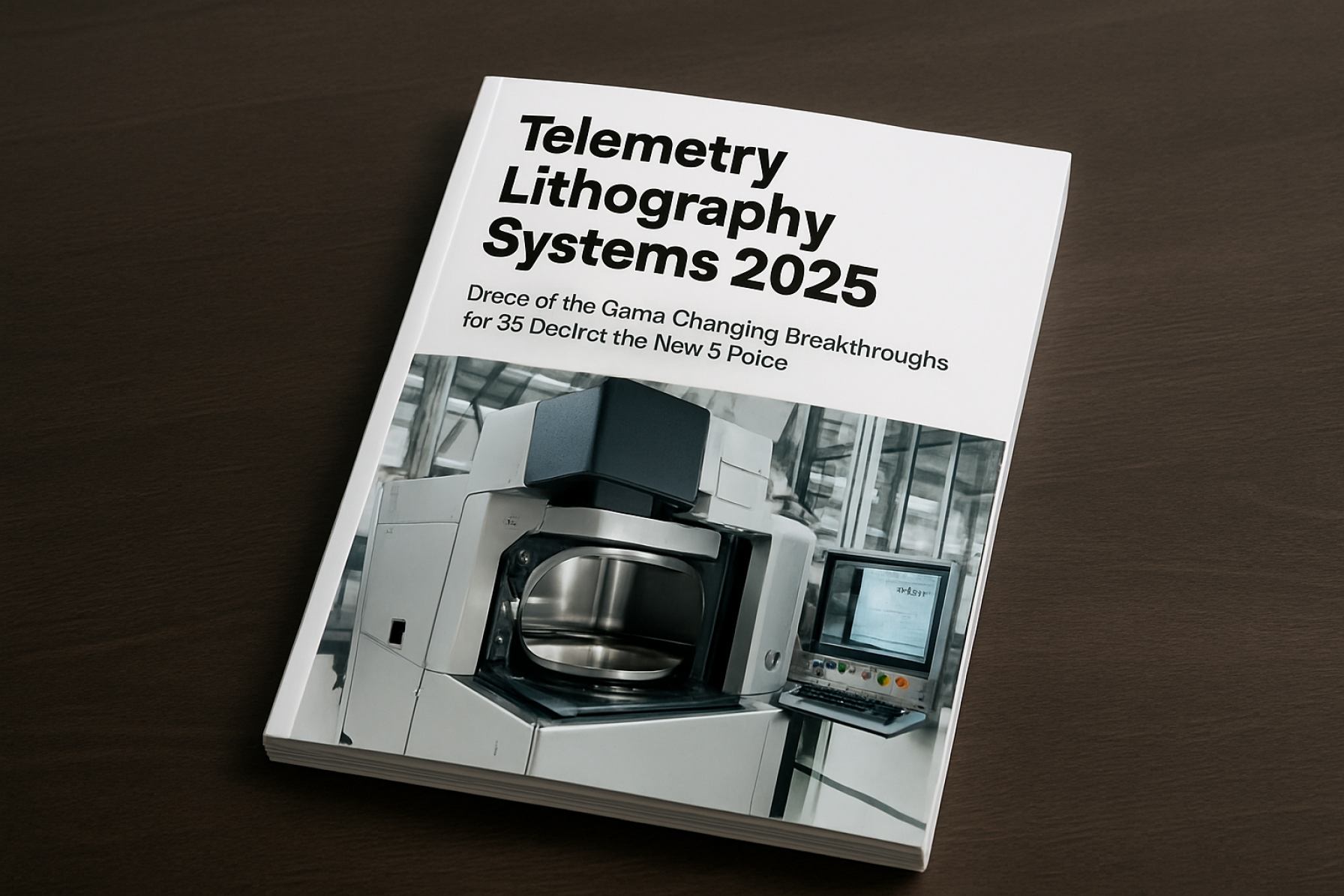
Table of Contents
- Executive Summary: 2025 Outlook & Key Takeaways
- Market Size & Growth Projections Through 2030
- Emerging Technologies Shaping Telemetry Lithography
- Competitive Landscape: Leading Companies and New Entrants
- Application Trends Across Semiconductor and Advanced Manufacturing
- Key Challenges: Technical Barriers and Supply Chain Risks
- Recent Regulatory Developments and Industry Standards
- Strategic Partnerships, M&A, and Investment Highlights
- Regional Analysis: Growth Hotspots and Global Expansion
- Future Outlook: Disruptive Opportunities and Long-Term Scenarios
- Sources & References
https://youtube.com/watch?v=wm06bbGFJUU
Executive Summary: 2025 Outlook & Key Takeaways
Telemetry lithography systems are poised to play a transformative role in semiconductor manufacturing as the industry advances into 2025 and beyond. These systems leverage real-time data acquisition and feedback mechanisms to enhance the precision, efficiency, and yield of lithographic processes, which are foundational for fabricating increasingly complex and miniaturized integrated circuits.
In 2025, the deployment of telemetry capabilities within lithography systems is being actively pursued by leading equipment manufacturers. Companies such as ASML Holding NV are integrating advanced sensor networks and data analytics into their next-generation extreme ultraviolet (EUV) and deep ultraviolet (DUV) scanners. These enhancements allow for continuous monitoring of critical parameters—such as stage alignment, temperature, vibration, and exposure dose—enabling immediate in situ adjustments. This level of process transparency is essential for meeting the sub-2 nm process requirements now being targeted by foundries and integrated device manufacturers (Taiwan Semiconductor Manufacturing Company).
The push towards “smart” fab environments is accelerating, with telemetry-enabled lithography systems forming a core element of advanced process control (APC) strategies. By embedding connectivity and leveraging AI-driven analytics, manufacturers aim to reduce downtime, predict maintenance needs, and optimize tool performance. For example, Canon Inc. and Nikon Corporation have highlighted their commitment to integrating sophisticated metrology and telemetry modules into their lithography platforms, supporting data-rich feedback loops for process optimization and defect reduction.
- Telemetry is expected to enable tighter process windows and higher yields, especially as critical dimensions shrink and overlay tolerances become more demanding.
- Major suppliers are collaborating with device makers to tailor telemetry solutions to specific fab requirements, supporting rapid troubleshooting and adaptive control.
- Data security and interoperability are emerging considerations, as telemetry systems generate vast volumes of sensitive process data that must be managed in accordance with industry standards and best practices (SEMI).
Looking ahead, the integration of telemetry within lithography systems is set to be a key enabler for the semiconductor industry’s roadmap, supporting the transition to smaller nodes, higher productivity, and “lights-out” smart manufacturing. The next few years will likely see further convergence of AI, telemetry, and advanced lithographic hardware, driving innovation in both tool capabilities and overall fab efficiency.
Market Size & Growth Projections Through 2030
The global market for telemetry lithography systems is positioned for steady growth through 2030, driven by escalating demand for advanced semiconductor manufacturing, increasing wafer complexity, and the ongoing expansion of 5G, AI, and IoT applications. As of 2025, leading equipment manufacturers are reporting record orders for lithography systems featuring integrated telemetry—real-time data acquisition and feedback mechanisms that optimize precision and yield. Notably, ASML Holding, the world’s foremost supplier of photolithography equipment, continues to see strong demand for its EUV (Extreme Ultraviolet) and DUV (Deep Ultraviolet) systems, which are increasingly incorporating advanced telemetry modules for process monitoring and predictive maintenance.
The drive toward sub-5nm and eventually 2nm process nodes is accelerating investment in telemetry-enabled lithography platforms, as chipmakers require ever-finer control over overlay, focus, and exposure parameters. Major foundries such as Taiwan Semiconductor Manufacturing Company (TSMC) and Samsung Electronics have publicly committed to ramping next-generation production lines, further fueling system orders and upgrades. In 2024–2025, ASML reported a surge in bookings for its latest EUV systems, which boast sophisticated telemetry sensors and analytics to enable real-time fault detection and process optimization, directly responding to these customer needs.
- 2025 Market Size: Based on disclosed shipment volumes and average system pricing from leading OEMs, the telemetry lithography systems market is estimated to be in the multi-billion USD range globally, with a high single-digit CAGR projected through 2030 (ASML Holding).
- Growth Drivers: Key growth factors include increasing adoption of telemetry for advanced process control, expansion of high-volume manufacturing of cutting-edge semiconductors, and rising investment in smart manufacturing by leading chipmakers (TSMC).
- Regional Trends: Asia-Pacific continues to dominate installations, led by Taiwan, South Korea, and China, as these regions account for a majority of new fab construction and lithography system deployments (SEMI).
- Outlook: Through 2030, adoption of increasingly intelligent telemetry solutions is expected to differentiate system offerings, with OEMs investing in AI-driven analytics, remote diagnostics, and closed-loop feedback to support sub-nanometer production targets (ASML Holding).
In summary, the telemetry lithography systems market is on a robust growth trajectory, underpinned by technological innovation, expanding end-use demand, and the semiconductor industry’s relentless pursuit of higher yields and process reliability.
Emerging Technologies Shaping Telemetry Lithography
Telemetry lithography systems are undergoing significant transformation in 2025, driven by the convergence of advanced sensor technologies, real-time data analytics, and the increasing demand for process precision in semiconductor manufacturing. These systems, which combine the principles of telemetry—remotely collecting and transmitting operational data—with lithographic processes, are essential for the next generation of integrated circuits and advanced packaging.
One of the most notable advancements is the integration of sophisticated telemetry modules directly into state-of-the-art extreme ultraviolet (EUV) lithography machines. Major industry players such as ASML have incorporated advanced sensor arrays and AI-driven data analysis within their EUV systems to monitor lens alignment, wafer stage movement, and environmental conditions in real time. These telemetry-enhanced systems are capable of detecting sub-nanometer deviations and immediately adjusting system parameters, thereby minimizing defect rates and maximizing yield.
Similarly, Canon Inc. is modernizing its lithography platforms with embedded telemetry for predictive maintenance and process optimization. Their systems use a network of IoT-enabled sensors to anticipate component wear and optimize exposure parameters, reducing downtime and improving throughput. This capability is critical as the industry moves toward <10 nm process nodes, where even minor deviations can lead to significant yield loss.
In addition, Nikon Corporation has expanded its focus on closed-loop telemetry feedback in its semiconductor lithography systems. By continuously measuring critical process variables such as focus, dose, and overlay, Nikon’s systems can self-correct during operation, leading to tighter process control and higher device uniformity across wafers.
Looking ahead, the outlook for telemetry lithography systems is marked by the growing incorporation of edge computing and machine learning. These technologies are expected to enable distributed data processing directly at the tool level, supporting real-time decision-making and further reducing response times. Strategic collaborations between equipment manufacturers and semiconductor foundries are also likely to increase, as fabs seek to customize telemetry protocols to their specific process needs.
Overall, the ongoing evolution of telemetry lithography systems in 2025 and beyond is poised to deliver unprecedented process transparency, higher yields, and faster time-to-market for advanced semiconductor devices. As telemetry becomes an integral component of lithography, continuous innovation will be essential to meet the escalating demands of next-generation chip fabrication.
Competitive Landscape: Leading Companies and New Entrants
The competitive landscape for telemetry lithography systems in 2025 is characterized by a dynamic interplay between established leaders and emerging entrants, with innovation and strategic partnerships defining the market’s direction. Telemetry lithography, which integrates real-time data collection and remote monitoring capabilities with advanced lithographic equipment, is gaining traction as semiconductor manufacturing nodes continue to shrink and process control demands intensify.
At the forefront, ASML Holding remains the dominant force. Known for its extreme ultraviolet (EUV) lithography systems, ASML has advanced telemetry functionality in its Twinscan and EXE platforms, enabling predictive maintenance and yield optimization through real-time sensor data integration. The company’s push toward high-NA EUV systems, slated for introduction in 2025, is expected to further embed telemetry for tighter process control and remote diagnostics, supporting the needs of leading-edge foundries and integrated device manufacturers (IDMs).
Rivals such as Nikon Corporation and Canon Inc. also maintain a significant presence, especially in deep ultraviolet (DUV) lithography. Both companies have upgraded their system architectures to accommodate telemetry modules, providing enhanced data analytics and remote service capabilities for customers in logic and memory sectors. Nikon’s latest NSR series and Canon’s FPA platform now offer remote equipment monitoring and process optimization features, reflecting the increasing importance of data-driven lithography workflows.
Emerging entrants are targeting specialized telemetry solutions, often focusing on software, middleware, and edge computing integration. Applied Materials and KLA Corporation, while not lithography tool OEMs, have expanded their telemetry-enabled process control and inspection systems, which interface seamlessly with leading lithography platforms to deliver comprehensive fab-wide monitoring and analytics.
- Cymer, an ASML subsidiary, is advancing light source telemetry, providing granular monitoring of laser performance to optimize uptime and exposure precision.
- Veeco Instruments and Ultratech (a division of Veeco) are integrating telemetry into advanced packaging and maskless lithography systems, targeting heterogeneous integration and rapid prototyping markets.
Looking ahead, the continued miniaturization of semiconductor devices and the rise of smart manufacturing will likely accelerate the adoption of telemetry lithography systems. Partnerships between equipment manufacturers and specialist telemetry providers are anticipated to deepen, with the goal of enabling fully autonomous, self-correcting lithography lines by the late 2020s. As new entrants bring AI-powered telemetry solutions and edge analytics to the sector, the competitive landscape is expected to remain vibrant and innovation-driven.
Application Trends Across Semiconductor and Advanced Manufacturing
Telemetry lithography systems have emerged as critical enablers of advanced process control and yield improvement across semiconductor and advanced manufacturing sectors. As chip architectures shrink and complexity rises, the demand for precise, real-time monitoring during lithography steps has accelerated the integration of telemetry solutions into both legacy and next-generation fabrication lines.
In 2025, leading lithography equipment manufacturers are embedding extensive telemetry capabilities within their latest extreme ultraviolet (EUV) and deep ultraviolet (DUV) platforms. These systems incorporate advanced sensor arrays capable of capturing high-frequency data on parameters such as stage position, lens temperature, vibration, exposure dose, and resist performance. For example, ASML—the world’s largest supplier of photolithography systems—has publicly detailed the expansion of in-situ metrology and telemetry modules in its EUV platforms, facilitating sub-nanometer overlay accuracy and supporting the transition to 2 nm and smaller nodes.
The telemetry data generated by these systems is increasingly being streamed in real-time to advanced process control (APC) software and digital twins for predictive maintenance and yield optimization. Canon Inc. and Panasonic Industry have both announced initiatives in 2024–2025 to enhance their lithography offerings with expanded telemetry interfaces, enabling tighter process windows and more robust defect detection.
A notable trend for 2025 and beyond is the integration of telemetry systems with AI-driven analytics platforms. This convergence allows fabs to rapidly identify drift, abnormal tool signatures, and environmental disturbances, minimizing downtime and maximizing throughput. Tokyo Electron Limited (TEL) has begun offering telemetry-enabled lithography tools that feed directly into factory-wide data lakes, supporting holistic optimization across multiple process steps.
Looking ahead, the outlook for telemetry lithography systems includes further standardization of data protocols, enhanced cybersecurity for sensitive process telemetry, and broader adoption in compound semiconductor and advanced packaging applications. Industry consortia such as SEMI are actively developing guidelines to facilitate secure, interoperable telemetry across multi-vendor environments, ensuring that the value of real-time lithography data can be fully realized as fabs scale to even more advanced nodes and heterogeneous integration strategies.
Key Challenges: Technical Barriers and Supply Chain Risks
Telemetry lithography systems, crucial for next-generation semiconductor manufacturing, face significant technical and supply chain challenges as the industry advances into 2025. These systems, which integrate real-time sensors and data transmission mechanisms within lithography tools, are essential for monitoring, controlling, and optimizing critical patterning processes used in advanced node fabrication.
A primary technical barrier is the integration of high-speed, high-fidelity telemetry sensors that can operate reliably under the extreme conditions of lithography environments—such as high vacuum, ultraviolet radiation, and rapid stage movement. Leading equipment manufacturers like ASML and Canon Inc. are investing in proprietary sensing technologies, but maintaining sensor accuracy and minimizing signal interference at nanometer-scale resolutions remains a persistent challenge. In 2025, further development in sensor miniaturization and robust data transmission protocols is required to align telemetry capabilities with the precision demands of sub-3nm process nodes.
Additionally, the complexity of telemetry data analytics is escalating. As system sensors multiply and data volumes surge, the need for advanced real-time analytics and machine learning integration is becoming critical. Vendors must ensure that telemetry subsystems do not introduce latency or bottleneck overall lithography throughput. Companies like Nikon Corporation and KLA Corporation are exploring edge computing and AI-driven analytics to process telemetry data locally within the equipment, but seamless implementation at scale is still a work in progress.
The supply chain for telemetry lithography components presents another major risk. Key sensors, optoelectronic parts, and high-speed data transmission modules often rely on a limited pool of specialized suppliers. Global disruptions—such as geopolitical tensions or material shortages—can severely impact the availability and cost of critical subsystems. Companies like AMETEK, Inc. and Honeywell International Inc., which supply precision sensors and industrial electronics, are investing in supply chain diversification and regional manufacturing, yet vulnerabilities remain, especially as demand for advanced semiconductors continues to soar.
Looking ahead, industry collaboration to standardize telemetry interfaces and protocols may help mitigate some technical and supply chain risks. However, for 2025 and the near future, the sector must navigate persistent challenges around sensor technology, analytics integration, and supply chain resilience to ensure the continued evolution and reliability of telemetry lithography systems.
Recent Regulatory Developments and Industry Standards
The regulatory landscape for telemetry lithography systems has become increasingly crucial as these advanced systems gain prominence in semiconductor manufacturing and other high-precision industries. In 2025, regulatory bodies and standards organizations are responding to the sector’s rapid technological evolution, focusing on interoperability, data integrity, and cybersecurity.
A key event in recent years was the update of the SEMI E10 and E40 standards by SEMI, which govern equipment reliability and communications interface protocols. These revisions, effective from late 2024, introduce more stringent requirements for real-time telemetry data collection and standardize interface protocols for lithography equipment—enhancing both traceability and integration across multi-vendor production lines.
On the cybersecurity front, the National Institute of Standards and Technology (NIST) in the United States released special guidance in early 2025 for industrial control systems, including advanced lithography tools. This guidance emphasizes secure telemetry data transmission and storage, in recognition of the sensitive nature of process and equipment data in advanced semiconductor fabrication.
The European Union has also taken steps, with the EU Cybersecurity Act now explicitly referencing industrial telemetry standards for critical infrastructure, which includes next-generation lithography systems. This regulatory inclusion compels manufacturers and suppliers to ensure compliance with both equipment safety and secure data handling protocols.
Industry players such as ASML and Canon Inc. are actively participating in industry consortia and working groups to help shape evolving standards. Both companies have publicly committed to aligning their telemetry-enabled lithography systems with SEMI and NIST guidelines, as well as regional data security mandates. For instance, ASML’s latest EUV systems feature enhanced telemetry modules designed for compliance with both SEMI E10/E40 revisions and NIST recommendations.
Looking ahead, regulatory bodies are expected to further refine standards as telemetry becomes integral to predictive maintenance, process optimization, and secure equipment networking. Ongoing collaboration between manufacturers, standards bodies, and governmental agencies will be essential to ensure that telemetry lithography systems remain both interoperable and secure in the fast-evolving semiconductor ecosystem.
Strategic Partnerships, M&A, and Investment Highlights
The telemetry lithography systems sector is witnessing heightened strategic activity in 2025, as industry leaders and emerging players pursue partnerships, mergers, and investments to accelerate technological advancements and expand market reach. Telemetry-enhanced lithography, which integrates real-time data collection and analysis into semiconductor manufacturing processes, is seen as a critical enabler for next-generation chip fabrication—driving intense interest across the global semiconductor value chain.
One of the most significant recent developments is the ongoing collaboration between ASML Holding and major semiconductor foundries. ASML, the world’s leading supplier of photolithography equipment, has been deepening its partnerships with leading-edge chip manufacturers to co-develop telemetry-driven enhancements for its extreme ultraviolet (EUV) and deep ultraviolet (DUV) platforms. In 2024, ASML announced a multi-year joint development program with Taiwan Semiconductor Manufacturing Company (TSMC), focused on integrating advanced process telemetry to optimize patterning control and yield for sub-2nm nodes. This collaboration is expected to deliver new telemetry modules starting in late 2025, improving real-time process monitoring and defect detection.
Strategic investments are also shaping the telemetry lithography landscape. Intel Corporation has committed over $1 billion in 2024–2025 towards telemetry-enabled lithography infrastructure at its new fabs in Ohio and Germany, aiming to streamline process diagnostics and predictive maintenance. These investments are paired with Intel’s internal initiatives to develop proprietary telemetry analytics, as well as partnerships with leading equipment vendors, including Lam Research and Applied Materials, to integrate advanced sensor arrays and data platforms into their lithography and etch tools.
Mergers and acquisitions are further consolidating expertise in the sector. In early 2025, KLA Corporation, a leader in process control and metrology, completed its acquisition of a telemetry software specialist to bolster its in-situ monitoring capabilities for lithography systems. This move aligns with KLA’s broader strategy to offer end-to-end data solutions for semiconductor manufacturing, leveraging real-time telemetry to enable smarter defect control and process optimization.
Looking ahead, the telemetry lithography ecosystem is poised for continued strategic convergence. Industry analysts anticipate more cross-company joint ventures and targeted investments, especially as the demand for advanced monitoring and AI-driven analytics intensifies with the transition to angstrom-level nodes and heterogeneous integration. Such collaborations are likely to remain instrumental in driving both innovation and competitiveness in the global semiconductor equipment market.
Regional Analysis: Growth Hotspots and Global Expansion
The global landscape for telemetry lithography systems is rapidly evolving, with growth hotspots emerging in regions actively investing in advanced semiconductor manufacturing and precision process control. In 2025, Asia-Pacific continues to dominate as the principal growth engine, driven by aggressive semiconductor expansion plans in Taiwan, South Korea, Japan, and increasingly, mainland China. Leading foundries such as Taiwan Semiconductor Manufacturing Company (TSMC) and Samsung Electronics are ramping up their adoption of telemetry-driven lithography equipment to enable real-time monitoring, yield optimization, and defect reduction at cutting-edge nodes.
Recent investments in new fab construction and upgrade cycles throughout East Asia have seen a surge in demand for telemetry-enabled lithography platforms provided by industry leaders such as ASML and Canon. For instance, ASML reported continued order growth in the region, attributing much of this to the integration of advanced telemetry and AI-driven analytics within their extreme ultraviolet (EUV) and deep ultraviolet (DUV) lithography systems. These systems are critical for fabrication facilities seeking to maintain competitiveness at sub-5nm process nodes.
North America, particularly the United States, is also experiencing robust growth in telemetry lithography system deployment. This expansion is fueled by federal incentives, such as the CHIPS Act, and strategic investments by companies like Intel and TSMC’s Arizona facility. U.S. fabs are prioritizing telemetry-based solutions to enhance process traceability, support advanced process control (APC), and meet stringent quality standards for automotive, aerospace, and AI-driven applications.
Europe, while traditionally focused on equipment supply through companies like ASML, is seeing renewed interest in local production enabled by telemetry lithography, supported by EU initiatives aimed at securing semiconductor supply chains and fostering innovation within member states.
- Asia-Pacific: Remains the largest and fastest-growing market, with telemetry lithography system adoption tightly linked to new fab construction and process node advancement.
- North America: Significant uptick in 2025 and beyond, backed by government funding and local manufacturing initiatives.
- Europe: Strategic investments in both R&D and manufacturing, with a focus on supply chain resilience and technological sovereignty.
Looking ahead, regional demand for telemetry lithography systems is expected to intensify through 2027 as chipmakers pursue higher yields, process miniaturization, and digital twin initiatives. Collaboration between equipment makers, foundries, and governments will likely accelerate the global proliferation of telemetry-enabled lithography technologies.
Future Outlook: Disruptive Opportunities and Long-Term Scenarios
Telemetry lithography systems—a convergence of advanced patterning, real-time monitoring, and closed-loop control—are poised to significantly influence microelectronics manufacturing from 2025 onward. As device scaling approaches the atomic level, the need for robust, in-situ telemetry is increasingly critical for yield, reliability, and cost control. In 2025, leading equipment manufacturers are actively integrating advanced telemetry into their latest extreme ultraviolet (EUV) and deep ultraviolet (DUV) lithography platforms. For example, ASML embeds sensors and analytics to continuously monitor focus, overlay, and critical dimension variations at nanoscale resolution, enabling dynamic process adjustments during wafer exposure.
Looking to the next several years, telemetry-enabled systems are expected to transition from passive monitoring to predictive and prescriptive control. Nikon Corporation and Canon Inc. are also advancing telemetric capabilities within their immersion and multi-patterning tools, focusing on AI-driven data analytics to anticipate process drifts and anomalies before defects occur. These enhancements are tightly coupled with the semiconductor industry’s push for higher throughput and smaller process nodes, especially as the industry moves toward 2 nm and sub-2 nm manufacturing.
A disruptive opportunity lies in the integration of telemetry data with fab-wide manufacturing execution systems (MES), enabling real-time feedback from lithography tools to upstream and downstream process modules. Applied Materials and KLA Corporation are actively developing telemetry-supported process control solutions that merge lithography data with metrology and inspection, accelerating defect root-cause analysis and adaptive process tuning.
- The next disruptive leap may come from cloud-connected lithography, where telemetry data is aggregated and analyzed across global fabs, enabling benchmarking and rapid deployment of best-known methods. This scenario aligns with the digital transformation strategies outlined by manufacturers such as ASML.
- In the long term, as wafer sizes potentially increase and heterogeneous integration becomes standard, telemetry lithography systems will play a pivotal role in process harmonization across diverse materials and device architectures.
- The industry outlook through the late 2020s anticipates telemetry to become a standard feature for all leading-edge lithography systems, with potential spillover into advanced packaging and emerging quantum device fabrication.
In summary, telemetry lithography systems in 2025 and beyond are set to underpin the next era of semiconductor manufacturing, unlocking unprecedented levels of process control, yield optimization, and cross-fab intelligence.