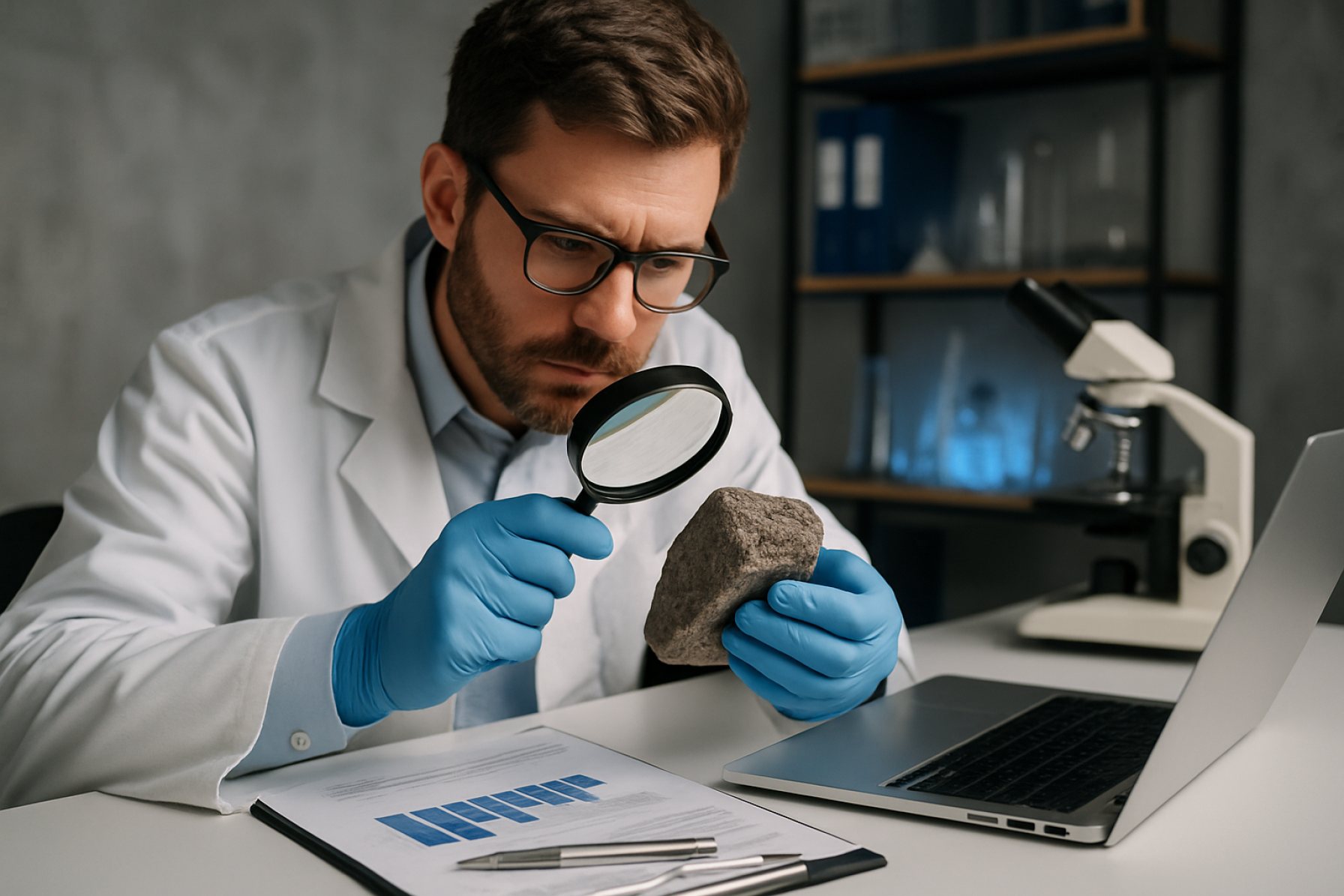
Table of Contents
- Executive Summary: Key Insights and Trends for 2025–2029
- Market Size, Growth Forecasts, and Demand Drivers
- Breakthrough Technologies Transforming Refractory Forensics
- Advanced Analytical Techniques: From SEM to AI-Powered Diagnostics
- Industry Applications: Steel, Cement, Petrochemicals, and More
- Leading Players and Emerging Innovators (e.g., calderys.com, rhi-magnesita.com, worldrefractories.org)
- Regulatory Standards and Compliance Requirements for 2025+
- Case Studies: High-Impact Forensic Investigations and Lessons Learned
- Challenges, Risks, and Opportunities in the Next 5 Years
- Future Outlook: Strategic Recommendations and Innovation Roadmap
- Sources & References
Executive Summary: Key Insights and Trends for 2025–2029
As the global industries reliant on high-temperature processes—such as steel, cement, glass, and non-ferrous metals—face escalating operational and decarbonization demands, the role of refractory forensics analysis is rapidly evolving. Through 2025 and into the latter half of the decade, refractory forensics is positioned as a cornerstone of asset integrity, process optimization, and sustainability initiatives.
Refractory forensics analysis involves the detailed investigation of refractory failures, wear mechanisms, and degradation patterns using advanced diagnostic tools and laboratory techniques. Its goal is to provide root-cause insights that inform material selection, lining design, and maintenance strategies. Leading producers and users, such as RHI Magnesita, Plibrico Company, and Vesuvius, are investing in forensics capabilities to support predictive maintenance and digital transformation of refractory management.
Key trends shaping the sector in 2025–2029 include the integration of digital monitoring and artificial intelligence with traditional forensic techniques. Real-time data from sensors embedded in refractory linings, coupled with AI-driven analysis, enable earlier detection of anomalies and more precise root-cause determinations. This is particularly relevant in the push for longer campaign lives and reduced downtime in energy- and emissions-intensive sectors (RHI Magnesita). The use of advanced analytical methods—such as scanning electron microscopy, X-ray diffraction, and chemical mapping—continues to grow, providing granular insights into failure modes like corrosion, thermal shock, and mechanical wear.
Sustainability is another driver. As carbon reduction targets tighten, industries are implementing alternative fuels and process modifications, directly impacting refractory performance. Forensic analysis is thus essential to swiftly adapt material specifications and extend refractory life in these new conditions (Vesuvius). Companies are also leveraging forensic insights to support circularity, such as reclaiming and reusing spent refractories where possible.
- Increasing adoption of AI and digital twins for predictive forensics and lifecycle management.
- Expanded laboratory and field forensics capabilities among leading refractory producers and end users.
- Rising importance of forensics in meeting regulatory and sustainability objectives.
- Enhanced collaboration between refractory suppliers and end-users to close feedback loops and accelerate innovation.
Looking ahead, refractory forensics analysis is set to become even more integral to industrial operations, as digitalization and sustainability pressures converge. Stakeholders that invest in robust forensic programs and cross-disciplinary expertise will be best positioned to drive operational reliability and meet the evolving demands of the coming years.
Market Size, Growth Forecasts, and Demand Drivers
The market for refractory forensics analysis is projected to register robust growth through 2025 and into the next several years, propelled by increasing demands for operational efficiency, asset longevity, and safety across high-temperature industrial sectors. Refractory forensics analysis—encompassing the post-service evaluation of refractory materials to determine causes of degradation, failure, or wear—has become a vital service in industries such as steel, cement, glass, and non-ferrous metals. As global steel production continues to rise, particularly in regions such as Asia-Pacific, the need for advanced refractory analysis is being amplified to ensure uninterrupted operations and cost control. According to direct industry sources, the global steel industry remains a leading consumer of refractories, with companies like Tata Steel and ArcelorMittal emphasizing improved refractory performance and post-mortem analysis to optimize their processes.
Growth forecasts for refractory forensics analysis closely track broader refractory market trends. As of 2025, major refractory manufacturers such as RHI Magnesita and Vesuvius have reported increased investments in laboratory capabilities and digital diagnostic tools, enabling more sophisticated forensic assessments. These advancements are driven by rising demand for predictive maintenance and data-driven root-cause analysis, particularly as industrial users seek to minimize unscheduled downtime and extend campaign life of their linings.
A key demand driver is the adoption of Industry 4.0 concepts, with integrated sensors and advanced analytics facilitating real-time monitoring of refractory performance. Companies are leveraging these technologies to inform forensic investigations and support continuous process improvement. The cement and glass industries are also increasing their reliance on forensic analysis, as energy efficiency and emissions reduction targets necessitate tighter process controls and higher refractory reliability. For instance, Lafarge (a global cement producer) and Saint-Gobain (a leading glass manufacturer) have both highlighted the critical role of post-service refractory evaluation in their maintenance and sustainability strategies.
Looking ahead to the next few years, demand for refractory forensics analysis is expected to accelerate, supported by stricter regulatory standards, the shift toward green steel and low-carbon production, and increasing capital investment in plant modernization. As industries expand their focus on lifecycle management and digitalization, forensic analysis services are set to become an indispensable element in both failure prevention and sustainability initiatives.
Breakthrough Technologies Transforming Refractory Forensics
Refractory forensics analysis is undergoing significant transformation as advanced diagnostic technologies and data-driven methodologies reshape how failures and material degradation are understood and prevented. As of 2025, the integration of high-resolution analytical tools, digitalization, and real-time monitoring systems is revolutionizing the field, offering unprecedented insight into the performance and lifespan of refractory linings used in high-temperature industrial processes.
One of the most notable breakthroughs is the growing deployment of advanced scanning electron microscopy (SEM) combined with energy-dispersive X-ray spectroscopy (EDS). Leading suppliers such as RHI Magnesita and Vesuvius are leveraging these techniques to pinpoint microstructural changes, corrosion patterns, and elemental mapping at a granular level, enabling root cause analysis of refractory failures with far greater precision than traditional methods. These powerful tools allow for the detection of early-stage degradation and chemical infiltration, providing operators with actionable data to refine maintenance strategies and material selection.
In parallel, non-destructive testing (NDT) technologies are advancing rapidly. Laser-induced breakdown spectroscopy (LIBS) and portable X-ray fluorescence (XRF) analyzers are now being increasingly adopted for on-site refractory analysis, offering real-time composition and contamination assessment without removing or destroying material. This capability is critical for continuous process industries such as steel, cement, and glass, where downtime and invasive inspections are costly. Companies like Vesuvius are developing proprietary diagnostic tools that integrate these technologies, helping clients maintain refractory integrity while minimizing operational disruptions.
Digitalization and Industrial Internet of Things (IIoT) solutions are further enhancing forensic analysis by enabling continuous monitoring of refractory health. Embedded sensor technologies—such as thermocouples, acoustic emission sensors, and fiber optic temperature measurement—are being integrated into refractory linings to collect real-time data on temperature gradients, hot spots, and mechanical stress. This data is analyzed using AI-driven platforms to predict failure and optimize replacement cycles, a trend championed by key industry players including RHI Magnesita.
Looking forward, the next few years are expected to see increased adoption of remote diagnostic platforms and digital twins for refractory assets, allowing predictive forensics and virtual simulation of failure scenarios. As the industry continues to emphasize sustainability and operational efficiency, these technological advances are set to become standard practice, radically improving reliability and lifecycle management of refractory systems.
Advanced Analytical Techniques: From SEM to AI-Powered Diagnostics
In 2025, refractory forensics analysis is experiencing a transformative evolution, propelled by advanced analytical techniques that integrate both traditional and cutting-edge methodologies. The primary goal of refractory forensics is to decipher the root causes of failure, wear, or unexpected performance in refractory linings, with direct implications for industries such as steel, cement, and glass manufacturing.
Scanning Electron Microscopy (SEM) remains a cornerstone in microstructural analysis. SEM, often coupled with Energy Dispersive X-ray Spectroscopy (EDS), enables high-resolution imaging and elemental mapping of damaged or worn refractory surfaces, revealing mechanisms such as corrosion, thermal shock, or mechanical erosion. In 2025, leading refractory producers and industrial users continue to invest in in-house SEM/EDS capabilities to expedite failure investigations and improve material design (RHI Magnesita, Vesuvius).
Simultaneously, X-ray Diffraction (XRD) and Electron Probe Microanalysis (EPMA) have become integral for phase identification and quantitative analysis. These techniques assist in elucidating phase transformations, reaction layers, and possible contaminant ingress. The increasing automation and data integration in XRD and EPMA systems are reducing turnaround times and enhancing the reliability of forensics data.
A significant development in 2025 is the convergence of these established techniques with artificial intelligence (AI). AI-powered diagnostics now process vast datasets from SEM, XRD, and other sources, accelerating pattern recognition and anomaly detection. Machine learning algorithms are being trained on extensive failure case libraries to predict likely root causes, suggest remediation strategies, and even propose new refractory formulations. These AI tools are being implemented both by leading refractory suppliers and end-users in process industries to reduce downtime and optimize maintenance cycles (Imerys).
Another emerging trend is the deployment of portable, non-destructive testing (NDT) tools for in situ refractory assessment. Handheld XRF analyzers, infrared thermography, and ultrasonic testing devices are now commonly used for preliminary diagnostics, feeding real-time data into centralized AI systems for instant analysis and reporting. This integration is streamlining decision-making on plant floors and reducing the reliance on off-site laboratory analysis.
Looking ahead, the outlook for refractory forensics analysis is defined by greater digitalization, predictive analytics, and collaborative data sharing across supply chains. As AI models mature and databases expand, the sector is poised for more proactive maintenance and the engineering of longer-lasting, failure-resistant refractory solutions—crucial for energy-intensive industries navigating tighter operational margins and sustainability targets.
Industry Applications: Steel, Cement, Petrochemicals, and More
Refractory forensics analysis has become increasingly vital for industries such as steel, cement, petrochemicals, and others that rely on high-temperature processes. These sectors face mounting pressures in 2025 to minimize downtime, enhance operational safety, and reduce costs—all directly impacted by the performance and longevity of refractory linings. Forensics analysis involves systematic examination of failed or worn refractory materials to determine failure modes, root causes, and to recommend improvements in material selection, installation, and operational practices.
In the steel industry, refractory forensics is closely tied to the drive for increased production efficiency and sustainability. Steel plants are intensifying efforts to understand corrosion, spalling, and erosion of refractories in critical units such as blast furnaces, ladles, and tundishes. For example, leading manufacturers like RHI Magnesita and Vesuvius are offering advanced diagnostic services and post-mortem analyses to help steelmakers extend refractory campaign life and adapt to alternative fuels or recycled raw materials, which introduce new chemical and thermal stresses.
The cement industry, facing stricter emissions regulations and growing use of alternative fuels, is also ramping up investment in refractory forensics. Kiln shell hotspots, alkali attack, and thermal shock are recurring issues. Companies such as Imerys and Calderys have recently expanded analytical services, using tools like scanning electron microscopy (SEM) and X-ray diffraction (XRD) to identify microstructural changes, contaminant penetration, and phase transformations in used linings.
In petrochemicals and refining, refractory analysis is critical for reactors, reformers, and crackers where unplanned outages can result in significant financial losses. The sector is witnessing an uptick in forensic investigations focused on cracking, glaze formation, and chemical attack by process media. Firms such as Morgan Advanced Materials provide post-service analysis and material characterization to optimize refractory selection for complex chemical environments.
Looking forward, the next few years will see the adoption of digital tools—such as AI-based pattern recognition and predictive analytics—integrated with traditional forensic techniques. Industry leaders are forming partnerships with equipment suppliers to enable real-time refractory condition monitoring, aiming for predictive maintenance rather than reactive repairs. As more industrial operators embrace circular economy models and alternative feedstocks, the demand for robust, data-driven refractory forensics will only intensify, setting new benchmarks for material performance and lifecycle optimization.
Leading Players and Emerging Innovators (e.g., calderys.com, rhi-magnesita.com, worldrefractories.org)
The landscape of refractory forensics analysis in 2025 is shaped by a combination of established global leaders and dynamic emerging innovators. As the industrial demand for higher performance and longevity in refractory materials intensifies, key players are leveraging advanced forensic analysis to drive product development, optimize failure investigations, and enhance lifecycle management.
Among the industry giants, Calderys continues to invest in cutting-edge laboratories and analytical technologies. Their forensic teams utilize advanced microscopy, chemical analysis, and simulation tools to dissect root causes of refractory failures, supporting industries such as steel, cement, and petrochemicals in minimizing costly downtimes. Similarly, RHI Magnesita, another global leader, has expanded its capabilities in digital forensics, employing big data analytics and artificial intelligence to detect wear patterns, corrosion mechanisms, and thermal damage in high-temperature linings.
On the organizational front, the World Refractories Association (WRA) facilitates collaboration and standardization efforts for forensic methodologies. In 2024 and 2025, WRA-supported initiatives have focused on harmonizing analytical protocols and sharing best practices, leading to greater consistency in failure analysis and reporting across member companies.
Emerging innovators are propelling the sector forward by integrating novel analytical approaches. Startups and research-driven SMEs are introducing portable spectroscopic devices, rapid microstructural mapping techniques, and machine learning algorithms tailored for complex refractory systems. These advancements allow faster on-site diagnostics, reducing the need for prolonged shutdowns and enabling predictive maintenance strategies.
The competitive landscape is also being shaped by increased cross-sector collaboration. Major refractory producers are partnering with academic research institutes and technology providers to co-develop new forensic tools and training modules. For example, digital twins and real-time monitoring sensors are being trialed in pilot projects to provide continuous feedback on refractory health, shortening the forensic loop and informing design improvements.
Looking ahead, the outlook for refractory forensics analysis is robust. With decarbonization and sustainability targets placing greater scrutiny on materials’ lifecycle performance, the ability to rapidly and accurately diagnose refractory issues will be critical. Industry leaders and innovators alike are expected to further integrate digital technologies, automation, and standardized procedures, reinforcing the importance of forensic analysis as a cornerstone of refractory management and innovation well beyond 2025.
Regulatory Standards and Compliance Requirements for 2025+
The regulatory landscape for refractory forensics analysis is evolving rapidly as industries such as steel, cement, glass, and petrochemicals face increasing scrutiny regarding safety, environmental compliance, and material integrity. In 2025 and the coming years, regulatory bodies and industry organizations are expected to enforce more stringent standards for the investigation and reporting of refractory failures, with a strong focus on traceability, documentation, and process transparency.
One of the key drivers for enhanced compliance requirements is the adoption of harmonized global standards, such as those established by the International Organization for Standardization (ISO) and ASTM International. Standards like ISO 1927 (monolithic refractory products testing) and ASTM C1338 (analysis of refractory corrosion) are being referenced with greater frequency in audits and compliance checks. Regulatory authorities are increasingly mandating that forensics laboratories and refractory suppliers adhere to these protocols when performing root cause failure analysis and generating compliance documentation.
Environmental regulations are also shaping practices in refractory forensics. With the European Union’s tightening of industrial emissions limits under the Industrial Emissions Directive (IED) and similar regulatory movements in North America and Asia, forensic analyses must now account for the environmental impact of refractory breakdowns, particularly concerning hazardous material release and waste management. This trend is pushing suppliers and service providers to invest in advanced analytical techniques and certified laboratory processes to ensure their reports meet regulatory expectations.
Additionally, digitalization is playing a significant role. The increasing implementation of digital record-keeping and traceability tools—such as those promoted by leading industry players like RHI Magnesita and Vesuvius—is helping to ensure that forensic analysis workflows and results are fully auditable and compliant with both internal and external standards. These companies are integrating real-time data capture, laboratory information management systems (LIMS), and secure reporting mechanisms to satisfy evolving compliance frameworks and to facilitate rapid response in the event of a regulatory inquiry.
Looking ahead, the outlook for refractory forensics analysis is characterized by a tightening of regulatory oversight and a growing expectation for robust, science-based investigative processes. Laboratories and manufacturers will need to maintain accreditation, stay current with standard revisions, and demonstrate the use of validated, reproducible testing methodologies. Collaboration with industry bodies such as Tata Steel and compliance with sectoral guidelines will be essential for maintaining market access and minimizing operational risks as regulatory frameworks continue to mature through 2025 and beyond.
Case Studies: High-Impact Forensic Investigations and Lessons Learned
In recent years, refractory forensics analysis has played an increasingly critical role in diagnosing root causes of high-profile refractory failures, enabling the development of more robust materials and optimized installation techniques. The period leading into 2025 has seen a marked rise in the sophistication of forensic investigations, driven by advances in analytical methods and a greater emphasis on life-cycle management within high-temperature industries.
One notable case involved a large European steel manufacturer that experienced premature wear of ladle linings, resulting in unplanned outages and significant production losses. Through detailed post-mortem analysis, including scanning electron microscopy (SEM) and X-ray diffraction (XRD), investigators identified that the main cause was alkali infiltration from slag, which reacted with the lining’s magnesia-carbon composition. The findings led to the adoption of a new binder system with enhanced alkali resistance, extending the lining life by over 20% and reducing maintenance downtime. Such outcomes have spurred other steelmakers to initiate proactive forensic studies, integrating continuous monitoring and rapid response protocols to minimize costly failures (RHI Magnesita).
In the cement industry, a 2024 incident at a major North American kiln operator highlighted the impact of improper brick installation and uncontrolled thermal cycling. Forensic analysis revealed that microcracking in the basic brick lining stemmed from uneven heating during startup and shutdown, leading to catastrophic spalling. The investigation prompted the operator to revise start-up procedures and invest in advanced thermomechanical simulation tools to predict stress points, setting a new industry benchmark for operational best practices (Vesuvius).
The glass sector has also benefited from forensic approaches. In one 2023 case, a float glass producer faced recurring glass defects traceable to alumina-silicate refractory corrosion. Detailed chemical mapping pinpointed the ingress of volatile sodium compounds, which had not been adequately accounted for in the original design. The subsequent switch to a high-purity fused cast refractory specification significantly reduced defect rates and improved overall furnace campaign life (Saint-Gobain).
Looking ahead to 2025 and beyond, refractory forensics is poised to become even more integral to asset management, with digitalization and machine learning increasingly leveraged for predictive diagnostics. As high-temperature industries continue to push operational limits, the lessons from these investigations will guide the development of advanced refractories and smarter monitoring systems, ensuring greater reliability and lower total cost of ownership.
Challenges, Risks, and Opportunities in the Next 5 Years
The refractory industry faces a dynamic landscape in the coming years, with forensics analysis playing a pivotal role in addressing challenges, mitigating risks, and unlocking new opportunities. The growing complexity of high-temperature industrial processes—especially in steel, cement, and nonferrous metallurgy—demands ever-greater scrutiny of refractory failure modes and root causes. As plants operate at higher intensities, the cost of unscheduled downtime and safety incidents linked to refractory degradation is rising, underscoring the need for robust forensics capabilities.
One key challenge is the evolution of refractory chemistries to accommodate decarbonization and cleaner fuel transitions. For instance, hydrogen-based steelmaking and alternative kiln fuels can introduce atypical chemical environments, accelerating wear mechanisms such as alkali attack or carbon deposition. Forensics teams must update analytical protocols to identify unfamiliar failure signatures and inform material selection. Leading suppliers like RHI Magnesita and Vesuvius are investing in advanced diagnostic laboratories and digital platforms to support this evolution, leveraging techniques from SEM-EDS to AI-assisted pattern recognition.
Data integration and digitalization present another opportunity—and risk. The adoption of Industry 4.0 tools enables continuous condition monitoring, allowing for predictive failure analytics rather than reactive investigations. While this can enhance the effectiveness of forensics, it also requires secure, interoperable data platforms and new skill sets among analysts. Companies such as Morgan Advanced Materials are actively developing digital twins and remote monitoring solutions to enable proactive root cause analysis and shorten investigative cycles.
A persistent risk is the shortage of experienced forensic specialists, as retirements outpace new talent entering the field. The demand for multidisciplinary expertise—spanning materials science, process engineering, and data analytics—will intensify, necessitating new training partnerships and knowledge-sharing initiatives. Industry bodies such as The Institute of Refractories Engineers are expanding certification programs and technical exchanges to address the skills gap.
Over the next five years, the opportunities in refractory forensics analysis will center on leveraging data-driven insights to extend asset lifecycles, reduce environmental impact, and drive innovation in material design. Firms that invest in integrated forensics—combining laboratory expertise with digital monitoring and cross-industry collaboration—will be best positioned to adapt to shifting process demands and regulatory pressures, ensuring both operational resilience and market leadership.
Future Outlook: Strategic Recommendations and Innovation Roadmap
Looking ahead to 2025 and beyond, the field of refractory forensics analysis is poised for significant transformation, driven by advancements in materials science, digitalization, and heightened demands for process efficiency and sustainability. The strategic outlook for industry stakeholders encompasses both adopting new technologies and evolving operational paradigms to meet increasingly complex performance and regulatory requirements.
A primary trend is the integration of advanced analytical and diagnostic tools—such as high-resolution scanning electron microscopy (SEM), energy-dispersive X-ray spectroscopy (EDS), and digital twin modeling—into routine refractory failure investigations. These technologies enable more precise identification of wear mechanisms, chemical interactions, and microstructural changes within refractory linings, supporting root-cause analysis and proactive maintenance strategies. Leading refractory producers such as RHI Magnesita and Vesuvius are already investing in digital laboratories and remote diagnostic services, signaling an industry-wide shift toward data-driven forensics.
Strategic recommendations for manufacturers and end-users center on fostering cross-disciplinary collaborations between material scientists, plant engineers, and digital experts. This approach is essential for translating forensic findings into actionable design improvements and operational protocols. The adoption of predictive maintenance programs—leveraging machine learning algorithms and IoT-based monitoring—will likely become standard practice in high-value sectors such as steelmaking, cement, and non-ferrous metallurgy. These initiatives are expected to reduce unplanned downtime and optimize refractory lifespans, offering clear economic and sustainability benefits.
Innovation roadmaps for the next few years highlight the need to develop next-generation refractory materials with enhanced resistance to thermal shock, corrosion, and mechanical stress. This requires ongoing investment in R&D and collaboration with academic institutions as well as direct feedback loops from forensic analysis outcomes. For example, companies like Krosaki Harima Corporation and Imerys are expanding their R&D activities to include AI-driven materials design and rapid prototyping, enabling faster iteration cycles from laboratory to industrial validation.
In summary, the future of refractory forensics analysis is characterized by digital transformation, material innovation, and closer industry-academia partnerships. The next few years will see forensic methodologies become integral not only to failure analysis but also to continuous improvement and sustainability initiatives across the refractory value chain. Industry participants who proactively invest in these areas are expected to gain competitive advantages in operational reliability, safety, and environmental performance.