrane chemistries to resist particulate and organic fouling in critical sectors such as pharmaceuticals, food & beverage, and microelectronics (Pall Corporation).
- Toray Industries is at the forefront of integrating advanced materials—including graphene oxide and zwitterionic polymers—into membrane surfaces for superior fouling resistance, targeting both desalination and wastewater reuse markets (Toray Industries).
- Koch Separation Solutions is advancing the field through proprietary surface modification techniques and the incorporation of nanoparticles that disrupt foulant accumulation, with a focus on energy efficiency and prolonged membrane lifespan (Koch Separation Solutions).
Strategic Directions and 2025 Outlook
As fouling remains a critical challenge, companies are increasingly adopting multi-pronged strategies—combining surface chemistry innovations, smart monitoring, and predictive maintenance enabled by digital platforms. By 2025, collaborations with academic institutions and industrial partners are expected to accelerate the translation of laboratory breakthroughs into scalable, real-world solutions. Looking ahead, the sector anticipates not only incremental improvements in membrane durability and cleaning intervals but also the emergence of new business models centered around membrane-as-a-service and performance guarantees. As regulatory and environmental pressures grow, the competitive edge will hinge on the ability to deliver membranes that consistently maintain high flux and selectivity, even in challenging feedwater conditions.
Emerging Materials and Coatings: Next-Gen Fouling Resistance
As the global demand for efficient and sustainable water treatment escalates, the development of fouling-resistant membranes stands at the forefront of next-generation filtration technologies. In 2025, membrane fouling—caused by the accumulation of organic matter, microorganisms, and colloids—remains a primary barrier to operational efficiency and longevity in desalination, wastewater reclamation, and industrial separation processes.
Recent advancements focus on both intrinsic material innovation and novel surface modifications. Hydrophilic polymers, such as polyvinyl alcohol (PVA) and zwitterionic materials, are increasingly integrated into membrane matrices, creating surfaces that repel foulants by forming strong hydration layers. Several manufacturers have reported promising results: for instance, membranes embedded with zwitterionic polymers demonstrated up to a 70% reduction in biofouling during pilot-scale seawater desalination operations, with stable flux recovery after extended cycles. This aligns with ongoing research and product development by industry leaders such as Toray Industries and Kubota Corporation, who are actively deploying new hydrophilic coatings in commercial-scale membrane modules.
Plasma surface modification continues to gain traction, enabling the grafting of antifouling functional groups directly onto polymeric membranes without compromising mechanical integrity. These plasma-treated membranes consistently show enhanced resistance to protein and microbial adhesion, a feature now seen in advanced offerings by SUEZ (now part of Veolia), particularly for municipal and industrial water reuse applications.
Another avenue involves the integration of nanomaterials. Nanocomposite membranes incorporating graphene oxide, titanium dioxide, or silver nanoparticles exhibit not only improved fouling resistance but also enhanced antimicrobial activity. For instance, pilot installations using titanium dioxide-embedded membranes have reported a 25% extension in cleaning intervals and a 30% reduction in chemical cleaning requirements, according to field data from DuPont and 3M, both of whom are scaling up the commercialization of such specialized membrane products.
Looking ahead to the next few years, the field is moving toward hybrid solutions that combine multiple antifouling strategies—such as the simultaneous use of hydrophilic coatings and nanoparticle impregnation. The adoption of automated membrane monitoring and predictive maintenance, facilitated by digital sensors, is expected to further optimize the use and lifespan of these advanced membranes. As regulatory pressures on water quality and sustainability rise, industry stakeholders anticipate accelerated integration of fouling-resistant technologies across both new and retrofit projects, ensuring more reliable and cost-effective membrane operations.
Critical Applications: Water Treatment, Energy, Bioprocessing, and More
Fouling-resistant membrane engineering stands at the forefront of innovation across critical applications such as water treatment, energy production, and bioprocessing, addressing persistent challenges associated with membrane fouling that compromise efficiency, lifespan, and operational cost. In 2025 and beyond, the sector is witnessing a pronounced shift toward advanced material science, surface modification, and hybrid membrane technologies to mitigate fouling while meeting stringent industry demands.
In municipal and industrial water treatment, fouling-resistant membranes are pivotal for both desalination and wastewater reclamation. Companies such as Toray Industries and DuPont are commercializing new generations of reverse osmosis (RO) and ultrafiltration membranes featuring enhanced hydrophilic coatings, nanomaterial integration, and anti-microbial surfaces. These advancements are achieving demonstrably lower fouling rates and reduced cleaning frequency, which, according to industry sources, can extend membrane life by 30–50% compared to conventional products. In large-scale desalination plants, the adoption of fouling-resistant modules is expected to help operators achieve higher operational uptime and decrease chemical use for cleaning, aligning with global sustainability goals.
In the energy sector, particularly within the fast-growing hydrogen economy and in power generation cooling systems, membrane-based gas separation and water management processes face acute fouling challenges. Manufacturers such as GE Vernova are advancing fouling-resistant polymeric and ceramic membranes to support reliable hydrogen purification and efficient cooling water reuse. These solutions are critical for scaling up green hydrogen production and for minimizing environmental impact in power plants. The next few years are expected to see broader deployment of membranes with tailored surface chemistries and structure, designed specifically for robustness in harsh operational environments.
Bioprocessing and pharmaceutical manufacturing are also benefitting from these innovations. Companies like Merck KGaA (operating as MilliporeSigma in North America) are introducing fouling-resistant membranes for sterile filtration, protein concentration, and virus removal, which are vital for the production of biologics and vaccines. These membranes exhibit improved throughput and reduced risk of contamination, enabling more reliable and cost-effective processing.
Looking ahead, the global outlook for fouling-resistant membranes is robust, with continued investment in R&D and expected regulatory support for greener, more efficient filtration solutions. Cross-disciplinary collaboration between material scientists, process engineers, and end-users will further accelerate the deployment of membranes with multifunctional anti-fouling, anti-scaling, and self-cleaning properties, setting new standards across water, energy, and bioprocessing industries.
2025–2030 Market Forecasts: Demand, Revenues, and Regional Trends
The market for fouling-resistant membrane engineering is set for significant growth between 2025 and 2030, driven by escalating demand in water treatment, industrial filtration, and bioprocessing. The increasing need for efficient, low-maintenance separation solutions in municipal and industrial sectors, alongside tightening environmental regulations, is expected to catalyze adoption rates for advanced membrane technologies globally.
Asia-Pacific remains the dominant region for membrane technology deployment, propelled by rapid urbanization, industrialization, and ambitious infrastructure projects in countries like China and India. Companies such as Toray Industries and Kubota Corporation are expanding their production capacities and introducing new antifouling membrane products tailored for large-scale municipal and industrial water reuse. The Middle East is also emerging as a key growth region, spurred by investments in desalination and water reuse, with membrane solutions from firms such as SUEZ and Dow increasingly favored due to their enhanced fouling resistance and operational longevity.
North America and Europe are expected to sustain robust demand, particularly in sectors such as pharmaceuticals, food and beverage, and chemicals, where process water quality and regulatory compliance are paramount. Manufacturers like Pall Corporation and GE (through its water & process technologies) are focusing on developing membranes with improved hydrophilic surfaces, antimicrobial coatings, and tailored pore structures to minimize fouling and extend service lifetimes. Notably, these advancements are projected to reduce operating costs and downtime, further strengthening the business case for membrane retrofits and upgrades across existing facilities.
Revenue forecasts for fouling-resistant membrane technologies indicate a compound annual growth rate (CAGR) in the high single digits for the period 2025–2030. Much of this growth is anticipated from the integration of novel materials—such as graphene oxide composites and zwitterionic polymers—by leading suppliers including Toray Industries and SUEZ. The strong pipeline of investments in smart and automated membrane systems, featuring real-time fouling detection and cleaning optimization, is anticipated to further accelerate market development.
Overall, the outlook for fouling-resistant membrane engineering through 2030 is characterized by technological innovation, regional expansion, and a growing emphasis on sustainability and total lifecycle cost reduction. With major industry players scaling up both R&D and manufacturing, the sector is well positioned to meet the intensifying global demand for advanced, low-fouling membrane solutions.
Regulatory Drivers and Industry Standards (e.g., ASTM, ISO, IWA)
Regulatory frameworks and industry standards are set to play a pivotal role in guiding the development and adoption of fouling-resistant membrane technologies through 2025 and the near future. With the increasing demand for efficient water treatment, desalination, and industrial separation processes, regulators and leading organizations are emphasizing performance, safety, and sustainability criteria for membrane materials and systems.
Key standards bodies, such as the ASTM International and the International Organization for Standardization (ISO), are actively updating and expanding their membrane-related standards. ASTM’s Committee D19 on Water and G01 on Corrosion are advancing protocols that address membrane fouling resistance, integrity, and cleaning efficiency, which are crucial for both municipal and industrial applications. ISO’s technical committee TC 282 for Water Reuse and TC 150 for Membrane Processes are similarly updating standards to incorporate new test methods for evaluating fouling propensity and cleaning performance of novel membrane materials.
A significant regulatory driver in 2025 is the push for enhanced water reuse and circular economy solutions, particularly in regions facing water scarcity and strict discharge regulations. The International Water Association (IWA) is working with utilities and manufacturers to define best practices and performance benchmarks for fouling-resistant reverse osmosis (RO), ultrafiltration (UF), and nanofiltration (NF) membranes. These initiatives are influencing purchasing specifications for water utilities and industrial end-users, linking compliance with eligibility for public funding and project approvals.
In the U.S., the Environmental Protection Agency (EPA) and relevant state agencies are expected to reference updated ASTM and ISO standards in their guidance for advanced treatment plants, especially where direct potable reuse is considered. Similar regulatory alignment is anticipated in the European Union as part of the Water Framework Directive and related directives for water reuse and industrial emissions.
Industry leaders, including membrane manufacturers such as Toray Industries and DuPont, are investing in third-party validation and certification based on these evolving international standards. This not only facilitates market access but also helps build customer trust in claims of fouling resistance and extended membrane life.
Looking ahead, the convergence of regulatory drivers, stricter standards, and global sustainability goals is expected to accelerate the adoption of fouling-resistant membrane engineering. Manufacturers and end users who proactively align their products and operations with these evolving benchmarks will be best positioned to thrive in an increasingly regulated and quality-driven market.
R&D Pipeline: Academic and Corporate Innovation Hotspots
Fouling-resistant membrane engineering represents a critical research and development (R&D) frontier in water treatment, bioprocessing, and industrial separations as the sector faces increasing demands for efficiency, sustainability, and operational longevity. In 2025, both academic and corporate laboratories are expanding efforts to address membrane fouling—an issue that significantly increases energy consumption, operational costs, and downtime across applications.
Recent years have seen a surge in collaborative innovation between universities and industrial partners focusing on advanced material science and surface engineering. Academic research hubs, particularly in North America, Europe, and East Asia, continue to pioneer new antifouling membrane materials. For example, leading universities are reporting promising results with zwitterionic polymers, superhydrophilic coatings, and nanocomposite membranes that demonstrate substantial resistance to organic, colloidal, and biological foulants. The translation of these innovations into scalable products, however, relies heavily on corporate engagement and technology transfer mechanisms.
On the corporate side, established membrane manufacturers are rapidly iterating on commercial antifouling technologies. Toray Industries, Inc. and SUEZ are among the sector’s key players investing in R&D facilities dedicated to advanced membrane surface modification and new polymer chemistries. In 2024 and 2025, these companies have reported the development of next-generation reverse osmosis (RO) and ultrafiltration (UF) membranes with improved fouling resistance, leveraging both proprietary surface grafting and nanoparticle embedding techniques.
Additionally, companies such as DuPont and Kubota Corporation are piloting membranes with enhanced antifouling layers, designed specifically for municipal and industrial wastewater reuse. These efforts align with the growing regulatory and sustainability pressures to expand water reuse and reduce chemical cleaning cycles. Notably, Lenntech, a global supplier and integrator, continues to showcase and commercialize advanced fouling-resistant membranes from multiple manufacturers, underscoring a robust supply chain for these innovations.
Looking ahead to the next few years, the R&D pipeline is expected to yield further advances in both membrane surface design and process integration. The incorporation of artificial intelligence for real-time fouling diagnostics and adaptive process control is emerging as a parallel trend, potentially enhancing the operational value of new membrane materials. As industry consortia and public-private partnerships intensify, the sector is poised for accelerated commercialization of fouling-resistant technologies, with a focus on reducing lifecycle costs and enabling broader adoption across challenging water matrices and industrial streams.
Barriers to Adoption and Commercialization Challenges
Fouling-resistant membrane engineering represents a critical frontier in membrane technology, promising to address persistent challenges in water treatment, desalination, and industrial separations. However, despite significant technical progress, several barriers continue to hinder the widespread adoption and commercialization of these advanced membranes as of 2025.
One of the foremost challenges is scaling up laboratory innovations to industrial-scale production. Many fouling-resistant membranes rely on novel surface chemistries or nanomaterials, such as zwitterionic coatings, graphene oxide, or advanced polymer blends. While these approaches have demonstrated excellent anti-fouling performance at the bench scale, translating them into reliable, repeatable manufacturing processes remains difficult. For example, ensuring uniform coating and long-term stability during large-scale fabrication is a complex task, often resulting in increased production costs and variable product quality, as acknowledged by membrane producers like Toray Industries and Hyflux.
Cost competitiveness is another significant barrier. Fouling-resistant membranes often entail higher material and fabrication costs compared to conventional membranes. The need for specialized raw materials, additional surface modification steps, or sophisticated manufacturing equipment drives up the price, making it challenging for these products to compete in cost-sensitive markets, particularly in municipal water treatment and developing regions. Industry leaders such as SUEZ and DuPont have highlighted the importance of balancing advanced functionality with affordability to achieve broader market penetration.
Performance verification and regulatory approval also pose adoption hurdles. Membrane fouling is influenced by a complex interplay of feed composition, operating conditions, and cleaning protocols, necessitating extensive field validation over prolonged periods. End users, such as municipal utilities or industrial operators, require robust data demonstrating sustained anti-fouling performance, mechanical integrity, and chemical resistance under real-world conditions. Standardization bodies and end-users alike are calling for more rigorous, transparent performance benchmarks and testing protocols to facilitate trust and acceptance.
In terms of outlook, industry participants are actively investing in pilot-scale trials, collaborative partnerships, and digital monitoring solutions to accelerate commercialization. For example, Pentair and Lenntech are working to integrate sensors and predictive analytics into membrane systems for early fouling detection and proactive maintenance, which could help bridge the gap between laboratory promise and operational reliability. Nevertheless, overcoming these barriers will require continued innovation in materials science, process engineering, and business models to enable fouling-resistant membranes to achieve their full commercial potential within the next few years.
Future Outlook: Disruptive Opportunities and Investment Landscape
Fouling-resistant membrane engineering is poised to witness significant advancements and investment activity as the global demand for efficient water treatment, desalination, and industrial separation processes intensifies through 2025 and beyond. The persistent challenge of membrane fouling—where contaminants accumulate on membrane surfaces, reducing permeability and operational lifespan—continues to drive innovation in materials science, surface modification, and membrane module design.
Recent years have seen the commercialization of next-generation membrane materials incorporating hydrophilic polymers, zwitterionic coatings, and nanostructured surfaces. These modifications aim to minimize the adhesion of organic, inorganic, and biological foulants, thereby extending cleaning intervals and reducing operational costs. Companies such as Toray Industries and DuPont are actively developing and deploying fouling-resistant reverse osmosis, ultrafiltration, and nanofiltration membranes for municipal and industrial water treatment. For example, Toray Industries has introduced advanced RO membranes with surface modifications that demonstrate reduced fouling propensity in both seawater and brackish water applications.
Simultaneously, the integration of smart monitoring and predictive maintenance technologies—enabled by sensors and data analytics—is expanding. These digital enhancements offer real-time tracking of membrane performance, fouling rates, and cleaning needs, supporting operational efficiency and prolonging membrane lifetime. Companies such as SUEZ (now part of Veolia) have incorporated IoT-driven solutions into their membrane systems, enabling predictive fouling management based on process data.
Looking ahead to 2025 and the following years, disruptive opportunities are expected to arise from several fronts:
- Advanced Materials: The development and scaling of membranes with anti-biofouling and anti-scaling properties—such as those utilizing graphene oxide, modified polyamide layers, or hybrid organic-inorganic surfaces—are attracting research investment. These next-gen materials are anticipated to enter pilot and commercial phases, supported by collaborations between material science startups and established manufacturers like Kuraray.
- Circular Economy and Sustainability: There is growing interest in recyclable membrane modules and green manufacturing processes, aligning with global sustainability goals. Companies leading in membrane recycling and eco-friendly production are poised for increased investment.
- Cross-Sector Applications: Fouling-resistant membranes are expanding beyond water treatment into food and beverage, pharmaceuticals, and resource recovery, creating new market niches and investment opportunities for diversified solution providers.
The investment landscape is characterized by strategic partnerships, venture capital interest, and public-private collaborations. As regulatory standards tighten and water scarcity concerns grow, innovative fouling-resistant membrane solutions are expected to command a premium, positioning key manufacturers and technology developers for robust growth through the second half of the decade.