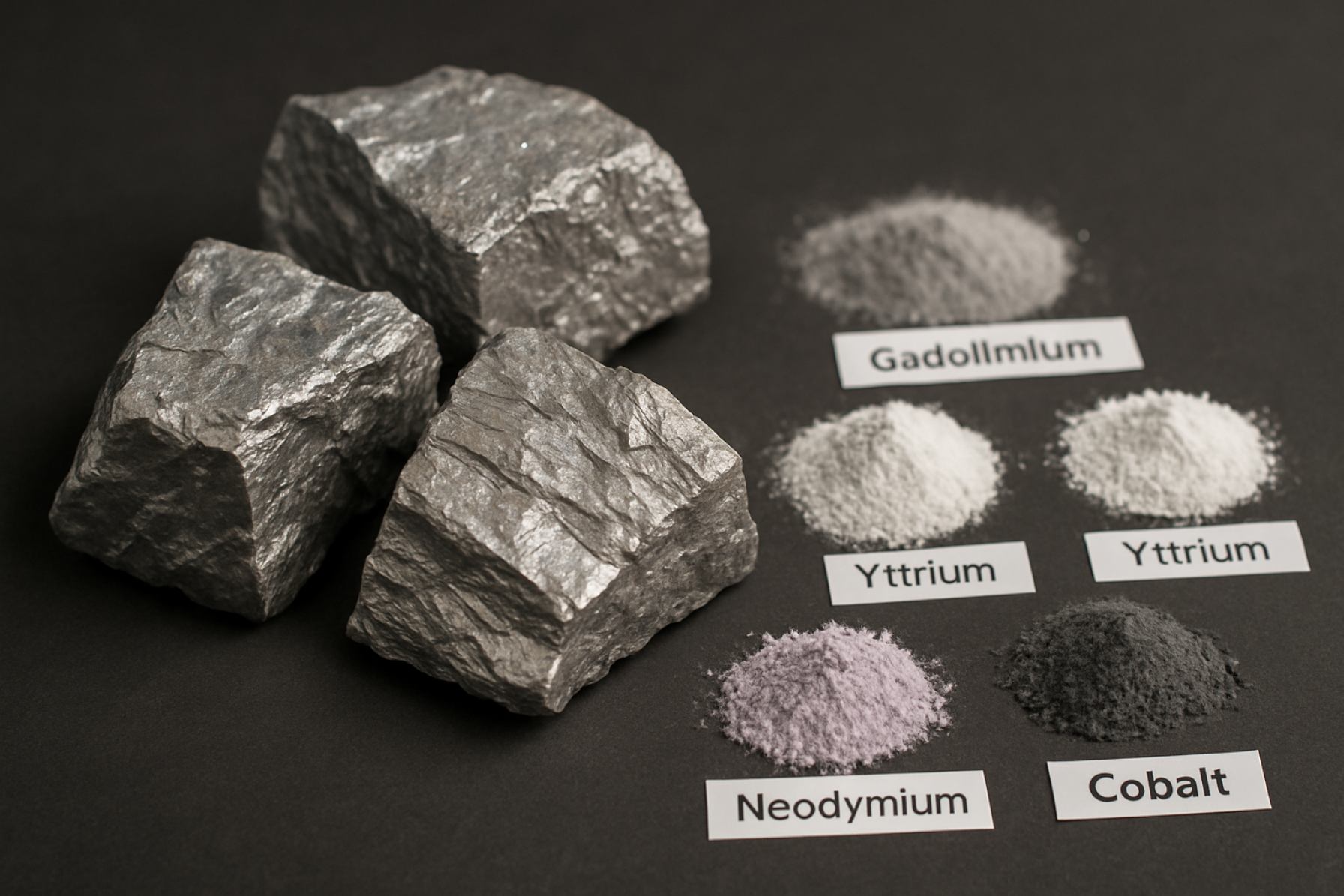
Table of Contents
- Executive Summary: 2025 and Beyond
- Market Size & Forecast: Growth Trajectories to 2030
- Breakthrough Technologies & Process Innovations
- Key Global Players and Recent Strategic Moves
- Supply Chain Dynamics & Raw Material Security
- Core Applications: Aerospace, Electronics, and Beyond
- Regulatory Standards and Industry Compliance
- Investment Hotspots and Funding Trends
- Sustainability Initiatives and Environmental Impact
- Future Outlook: Emerging Opportunities & Challenges
- Sources & References
Executive Summary: 2025 and Beyond
The rare earth quaternary alloy manufacturing sector is entering a period of significant transformation in 2025, driven by escalating demand for advanced materials in clean energy, electronics, and defense technologies. Quaternary alloys—complex mixtures of four or more rare earth elements with transition metals—offer enhanced magnetic, thermal, and corrosion-resistant properties. These characteristics are pivotal for next-generation permanent magnets, high-temperature-resistant components, and specialized electronic devices.
Production capabilities are expanding, particularly in Asia and North America, as nations seek to secure supply chains and reduce dependence on single-country sources. China, which remains the dominant player in rare earth refining and alloy production, continues to invest in process innovation and environmental compliance. Companies such as Chinalco and China Rare Earth Group are scaling up both capacity and R&D to meet domestic and international demand, with an emphasis on quaternary alloys tailored for electric vehicle (EV) motors, wind turbines, and advanced defense applications.
In North America, MP Materials is advancing downstream integration, moving from concentrate production to alloy manufacturing. Their initiatives, supported by public-private partnerships, focus on establishing a reliable domestic supply of rare earth alloys for the U.S. defense and automotive sectors. Similarly, LANXESS in Europe is investing in rare earth alloy capabilities, aligning with EU strategies for raw material security and green technology leadership.
Key events shaping the sector in 2025 include the commissioning of new alloy plants, ongoing joint ventures between mining and technology firms, and the implementation of stricter environmental standards. Data from industry bodies indicate a projected annual growth rate of 7-10% for rare earth alloy demand through 2028, underpinned by the rapid adoption of EVs and renewable energy infrastructure.
Challenges persist, notably in raw material sourcing, technological complexity, and the recycling of end-of-life components. However, ongoing research into process optimization and alternative feedstocks, including secondary sources, is expected to enhance both sustainability and supply resilience. Strategic collaborations between producers, automotive OEMs, and energy companies will likely accelerate innovation and commercialization of new quaternary alloy compositions.
Looking ahead, the rare earth quaternary alloy manufacturing industry is poised for robust growth, with diversification of supply chains and technological advancements at its core. Stakeholders must continue to prioritize environmental stewardship and strategic investments to capture emerging opportunities and navigate evolving regulatory landscapes.
Market Size & Forecast: Growth Trajectories to 2030
The global rare earth quaternary alloy manufacturing sector is positioned for robust growth through 2030, driven by escalating demand across high-performance magnets, advanced electronics, renewable energy systems, and emerging defense applications. By 2025, production capacity expansions and technological innovations are anticipated to reshape the competitive landscape, with leading producers investing in vertically integrated supply chains and advanced metallurgical processes.
As of 2025, key players such as LKAB, The Chemours Company, and Nornickel are actively scaling up their output of rare earth alloys, including neodymium, samarium, and dysprosium-based quaternary compositions. These alloys are critical for next-generation permanent magnets used in electric vehicles (EVs), wind turbines, and miniaturized electronics. Industry data indicates that global demand for advanced rare earth alloys, particularly quaternary systems, is projected to grow at a compound annual growth rate (CAGR) exceeding 8% through 2030, with the Asia-Pacific region maintaining its dominance in both production and consumption.
China remains the principal supplier of rare earth alloys, accounting for over 60% of worldwide output. However, policy initiatives and new investments in North America and Europe are expected to moderately diversify supply. For instance, LKAB is advancing its REE processing complex in Sweden, aiming to bolster Europe’s capacity for producing rare earth alloys and mitigate dependence on imports. Similarly, The Chemours Company has announced plans to increase its rare earth separation and alloy production capabilities in the United States, targeting strategic sectors such as aerospace and defense.
Technological progress in metallurgical engineering is also driving higher yields and improved quality in quaternary alloy manufacturing. Companies are investing in proprietary melting, casting, and powder metallurgy techniques to enhance uniformity, reduce impurities, and enable tailored alloy compositions for specific industrial needs. The introduction of closed-loop recycling initiatives is further expected to supplement primary production and support sustainability objectives, as promoted by organizations such as Nornickel through their expanded circular economy programs.
Looking ahead, the rare earth quaternary alloy market is projected to surpass $2.5 billion by 2030, underpinned by surging adoption in EV powertrains, renewable energy infrastructure, and miniaturized electronics. Strategic investments by established producers and new entrants, coupled with government-backed supply chain initiatives, will likely shape the market’s trajectory, with ongoing focus on security of supply, product innovation, and environmental stewardship.
Breakthrough Technologies & Process Innovations
The manufacturing of rare earth quaternary alloys—materials composed of four different rare earth elements or combinations with transition metals—has seen significant technological breakthroughs entering 2025. This sector, vital for next-generation magnets, hydrogen storage, and advanced electronics, is experiencing a shift driven by both global demand for high-performance materials and supply chain resiliency concerns.
A prominent innovation in 2025 is the adoption of advanced powder metallurgy processes, such as spark plasma sintering (SPS) and high-pressure inert gas atomization. These techniques enable the production of ultra-fine, highly homogeneous alloy powders, reducing contamination and ensuring consistent microstructure. For example, Hitachi Metals has intensified its R&D in SPS, targeting improved energy efficiency and reduced cycle times in quaternary alloy fabrication. Simultaneously, Sumitomo Metal Mining is leveraging inert gas atomization to deliver tailored alloy chemistries for high-coercivity magnets, essential for electric vehicles and wind turbines.
Another 2025 milestone is the integration of artificial intelligence and machine learning into process control. By implementing real-time monitoring of alloying elements and phase evolution, manufacturers can now achieve tighter tolerances and optimize rare earth utilization. LKAB and Australian Mines are collaborating on digital twin models, enabling predictive adjustments during alloy synthesis, thus minimizing waste and improving yield.
Environmental sustainability is also at the forefront of process innovation. Closed-loop recycling systems for rare earth scrap are being scaled up, dramatically reducing the environmental footprint of quaternary alloy production. UrbanMines, a recycler and supplier, has launched pilot plants for recovering and remanufacturing rare earth alloys from end-of-life electronics using hydrometallurgical separation coupled with solvent extraction, which is projected to become a standard practice by 2027.
Looking ahead, the outlook for rare earth quaternary alloy manufacturing is marked by continued investment in automation, advanced separation technologies, and green chemistry approaches. As global industries accelerate the transition to electrification and digitalization, demand for these specialty alloys is expected to rise sharply. Industry leaders anticipate further breakthroughs in additive manufacturing (3D printing) of complex alloy geometries, with pilot deployments already underway at facilities operated by Advanced Alloys and other major producers. The coming years are poised to deliver higher performance materials, greater supply security, and a reduced environmental impact, solidifying quaternary alloys’ role in critical technologies.
Key Global Players and Recent Strategic Moves
The rare earth quaternary alloy manufacturing sector has witnessed significant strategic activity among leading global players entering 2025, as the demand for advanced magnetic, electronic, and energy materials continues to rise. These alloys, typically comprising four rare earth elements or a combination of rare earths with transition metals, are essential for high-performance magnets, hydrogen storage, and various clean energy technologies.
China retains its dominant position in rare earth alloy production, with state-backed enterprises such as Aluminum Corporation of China (Chinalco) and China Molybdenum Co., Ltd. expanding vertically integrated operations. In early 2024, Chinalco announced upgrades to its alloy manufacturing lines, incorporating advanced separation and alloying technologies to improve the consistency and performance of quaternary alloys for the EV and wind power sectors. Meanwhile, Baotou Steel Rare-Earth—the world’s largest rare earth supplier—initiated collaborative R&D partnerships with downstream magnet producers to co-develop custom quaternary alloy compositions targeting ultra-high coercivity for next-generation motors.
Outside China, Japanese manufacturers such as Hitachi Metals (now part of Proterial) have intensified R&D investments, aiming to secure supply chains and proprietary alloy formulations. In mid-2024, Hitachi Metals completed a major capacity expansion for rare earth alloy melting and strip casting, designed to serve both domestic and international partners in the automotive and electronics industries. South Korea’s POSCO has also entered the market, leveraging its metallurgical expertise to develop high-purity quaternary alloys for green hydrogen and energy storage applications, with a pilot plant established in late 2023.
- Strategic Alliances and Supply Chain Diversification: In the wake of supply chain disruptions, Western firms are actively seeking non-Chinese sources and joint ventures. Lynas Rare Earths from Australia, for example, has signed multi-year supply and R&D agreements with European advanced materials companies to co-produce specialty quaternary alloys, focusing on traceability and sustainability.
- Technology Transfer and Localization: North American initiatives, led by MP Materials, include new alloying facilities in the US to localize magnet and alloy production, with pilot-scale quaternary alloy output commencing in 2025 to support domestic electronics and defense sectors.
Looking forward, the global rare earth quaternary alloy market is expected to see further capacity expansions, deeper vertical integration, and intensified R&D collaboration. Strategic moves by leading players aim to address not only surging demand but also the growing imperative for supply chain resilience, regional self-sufficiency, and advanced material innovation.
Supply Chain Dynamics & Raw Material Security
The supply chain dynamics and raw material security for rare earth quaternary alloy manufacturing are under significant scrutiny in 2025. Rare earth quaternary alloys—comprising four different rare earth elements and/or metals—are critical for high-performance magnets, hydrogen storage, advanced catalysts, and emerging green technologies. However, their supply chain is complex, spanning resource extraction, separation, alloying, and distribution, each stage susceptible to geopolitical and logistical disruptions.
China continues to dominate the upstream supply of rare earth oxides and metals, accounting for more than 60% of global production and an even higher share in refined products. Leading Chinese conglomerates, such as Aluminum Corporation of China and China Molybdenum Co., maintain extensive mining and processing operations, ensuring a steady domestic supply for alloy manufacturers. However, export controls implemented in recent years, particularly on high-value rare earth compounds, have increased uncertainty and spurred global diversification efforts.
Outside China, countries such as Australia and the United States have accelerated investments in mining and downstream processing. Lynas Rare Earths in Australia remains the largest non-Chinese producer, supplying strategic feedstocks to alloy plants in Japan and Europe. In the U.S., MP Materials has expanded its Mountain Pass operations and is advancing domestic separation and alloying capabilities to serve North American markets. These initiatives aim to secure supply for critical industries and reduce reliance on Chinese exports.
The manufacture of quaternary alloys is also dependent on availability and purity of transition metals such as cobalt, nickel, and iron. Volatile pricing and mining risks—particularly for cobalt sourced from the Democratic Republic of Congo—add complexity to raw material security. As a result, manufacturers are increasingly pursuing long-term offtake agreements and exploring recycling as a supplementary source of rare earth elements and metals.
Looking ahead, the global rare earth quaternary alloy supply chain is expected to remain tight through 2025 and beyond, as demand from electric vehicles, wind power, and defense sectors outpaces new supply. Governments and industry consortia are investing in alternative sources, recycling technologies, and robust certification systems to ensure traceability and security of supply. The success of these efforts will likely shape the competitive landscape for rare earth alloy manufacturing over the next several years.
Core Applications: Aerospace, Electronics, and Beyond
Rare earth quaternary alloys—materials containing four principal elements, including at least one rare earth element—are gaining strategic importance in advanced manufacturing sectors. As of 2025, their core applications span aerospace, electronics, and a growing list of emerging technologies, driven by rising demands for high-performance materials that offer tailored magnetic, structural, and thermal properties.
In the aerospace sector, rare earth quaternary alloys are being increasingly utilized for their superior strength-to-weight ratios and exceptional resistance to corrosion and extreme temperatures. These characteristics are critical for jet engine components, turbine blades, and airframe structures, where reliability and performance are non-negotiable. Leading aerospace manufacturers are actively collaborating with materials suppliers to integrate rare earth alloys into next-generation designs. For instance, GE Aerospace and Rolls-Royce have both publicized efforts to incorporate advanced rare earth alloys in their latest propulsion systems, with ongoing research into quaternary compositions that optimize magnetic and mechanical properties for electric aircraft propulsion and hybrid systems.
In electronics, rare earth quaternary alloys are essential for the miniaturization and efficiency of devices. Alloys containing neodymium, dysprosium, iron, and boron form the basis of high-strength permanent magnets employed in motors, actuators, and sensors. The market for these alloys is expanding in response to surging demand for electric vehicles (EVs), smartphones, and wind turbines. Companies such as Hitachi and TDK are leading innovation in rare earth magnet manufacturing, including research into quaternary and more complex alloys to enhance magnetic performance while addressing supply chain concerns around critical rare earth elements.
Beyond aerospace and electronics, rare earth quaternary alloys are finding new roles in renewable energy, robotics, and quantum computing. Wind turbine manufacturers are seeking alloys with improved magnetic retention at high temperatures, while quantum device developers require materials with precisely engineered magnetic anisotropy. Producers such as LKAB and Lynas Rare Earths are scaling up capacity and partnering with technology companies to develop application-specific alloy solutions.
Looking ahead, the outlook for rare earth quaternary alloy manufacturing is robust. Ongoing investments in R&D and strategic partnerships across the value chain—from mining to finished components—are expected to accelerate. As global supply chains for rare earths evolve and sustainability pressures mount, manufacturers are also pursuing recycling initiatives and alternative alloy formulations to reduce reliance on scarce elements, further broadening the scope of applications into the late 2020s.
Regulatory Standards and Industry Compliance
The regulatory landscape for rare earth quaternary alloy manufacturing is evolving rapidly in 2025, shaped by growing geopolitical sensitivities, environmental awareness, and the critical role these materials play in strategic industries. Governments and industry bodies worldwide are intensifying oversight to ensure responsible sourcing, sustainable processing, and product reliability, particularly as rare earth alloys underpin advanced technologies in energy, defense, and electronics.
In 2025, China remains the dominant producer and regulator of rare earth materials, with the China Nonferrous Metals Industry Association (CNIA) implementing stricter controls on export quotas, traceability, and environmental compliance. Recent policies require manufacturers to adopt closed-loop processing and emissions monitoring, impacting the operations of major alloy producers such as Aluminum Corporation of China and Baosteel Group. These measures aim to reduce illegal mining and pollution, while ensuring that downstream alloy manufacturing, including quaternary alloys, adheres to both domestic and international standards.
Globally, the European Union has enacted updated directives through the Eurare Consortium and related bodies to harmonize standards for rare earth alloy content, recycling, and carbon footprint. These guidelines influence not just European manufacturers but also global suppliers wishing to access the EU market, requiring detailed certification of sourcing, processing, and end-use documentation. The United States, through the U.S. Geological Survey and the Department of Energy, has issued new recommendations for critical material supply chains, with a particular focus on rare earth alloy purity and lifecycle management.
Compliance frameworks increasingly emphasize third-party audits and digital traceability, with blockchain and AI-powered monitoring systems gaining traction. Major rare earth alloy manufacturers such as LKAB and Neo Performance Materials are investing in these technologies to maintain regulatory alignment and client trust. Industry groups like the Rare Earth Magnet Industry Association also contribute to standardization efforts, fostering collaboration on best practices for alloy formulation and environmental responsibility.
Looking ahead, regulatory standards are expected to become even more stringent, with a growing emphasis on circular economy principles and cross-border data sharing. Manufacturers that proactively align with evolving compliance regimes will be best positioned to capitalize on global demand, minimize operational risks, and contribute to a more transparent and sustainable rare earth quaternary alloy supply chain.
Investment Hotspots and Funding Trends
The investment landscape for rare earth quaternary alloy manufacturing is evolving rapidly as global demand for advanced materials in high-tech and clean energy sectors accelerates. In 2025, key regions such as East Asia, North America, and Europe are emerging as investment hotspots, driven by government policies, supply chain resilience strategies, and the growing need for high-performance magnets, batteries, and electronic components. Notably, rare earth quaternary alloys—composed of four rare earth elements or combinations with transition metals—are critical for next-generation electric vehicles, wind turbines, and aerospace technologies.
In East Asia, China continues to dominate as both a producer and an investor in rare earth alloy manufacturing. Major enterprises, including Aluminum Corporation of China Limited (CHALCO) and Baotou Steel Rare-Earth Group, are expanding their capabilities through new facilities and technology upgrades, focusing on alloys such as NdFeB-based quaternary magnets. These investments are supported by national initiatives to maintain supply chain control and enhance value-added processing.
Japan and South Korea are also intensifying their involvement. Sumitomo Metal Mining and LG Chem are investing in R&D and production partnerships to secure alloy supplies for domestic electronics and automotive industries. This trend is reinforced by joint ventures with global automakers and electronics manufacturers seeking to localize key materials and reduce exposure to geopolitical risks.
In the United States, the Inflation Reduction Act and Department of Defense funding have catalyzed new investments in rare earth alloy processing. Companies such as MP Materials are expanding their value chain from mining to advanced alloy production. The aim is to establish a resilient domestic supply chain for rare earth alloys, particularly those used in defense and clean energy applications. Funding rounds in 2024 and 2025 have targeted pilot plants and commercial-scale facilities, signaling a move beyond raw material extraction to high-value manufacturing.
Europe is positioning itself as an emerging hub for rare earth alloy innovation, with the European Raw Materials Alliance coordinating public-private funding and fostering collaboration between mining, refining, and alloy manufacturing firms. Companies like Neo Performance Materials are investing in new alloy processing lines and recycling initiatives within the EU, supported by grants and strategic partnerships.
Looking ahead, investment is expected to flow increasingly into sustainable production methods, recycling technologies, and regional supply chain integration. The sector’s outlook for the next few years includes intensified competition for technical expertise, strategic resource agreements, and public funding, with a focus on reducing environmental impact and supporting the green transition across global manufacturing hubs.
Sustainability Initiatives and Environmental Impact
Sustainability considerations in rare earth quaternary alloy manufacturing are gaining unprecedented prominence in 2025, as governments and industry stakeholders respond to both environmental regulations and growing demand for ethically sourced advanced materials. The extraction and processing of rare earth elements (REEs)—critical for manufacturing quaternary alloys used in magnets, batteries, and electronics—have historically posed significant environmental challenges, including hazardous waste generation, radioactive byproducts, and substantial water and energy use.
Leading manufacturers are now investing in cleaner production technologies and circular economy models. For example, China Northern Rare Earth (Group) High-Tech Co., Ltd., one of the world’s largest rare earth producers, has implemented closed-loop water recycling systems and enhanced waste management protocols at its facilities to minimize the ecological footprint of alloy production. Additionally, Lynas Rare Earths has made commitments to reduce process emissions and is actively engaging in efforts to recycle process residues and develop sustainable disposal solutions for radioactive waste, particularly at its Malaysian separation plant.
In parallel, European manufacturers like Eramet are piloting advanced solvent extraction and ion-exchange techniques that reduce chemical reagent consumption and enable recovery of byproducts, thus aligning with the European Union’s Green Deal objectives. These advancements are complemented by industry-wide initiatives to increase the use of secondary raw materials. Several companies, including Umicore, are scaling up rare earth magnet recycling programs, aiming to source a significant portion of feedstock from end-of-life electronics and automotive components over the next few years.
Furthermore, industry consortia and organizations such as the Rare Earth Industry Association are promoting the development of voluntary sustainability standards and traceability systems to address both environmental and social impacts along the supply chain. These frameworks seek to ensure responsible sourcing, transparent reporting, and continual improvement in environmental performance.
Looking ahead, the outlook for sustainable rare earth quaternary alloy manufacturing is shaped by tightening global regulations, increased scrutiny from downstream sectors (especially electric vehicles and renewable energy producers), and greater public awareness. The sector is expected to witness accelerated investment in eco-innovative extraction, closed-loop recycling, and carbon footprint reduction technologies through 2026 and beyond, as manufacturers seek to balance operational efficiency with environmental stewardship.
Future Outlook: Emerging Opportunities & Challenges
The future of rare earth quaternary alloy manufacturing is poised at a critical juncture in 2025, with both emerging opportunities and significant challenges shaping the landscape. As demand intensifies for advanced materials in green technologies, energy storage, high-performance magnets, and electronics, the drive to develop and optimize quaternary alloys—those combining four rare earth or related elements—has accelerated. These alloys offer enhanced properties such as higher magnetic strength, thermal stability, and corrosion resistance compared to their binary or ternary counterparts, making them increasingly vital for next-generation applications.
One of the most promising opportunities lies in the electric vehicle (EV) and renewable energy sectors. The push for higher efficiency motors and generators is fueling research into neodymium-iron-boron (NdFeB) magnets, with the addition of elements such as dysprosium, terbium, and praseodymium to form quaternary systems. Leading producers like Lynas Rare Earths and Aluminum Corporation of China (Chinalco) are investing in advanced separation and alloying processes to meet stricter performance requirements. Latest announcements suggest that both companies are scaling pilot projects and considering joint ventures to localize more value-added alloy manufacturing, especially in response to tightening global supply chains.
However, several challenges complicate this outlook. The technical complexity of quaternary alloy production—requiring precise control over element ratios and purity—demands sophisticated equipment and skilled personnel. The supply of critical rare earths remains constrained, with geopolitical tensions and resource nationalism affecting material flows. For example, China Rare Earth Group, which controls a significant portion of global rare earth output, has signaled possible export restrictions and is prioritizing domestic downstream industries. This has spurred parallel efforts in the US, EU, Japan, and Australia to build independent supply chains and recycling capabilities.
On the technological front, consortiums and manufacturers are experimenting with alternative alloy chemistries and additive manufacturing techniques to reduce reliance on the most supply-risk elements. Companies such as Hitachi Metals are developing proprietary processes to tailor alloy microstructures for specialized applications, while automakers and electronics firms are forming direct partnerships with alloy producers to stabilize long-term supply.
Looking ahead, the market for rare earth quaternary alloys is expected to experience steady growth, provided that supply chain resilience, environmental sustainability, and manufacturing scalability can be maintained. The years immediately following 2025 will likely see increased investment in R&D, expansion of recycling infrastructure, and deeper collaboration between upstream miners and downstream alloy fabricators to capture emerging market opportunities and mitigate ongoing risks.
Sources & References
- Chinalco
- MP Materials
- LANXESS
- LKAB
- Nornickel
- Sumitomo Metal Mining
- Australian Mines
- UrbanMines
- China Molybdenum Co., Ltd.
- POSCO
- Lynas Rare Earths
- GE Aerospace
- Hitachi
- Lynas Rare Earths
- Eurare Consortium
- Neo Performance Materials
- China Northern Rare Earth (Group) High-Tech Co., Ltd.
- Eramet
- Umicore
- Lynas Rare Earths
- China Rare Earth Group