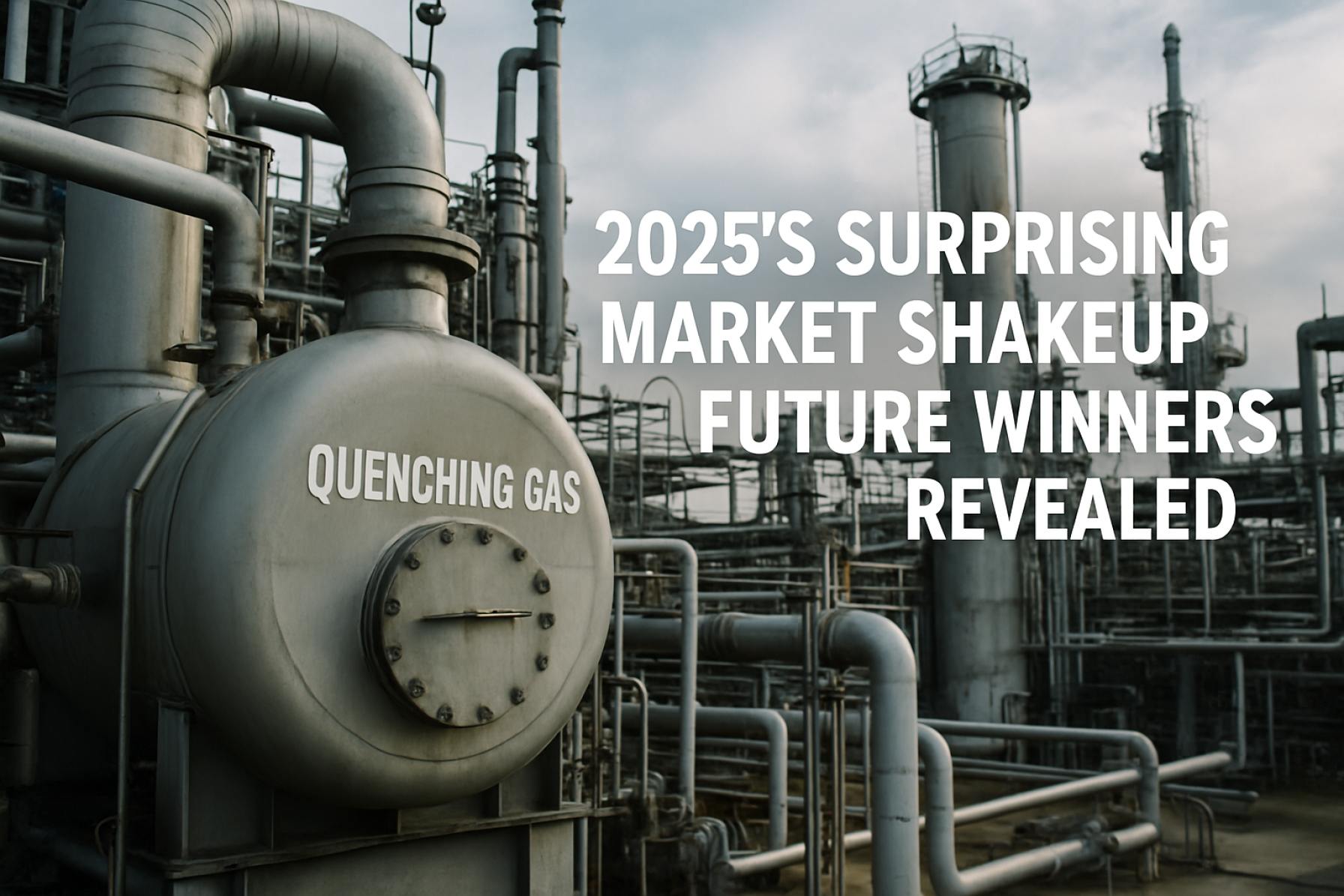
Table of Contents
- Executive Summary: Key Findings & Industry Snapshot (2025–2030)
- Global Market Forecast: Growth Trends and Revenue Projections
- Emerging Technologies: Next-Gen Quenching Gas Equipment Innovations
- Sustainability & Regulatory Drivers: Impact on Manufacturing Standards
- Competitive Landscape: Leading Manufacturers and New Entrants
- Demand Drivers: Automotive, Aerospace, and Heavy Industry Analysis
- Supply Chain Dynamics: Challenges, Opportunities, and Regional Hubs
- Case Studies: Breakthrough Solutions from Industry Leaders
- Investment & M&A Activity: Funding Trends and Strategic Partnerships
- Future Outlook: Disruptive Trends, Risks, and Strategic Recommendations
- Sources & References
Executive Summary: Key Findings & Industry Snapshot (2025–2030)
The global quenching gas equipment manufacturing sector is entering a pivotal phase from 2025 onward, marked by intensified innovation, regulatory shifts, and strategic investments. Quenching gas systems, essential for controlled cooling in heat treatment processes, are experiencing heightened demand due to expanding automotive, aerospace, and advanced manufacturing industries. The push for higher-performance materials and energy efficiency is accelerating the adoption of next-generation quenching gas solutions, with manufacturers focusing on enhanced precision, automation, and sustainability.
- Market Expansion: Leading companies such as Air Liquide and Linde report increased orders for specialized quenching gas supply systems, particularly in North America, Europe, and Asia-Pacific. Investments in new manufacturing facilities and partnerships with furnace manufacturers are expected to support double-digit growth rates through 2030.
- Technological Advancements: Automation, digital monitoring, and integration with Industry 4.0 frameworks are becoming standard among major producers. For instance, Praxair (now part of Linde) has introduced digitally monitored gas flow systems to optimize quenching uniformity and reduce cycle times, supporting higher throughput and quality.
- Regulatory Drivers: Tighter environmental standards are influencing equipment design, with a focus on reducing nitrogen and hydrogen consumption and minimizing emissions. Major suppliers like Air Products are developing low-leakage, high-efficiency quenching gas delivery systems to meet evolving regulations in the EU, US, and Asia.
- Sustainability Trends: The sector is witnessing increased R&D in alternative and blended gases, aiming to reduce carbon footprints and improve process efficiency. Air Liquide has publicly committed to developing greener gas technologies and lifecycle management solutions for industrial clients.
- Outlook (2025–2030): The quenching gas equipment manufacturing industry is projected to maintain robust growth as end-user sectors pursue advanced heat treatment capabilities. Strategic collaborations between gas suppliers and furnace manufacturers, such as those led by Linde, are expected to drive innovation, standardization, and market expansion.
In summary, from 2025 to 2030, the quenching gas equipment manufacturing landscape will be defined by smart technology integration, environmental compliance, and the pursuit of operational excellence. Leading global suppliers are poised to shape the market through sustained investment in advanced solutions and strategic partnerships.
Global Market Forecast: Growth Trends and Revenue Projections
The global quenching gas equipment manufacturing sector is poised for solid growth in 2025, driven by sustained demand from heat treatment, metallurgy, and advanced manufacturing industries. Equipment used to deliver, control, and recycle quenching gases—such as nitrogen, hydrogen, and specially engineered mixtures—remains critical for ensuring uniform mechanical properties and process efficiency in metalworking and alloy production. As industries seek higher precision and energy efficiency, investment in next-generation quenching gas systems is accelerating.
Major manufacturers are expanding their portfolios to include advanced gas delivery and monitoring systems. For example, Linde and Air Liquide have recently introduced modular gas supply systems and digital controls aimed at enhancing safety, reducing downtime, and optimizing gas usage in quenching applications. These systems are tailored for integration with Industry 4.0 frameworks, enabling real-time data analysis and remote maintenance, which are increasingly sought after by automotive, aerospace, and toolmaking customers.
Geographically, Asia-Pacific continues to be the fastest-growing market, propelled by large-scale investments in automotive and heavy machinery manufacturing in China, India, and Southeast Asia. Nippon Steel Corporation and Tokyo Gas Engineering Solutions have expanded their manufacturing capabilities and supply chain partnerships to meet the growing regional demand for heat treatment solutions. In North America and Europe, replacement and upgrade cycles for legacy quenching systems are fueling demand, particularly as companies seek to comply with stricter emissions and energy standards.
The outlook for 2025 and the subsequent years also reflects a shift toward environmental compliance and resource efficiency. Manufacturers are increasingly partnering with industrial gas suppliers to offer turnkey solutions that incorporate gas recovery and recycling technology. For instance, Praxair (part of Linde) has been actively deploying integrated quenching gas management systems designed to reduce gas consumption and minimize environmental impact.
Overall, the global quenching gas equipment manufacturing market is expected to see steady revenue growth through 2025 and beyond, underpinned by ongoing industrial modernization, regulatory requirements, and the adoption of digital and sustainable manufacturing practices. The sector’s trajectory will be shaped by continued innovation in gas delivery systems, automation, and eco-friendly solutions, positioning leading manufacturers to capture emerging opportunities across established and developing markets.
Emerging Technologies: Next-Gen Quenching Gas Equipment Innovations
The quenching gas equipment manufacturing sector is rapidly evolving in 2025, driven by the automotive, aerospace, and advanced manufacturing industries’ demand for more efficient, sustainable, and precise heat treatment solutions. Innovations in this field focus on improving energy efficiency, reducing environmental impact, and enhancing process control through digitalization and advanced materials.
A significant trend is the integration of Industry 4.0 principles into quenching gas systems. Leading manufacturers such as Linde and Air Liquide are deploying smart sensors, real-time monitoring, and AI-driven controls to optimize gas flows, pressure, and cooling rates. These advancements enable predictive maintenance and enhanced quality assurance, reducing downtime and improving consistency in metallurgical properties. For instance, Linde has introduced tailored digital solutions for its quenching gas delivery systems, allowing customers to monitor and adjust processes remotely.
Environmental sustainability remains a top priority. Equipment manufacturers are developing systems compatible with a broader range of environmentally friendly gases, including nitrogen and hydrogen blends, to replace traditional oil-based or high-carbon gas quenching. Air Products has been at the forefront, offering new gas mixing and delivery equipment that supports the transition to low-emission quenching environments. The adoption of hydrogen as a quenching medium is being actively explored, thanks to its clean-burning qualities and potential to drastically reduce CO2 emissions during heat treatment processes.
Materials innovation also plays a key role. New refractory alloys and ceramic-based components are being incorporated into quenching gas furnaces to withstand higher temperatures and corrosive atmospheres, extending equipment life and improving efficiency. Tenova, for example, is developing advanced furnace designs equipped with enhanced insulation and improved gas circulation systems, aimed at achieving faster and more uniform cooling rates.
Looking ahead into the next few years, the quenching gas equipment sector is expected to see further adoption of modular, scalable systems that allow for flexible production capacities and integration with renewable energy sources. Ongoing R&D by industry leaders is focused on expanding the use of digital twins, advanced analytics, and automated process controls, paving the way for fully autonomous quenching operations. As manufacturers respond to stricter regulatory requirements and sustainability goals, the pace of innovation in this sector is anticipated to accelerate through 2026 and beyond.
Sustainability & Regulatory Drivers: Impact on Manufacturing Standards
The quenching gas equipment manufacturing sector is experiencing significant evolution in 2025 as sustainability imperatives and regulatory frameworks increasingly shape production standards. Key environmental concerns—particularly those related to greenhouse gas emissions and energy efficiency—are driving manufacturers to innovate both equipment design and operational processes. Regulatory agencies across major markets have intensified scrutiny on industrial gas emissions, placing pressure on manufacturers to comply with stricter standards for quenching processes that utilize gases such as nitrogen, hydrogen, and argon.
In the European Union, the implementation of the Industrial Emissions Directive (IED) and the ongoing transition to the European Green Deal’s climate neutrality objectives have prompted equipment manufacturers to adopt advanced emission-reducing technologies. Companies like Linde are increasingly developing gas delivery and control systems that minimize leaks and optimize gas usage, aligning with the EU’s push for circularity and reduced carbon footprints. Similarly, in North America, the U.S. Environmental Protection Agency (EPA) has updated standards for emissions from industrial furnaces and heat treatment processes, compelling equipment makers to integrate energy recovery and monitoring features into their offerings, as exemplified by Air Products and Praxair.
Sustainability certification frameworks, such as ISO 14001 for environmental management and ISO 50001 for energy management, are becoming standard requirements in supplier qualification processes. Manufacturers like AFC-Holcroft have responded by redesigning quenching gas systems with improved insulation, waste heat recovery modules, and digital controls for real-time efficiency monitoring. This shift not only ensures regulatory compliance but also meets the growing demand from end-users in automotive and aerospace sectors for verifiably sustainable supply chains.
Looking ahead, the convergence of digitalization and regulatory compliance is expected to further transform the sector. The adoption of remote monitoring and predictive maintenance technologies, as seen in new equipment lines from Tenova, will allow manufacturers and operators to proactively address inefficiencies and reduce environmental impact. Additionally, alternative quenching gases and hybrid systems are under development to meet or exceed forthcoming emissions and safety standards. These trends suggest that, through 2025 and beyond, sustainability and regulatory drivers will remain central to innovation and competitiveness in quenching gas equipment manufacturing.
Competitive Landscape: Leading Manufacturers and New Entrants
The competitive landscape of quenching gas equipment manufacturing in 2025 is characterized by a mix of established global manufacturers and innovative new entrants, responding to growing demand from automotive, aerospace, and metallurgical sectors. Major industry incumbents such as Air Liquide, Linde, and Air Products and Chemicals, Inc. continue to hold significant market share, leveraging extensive R&D capabilities and global distribution networks to provide advanced gas supply systems, quench gas generators, and integrated safety solutions. These companies are increasingly focused on digitalization—incorporating industrial IoT, predictive maintenance, and automation to deliver greater efficiency and traceability in heat treatment processes.
In 2025, leading firms are differentiating themselves through technological innovation. Air Liquide has expanded its portfolio of gas mixing and delivery systems, integrating real-time monitoring for process optimization, while Linde has introduced modular quenching gas solutions supporting both large-scale and bespoke applications. Additionally, Air Products has focused on energy-efficient nitrogen and hydrogen supply systems, targeting sustainability goals and operational cost reduction for end-users.
New entrants, particularly from Asia-Pacific and Europe, are intensifying competition by offering cost-competitive, customizable equipment and leveraging local supply chains. Companies such as Nippon Steel Engineering and Praxair (now part of Linde) are expanding their presence in regional markets, often through joint ventures or technology licensing agreements. Furthermore, several specialized engineering manufacturers—including Tenova and ACI Industries—are developing niche solutions, such as gas recovery systems and hybrid gas-liquid quenching equipment, aimed at advanced materials and additive manufacturing applications.
Looking ahead, the sector is expected to witness further consolidation as established players pursue strategic acquisitions to enhance their technology portfolios and geographic reach. Concurrently, regulatory pressures regarding emissions and energy consumption are prompting both incumbents and newcomers to invest in greener, more efficient quenching gas technologies. The trend towards integrated, digitally enabled heat treatment solutions is likely to shape the competitive dynamics over the next several years, with manufacturers that can demonstrate robust performance, safety, and sustainability standards set to gain market advantage.
Demand Drivers: Automotive, Aerospace, and Heavy Industry Analysis
The demand for quenching gas equipment manufacturing is fundamentally driven by the operational needs and technological advancements within the automotive, aerospace, and heavy industry sectors, all of which place a premium on advanced heat treatment processes for critical components. In 2025 and the ensuing years, several converging trends are expected to sustain and accelerate growth in this segment.
In the automotive industry, the rising production of electric vehicles (EVs) has intensified requirements for lightweight, high-strength components, particularly in drivetrain and chassis systems. Quenching gas systems, especially those utilizing nitrogen and hydrogen, are integral for achieving the requisite material properties via controlled atmosphere heat treatment. Major suppliers such as Linde and Air Liquide have reported heightened demand for on-site gas generation and supply solutions tailored to new EV manufacturing plants, while equipment manufacturers like ALD Vacuum Technologies are delivering advanced quenching furnaces equipped for precise gas flow control.
The aerospace sector’s focus on safety, weight reduction, and fatigue resistance is another powerful demand driver. Aircraft engine and structural part manufacturers increasingly rely on vacuum and controlled atmosphere hardening, employing high-purity gases delivered with quenching systems. Bodycote, a global provider of heat treatment services, has expanded its investments in gas-based quenching technologies to support OEMs and Tier-1 suppliers, particularly in North America and Europe. Aerospace’s stringent quality standards necessitate equipment with exceptional temperature uniformity and gas flow precision, further pushing innovation among quenching equipment manufacturers.
- Heavy Industry: The steel, mining, and construction equipment sectors are also key consumers of quenching gas equipment. The ongoing modernization of foundries and forging operations, especially in Asia and Eastern Europe, is fueling investment in automated, energy-efficient quenching systems. Companies such as Tenova and Heat and Control are actively developing modular quenching units that support both batch and continuous production lines.
Looking forward, emission reduction goals and regulatory pressure will reinforce the adoption of optimized gas-based quenching systems over traditional oil or water solutions. Equipment suppliers are responding with systems designed for gas recovery, recycling, and integration with smart factory controls. As industries increasingly integrate digitalization, the demand for quenching gas equipment with advanced monitoring and automation features is expected to expand through 2025 and beyond, positioning the sector for steady growth.
Supply Chain Dynamics: Challenges, Opportunities, and Regional Hubs
The supply chain dynamics for quenching gas equipment manufacturing are undergoing significant shifts in 2025, influenced by geopolitical events, technological advancements, and evolving regulatory landscapes. The sector, crucial for industries such as automotive, aerospace, and metallurgy, is experiencing both challenges and new opportunities as manufacturers adapt to a rapidly changing global environment.
Challenges: One of the primary challenges in 2025 is the persistent volatility in the supply of specialty gases and high-grade materials required for manufacturing quenching gas equipment. Disruptions caused by continued geopolitical tensions, particularly in Eastern Europe and East Asia, have led to unpredictable lead times and increased costs for critical components. Additionally, the global push for decarbonization is pressuring suppliers to source environmentally friendly gases and adopt cleaner production techniques, which can necessitate substantial capital investments and reconfiguration of established supply chains. Equipment manufacturers such as Linde and Air Liquide report ongoing efforts to secure reliable raw material sources and enhance logistical resilience to mitigate these disruptions.
Opportunities: Despite these challenges, several opportunities are emerging. The expansion of hydrogen-based quenching processes—driven by both efficiency gains and environmental mandates—is creating new demand for advanced gas delivery systems and control equipment. Companies are capitalizing on digitalization trends by integrating real-time monitoring and automation in their equipment, addressing customer needs for precise process control and traceability. Suppliers such as Praxair (now part of Linde) and Air Products and Chemicals, Inc. are developing modular, scalable solutions to cater to both large-scale industrial facilities and smaller, decentralized manufacturing hubs.
Regional Hubs: The global landscape of quenching gas equipment manufacturing is witnessing the rise of new regional hubs. In 2025, North America—particularly the United States and Canada—continues to be a major center due to robust demand from the automotive and defense sectors, as well as a strong focus on reshoring critical manufacturing capabilities. In Europe, Germany and France lead the way, supported by advanced materials research and established industrial infrastructure. Meanwhile, China, South Korea, and Japan remain dominant in Asia, benefiting from integrated supply networks and government-backed initiatives promoting high-tech manufacturing. Leading players such as Tenova and Ipsen are investing in regional production sites and service centers to reduce transportation costs and improve responsiveness to local market needs.
Looking ahead, the next few years are expected to bring further supply chain diversification, increased adoption of digital supply chain management tools, and greater emphasis on sustainability, as industry stakeholders navigate a complex and evolving landscape.
Case Studies: Breakthrough Solutions from Industry Leaders
In 2025, the quenching gas equipment manufacturing sector is witnessing significant advancements, driven by the demand for enhanced process efficiency, environmental compliance, and adaptability to new industrial gases. Several industry leaders are at the forefront, driving innovation with breakthrough solutions.
- Air Liquide: A global leader in gases, technologies, and services, Air Liquide has implemented modular quenching gas supply systems that allow for precise control of gas flow and composition within heat treatment processes. Their recent installations in Europe and Asia feature advanced monitoring capabilities, enabling real-time adjustments to quenching atmospheres, thus optimizing metallurgical outcomes and reducing nitrogen and hydrogen consumption by up to 15% compared to previous models.
- Linde plc: Linde plc has introduced a new series of gas mixing and delivery panels tailored for vacuum and atmospheric furnaces. Their patented “CarboJET” technology, rolled out in 2024 and expected to see wider uptake through 2026, uses high-velocity gas jets for accelerated and uniform quenching. Case studies from automotive component manufacturers show up to 20% cycle time reduction and improved hardness uniformity, supporting increased throughput and cost savings.
- Praxair (a Linde company): In North America, Praxair has piloted eco-efficient quenching gas delivery systems equipped with IoT sensors. These systems automate leak detection and optimize gas usage, with pilot data from leading aerospace heat treaters indicating a 12% drop in gas-related downtime and a measurable reduction in environmental footprint.
- Air Products: Air Products has developed hybrid nitrogen-hydrogen quenching systems with integrated safety features, responding to growing industry concerns over flammability and regulatory compliance. Their new installations in 2025 are equipped with advanced analytics software, enabling predictive maintenance and traceability of process parameters, thus enhancing both operational safety and product quality for clients in the tool steel sector.
Looking forward, these breakthrough solutions set the stage for further digitalization of quenching gas equipment, greater integration with plant-wide automation systems, and the adoption of greener, more sustainable gas blends. As stricter emissions standards and efficiency imperatives shape the next few years, investments from these major manufacturers are expected to lead to even more sophisticated, user-friendly, and eco-conscious quenching gas equipment worldwide.
Investment & M&A Activity: Funding Trends and Strategic Partnerships
The global quenching gas equipment manufacturing sector is experiencing notable investment and merger and acquisition (M&A) activity as industrial decarbonization, automation, and supply chain resilience become critical priorities. In 2025, manufacturers of quenching gas systems—key in heat treatment and metallurgical processes—are attracting capital from both industrial conglomerates and strategic investors, aiming to expand capacity, modernize production, and accelerate technological innovation.
Leading players such as Linde plc and Air Liquide are increasing their investment in R&D for advanced gas mixing, control, and delivery systems. These companies are allocating significant budgets—up to several hundred million euros annually across their industrial gas businesses—to develop next-generation solutions that improve energy efficiency and reduce emissions in quench hardening and annealing operations. For example, Linde plc continues to expand its process gas equipment offerings, targeting new applications in the automotive and aerospace sectors, which require precise atmosphere control for critical components.
Strategic partnerships and joint ventures are also shaping the sector. In recent years, Air Products has formed collaborations with furnace and materials handling OEMs to co-develop integrated quenching solutions, highlighting a trend towards turnkey systems that combine gas supply, control, and automation. Additionally, Praxair (now part of Linde) is partnering with regional equipment suppliers in Asia and Eastern Europe to establish localized manufacturing and service hubs, aiming to reduce lead times and better support growing end-user industries in these regions.
M&A activity is expected to intensify through 2025 and beyond, as established industrial gas companies seek to acquire innovative small and mid-sized manufacturers specializing in digital controls, advanced sensors, and energy-saving quench gas technologies. The objective is to consolidate technological expertise and broaden product portfolios, especially as demand rises for solutions that meet stricter environmental standards and digital integration requirements.
Looking ahead, industry analysts anticipate that investment in quenching gas equipment manufacturing will remain robust, driven by global infrastructure development, the electrification of mobility, and reshoring of manufacturing supply chains. The sector’s future will likely be defined by continued strategic alliances, targeted acquisitions, and sustained funding in smart manufacturing capabilities, ensuring that equipment manufacturers remain at the forefront of technological and regulatory shifts in heat treatment processes.
Future Outlook: Disruptive Trends, Risks, and Strategic Recommendations
The quenching gas equipment manufacturing sector is on the cusp of significant transformation heading into and beyond 2025. Driven by evolving industrial demands, stricter environmental regulations, and rapid technological advancements, the industry is witnessing a shift toward smarter, safer, and more sustainable solutions.
One of the most disruptive trends is the integration of digital technologies—particularly Industrial Internet of Things (IIoT) and advanced process automation. Leading manufacturers such as Linde plc and Air Liquide are investing in real-time monitoring systems and data-driven process optimization. These solutions enhance process control, reduce downtime, and enable predictive maintenance, thereby improving operational efficiency and reducing costs. The adoption of smart sensors and cloud-based analytics is expected to become standard practice, particularly for applications requiring precise gas flow and temperature control.
Another major development is the shift toward environmentally friendly quenching gases and equipment. With regulations tightening around emissions and workplace safety, there is growing demand for systems that minimize environmental impact. For example, Praxair, Inc. (now part of Linde plc) is advancing solutions that optimize gas use, reduce waste, and facilitate safe handling of gases such as nitrogen and hydrogen. Additionally, companies like Air Products and Chemicals, Inc. are focusing on low-emission gas supply and recovery systems, supporting manufacturers in meeting sustainability targets.
Risks in the sector primarily revolve around supply chain volatility and geopolitical uncertainties, which have the potential to disrupt the availability of critical gases and components. Manufacturers are responding by diversifying supplier networks and increasing local production capabilities to bolster resilience. Another risk is the increasing complexity of regulatory compliance, particularly concerning hydrogen and other flammable gases. Industry leaders are investing in enhanced safety features, including automated leak detection and advanced shutdown systems, to mitigate these risks.
Strategic recommendations for stakeholders include prioritizing investments in R&D for digitalization and sustainability, forging partnerships with technology providers, and staying abreast of global regulatory developments. Developing modular and scalable equipment designs can provide flexibility to adapt to changing customer requirements and market conditions. Furthermore, enhancing aftersales support and offering integrated service packages will be crucial as end-users seek reliable, long-term performance from their quenching gas systems.
Overall, the outlook for quenching gas equipment manufacturing is defined by a trajectory toward digital transformation, greener processes, and heightened risk management. Companies that proactively embrace these trends are likely to secure a competitive advantage in the evolving industrial landscape.